Файл: Важную роль играет предприятия Акционерное общество Акционерная компания Железные дороги Якутии.docx
ВУЗ: Не указан
Категория: Не указан
Дисциплина: Не указана
Добавлен: 10.11.2023
Просмотров: 177
Скачиваний: 3
СОДЕРЖАНИЕ
1.1 Оценка качества работ в цехе ТО4
1.2 Оценка уровня механизации в цехе ТО-4
1.3 Выводы и предложения по улучшению производства в цехе
2. РАЗРАБОТКА ТЕХНОЛОГИЧЕСКОГО ПРОЦЕССА РЕМОНТА УЗЛА
2.1.2 Моторно-осевые подшипники
2.1.3 Циркуляционная система смазывания осевых подшипников
2.1.8 Кожух тягового редуктора
2.1.9 Подвешивание тягового электродвигателя
2.2 Работы выполняемые на ТО и ТР
2.3 Организация технологического процесса ремонта узла
2.3.2 Разборка и ремонт колесно-моторного блока
2.3.3 Сборка колесно-моторного блока
3.1 Опыт передовых предприятий по организации производства в цехе
3.2 Экономическая эффективность механизированных позиций
3.3. Основные показатели и преимущества разработанного оборудования
2.1.4 Шестеренный насос.
Шестеренный насос состоит из корпуса 4, изготовленного из отливки чугуна, в который вставлены шестерни 2 и 3, имеющие 14 зубьев каждая, модуль – 2 мм и ширину венца 14 мм. Шестерни являются рабочими органами подачи масла в систему смазывания осевого подшипника. К корпусу насоса через штифты 9 и болты 14 крепится клапанная коробка 1, в которой размещаются обратные шариковые клапаны 13 на всасывание и нагнетание для каждого направления вращения насоса. Всасывающие отверстия клапанной кробки закрыты сеткой 12. На хвостовик валашестерни 3 установлено приводное зубчатое колесо 10, которое находится в зацеплении с шестерней, установленной на оси колесной пары. Приводное зубчатое колесо снизу ограждено кожухом 11 для уменьшения барботажных потерь (вспенивания).
Рис. 2.3. Шестеренный насос: 1-клаппанная коробка; 2, 3-шестерни; 4-корпус насоса; 5-втулка; 6-шпонка; 7, 8-винт; 9-штифт; 10-приводное зубчатое колесо; 11-кожух; 12-сетка (фильтр); 13-обратный клапан; 14-болт; 15-гнездо клапана; 16-уплотняющее кольцо; 17-пробка.
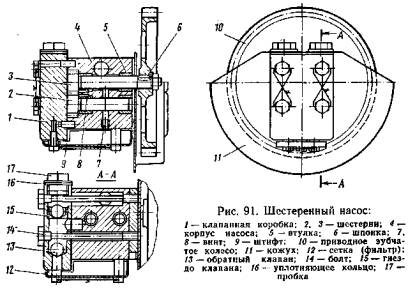
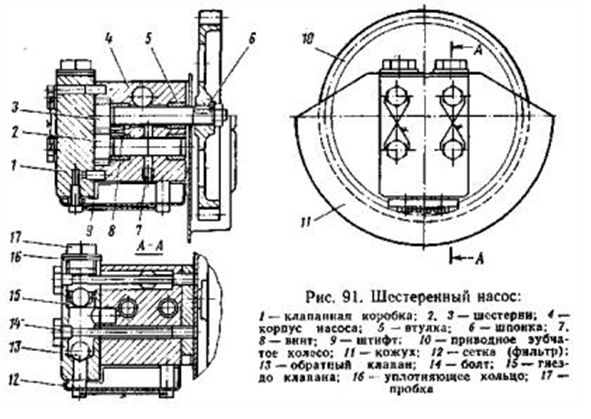
2.1.5 Тяговый редуктор
Тяговый редуктор тепловоза предназначен для повышения вращающего момента, передаваемого тяговым электродвигателем на колесную пару, и обеспечения заданной длительной и конструкционной скоростей движения тепловоза.
