Файл: Анизаций выполняющих строительство, реконструкцию, капитальный ремонт объектов атомной отрасли.doc
ВУЗ: Не указан
Категория: Не указан
Дисциплина: Не указана
Добавлен: 09.01.2024
Просмотров: 155
Скачиваний: 1
ВНИМАНИЕ! Если данный файл нарушает Ваши авторские права, то обязательно сообщите нам.
Сборка соединений под сварку
Рисунок 11.1 – Схема сборки соединений труб с применением временных креплений
Таблица 11.1 Рекомендуемое количество прихваток и их протяженность в зависимости от диаметра свариваемых труб.
Просвет между линейкой и поверхностью трубы (α**≤1,5мм) на расстоянии 200 мм от центра соединения для труб диаметром более 100 мм.
Рисунок 11.2
Рисунок 11.3 – Отклонение от перпендикулярности штуцеров (врезок в трубопровод).
-
К сборке соединений труб и деталей под сварку разрешается приступать после приёмки качества подготовки кромок. -
Сборку соединений трубопроводов под сварку следует производить в соответствии с требованиями ПТД, оговаривающей последовательность сборки соединений трубопроводов, способ закрепления собираемых деталей, необходимость установки приспособления для поддува защитного газа, требования к качеству сборки. -
Сборку стыковых соединений труб рекомендуется осуществлять с помощью инвентарных приспособлений (центраторы, стяжки), обеспечивающие достижения соосности стыкуемых трубных деталей и регулировку зазора в соединении. -
Рекомендуется применять приспособления, позволяющие выполнять сварку без установки прихваток, например, центраторы типа ЦСА 14-42;
ЦСА 57-76; ЦСА 89-108 или других типов. -
Укрупнительную сборку стыковых соединений труб в плоские и пространственные блоки выполнять на стендах, при сборке пространственных блоков для удержания их при сборке применять переносные зажимы и стойки-захваты. -
Приварка временных технологических креплений допускается только в случаях, предусмотренных чертежами или ПТД. При этом должна быть оговорены марка стали, форма, размеры, количество и расположение указанных креплений, квалификация сварщиков, осуществляющих приварку креплений, сварочные материалы, способы и режимы приварки. Использование временных технологических креплений при сборке деталей из сталей аустенитного класса допускается при номинальной толщине деталей не менее 6 мм. -
Сборку соединений труб диаметром 219 мм и более, свариваемые ручными методами сварки допускается выполнять с применением временных технологических креплений (рисунок 11.1) состоящих из уголков, привариваемых к наружной поверхности трубы. Соединения временных технологических креплений с трубой выполняются ручной аргонодуговой сваркой (РАДС) или дуговой сваркой (РДС) с применением сварочных материалов (проволоки, электродов), приведённых в таблице 8.1 для данной марки стали труб. -
Сборка выполняется 3-4 стяжками, равномерно расположенными по периметру соединения. -
Для приварки временных технологических креплений из углеродистой стали к деталям (сборочным единицам) из сталей аустенитного класса следует применять покрытые электроды марок ЭА-395/9, ЦТ-10 или сварочную проволоку марки Св-10Х16Н25АМ6. -
Поверхность деталей в местах приварки креплений должна быть предварительно зачищена от окалины, ржавчины, краски, масла и других загрязнений. -
Швы приварки временных технологических креплений должны быть расположены на расстоянии не менее 60 мм от подлежащей сварке кромок. При сборке под сварку деталей из углеродистых и кремнемарганцовистых сталей допускается уменьшение указанного расстояния до 30 мм. -
Временные технологические крепления удаляются механическим способом. При этом на деталях из углеродистых и кремнемарганцовистых сталей допускается полное удаление временных технологических креплений кислородной или воздушно-дуговой резкой, без углублений в основной металл с последующим шлифованием поверхности деталей до удаления следов резки. На деталях из сталей аустенитного класса допускается неполное удаление временных технологических креплений кислородной (кислородно-флюсовой) плазменно-дуговой или воздушно-дуговой резкой. При этом оставшаяся часть крепления должна иметь высоту не менее 4 мм и подлежит последующему удалению механической обработкой. -
При удалении временных технологических креплений допускается неполное удаление металла шва приварки. В случае приварки временных технологических креплений аустенитными присадочными материалами к деталям из сталей перлитного класса, а также при приварке указанными материалами креплений из углеродистых сталей к деталям из сталей аустенитного класса неполное удаление аустенитного металла шва допускается со стороны, не контактирующей с рабочей средой.
