Файл: Важную роль играет предприятия Акционерное общество Акционерная компания Железные дороги Якутии.docx
ВУЗ: Не указан
Категория: Не указан
Дисциплина: Не указана
Добавлен: 10.11.2023
Просмотров: 194
Скачиваний: 3
СОДЕРЖАНИЕ
1.1 Оценка качества работ в цехе ТО4
1.2 Оценка уровня механизации в цехе ТО-4
1.3 Выводы и предложения по улучшению производства в цехе
2. РАЗРАБОТКА ТЕХНОЛОГИЧЕСКОГО ПРОЦЕССА РЕМОНТА УЗЛА
2.1.2 Моторно-осевые подшипники
2.1.3 Циркуляционная система смазывания осевых подшипников
2.1.8 Кожух тягового редуктора
2.1.9 Подвешивание тягового электродвигателя
2.2 Работы выполняемые на ТО и ТР
2.3 Организация технологического процесса ремонта узла
2.3.2 Разборка и ремонт колесно-моторного блока
2.3.3 Сборка колесно-моторного блока
3.1 Опыт передовых предприятий по организации производства в цехе
3.2 Экономическая эффективность механизированных позиций
3.3. Основные показатели и преимущества разработанного оборудования
2.3 Организация технологического процесса ремонта узла
2.3.1 предварительные работы
Перед разборкой колёсно-моторного блока и отдельных его сборочных единиц необходимо поставить метки спаренности на половинках кожуха, корпусах моторно-осевых подшипников (МОП), вкладышах. Также при демонтаже следует обеспечивать сохранность всех прокладок, запоминать расположение всех контрольных штифтов и проверять наличие знаков маркировки на деталях.
Перед самой разборкой колёсно-моторный блок подвергается механическому способу очистки, сдувание пыли сжатым воздухом. Этот способ применяется для очистки поверхности от пыли, металлической стружки и других загрязнений. Давление струи воздуха должно быть в пределах Р=0,25-0,35 МПа. разборки все части колёсно-моторного бло-ка проходят очистку в моечной машине ММД-13Б Отчистке подвергаются: колесная пара в сборе, хомут, обе половины кожуха в сборе, корпус подшипника со всеми комплектующими, шестерёнчатый насос в сборе, вкладыши МОП. Они очищаются от обычных загрязнению и от смолистых отложений.
2.3.2 Разборка и ремонт колесно-моторного блока
Зачаленные при разборке тележек колесно-моторные блоки поочередно подают и устанавливают на позицию разборки. Отвернув пробки, спускают смазку из моторно-осевых подшипников в противень. Отворачивают болты, снимают половинки кожухов редукторов, маркируют их метками парности, укладывают в кассеты и транспортируют в моечную машину. После отворачивания болтов демонтируют буксы моторно-осевых подшипников вместе с верхними вкладышами. При этом необходимо убедиться в наличии меток парности, а также меток принадлежности к данному остову тягового двигателя.
Грязную подбивку вынимают из букс и укладывают в контейнер для транспортировки в шерстемоечное отделение. Демонтируют колесную пару и отправляют ее на мойку, а затем в колесный цех. Вынимают нижние вкладыши, буксы моторно-осевых подшипников устанавливают на место и закрепляют болтами, а скомплектованные вкладыши моторно-осевых подшипников отправляют на мойку.
Буксы, моторно-осевую горловину осмотреть, отремонтировать. Протереть ветошью, смоченной керосином, насухо протереть. Осмотреть моторно-осевую горловину ТЭД и обстучать на отсутствие трещин в торцах и углах привалочных плоскостей горловины у отверстий для крепления МОП и в других местах.
Осмотреть корпус буксы МОП, при необходимости проверить её посадку в горловине остова. Замерить расстояние между наружными торцами горловины остова с помощью микрометрического нутромера, в двух крайних местах по длине посадочной поверхности, рассчитать среднее значение (разница замеров определит непараллельность граней пазов, которая не должна превышать более 0,1мм).
Аналогичные замеры с помощью микрометрической скобы произвести для буксы, между посадочными поверхностями-направляющими буксы и подсчитать средний размер- непараллельность должна быть не более 0,005мм. Зазор определится как разница размеров направляющих букс и торцами горловины остова. Зазор должен быть 0-0,1мм
Проверить отсутствие трещин в корпусах букс. При наличии следов течи масла в корпусе буксы, проверить герметичность керосином (покрыть меловым раствором наружную поверхность масляной камеры буксы, установить буксу на подставку и залить в неё керосин).
