Файл: Болат 20Х2Н4А маркасынан жылды бадарламасы 50000 дана тісті дгелекті жасау шін термиялы дайындама блімін жобалау мазмНЫ.doc
ВУЗ: Не указан
Категория: Не указан
Дисциплина: Не указана
Добавлен: 12.12.2023
Просмотров: 74
Скачиваний: 1
ВНИМАНИЕ! Если данный файл нарушает Ваши авторские права, то обязательно сообщите нам.
а) сыртқы дөңгелектену бұрышының радиусы 6мм,Г0СТ 75-05
7-ші бойынша;
б) штампалық еңістігі 5°.Г0СТ 75-05-89, 18-ші кесте бойынша;
в) Ішкі дөңгелектенудің радиусы 5мм. ГОСТ 75-05-89,
Кесте 2.3 -Мүмкіндік ауытқулар..
-
Болшектің өлшемдері,мм
Шыңдалманың мүмкіндік ауытқуларымен өлшемдері, мм
070
074
0345
0349
0110
0114
0210
0214
0300
0304
Қалған өлшемдер симметриялы
2.2 Дайындаманы дайындау бойынша бағыттық технологияны өңдеу (соғу, штамптау, қүю цехтары) және дайын бөлшекті сонғы механикалық өңдеу
Дайындамаларды штамп және арнайы пресс көмегі арқылы қысыммен өндеу арқылы алады. Штамптаудың алдында бастапқы металды өңдеуге дайындайды, металлдың тазартуын жүргізеді. Болат 20Х2Н4А үшін ақауларды жою үшін, фрезерлі станокта газарту әдісін тандайды. Тазартудың тереңдігі диаметр мен щыңдықтың 5-6 пайызын құрайды. Кейінен бастапқы металлды дайындамаларға бөлу операциясы жүреді. Олардың үнемқорлығы штамптаудың барлық технологиялық процесінің тиімділігіне, голлдың шығынына әсер етеді. Бөлуді, кескіш тісті аралармен немесе дискілі кейде таспалы ара көмегі арқылы іске асырады.
Таспалы бөлгіш станоктары дайындама өндірісінде үлкен қолданыс табуда. Олардың жылдамдығы 10-240 м/мин дейін жете алады, фреза бетінің жақсы сапасыз, жоғары өнімділікті, металдың : не энергияның аз шығынын қамтамасыз етеді.
Қазіргі кезде машина жасау өндірісінде қолданылатын бөлшектердің 20 пайыздан астамы (салмағы жағынан) шындалған темірді ыстық күйде штамптау әдісімен жасалады.
Металды ыстық күйде штамптау үшін, оны белгілі температураға дейін қыздырып, формасы жасалынатын бөлшектің формасындай етіп жасалған штампқа салып қысады. Нәтижесінде металға түсірілген күштің әсерінен металл деформацияланып, штамптың ішкі қуыстарын толтырады да, формасы штамптың ішкі кеңістігінің түріне сәйкес бөлшек пайда болады. Металды ыстық күйде штамптау процесі жабық және ашық штамптарда жүргізіледі. Ашық штамптарда өнделетін металл штамптың ішкі кеңістігін толық толтырған соң, артық металл штамптың екі бөлігінің қосылған жерінен сығылып сыртқа шығады, ал жабық штампта артық металл штамптың ішкі қуысында қалады.
Ыстық күйде штамптау процесінің шикізаттары көлденең қимасы дөңгелек, квадрат, тік төртбұрыш формалы сом темірлер мен әр түрлі формалы периодты прокаттар болып табылады.
Металды иінді штамптау пресінде штамптаудың , балғамен
штамптауға қарағанда, бірқатар артықшылықтары бар: металл сығындысы аз, бөлшектің дәлдігі мен жұмыс өнімділігі артық. Штампта өңделген бөлшекті автоматты түрде итеріп шығаруға арналған қондырғы бар. Қазіргі кезде елімізде металға 630-6300 тонналық күшпен әсер ететін престер бар.