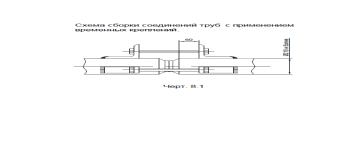
Рисунок 11.1 – Схема сборки соединений труб с применением временных креплений
-
Места приварки временных технологических креплений подлежат контролю неразрушающими методами, исходя из требований ПКД. -
При сборке соединений труб на прихватках необходимо выполнять следующие требования:
-
прихватки должны выполнять сварщики, допущенные к сварке соединений, на которых выполняется прихватка; -
прихватки выполняются способом РАДС или РДС; -
при выполнении прихваток применяются сварочные материалы, указанные в таблицах 8.1; -
при сварке деталей, подлежащих сварке с поддувом защитного газа во внутреннюю полость для защиты обратной стороны шва, прихватки также следует выполнять с поддувом; -
дефектные прихватки должны быть удалены механической обработкой (шлифованием или т.п). В случаях, оговоренных в ПТД, в соединениях деталей из сталей перлитного класса допускается удаление дефектных прихваток воздушно-дуговой строжки.
-
Наложение прихваток в местах пересечения или сопряжения двух или нескольких подлежащих сварке соединений не допускается. -
Прихватку собранных сварных соединений рекомендуется выполнять аргонодуговой сваркой с присадочной проволокой или без присадочной проволоки в случае заварки сварного соединения способам РАДС. -
Прихватки соединений, свариваемых ручной дуговой сваркой (РДС) разрешается выполнять также ручной дуговой сваркой. Прихватки в соединениях, корень шва которых сваривают ручными способами, выполняют с полным проплавом. -
Прихватки следует располагать равномерно по периметру стыка. Рекомендуемое количество прихваток и их протяженность указана в табл.11.1
Таблица 11.1 Рекомендуемое количество прихваток и их протяженность в зависимости от диаметра свариваемых труб.
Наружный диаметр стыкуемых труб, мм | Количество прихваток, шт. | Протяженность одной прихватки, мм |
До 89 | 2-3 | 10-20 |
Более 89 до 426 | 3-4 | 20-50 |
Более 426 | Через каждые 250-300 мм | 50-80 |
-
К качеству прихваток предъявляются такие же требования, как к сварному шву. Оценка качества прихватки производится по результатам визуального контроля после зачистки поверхности от шлака (при способе РДС). -
Перед установкой прихваток (при сборке) зачищенные кромки и поверхности труб обезжирить ацетоном или уайт-спиритом. Необходимость обезжиривания кромок устанавливается ПТД. -
Собранное под сварку соединение подлежит визуальному и измерительному контролю, при котором контролируется:
-
чистота поверхности основного металла и кромок; -
зазоры в соединении; -
правильность сборки деталей и их закрепление; -
качество прихваток и правильность их выполнения; -
правильность установки временных креплений; -
перелом осей соединяемых деталей; -
соответствие размеров собранного узла требованиям рабочих чертежей и ПТД; -
отклонение оси штуцера(врезки) от оси перпендикулярной оси труб; -
правильность сборки элементов крепления с трубопроводом; -
в процессе производства работ по сборке контролируется на соответствие ПТД; -
соответствие сварочных материалов и квалификация сварщиков; -
наличие и режим поддува защитного газа; -
режимы сварки (для прихватки и приварки временных технологических креплений).
