Файл: Курсовой проект по дисциплине Оборудование машиностроительных производств.docx
ВУЗ: Не указан
Категория: Не указан
Дисциплина: Не указана
Добавлен: 09.11.2023
Просмотров: 82
Скачиваний: 1
ВНИМАНИЕ! Если данный файл нарушает Ваши авторские права, то обязательно сообщите нам.
СОДЕРЖАНИЕ
Расчет усилия штамповки.
Температура заготовки в этот момент t = 1000°С. Материал детали - качественная конструкционная углеродистая сталь 45Л ГОСТ 133-71.
Таблица 2. Механические свойства стали при ковочных температурах
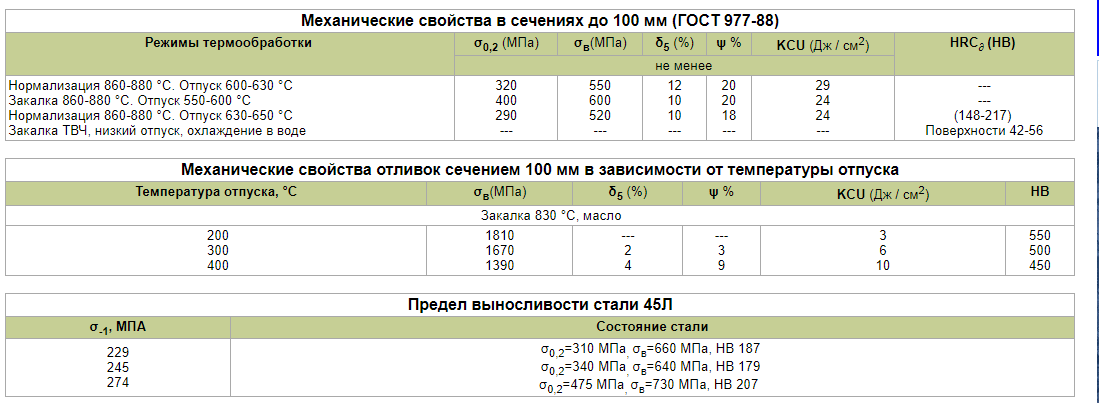
Определение усилия штамповки.
Окончательную штамповку проводят в открытом ручье. Температура заготовки перед штамповкой t = 1000°С. Расчет усилий штамповки на КГШП (кривошипный горячештамповочный пресс) необходимо выполнять с максимально возможной точностью, так как при использовании пресса с недостаточным усилием может произойти авария, а при использовании пресса по завышенному усилию пресс будет использоваться нерационально.
Усилие при штамповке осаживанием в открытых штампах определяют по формуле:
P=σт× [(1,5+М0×



где σт - предел текучести металла при температуре штамповки, МПа;
М0= 0,5 - коэффициент внешнего трения (на мостике облоя); в расчете принимается его максимальное значение, равное 0,5;


F0 - площадь проекции мостика облоя, мм2;

Fn - площадь проекции поковки на плоскость разъема, мм2;

Предел текучести металла принимают приблизительно равным временному сопротивлению растяжению при соответствующих температуре и скорости деформации. В нашем случае:
σв=53 МПа,
где - скоростной коэффициент, = 1,7; - значение предела прочности при t = 1000°С .
σт=53×1,7=90,1 МПа.
Площадь проекции мостика облоя находится по формуле:
F0=



где


F0=

Рассчитаем площадь проекции:
Fn=????×

Fn=3,14×1082/4=9 156 мм2
По формуле (1) определим усилие штамповки:
P=90,1× [(1,5+0,5×