Зубчатая передача редуктора при опорно-осевом подвешивании тягового электродвигателя работает в тяжелых условиях, обусловленных переменными режимами работы и динамическими нагрузками, перекосом зубчатых колес от деформации оси и вала якоря, а также перекосом остова тягового электродвигателя вследствие зазоров в осевом подшипнике, которые в эксплуатации могут достигать 2 мм и более. Для обеспечения надежности и увеличения срока службы редуктора зубчатое зацепление выполнено с самоустанавливающимся зубчатым венцом упругого колеса. Венец и ведущую шестерню изготавливают из легированных сталей.
2.1.6 Шестерня
Шестерня изготавливается из стали 12Х2Н4А. Поверхности зубьев и впадин шестерен цементируют на глубину 1,6–1,9 мм (после шлифовки) и подвергают закалке до твердости HRC59; твердость сердцевины зуба и обода – HRC35. С целью повышения усталостной прочности при изгибе шестерен исходный профиль впадин зубьев выполняют с выкружками (протуберанцами) и не шлифуют. Продольных скосов зубья шестерен не имеют, как на прежних жестких передачах, а влияние перекоса компенсируется самоустанавливающимся зубчатым венцом упругого колеса. После закалки и шлифовки профиль зуба и впадин шестерни подвергают магнитной дефектоскопии.
Посадка шестерни производится в нагретом до 443 К (170°С) состоянии на конический (конусность 1:10) хвостовик вала якоря тягового электродвигателя с осевым натягом 1,3-1,45 мм. Перед насадкой шестерни на вал сопрягаемые их посадочные поверхности проверяют на прилегание по краске (прилегание должно быть не менее 75%). На валу электродвигателя шестерни от сползания с конуса в нагретом состоянии дополнительно крепят гайкой с моментом затяжки 500 Н•м (50 кгс•м) и контрятся отгибочной шайбой. Для съема шестерни гидрораспрессовкой на торце вала электродвигателя предусмотрено резьбовое отверстие с выходом на сопрягаемую посадочную поверхность под установку специального ручного гидронасоса.
2.1.7 Зубчатое колесо
Зубчатое колесо состоит из зубчатого венца 6, который через упругие элементы 1 и 2 посредством тарелок 19, призонных втулок 4, болтов 11 и гаек 3 соединен со ступицей 20, насаженной на ось колесной пары с натягом 0,16–0,22 мм, и жестко центрирован через ролики 10 по ее сферической поверхности. Момент затяжки болтов крепления тарелок 80 – 90 Н•м (8–9 кгс•м).
Зубчатый венец изготавливают из стали 45ХН. Рабочая поверхность зубьев подвергается секторной закалке токами высокой частоты на глубину 3–5 мм и по высоте 4-б мм от впадины зуба до твердости HRC50, твердость сердцевины зуба и обода венца НВ255-НВ302. Впадины зубьев упрочняют накаткой роликами диаметром 120 мм с усилием 85–95 кН (8500–9500 кгс). После закалки и шлифовки профиль зуба и впадины венца подвергают магнитной дефектоскопии.