Сурет і - Шықдалма
Өндіріс орындарында өндірілетін металдардың басым көпшілігі ыстык күйде өңделетін болғандықтан, штамптау прцестерінің механикалаыдыру мен автоматтандыруға көп көңіл бөлінеді
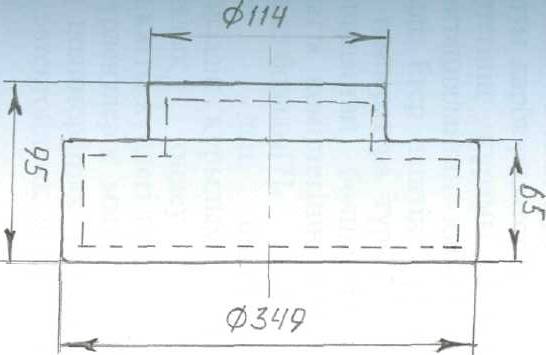
2 Технологиялық бөлімі
2.1 Термиялық өңдеудің технологиялық процесін таңдау және техника экономикалық құрылуы
Қыздырып, сонан соң тез немесе баяу түрде болат мөлшерін суыту арқылы металдың құрылысын өзгертуге және бөлшектердің тиісті беріктілігі мен технологиялық қасиетін сақтауға болады. Мұндай процесті болатты термиялық өңдеу деп аталады. Болатты армиялық өңдеу белгілі бір температуруда және уақытта жұргізіледі, әрі мүлде басқа құрылымды түзумен аяқталады.
Шыңдалмаларды алдын ала термиялық өндеуге түсірілетін ең көп таралған операциялардың бірі қалыптастыру болып табылады.
Қалыптастыру деп жұқа қаңылтақты перлитті құрлымды алу мақсатымен эвтектойдқа дейінгі болатты Ас3 нүктесінен 40-50 °С жоғары температураға дейін қыздырудан кейінен ауада суынуынан тұратын термиялық өңдеу процесін айтамыз.
Аз көміртекті болаттарды қалыптастыруға түсіргенде үйірлердің ұсақталуы басталады. Қалыптастыру жасытумен салыстырғанда үнемді операция болып табылады, өйткені ол пешпен бірге суытуды қажет етілдірмейді. Аз көміртекті болаттар үшін қалыптастыру жасытуға қарағанда кеңінен қолданылады
Цементация деп қатты, газ тәрізді және сұйық зат көмегі арқылы көміртегімен қанықтыру. Көміртегіге бай цементацияға қолданылатын затты карбюризаторлар деп атайды. Цементацияланған абапағы көміртегінің құрамы температураға, газ қысымына байланысты. Цементацияланған қабаттың тереңдігі процестің жүру ақтығына тәуелді. Егер пештің жұмыс көлемінде газ құрамының іртектілігі және температура түрақтылығы сақталса, процесс дұрыс жүреді. Цементацияланған бөлшектің сапасы қабаттың тереңдігіне байланысты, болатта көміртегінің мөлшері көбейген сайын, қабат ереңдігі соншама аз болады
Шынықтыру деп, өндеу нәтижесінде металдармен
қорытпаларда теңсіздік құрылым түзетін термиялық өңдеу түрін айтамыз. Термиялық өңдеу кезіндегі теңсіздік құрылымды орытпаларда тек қатты күйдегі түрлену болатын жағдайда ғана алуға болады. Ондай түрленулерге мыналар жатады: айнымалы ерігіштік, атты ерітіндінің полиморфтық түрленуі, жоғарғы температурадағы қатты ерітіндінің эвтектойдтық әсерлестік бойынша ыдырауы және т.б.
Теңсіздік құрылымды шығарып алу үшін корытпаны қатты күйдегі фазалық түрлену температурасына дейін қыздырады, сонан кейін суыту кезіндегі тепе-теңдік түрленуді болдырмау үшін оны тез қындатады. Мысалы эвтектойдқа дейінгі және эвтектойдтық құрамды болаттарды шынықтыру үшін қыздыру температурасы АсЗ сызығынан 30-50°С жоғары болады. Ал эвтектойдтан кейінгі болаттардың қыздыру температурасы Ас 1 -ден 30-50°С жоғары алынады. Әрі болаттардың барлығын қыздыру үшін суыту жылдамдығы керекті құрылымға байланысты тағайындалады
Босату деп өңдеу нәтижесінде алдын ала шынықтырылған қорытпаларда құрылымы тепе-теңдік құрылымға жақындай түсетін фазалық түрленулер болатын термиялық өңдеу түрін айтады. Жасытылған күймен салыстырғанда шынықтыруды босатумен немесе ескіртумен үйлестіргенде қорытпа қасиеттерінің (каттылығынан, беріктік сипаттамасының, коэрцитивтік күшінің, меншікті электр кедергісін және т.б) ең жоғарғы деңгейіне жету мақсаты көзделеді.
Төменгі босату болатты 250°С төмен қыздырудан кейінен алудан турады, босату мартенситін алу үшін және ішкі кернеуді жою үшін қолданылады.