По полученному значению усилия штамповки выбирается пресс горячештамповочный усилием 2,5 МН, так как технологическое усилие штамповки должно быть меньше 85% от номинального усилия пресса.
Так как Р <2,2%, то выбранный пресс модели К0134 отвечает данному условию Р <85% Рн. Пресс предназначен для производства поковок из черных и цветных металлов. Технические характеристики пресса приведены в табл. 3.
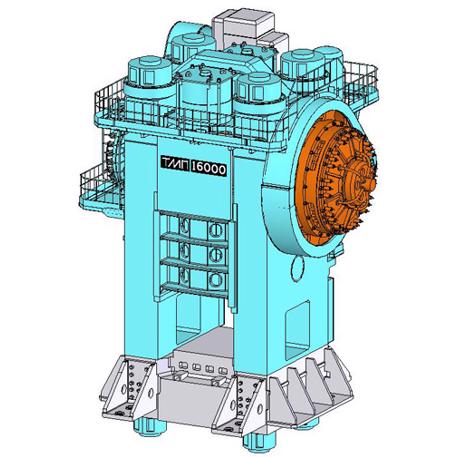
Рис.4 Пресс кривошипный горячештамповочный К0134.
Таблица 3. Основные технические характеристики ГШП К0134.
Параметр | Значение |
Номинальное усилие, кН | 2500 |
Ход ползуна, мм | 200 |
Расстояние между столом и ползуном, мм | 420 |
Частота ходов ползуна непрерывных, 1/мин | 42 |
Размеры стола: ширина/ длина, мм | 750/1120 |
Мощность двигателя главного движения / мощность суммарная, кВт | 26,5 |
Габариты станка, мм | 2640×2700×4810 |
Масса, кг | 200000 |
5. Разработка технологического процесса механической обработки детали.
Необходимо учесть тип производства и конструктивные особенности детали. Здесь осуществляется выбор технологических баз. От правильного выбора технологических баз во многом зависит точность обработки детали.
Рекомендации по выбору баз следующие:
- установочная база должна иметь достаточные размеры, чтобы обеспечить устойчивое положение заготовки при обработке;
- на первой операции обрабатывают поверхность, которая, в дальнейшем, служит основной установочной базой;
- при выборе чистовых баз нужно стремиться к тому, чтобы установочные базы совпадали с измерительными или конструкторскими базами. В этом случае погрешность базирования равна нулю (принцип совмещения баз).
- при выборе чистовых баз нужно стремиться к тому, чтобы на всех операциях вести обработку от одних и тех же установочных баз (принцип постоянства баз).
Указать, какие приняты черновые базы, какие приняты чистовые базы.
При выборе модели станка нужно руководствоваться следующими соображениями:
- функциональным назначением и технологическими возможностями станка,
- обеспечением требуемой точности;
- обеспечением требуемой мощности;
Здесь приводятся пооперационно модели станков, выделяются среди них станки-полуавтоматы.
Выбор оборудования производится по каталогам, номенклатурным справочникам.
При выборе модели станка нужно руководствоваться следующими соображениями:
- функциональным назначением и технологическими возможностями станка,
- обеспечением требуемой точности;
- обеспечением требуемой мощности;
Выполняются технологические эскизы на все разработанные операции (с указанием базовых поверхностей, крепления детали, толстыми линиями выделяются обрабатываемые на данной операции поверхности), указывается ее название, оборудование, приспособление, режущий и измерительный инструмент, содержание операции. Деталь изображается в таком виде, какой она примет после выполнения данной операции; в таком положении, в каком она выполняется на данной операции. Обязательно проставляется шероховатость обрабатываемых поверхностей.
Зная вид заготовки, решают задачу о выборе первого метода маршрута. Если, например, точность заготовки невысока, то обработку данной поверхности начинают с использования чернового метода. При точной заготовке сразу можно назначить чистовую, а в некоторых случаях и отделочную обработку.
Исходя из завершающего и первого методов маршрута обработки, устанавливают промежуточные методы. При этом исходя из того, что каждому методу окончательной обработки предшествует один или несколько возможных предварительных, менее точных методов. Так, чистовому развертыванию предшествует предварительное, а предварительному развертыванию – чистовое зенкерование, а ему – сверление.
Таким образом, технологический допуск на промежуточный размер и качество поверхности, полученной на предыдущей ступени обработки, должны находится в тех пределах, при которых возможно нормальное использование намеченного последующего метода обработки.
При составлении маршрута обработки в целом необходимо учитывать следующие рекомендации.
1. Сначала обрабатывают поверхности, которые на последующих операциях будут использоваться в качестве технологических баз (центровые отверстия, базовые торцы, шейки, плоскости и т.п.).
2. Затем обрабатывают остальные поверхности в последовательности, обратной степени их точности, т.е. чем точнее должна быть обработана поверхность, тем позднее она обрабатывается.
3. Заканчивается обработка той рабочей поверхности, которая является наиболее точной и имеет наибольшее значение для детали с точки зрения ее функционирования.
4. В конец маршрута часто выносят обработку легкоповреждаемых поверхностей, к которым, например, относят резьбы, особенно наружные, и т.п.
5. Операция термообработки (закалка или цементация и закалка), если она предусмотрена, должна располагаться после лезвийной обработки (точение, сверление, нарезание резьбы и пр.) и перед операциями с абразивными методами отделочной обработки поверхностей (шлифование, полирование и др.).
В производстве точных машин обработку деталей часто разделяют на три последовательные стадии: черновую, чистовую и отделочную (чистовую). Такое расчленение маршрута производят по следующим соображениям. На черновой стадии имеют место сравнительно большие погрешности, вызванные деформациями технологической системы от сил резания и закрепления заготовки, а также ее интенсивным нагревом. Чередование в этих условиях черновой и чистовой обработки не обеспечивает заданную точность. Такой принцип построения маршрута не во всех случаях является обязательным. Так при большей жесткости технологической системы и малых размерах обрабатываемых поверхностей окончательная обработка отдельных элементов может выполняться и в начале маршрута. Данный принцип в определенной степени