Рис. 2.3: Зубчатое колесо: 1, 2 – упругие элементы; 3 – гайка; 4 – призонные втулки; 5, 7, 8, 16, 18 – втулки; 6 – зубчатый венец; 9 – кольцо; 10 – ролик; 11 – болт; 12 – отражательное кольцо; 13 – шайба 14 – полукольцо; 15, 22 – пальцы; 17, 23, 24 – амортизаторы; 19 – тарелка; 20 – ступица; 21 – пружинное кольцо
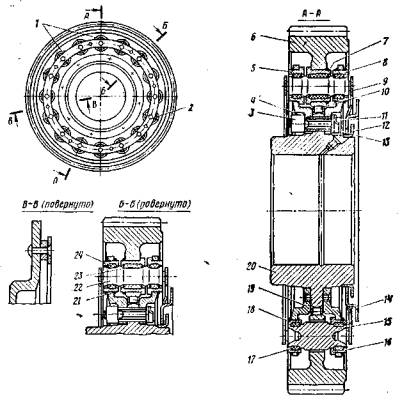
Упругие элементы для получения нелинейной характеристики тангенциальной жесткости зубчатого колеса выполнены разной жесткости двух типов. Восемь элементов 1 (малой жесткости) имеют жесткость (125–135) 104 Н/м (125–135 кгс/мм) и установлены в отверстия диаметром 70 мм тарелок и зубчатого венца по скользящей посадке. Они состоят из пальца 22, на наружную профильную поверхность которого насажены резиновые амортизаторы 24 и 23, предварительно вставленные в металлические втулки 5, 7 и 8. Втулки 5 и 7 выполнены с ограничительными буртами, препятствующими одностороннему свободному осевому перемещению по ним венца.
Поэтому сформированные упругие элементы 1 устанавливают на колесе по четыре ограничительными буртами на каждой стороне зубчатого венца. Упругие элементы в тарелках и венце закрепляют стопорными пружинными кольцами 21.
Восемь других упругих элементов 2 имеют большую жесткость, равную (47–50) 106 Н/м (470–500 кгс/мм). Они установлены в отверстия тарелок по скользящей посадке, а в отверстие венца – с радиальным зазором 4 мм. Упругий элемент 2 также состоит из профильного пальца 15, на концы которого напрессованы резиновые амортизаторы 17, предварительно вставленные в металлические втулки 16 и 18. Для предотвращения сползания втулка 16 имеет ограничительный бурт и проточку, а втулка 18 – две проточки под установку стопорных пружинных колец 21. Необрезиненная поверхность пальца выполнена бочкообразной (радиусом 270 мм).
Все резиновые амортизаторы упругих элементов изготовляют из маслобензостойкой резины. Формирование упругих элементов производится способом запрессовки резиновых амортизаторов в металлическую арматуру, при этом посадочные поверхности предварительно смазывают смесью из 30% касторового масла и 70% этилового спирта. Сформированные упругие элементы для стабилизации сцепления резины с металлом выдерживают в течение 20 дней при температуре 288–303 К (15–30°С) без нагружения и доступа света.
При сборке упругого зубчатого колеса между венцом и ступицей устанавливают без сепаратора 90 роликов 10 размером 15х25 мм, которые обеспечивают относительное поворачивание венца и ступицы через тело качения, жесткую их центровку и разгрузку упругих элементов от радиальных усилий в зубчатом зацеплении тяговой передачи. Для возможности самоустановки зубчатого венца поверхность ступицы под роликами выполнена сферической радиусом 300 мм и упругие элементы сформированы с зазорами до 5 мм между ограничительными буртами втулок. Поверхности венца и ступицы под роликами термообработаны до твердости HRC 48. В целях предотвращения выпадания пальцев 15 и 22 с наружных сторон тарелок прикреплены ограничительные кольца 9. Тарелки, втулки и пальцы изготовлены из стали 45 или 38ХС и термообработаны с целью повышения износостойкости гнезд под упругие элементы.
Передача вращающего момента зубчатым колесом, имеющим упругие элементы разной жесткости двух типов, осуществляется как бы в два этапа: сначала при малом вращающем моменте в работу вступают упругие элементы 1 с меньшей жесткостью, а затем с увеличением вращающего момента (при трогании) венец поворачивается, и при угле поворота примерно Г вступают в работу более жесткие элементы 2. Таким образом обеспечивается требуемая нелинейная характеристика тангенциальной жесткости упругого зубчатого колеса.