-
Перелом осей собранных элементов в стыковом соединении проверяется с помощью линейки длиной 400 мм и щупа. -
Просвет между линейкой и поверхностью трубы (α) на расстоянии 200 мм от центра соединения, не более указанных на рисунке 11.2. Для труб диаметром менее 100 мм величина просвета (α) α**≤1мм. Не допускается сборка труб с применением натяга. -
Отклонение штуцера (врезки) от вертикального положения должно быть не больше величин, указанных на рисунке 11.3. -
В собранном и проконтролированном сварном соединении труб из аустенитной стали, подлежащему дуговой сварке покрытыми электродами, с наружной стороны трубы на ширине не менее 100 мм в каждую сторону от разделки поверхность основного металла должна быть защищена от попадания брызг расплавленного металла. В качестве защитного покрытия разрешается применять каолин по ГОСТ 21287-75, разведённый водой, аэрозольный препарат «Дуга-1», «Дуга -2» или другие. Попадание каолина, эмульсии, в разделку не допускается. Удаление каолина производится водой после окончания сварки. -
Собранное под сварку соединение должно быть укрыто хлопчатобумажной тканью с целью предотвращения попадания влаги, абразивной пыли, и прочих загрязнений в разделку, зазоры соединений и на прилегающие к разделке поверхности деталей. -
При необходимости транспортирования собранных деталей (сборочных единиц) к месту сварки следует обеспечить условия, предотвращающие разрушение прихваток или швов приварки временных технологических креплений, а также деформацию, повреждение и загрязнение собранных под сварку деталей.
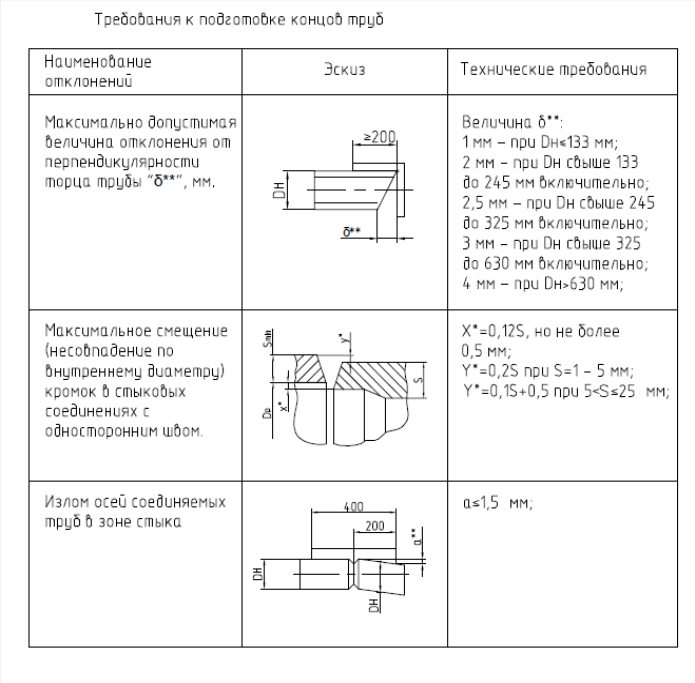
Просвет между линейкой и поверхностью трубы (α**≤1,5мм) на расстоянии 200 мм от центра соединения для труб диаметром более 100 мм.
Рисунок 11.2
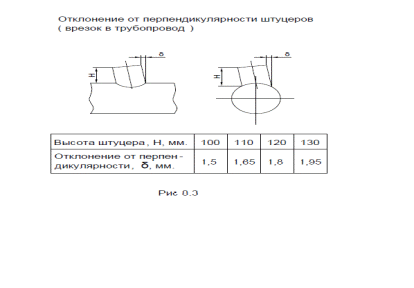
Рисунок 11.3 – Отклонение от перпендикулярности штуцеров (врезок в трубопровод).
-
Сварка-
Способы сварки стыковых и угловых соединений трубопроводов
-
-
Согласно требованиям Правил АЭУ [10] и таблицы 10.1 настоящего стандарта для выполнения сварных соединений трубопроводов могут применяться следующие способы сварки:
-
ручная дуговая сварка покрытыми электродами; -
ручная аргонодуговая сварка; -
полуавтоматическая (механизированная) сварка плавящимся электродом в смеси газов (Аr+СО2); -
автоматическая аргонодуговая сварка неплавящимся электродом без присадочной проволоки; -
автоматическая аргонодуговая сварка с присадочной проволокой; -
автоматическая сварка под слоем флюса.