Төменгі босатудың нәтижесінде болаттың морттылығы азайып, қаттылығы мен тозуға тұрақтылығы жоғары деңгейде сақталады (НҒІС58-64), егерде бөлшек тұтқырлы орталыққа ие болмаса, ол динамикалық жүктемелерге шыдай алмайды. Сондықтанда төменгі босатуда бөлшектерді термиялық өңдеуден кейін түсіреді
3..2. Бөлшекті термиялық өңдеудің бағыттық технологиясы
Ең тиімді эксплуатациялық қасиеттерге жету үшін, қажуға жоғары карсыластық, жоғары тозуға тұрақтылық, жемірілуге жоғары тұрақтылық келесі технологиялық операцияларды жүргізу керек:
-кривошипты ыссыштампты престе штамптау (КГШП);
-950°С температурада цементацияны жүргізу;
-910°С температурада қалыптастыруды жүргізу;
-830°С температурада беттік шынықтыруды, кейінен
төменгі босатуды жүргізу керек.
3..3. Бұйымды термиялық өңдеу операциясын орындау үшін
уақыттың есептелген нормасын анықтау
Термиялық өндеудің мақсаты болаттан жасалған тісті дөңгелектердің эксплуотацияға қажетті қасиеттерін жақсаратын белгілі бір құрлымға келтіру. Термиялық өңдеу ұзақ уақыттылыққа әсер етеді.
Қыздыру уақытын есептеу үшін ең алдымен тісті дөңгелектің қай денелерге жататынын анықтау керек.
- егер Ві>0,25 болса, онда кесек денелерге жатады;
-егер Ві<0,25 болса, онда жіңішке денелерге жатады және келесі теңдікпен анықталады:
Ві=Sά/λ (3.1)
Мүндағы: S-дененің өлшемі, м;
ά-жылу беру коэфиценті;
λ -жылу өткізгіштік коэфиценті, ол 28Вт/(м2к)тең. Био айқын өлшемінің мәнін анықтау үшін, металға жылу беру коэфицент қосындысының мәнін табу керск.

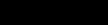
Мүндағы, акопв -конвекциямен жылу беру коэфиценті, пеш үшін оның орташа мәнін 11.8Вт(м2 к)деп аламыз а иіл - сәулеленумен жылу беру коэфиценті, оның мәні келесі теңдікпен анықталады.
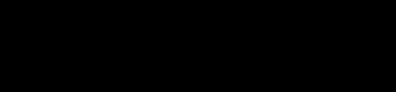
Мүндағы: С1КМ -алыну коэфиценті (электр пешінде қыздыруда) ол 1,5Вт/м2 деп алынады.
1000 + 293 4 20 + 273 4 1000 + 273 4+ 920 + 273
а =
1000-20)* (1000-920)]
а,пл = 54,32 Вт/(м2хК) Осыдан: ао6щ=66,12 Вт/(м2хК)
8-дененің қалыңдығы цилиндр үшін 0.085 м Алынған мәндерді 3.1 теңдеуге қойып
Ві =0,085*66,12/28-0,28
Ві-0,25-тен үлкен болғандықтан кесек денеге жатады. Дененің қыздыру уақытын анықтау.
Мүндағы: Мб- бөлшектің массасы кг;
С- жылусыймдылығы 0,59 кдж/(кг к);
Тс- металл ортасының темперасы °С;
Тнач жәнеТкон —металдың бастапқы және соңғы
температурасы, °С;
Ғ- бұйымның активті ауданы келесі, м2
тендеумеумен анықталады:
(3.5)
Ғ=2*3,14*172,8*(172,8+85)=279863,5мм2=0,27м2 Табылған бұйымның активті ауданын (3.4) теңдеуіне қойып тісті дөңгелектің цементацияға 950 С қыздыру
уақытын табамыз.
Тн= 19,2*0,59/78,9*0,27 Лп(1000-20/1000-950)=1,57=94,4мин
910°С темепратурада қалыптастыру үшін Тн=19,2*0,9/78,9*0,27*1п(10ОО-2О/10О0-91О)=1,25=75, З мин
200°С температурада төменгі босату үшін, Тн=19,2*0,59/78,9*0,27*1п(230-20/230-200)=1,02=61,6мин Цементация кезіндегі ұстау уақыты келесі теңдеумен анықталады:
(3.6)
Т¥=1/4-1,57+6О-33,3/1ОО=2Ос=12ООмин
Цементациядан кейінгі суыту уақыты б0 мин. Қалыптастыру үшін ұстау уақыты келесі теңдікпен анықталады:
=10+1 мин/1мм қалың (3.7)
=10+172=182 мин .
Қалыптастырудан кейінгі суыту уақыты 110 мин.
Төменгі босату үшін ұстау уақыты :
=10+ 1мин/1мм қалың=68мин.
Төменгі босатудан кейінгі суыну уақыты б0 минут.
830 °С температурада беттік шынықтыруда, бөлшектің қыздыру уақытын есептейміз.
Тоқтың жилігін анықтаймыз, 2 мм қалыңдыққа кіретін.
Ғ=(60/бк)2 (3.8)
Мүндағы: бк- қабат калындығы мм.
Ғ=(6О/О,23)2=7О кГц 20-73О°С температура интервалында тоқтың жилігі 70000 Гц
К

V =
V п
мүндағы: g-меншікті қуат, Вт/м2;
λ - жылу өткізгіштік коэфицент, Вт/(м2-К)
а - температура өткізгіштік коэфицент а=0,9х10-5м2/сек.
3.4 Бөлшекті қыздыруды есептеу бағдарының блок-схемасы Технологиялық есептеулерде ЭВМ-ды қолдану арқылы процесстерді тездетуге болады.
Program nagrev;
Uses crt, dos;
Label out, big, plast;
Var
t, tn, ts, integer;
Bi,Fo,e,c,P, m2, NO, UO, tz, tp:real;
Q1,Q2, as, at, Aluc, Asum, Akonv,
Atemp, cnag, Ytep: real;
Begin
Clrscr;
Writeln (Қыздыру (суыту) уақытын есептейтін программа))
Write (Есептеу үшін кестелер мен сүлбелерді қолдану керек);
Write (Жылумен өңдеу технологиясы бойынша кітаптар);
Write ln (Цилиндрлк бөлшектің есептелуі);
Write ln (Пластинаны есептеу үшін г орнына S);
Write ( Бөлшектердің өлшемдерін еңгізу);
Read ln (t);
Write (Бөлшектің қыздырылу(суыну) температурасын еңгіз)
Read ln (t)
Write (Бөлшектің бастапқы температурасын еңгіз);
Read ln(tn);
Write (орта температурасы 30-50 градусқа);
ts:=t+40
Write ln (бөлшектің жоғары кыздыру температурасы тең);
(ts, градус);
(температуралық критерий
(жылу беру коэфиценті Аsum есептеледі);
(ол жылу беру коэфиценті Аlus құралады);
(конвекция Аkonv);
( Стефана-Больцмана заңы бойынша Аlus тең);
(Аlus =С[(Т8/100)х4-(Т/100)х4]/(Тз-Т));
( С- сәулелену коэфиценті с=5,7е);
(е-қаралық дәрежесі);
(Тs и Т - орта мен материалдың температурасы);
(материалдың қаралық дәрежесін енгіз е=);
read (е)
аs:=((ts+273)/100)х((ts+273)/100)х((ts+273)/ІОО);
аt: = ((ts+273)/100)х((ts+273)/ 100)х((ts+273)/100);
Аluc:=5.7е(as-аt)/(ts-t);
(Конвекциямен жылу беру коэфиценті Аkonv
осылайша есептеледі:);
( пештегі ауа қабатының айналу жылдамдығының
теңдeуі бойынша:);
(сәулетарату арқылы жылуберу коэфиценті Аluc);
( конвкция арқылы есептелген жылуберу
коэфицентін Аkonv еңгіз);
Read ll n(Akonv);
Аsum:=Аkonv+Аluc;
(жалпы жылуберу коэфиценті Аsum тең, Аsum);
(жылу өткізгіш коэфицентін Ytep eңгіз:);
Read (Ytep);
Bi: Asum r/Ytep;
(Критерий Био тең, Ві);
If Bi <0.25 then goto big;
( био критериі 0,25 аз болғандықтан жіңішке
дененің есебін еңгіземіз);
(Био, Ві критериін біліп);
(және температуралық критерий Q1);
(номограмма арқылы критерий Фурье,
табамыз);
( критерий Фурье еңгізу:);
Read(Ғ(І);
( Фурье критерий мәні бойынша қыздыру
(суыту) уақытын есептейміз );
( Спад=Ғпг 2/Аtemp теңдеуі бойынша);
(мұндағы, Аtemp=Үtер/с р - температура өткігіштік
коэфиценті);
(с –жылусыймдылық,);
(р - материалдың тығыздығы);
(дайындама материалының жылу сыймдылығын
Енгіз:);
Readln(c);
(материалдың тығыздығын еңгіз);
Readln(Р);
Atemp:= Үtер/с р;
(температура өткізгіш коэфицент Аtemp тең, Аtemp);
Спад:=Ғ(І гг/Аіtemp;
(қыздыру суыту уақыты тең: Спад, ч);
Goto out;
Out:repeat until keypressed;
END
-
Айлабұйымның тағайындалуы
Айлабұйым пісірмелі құрылғыдан тұрады. Ол бұйымдарды газды, нитроцементация немесе азоттау кезінде шахталы пештерге орналастыру үшін қызмет атқарады. Айлабұйым бөлшектерді пештік жұмыс ортасында жүктеу мен тасымалдауға ыңғайлы болып жасалған. Айлабұйым ішінде жоғары температураларда жұмыс істейтіндігінен, сенімділік пен ұзақ уақыттылық талаптары жоғарылайды..