Для осмотра состояния деталей упругого зубчатого колеса при ремонтах, а также замены упругих элементов предусмотрена возможность полной его разборки без расформирования колесной пары. Разборка производится в сторону противоположного колесного центра.
Применение в тяговом редукторе упругого зубчатого колеса позволило значительно (в 3 раза) снизить динамические нагрузки, возникающие в зацеплении при движении тепловоза, и, как показал опыт эксплуатации тепловозов, главное – достичь эксплуатационной долговечности зубчатой передачи не менее 1,2 млн. км пробега.
Для создания масляной ванны и предохранения зубчатых колес и шестерен от песка, пыли и других абразивных материалов тяговая зубчатая передача помещена в кожухе.
2.1.8 Кожух тягового редуктора
Кожух тягового редуктора состоит из двух разъемных сварной конструкции половин верхней 1 и нижней 9 с линией разъема по центрам шестерни и зубчатого колеса. Между верхней и нижней половинами кожуха для уплотнения разъема по всему периметру в паз, образованный приваренными изнутри и снаружи верхней половины кожуха накладками 3 и 4, укладывают уплотнительную резиновую трубку 5. Скрепляют две половины четырьмя болтами 7 через прокладки 6 толщиной, обеспечивающей установку уплотнительной трубки по разъему с преднатягом.
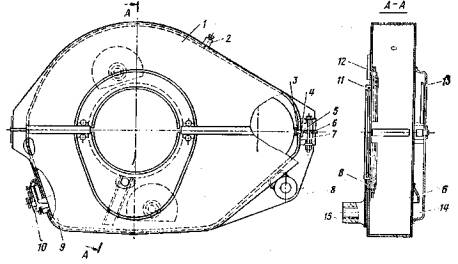
Рис. 2.4:Кожух тягового редуктора
Кожух центрируют горловиной по бурту вкладыша осевого подшипника и жестко крепят к остову тягового электродвигателя в трех точках болтами М42 через две бонки 15, приваренные к несущей боковой стенке вблизи центра зубчатого колеса для восприятия основной массы кожуха, и бонку 8, приваренную на нижней половине к листу и обечайке для обеспечения правильной установки кожуха относительно зубчатого колеса. С помощью прокладок, устанавливаемых под бонки крепления, регулируют зазор между торцами зубчатого колеса и стенками кожуха (который должен быть не менее 8 мм), а также радиальный зазор между ступицей колесного центра и горловиной кожуха (который должен быть не менее 1,5 мм). Регулирование зазоров необходимо из-за износа осевого подшипника в процессе эксплуатации. Момент затяжки болтов должен быть 1400–1600 Н•м (140–160 кгс•м).
Кожух от внешней среды в месте соприкосновения горловины с буртом вкладыша осевого подшипника уплотняют войлочными полукольцами 11, уложенными в пазы горловины, а по отверстию монтажа ведущей шестерни установкой с преднатягом войлочного кольца между стенкой кожуха и подшипниковым щитом тягового электродвигателя. По оси уплотнение кожуха выполнено бесконтактным с дополнительным расширительным коробом 14, который имеет отражательное полукольцо 13 и в нижней части отверстие Б для возврата проникшей смазки снова в полость кожуха. Герметичность сварных соединений кожуха проверяют керосином. Особое внимание уделяют уплотнению между кожухом и осевым подшипником, так как смазки разные и их смешивание резко снижает работоспособность рассматриваемых узлов и особенно польстерного устройства смазки осевого подшипника вследствие замасливания фитилей вязкой смазкой зубчатой передачи. Это уплотнение выполнено бесконтактным лабиринтно-кольцевым, образованным отбойным кольцом на ступице зубчатого колеса и желобом, который удерживается полукольцами 12 (по одному на каждой половине), приваренными внутри на несущей боковине кожуха. На пути уплотнения в нижней части полукольца 12 имеется отверстие В, которое служит для отвода проникшей через уплотнение смазки за пределы кожуха.