Замерить толщину приливов остова и проверить метчиком резьбу под болты и отверстия для установки и крепления букс МОП и кожухов редуктора. Осмотреть приливы остова в местах прилегания фланцев буксы. Эти места должны иметь ровную поверхность, обработанную под угольник. Замерить диаметр горловины остова в сборе с буксами при полностью затянутых болтах крепления буксы. Замер производится в двух плоскостях по обе стороны от линии разъема на расстоянии 10 мм и в трёх сечениях по длине опорно-осевой горловины. За фактический размер диаметра принимается среднее значение полусумм диаметров замеренных по сечениям. Для определения конусности горловины произвести замеры в двух взаимно параллельных плоскостях с обоих концов горловины, конусность
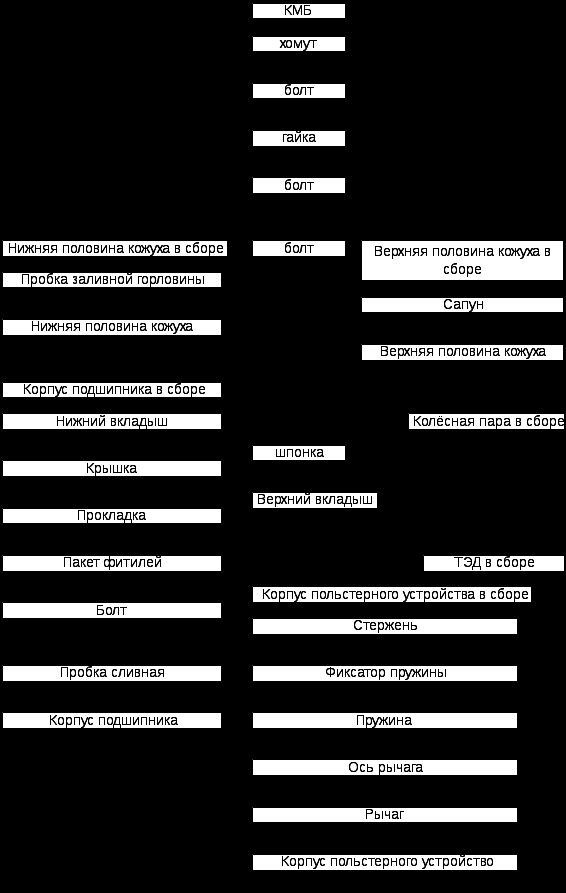
Рисунок 2.6:– Схема разборки узла
определяется как разница средних значений диаметров каждого сечения. Овальность горловины определяется как разность диаметров измеренных в каком-либо сечении в двух взаимно перпендикулярных плоскостях.
Разборку колесно-моторного блока завершают снятием шестерни с вала тягового двигателя при помощи специального пресса. Для этого предварительно пальцевым ключом отворачивают торцовые гайки с вала двигателя. Снятые шестерни свободно навешивают на среднюю часть оси и вместе с колесной парой транспортируют в моечную машину, а затем в колесный цех для осмотра и ремонта. Торцовые гайки от руки наворачивают на свои места и тяговые двигатели транспортируют в электромашинный цех.
Снятые при разборке колесно-моторного блока вкладыши моторно-осевых подшипников клеймят или стягивают хомутами для сохранения парности, обмывают в моечной машине и подают в специализированное ремонтное отделение. В случае износа наружной поверхности вкладыша необходимый натяг восстанавливают методом электролитического меднения или с помощью пресса.
При меднении электролит готовят из водного раствора медного купороса (200—270 г/л) и серной кислоты (30—50 г/л). Токи выбирают в зависимости от плотности электролита. При плотности электролита 1,15; 1,17; 1,19 и 1,20 г/л рекомендуются токи соответственно 270—300, 200—220, 160— 170 и 150—160 А.
Восстановление вкладышей с помощью пресса разрешается выполнять только один раз. После такого восстановления по всей плоскости соединения выполняют ацетилено-кислородную или электродуговую (на постоянном токе) наплавку на 2—3 мм.
Подшипники, не требующие восстановления наружной поверхности, сортируют по марке баббита, который выплавляют в специальной печи. Выплавленный баббит после анализа химического состава и проверки твердости используют в качестве добавки к свежему баббиту. Вкладыши, имеющие трещины или толщину основания менее допускаемой, перезаливать нельзя. Подготовленные к заливке баббитом вкладыши нагревают в электрической печи, смазывают кистью, смоченной соляной кислотой, в которой растворена цинковая стружка, или водным раствором хлористого цинка. Сильно окисленную внутреннюю поверхность вкладыша предварительно протравливают соляной кислотой и зачищают стальной щеткой.
Затем вкладыши нагревают в электрической печи до температуры 260 °С и лудят до получения гладкого блестящего слоя полуды. Для полуды применяют припой ПОС-30. После этого на специальном станке конструкции ПКБ ЦТ выполняют центробежную заливку вкладышей баббитом, находящимся в электротигле и подогретом до температуры 460—500 °С для баббита Б-16 и 400—500 °С для баббита Б-83. Температура нагрева баббита контролируется термопарой. Перед заливкой баббит в тигле тщательно перемешивают. Расплавленный баббит заливают в воронку станка непрерывной ровной струей, ускоряя ее к концу заливки. Продолжительность заливки вкладыша не должна превышать 15—20 с. Станок для центробежной заливки подшипников должен иметь ограждение. При заливке подшипников рабочие должны быть в спецодежде, очках и рукавицах, приточно-вытяжную вентиляцию необходимо включить.
Баббитовая заливка должна плотно прилегать к корпусу вкладыша. Плотность прилегания проверяют обстукиванием молотком, при этом должен быть звонкий, недребезжащий звук. Залитые с припуском подшипники подвергают очистке и механической обработке, перед которой проводят испытание заливки на твердость. Замеренная не менее чем через 3 ч после заливки, она должна быть в пределах 22—30 единиц по Бринеллю.
Изношенный бурт подшипника восстанавливают наплавкой бронзой с последующей обработкой на станке, но чаще восстановление бурта осуществляют заливкой баббитом одновременно с заливкой внутренней поверхности.
Комплект вкладышей растачивают на токарном станке, подгоняя их по шейке оси колесной пары к горловине остова с соблюдением централи. Обычно расточку вкладышей осуществляют на собранном двигателе при помощи переносного станка, монтируемого на остове двигателя.
Тщательная обработка пряжи, применяемой для подачи смазки к моторно-осевым подшипникам, повышает надежность их работы и срок службы. Удаленную при разборке колесно-моторных блоков из шапок моторно-осевых подшипников подбивку складывают в закрытый металлический ящик и транспортируют в шерстемоечное отделение. Первичную очистку подбивки выполняют в масле, подогретом до температуры 30—40 °С, а затем отжимают масло в прессе и центрифуге. Отжатые косы поступают в стиральную машину, где их стирают в масле, подогретом до температуры 80—90 °С, а затем отжимают в резиновых валках и центрифуге.
Масло периодически фильтруют в специальной машине. После центрифугирования выстиранных кос их расплетают, удаляют из них механические примеси, бракуют негодные нити пряжи и вновь заплетают. Косы, сплетенные из новой пряжи, пропитывают индустриальным маслом при температуре 55—60 °С в течение 24 ч, а сплетенные из восстановленной пряжи — в течение 12 ч. После стока масла косы подаются на позицию сборки моторно-осевых подшипников.
Демонтированную при разборке колесно-моторного блока подвеску тягового двигателя обмывают в моечной машине. Затем ее протирают салфетками, смоченными в керосине, и насухо протирают. После этого подвеску осматривают, проверяют резьбу, посадку и размеры втулок и валика, подсчитывают зазор между ними. Суммарный зазор должен быть 1,4—2,3 мм. Изношенную или ослабшую в посадке сферическую втулку заменяют. При этом отверстие в головке подвески проверяют на станке,, после чего запрессовывают новую втулку с натягом согласно чертежу. Диаметр отверстия в головке подвески разрешается увеличивать не более чем на 2 мм по сравнению с чертежным размером, диаметр втулки в таких случаях должен быть соответственно увеличен.
После зачистки валик и подвеску подвергают дефектоскопии; при обнаружении трещин в любом месте они подлежат замене. В случае износа торцовых поверхностей или круглой резьбы на хвостовике подвески допускается их восстановление вибродуговой наплавкой с последующей механической обработкой и дефектоскопией. Таким же образом восстанавливают валики, имеющие выработку.
Просевшие резиновые шайбы, а также шайбы, имеющие трещины, заменяют новыми. Изношенные стальные диски подлежат наплавке, выправке и обработке.
Тяговая передача. Металлические кожуха (верхние и нижние половины) зубчатой передачи тепловоза после обмывки в моечной машине передают в ремонтное отделение. Старые войлочные уплотнения извлекают из обеих половин кожуха, которые затем тщательно осматривают и бракуют негодные. Для обнаружения трещин половины кожухов наполняют керосином и оставляют на 2 ч. Особое внимание обращают на состояние сварных швов. При обнаружении трещин их засверливают по краям, разделывают и заваривают качественными электродами. Если трещина возникла в сварном шве, то сначала срубают старый шов, а затем обрубают кромки листа. Разрешается усиливать боковые листы приваркой бобышек в местах крепления кожуха.
Линейкой проверяют прогиб стенок кожуха. Если он превышает норму, стенки правят, предварительно подогревая деформированное место газовой горелкой. После окончания сварочных работ необходимо убедиться в отсутствии течи в кожухе. Для этого в него наливают керосин, который не должен просачиваться. В случае обнаружения течи необходимо вновь разделать и заварить место течи.
Состояние резьбы бобышек проверяют калибром или болтом. Если резьба имеет повреждения, ее необходимо восстановить метчиком. Ремонт кожуха заканчивается набивкой в пазы войлочных уплотнений. После ремонта кожуха окрашивают, причем для окраски внутренних поверхностей следует использовать маслостойкую краску или эмаль.
При сборке устанавливают сначала нижние половины кожухов и закрепляют их так, чтобы выдержать установленное расстояние от внутренней грани бандажей колесной пары до наружной боковой стенки кожухов, а также зазор между стенками кожухов и торцовыми поверхностями зубчатых колес и шестерен. Для регулирования положения кожухов на болты между остовом двигателя и кожухом разрешается ставить шайбы. После установки верхних половин кожухов затягивают стяжные болты и заправляют кожуха зимой осерненной смазкой марки 3, а летом Л.