Осыған байланысты оларды ыстыққа берікті болаттардан жасайды.
4.2 Айлабұйымды есептеу
Айлабұйымның қима диаметрін, жүктеменің өзгермелі қосымшасының жағдайынан анықтаймыз (жүктеме 0 ден максимумға дейін жоғарылайды).
Созу кезіндегі кернеуі [б]с=90 Мпа
Түсірілстін жүктеме Р келесі теңдеумен анықталады
Р=гтС (4.1)
Мүндағы: п- жүктердің саны
С - жүктердің ауырлық күші.
Онда жүктеме келесі теңдікпен анықталады:
Р=п-т-§=8-19,2-10=1536 Н
Тұтқаның көлденең қимасының ауданы келесі теңдеумен анықталады.
Ғ=Р/бс= 17 см ;
Дөңгелек қиманың ауданы келесі теңдеумен анықталады.
_ Ғ=ясі2/ (4.2)
Ід р
осыдан 6= — =4,6см=46мм V п
Бөлшектерді пешке жүктету үшін арнайы ыстыққа берікті
12X13 маркалы болаттан жасалған кәрзенкені таңдап аламыз.
Бөлшектің ең үлкен диаметрі 345 мм. Барлығы 8 бөлшек
сүктеледі. Кәрзенкенің диаметрін 500 мм, биіктігін 800 мм, қабырғаның қалыңдығын 20 мм деп аламыз
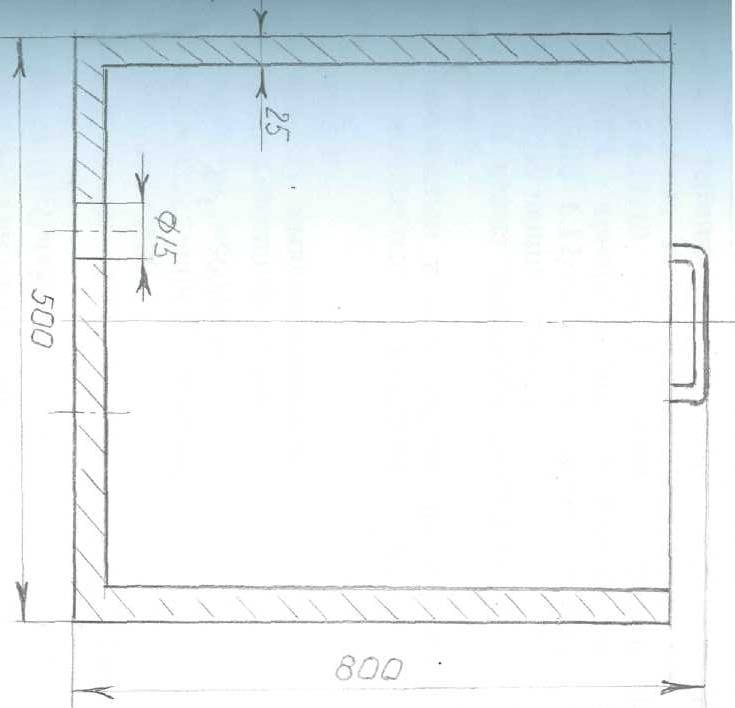
Сурет 2 Айлабұйымның кұрассызбасы.
Айлабұйымның өлшемдерін келесі тендеумен анықтаймыз:
На-Нш х п=95х8=760 мм
Мұндағы: На-айлабұйымның биіктігі;мм
Нш - шыңдалманың қалыңдығы; мм
n-жүктеменің саны;
с1а-(Зб+Ас1к+2 ДсІ=349+2х25+2х50,5=500 мм
Мұндағы : dа-айлабұйымның сыртқы диаметрі; мм
dқ-қабырғаның калыңдығы; мм
d-қабырғамен бөлшектің арасындағы кашықтығы; мм
5 ӨНДІРІСТІ ҮЙЫМДАСТЫРУ