-
Ручную и автоматическую аргонодуговую сварку соединений трубопроводов категории IIв, IIIв, IIIc по Правилам АЭУ [11] разрешается выполнять в комбинированной (двухгазовой) защитной среде, когда аргон и двуокись углерода истекает из горелки по самостоятельным концентрически расположенным соплам (по внутреннему – аргон, по периферийному – двуокись углерода). -
Для выполнения сварных соединений трубопроводов III категории по Правилам АЭУ [11] из углеродистых и кремнемарганцовистых сталей разрешается применять механизированную сварку в среде двуокиси углерода сварочной проволокой марки Св-08Г2С. -
Ручную и автоматическую аргонодуговую сварку неплавящимся электродом, а также механизированную сварку плавящимся электродом в среде защитного газа разрешается выполнять в непрерывном и импульсном режимах горения дуги. Автоматическая аргонодуговая сварка импульсной дугой может выполняться с непрерывной и шаговой (прерывистой) скоростью перемещения электрода. -
При выполнении одного соединения допускается использование двух или нескольких способов сварки из числа указанных в п.12.1.1.
-
Условия производства сварочных работ
-
Сварку соединений трубопроводов в монтажных условиях рекомендуется выполнять в закрытых помещениях (цех предмонтажных работ, временные помещения) при наличии естественного или искусственного освещения. Допускается выполнение работ по укрупнению блоков на открытой площадке при условии создания временных укрытий мест сварки от ветра и осадков. -
При выполнении работ в помещениях энергоблока не допускается производства сварочных работ в период совмещённых строительно-монтажных работ. При монтаже трубопроводов категорий IIa, IIв, IIIa по Правилам АЭУ [11] сварочные работы рекомендуется выполнять в помещениях, сданных под «чистый монтаж». -
Места производства сварочных работ должны быть защищены от любых воздействий, влияющих на качество сварных соединений (атмосферные осадки, направленные потоки воздуха и т.д.). -
Сварку в монтажных условиях допускается выполнять при температуре не ниже минус 15С. -
Изготовление сборочных единиц или деталей трубопроводов в монтажных условиях допускается при температуре не ниже 0С. -
Сварку соединений, выполняемых при положительной температуре без подогрева, при отрицательной температуре следует сваривать с подогревом не ниже 50С. -
Сварку соединений труб из сталей аустенитного класса разрешается выполнять без подогрева при температуре окружающего воздуха не ниже минус 5С. При более низкой температуре сварку выполнять с подогревом, температура которого должна быть не ниже 0С. -
В процессе производства сварочных работ на участке (в помещении), где они выполняются, должны выполняться меры по поддержанию необходимой чистоты (периодическая уборка с увлажнением полов).
-
Требования к расположению сварных соединений
-
Сварные соединения по месту монтажа должны располагаться в местах, удобных для их качественного выполнения. Расстояние между трубой и стеной (полом, потолком) или соседней трубой должно составлять не менее 150 мм. Сварные соединения на участках трубопровода, расположенные на расстоянии меньше 150 мм от стены (пола, потолка) должны быть сварены при укрупнении блока. Уменьшение указанного расстояния допускается в исключительных случаях. Проектное решение о расположении соединения на расстоянии ближе 150 мм должно быть согласовано с монтажной организацией. Также при расстояниях меньше 150 мм соединения труб Ду до 150 мм включительно рекомендуется выполнять автоматической аргонодуговой сваркой неплавящимся вольфрамовым электродом. -
При разработке технологии монтажа трубопровода предусматривать возможность сварки соединений автоматами типа «ОДА» и другие. При этом длина свободного цилиндрического участка в одну из сторон соединения свободного от любых других элементов (штуцеров, упоров опор и пр.) и отверстий должна составлять не менее величины, указанной в графе «Установочная длина» (Таблица 6.8 настоящей Инструкции), а в другую сторону от соединения не менее 30 мм- для труб диаметром до 42 мм; не менее 50 мм - для труб диаметром от 57 до 159 мм, не менее 100 мм - для труб диаметром от 219 мм до 720 мм. -
Расстояние трубы от стен, потолка, пола, соседней трубы и т.д. должно быть не менее величин, указанных в графе «Радиус вращающихся частей» (Таблицы 9.8, 9.9 настоящего стандарта). -
Сварные соединения должны располагаться вне опор. Расположение опор над (под) сварным соединением допускается при одновременном соблюдении следующих условий: