Файл: Курсовая работа по метрологии, стандартизации и сертификации Вариант хх выполнил обучающийся иоб 23 аэл группы.doc
Добавлен: 09.01.2024
Просмотров: 121
Скачиваний: 3
ВНИМАНИЕ! Если данный файл нарушает Ваши авторские права, то обязательно сообщите нам.
В данном случае: наружное кольцо нагружено местным нагружением, а внешнее – циркуляционно.
3.3 Расчет и выбор посадок
Для циркуляционно нагруженных колец посадку можно выбрать более определенно по интенсивности радиальной нагрузки на посадочной поверхности PR (2.1) [1]:
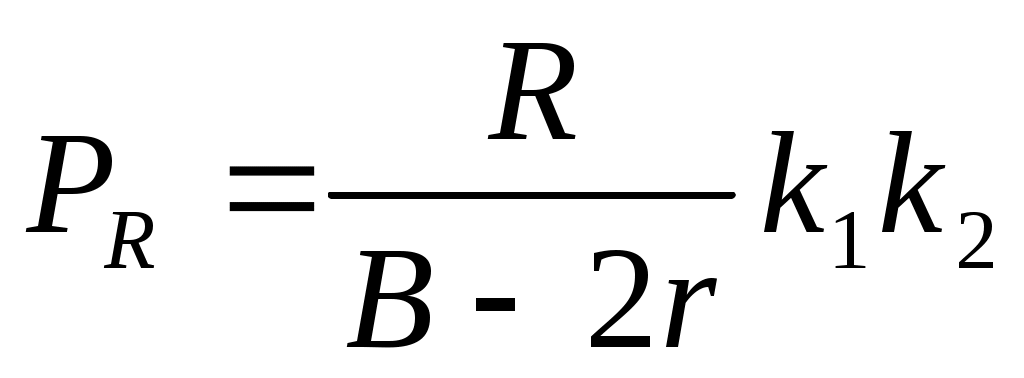
где, R – расчетная радиальная нагрузка на опору, Н;
В – ширина кольца подшипника, м;
r – радиус монтажных фасок, м;
k1 – динамический коэффициент посадки, зависящий от характера нагрузки. Выбирается по таблице 2.2 [1];
k2– коэффициент, учитывающий степень ослабления посадочного натяга при полом вале или тонкостенном корпусе (при сплошном вале или неразъемном корпусе k2 =1). Выбирается по таблице 2.3 [1].
Для 0-го класса точности по таблице 2.7 [1] находим предельные отклонения диаметра отверстия внутреннего кольца – Ø50L0(-0,012) и диметра наружной поверхности наружного кольца – Ø110l0(-0.015).
Рассчитываем интенсивность радиальной нагрузки Pr на посадочной поверхности вращающегося циркуляционно нагруженного внутреннего кольца. Предварительно по таблице 2.2 устанавливаем значение коэффициента k1 = 1, а значение коэффициента k2 = 1.6.
Тогда
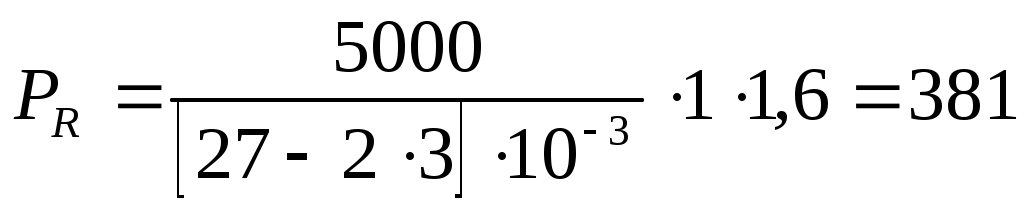
По таблице 2.4 [1] выбираем поле допуска отверстия корпуса Ø110,М7(
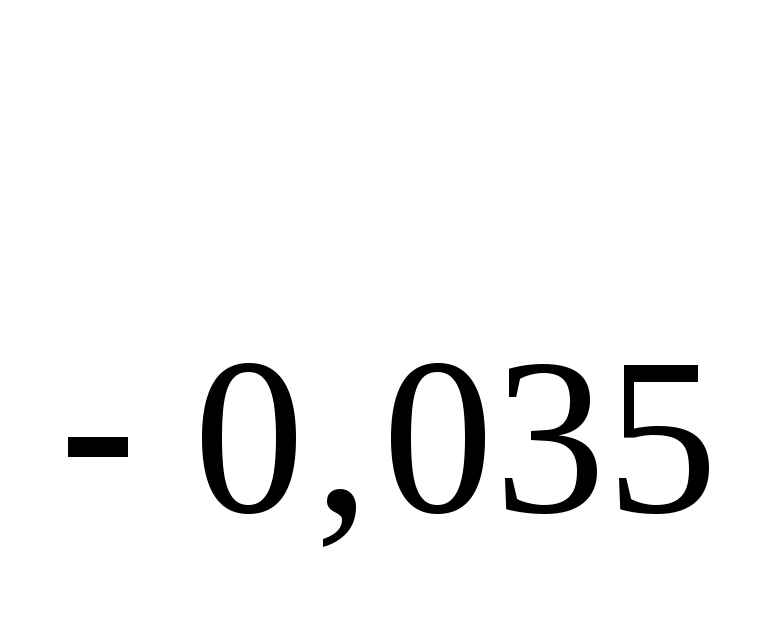
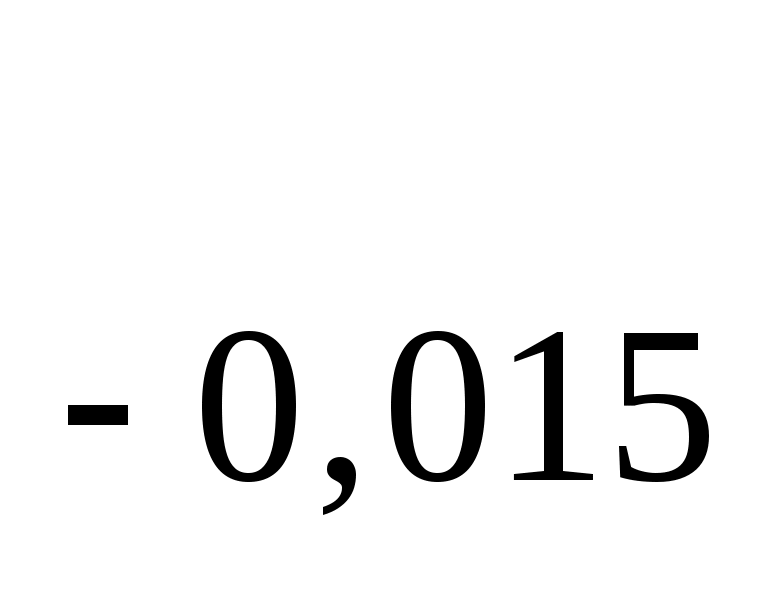

где em= 0,5(es-ei) и Em=0,5(ES-EI) – средние отклонения соответственно вала и отверстия внутреннего кольца, мкм.
Для посадки не вращающегося внутреннего кольца подшипника, воспринимающего местное нагружение, выбираем по таблице 2.6 [1] поле допуска вала Ø50h6(
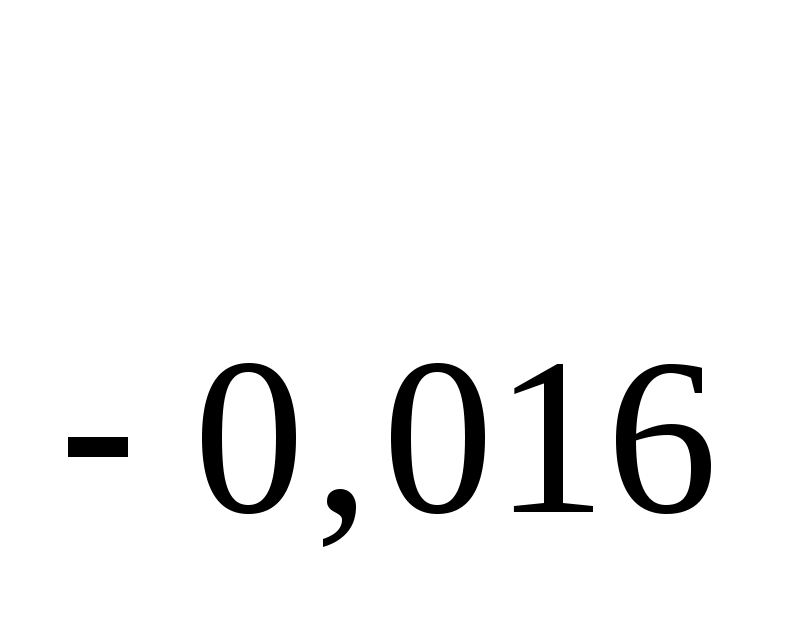
), образующее с полем допуска отверстия внутреннего кольца L0(-0.012) посадку со средвероятным зазором:

3.4 Определение посадочного радиального зазора
Для нормальной работы подшипника необходимо, чтобы между кольцами и телами вращения был зазор. При изготовлении подшипника обеспечивают начальный зазор, размер которого регламентирован. После посадки циркуляционно нагруженного кольца на вал или корпус с натягом, начальный зазор из-за деформации уменьшается.
Пользуясь формулой (2.2) [1], определяем наличие радиального посадочного зазора
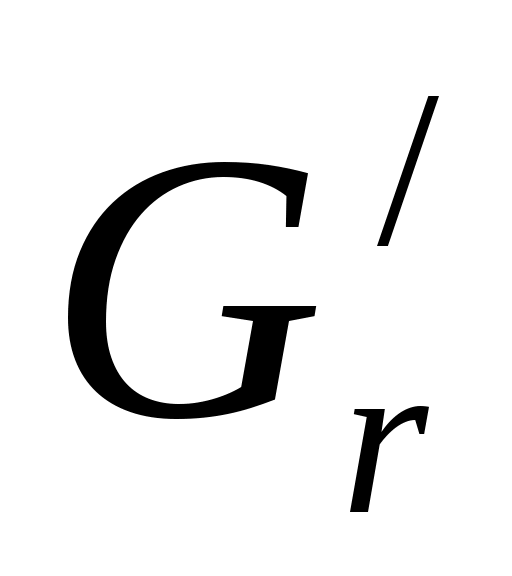

Предварительно по таблице 2.5 [1] находим начальные радиальные зазоры
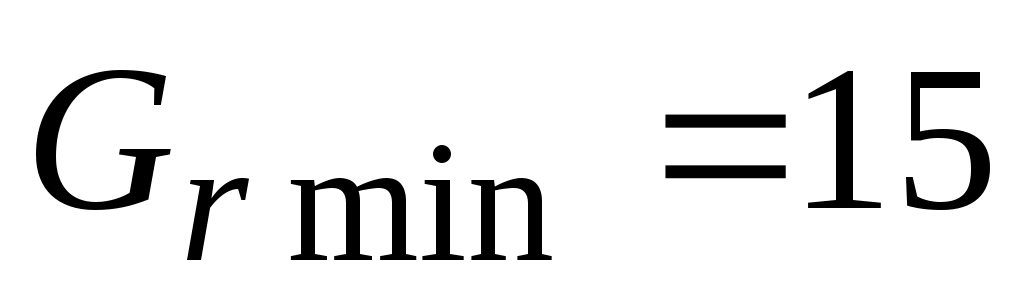
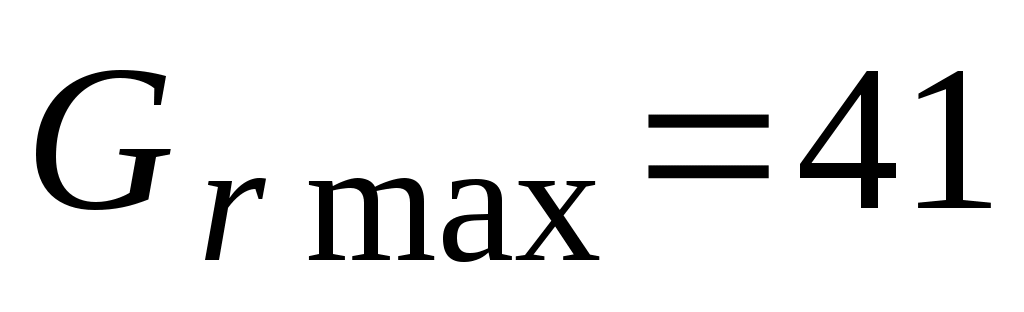

Устанавливаем значение эффективного посадочного натяга по формуле (2.5) [1]:

приведенного наружного диаметра внутреннего кольца по формуле (2.6) [1]:

и диаметральной деформации его дорожки качения по формуле (2.4) [1]:

Тогда

Следовательно, при намеченной посадке после установки подшипника на вал, в нем сохраняется зазор, который и является посадочным радиальным зазором.
3.5 Схема расположения полей допусков


Рисунок 3.1 – Схемы расположения полей допусков
3.6 Эскизы подшипникового узла и сопрягаемых деталей
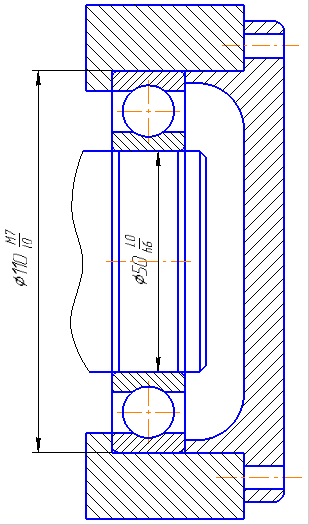
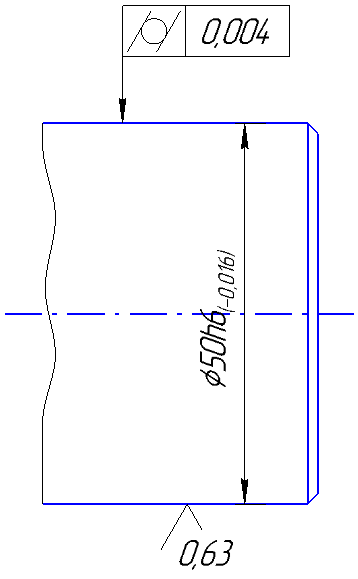
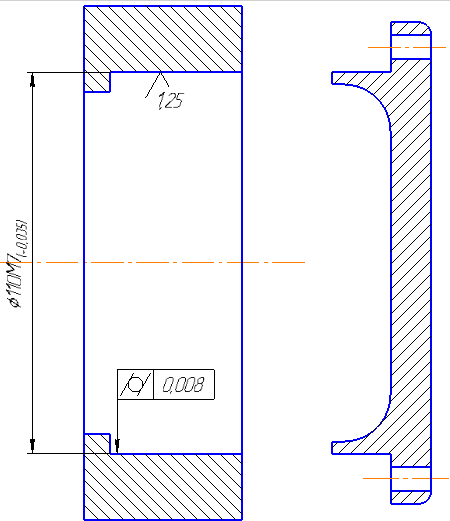
4 РАСЧЕТ ТОЧНОСТНЫХ ПАРАМЕТРОВ РЕЗЬБОВОГО СОЕДИНЕНИЯ
4.1 Задание и исходные данные
Исходные данные сведем в таблицу 4.1
Таблица 4.1 – Исходные данные
Параметр | Обозначение | Значение |
Шаг резьбы, мм | Р | 1,25 |
Поле допуска | d2 | 6g |
d | 6g | |
D2 | 7H | |
D1 | 7H | |
Резьба | М14 | - |
Требуется:
-
Записать условное обозначение по ГОСТу и расшифровать основные параметры резьбового соединения, болта и гайки. -
Определить номинальные размеры и предельные отклонения наружного, среднего и внутреннего диаметров болта и гайки. -
Дать эскиз профиля с указанием основных параметров и полей допусков резьбового соединения.
Метрические резьбы разделяются на две группы: с крупным шагом, с мелким шагом. У резьбы с крупным шагом каждому диаметру соответствует определенный шаг, а у резьбы с мелким шагом для каждого диаметра могут назначаться различные шаги. Резьбу с крупным шагом применяют для соединений, работающих при постоянных нагрузках, а с мелким – при переменных нагрузках и вибрациях.
Номинальным размером резьбы, одинаковым для наружной (болта, шпильки, винта и др.) и внутренней (гайки, резьбового отверстия и т.д.), является наружный диаметр d(D). Кроме наружного диаметра профиль резьбы определяется следующими размерами: внутренний диаметр резьбы d1(D1), средний диаметр резьбы d2(D2), высота Н исходного треугольника, рабочая высота профиля Н1, шаг резьбы Р, угол профиля резьбы α.
На работу резьбового соединения небольшое влияние оказывают отклонения шага, угла профиля и среднего диаметра, т.к. они определяют характер контакта резьбового соединения. Но назначать допуски и контролировать все эти параметры чрезвычайно сложно и трудоемко. Поэтому для удобства контроля и расчета допусков введено понятие «приведенный средний диаметр» резьбы. Допускаемые отклонения шага и угла профиля нормируют, а устанавливают только суммарный допуск на средний диаметр натужной Td2 и внутренней TD2 резьбы, который включает отклонения собственного среднего диаметра и диаметральные компенсации отклонений шага и угла профиля.
Обозначение поля допуска диаметра резьбы состоит из цифры, показывающей степень точности, и буквы, обозначающей основное отклонение (4h ,6h, 7h). Обозначение поля допуска резьбы или гайки состоит из обозначения поля допуска среднего диаметра, помещенного на первом месте, и обозначения поля допуска диаметра выступов (7g6g, 4h5h). Если обозначения поля допуска диаметра выступов совпадает с обозначением поля допуска среднего диаметра, его в обозначении поля допуска резьбы не повторяют. Поле допуска резьбы указывают через тире после размера, например, болт М10-7g6g, гайка М12-7Н, болт 12х1-6g. Посадки резьбовых деталей обозначают дробью, в числителе которой указывают поле допуска гайки, а в знаменателе – поле допуска болта: М14-
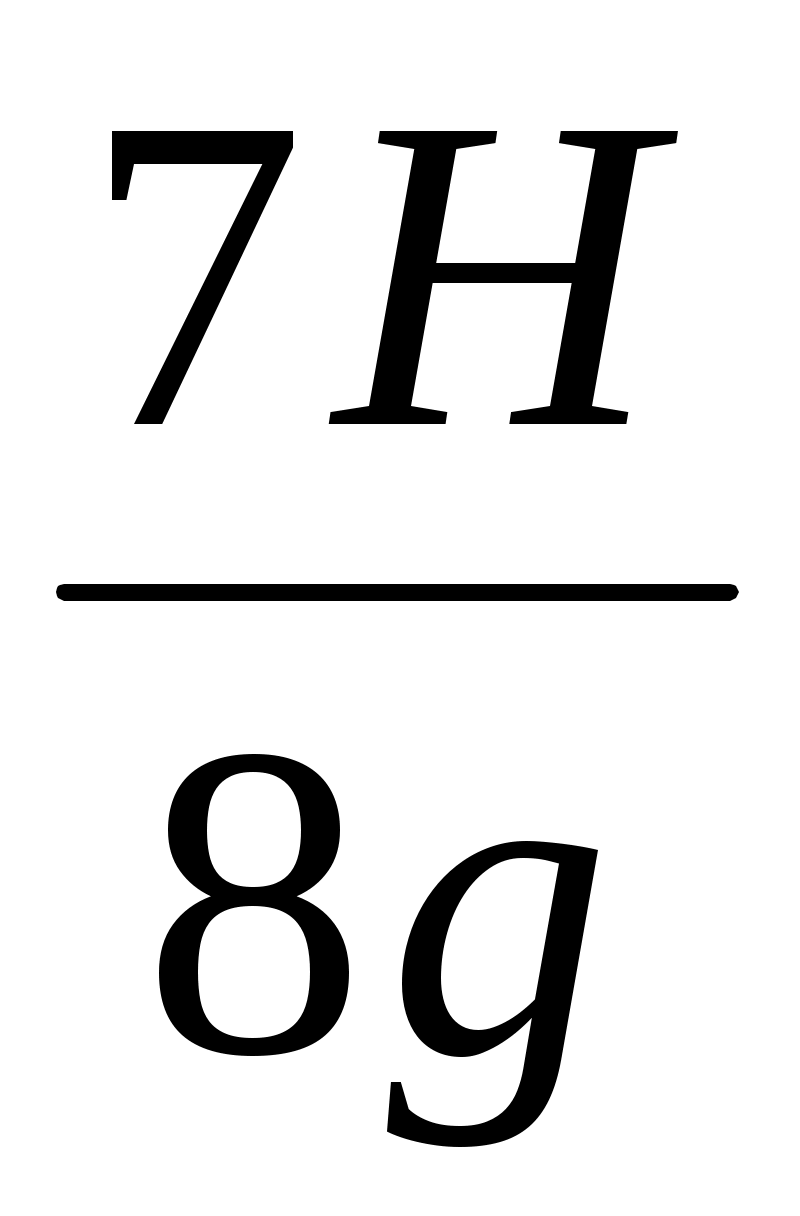
При графическом изображении допусков резьбы началом отсчета отклонений диметров служит номинальный профиль, общий для наружной и внутренней резьбы. Отсчет ведется в направлении, перпендикулярном оси резьбы.
Для метрической резьбы диаметром 14 мм, с шагом Р=1.25 мм, выписываем номинальные диаметры по ГОСТ 24705-81 [1]:
наружный -
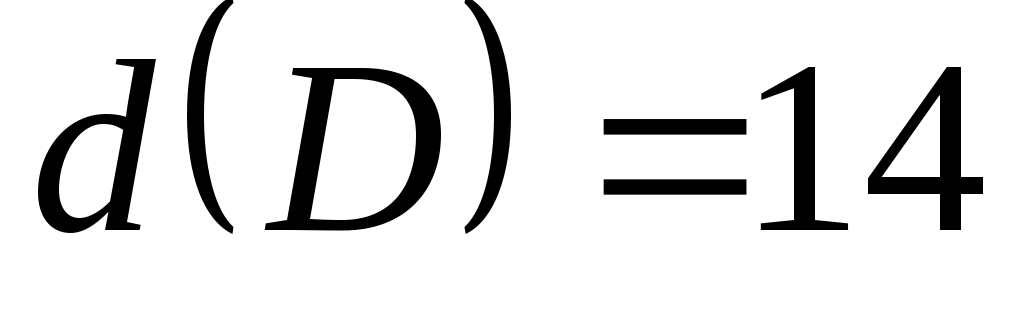
средний -
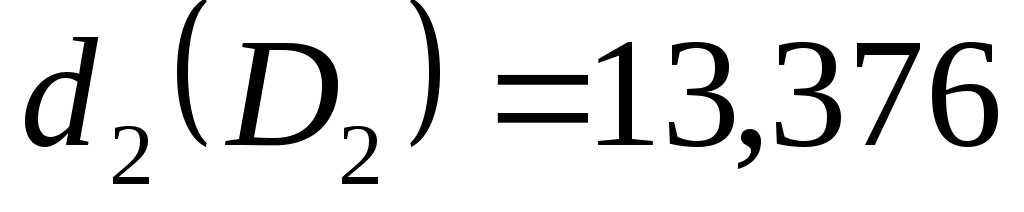
внутренний -

4.2 Определение номинальных размеров и предельных отклонений
Пользуясь, ГОСТ 16093-81 для резьбы с номинальным диаметром d(D)=24 мм и шагом Р = 2 мм, находим предельные отклонения диаметров резьбы болта с полем допуска 4h:
es= -0.028 мкм (для d,d1,d2)
ei = -0,363 мкм (для d)
ei = -0,240 мкм (для d2)
и предельные отклонения диаметров резьбы гайки с полями допусков 5G:
EI = 0 (для D,D1,D2)
ES = +0,224 мкм (для D2)
ES = +0,335 мкм (для D1)
Предельные диаметры и допуски резьбы болта рассчитываем по формулам:
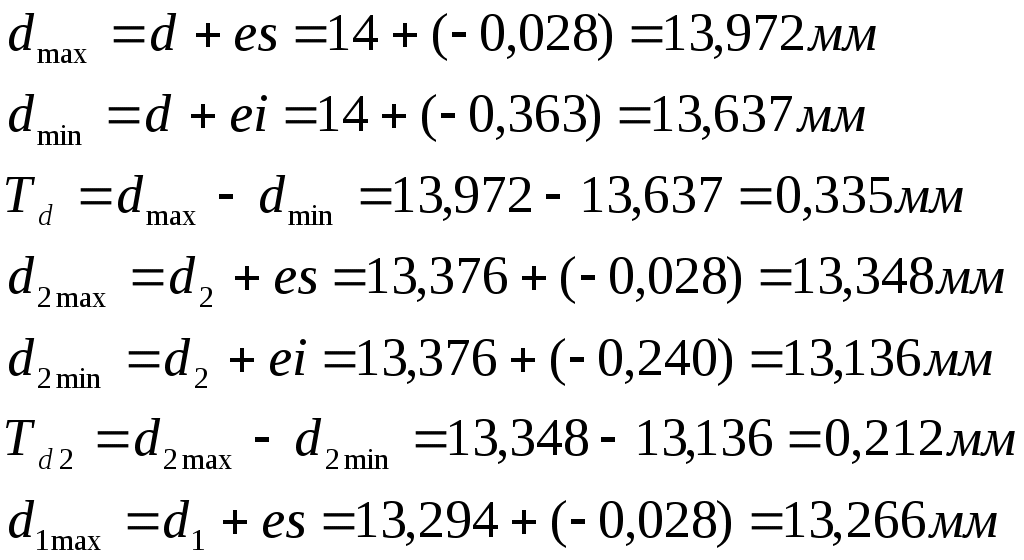
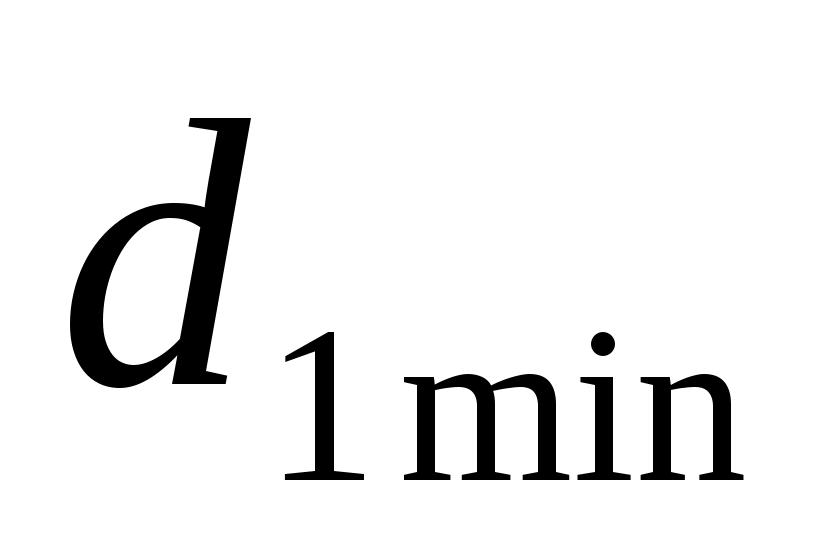
Предельные параметры и допуски резьбы гайки рассчитываются по формулам:
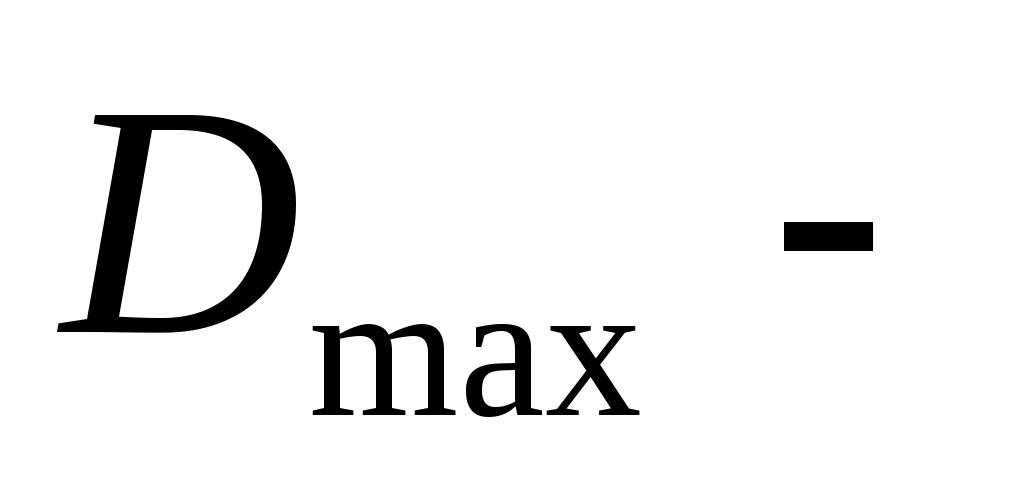
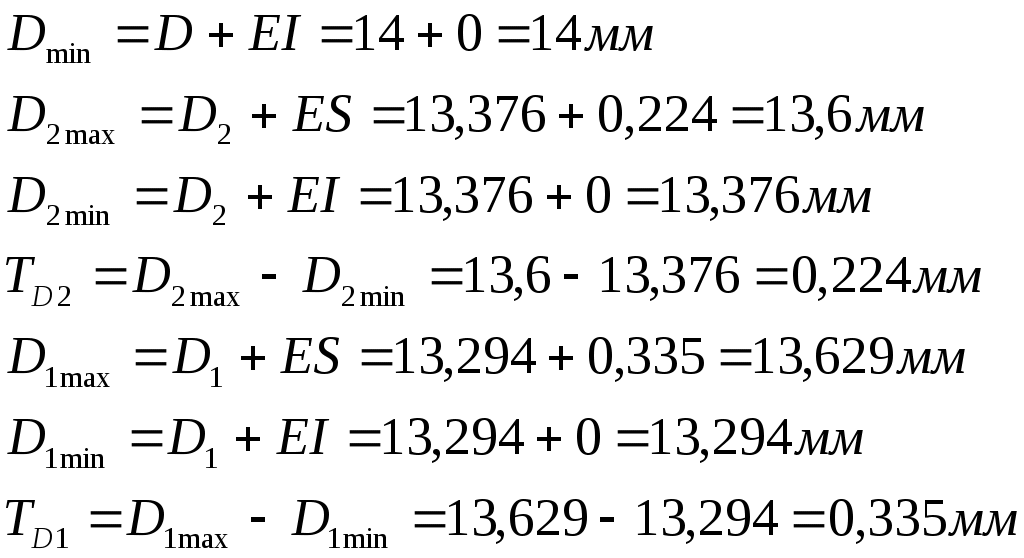
4.3 Эскиз профиля
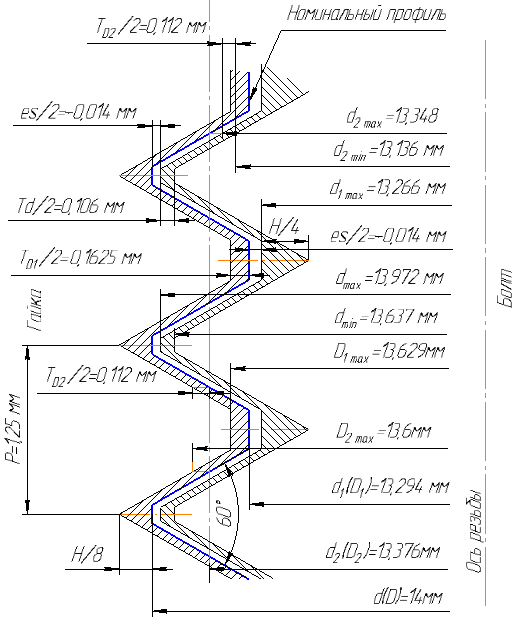
5 ВЫБОР ПОСАДОК ШПОНОЧНЫХ СОЕДИНЕНИЙ
5.1 Задание и исходные данные
Исходные данные сведем в таблицу 5.1.
Таблица 5.1 – Исходные данные
Параметр | Обозначение | Значение |
Тип шпонки | Призматическая | - |
Вид соединения | Свободное | |
Условия работы | Точное центрирование | - |
Диаметр вала, мм | dn | 9 |
Требуется:
-
Определить основные размеры шпоночного соединения. -
Выбрать поля допусков соединения по номинальному размеру dn «вал-втулка». -
Выбрать поля допусков деталей шпоночного соединения по ширине шпонки -
Назначить поля допусков и определить предельные отклонения остальных размеров шпоночного соединения. -
Дать схему расположения полей допусков шпоночного соединения по размеру ширины шпонки. -
Определить предельные зазоры и натяги в соединениях: по номинальному размеру dn, по ширине шпонки. -
Вычертить эскизы шпоночного соединения и его деталей с указанием основных размеров и полей допусков, параметров шероховатости.
Шпонки являются соединительным звеном между вращающимися деталями и валом или осью. Из всего разнообразия конструкции шпоночных соединений в автотракторном и сельскохозяйственном машиностроении наиболее распространены призматические и сегментные шпонки.
Поля допусков шпоночного соединения по номинальному размеру dn «вал-втулка» устанавливают в зависимости от условий работы.
Выбор полей допусков деталей шпоночного соединения по ширине шпонки зависит от вида соединения. Стандарт предусматривает три вида соединений по ширине шпонки: плотное, нормальное, свободное. Каждому из этих видов соединений соответствует определенный набор полей допусков на ширину шпонки, ширину паза вала и паза втулки.
По таблице 5.2 [1] определяем размер деталей соединения.
При dn = 9 мм:
ширина сегментной шпонки – b =3 мм;
высота – h = 3 мм;
интервалы длин l= 6…36
глубина паза на валу – t1 = 1,8мм;
глубина паза во втулке – t2 = 1,4 мм;
5.2 Выбор поля допусков «вал-втулка».
По таблице 5.3 [1] при больших точном центрировании выбираем поля допусков по размеру dn =9 мм, принимаем для втулки Н6, для вала m6.
5.3 Выбор поля допусков по ширине шпонки.
По таблице 5.4 [1], назначаем поля допусков по ширине шпонки при плотном соединении:
по ширине шпонки – h9;
по ширине паза вала – Н9;
по ширине паза втулки – D9.
5.4 Поля допусков и предельные отклонения остальных размеров
Определяем поля допусков на остальные размеры деталей шпоночного соединения и заносим их в форму 1.
Форма 1 – Размерные характеристики деталей шпоночного соединения
Наименование размера | Номинальный размер, мм | Поле допуска | Допуск размера Т, мм | Предельные отклонения, мм | Предельные размеры, мм | ||
верхнее ES(es) | нижнее EI(ei) | max | min | ||||
1 | 2 | 3 | 4 | 5 | 6 | 7 | 8 |
Ширина паза вала | 3 | Н9 | 0,025 | +0,025 | 0 | 3,025 | 3,000 |
Ширина паза втулки | 3 | D9 | 0,025 | +0,045 | +0,020 | 3,045 | 3,020 |
Ширина шпонки | 3 | h9 | 0,025 | 0 | -0,025 | 3,000 | 2,975 |
Глубина паза вала | 1,8 | H12 | 0,100 | +0,100 | 0 | 1,900 | 1,800 |
Высота шпонки | 3 | h11 | 0,060 | 0 | -0,060 | 3,000 | 2,940 |
Глубина паза втулки | 1,4 | H12 | 0,100 | +0,100 | 0 | 1,500 | 1,400 |
Диаметр втулки | 9 | H6 | 0,009 | +0,009 | 0 | 9,009 | 9,000 |
Диаметр вала | 9 | m6 | 0,009 | +0,015 | +0,006 | 9,015 | 9,006 |
Длина шпонки | 10 | h14 | 0,360 | 0 | -0,360 | 10,000 | 9,640 |
Длина паза вала | 10 | Н15 | 0,580 | +0,580 | 0 | 10,580 | 10,000 |
5.5 Схема расположения полей допусков по ширине шпонки

Рисунок 5.1 – Схема расположения полей допусков шпоночного соединения
5.6 Определение предельных зазоров и натягов
Предельные зазоры и натяги в соединениях «шпонка-паз вала» и «шпонка-паз втулки» определяем как в гладких соединениях. Для рассматриваемого примера:
в соединении по ширине «шпонка-паз вала»:
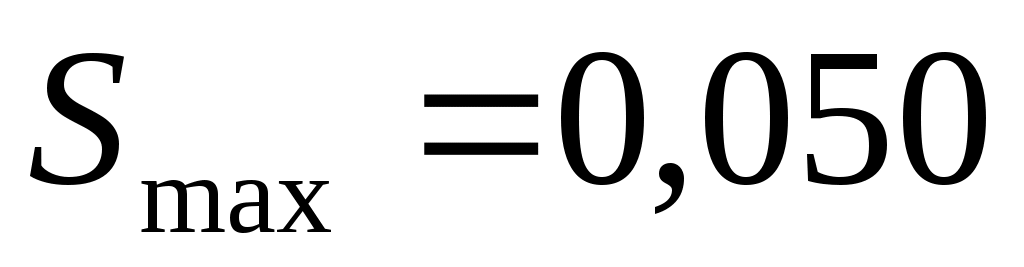
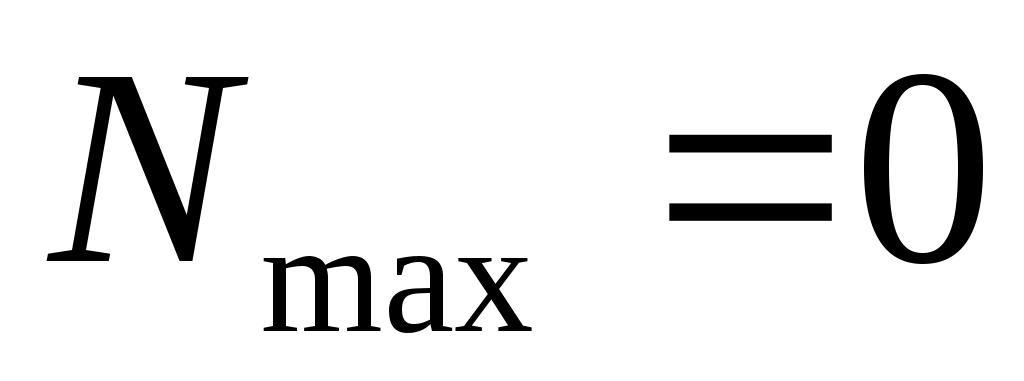
в соединении по ширине «шпонка-паз втулки»:
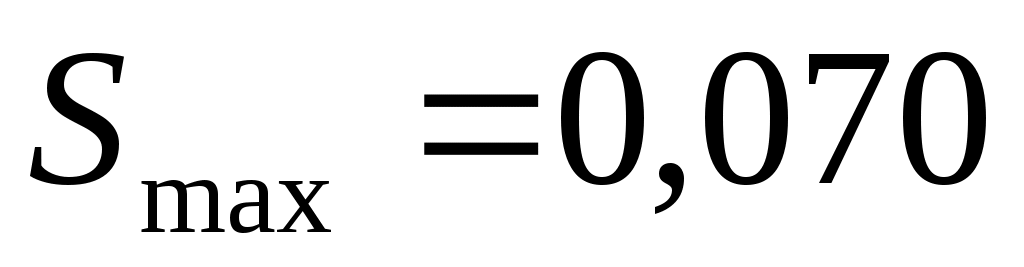
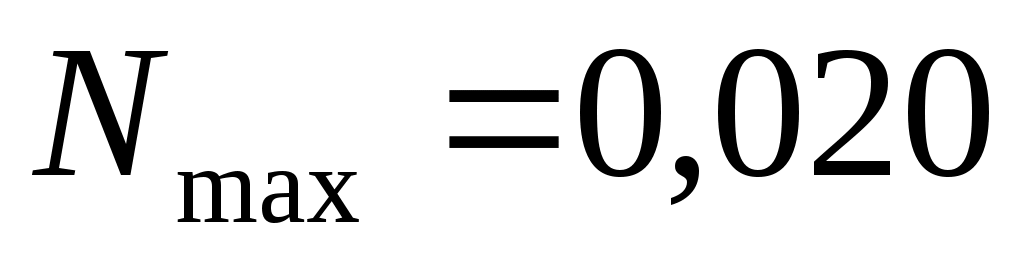
в соединении по диаметру «вал-втулка»:
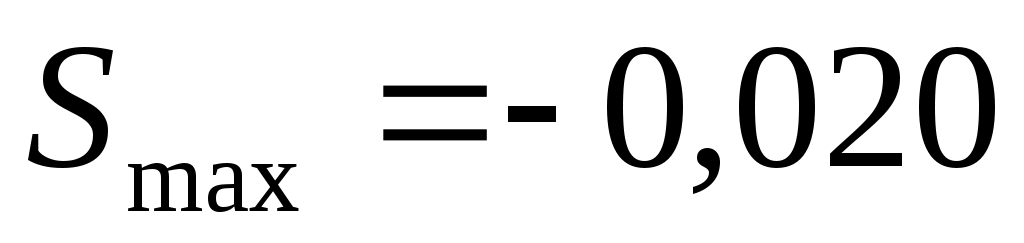
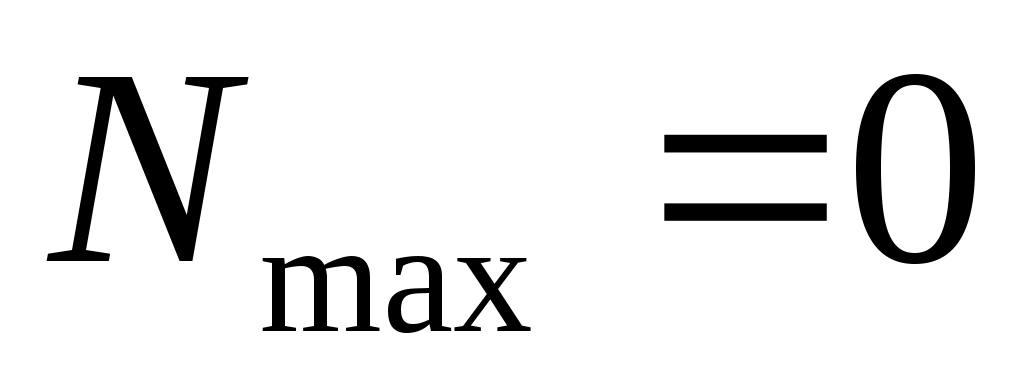
5.7 Эскиз шпоночного соединения и его деталей
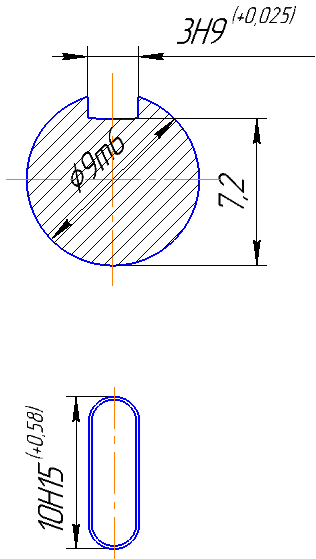
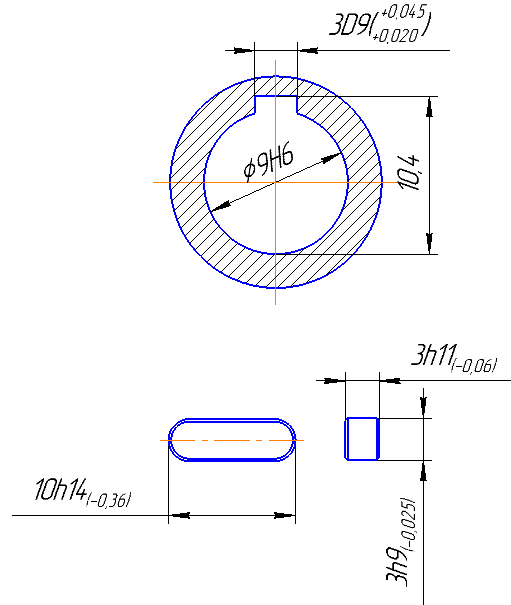
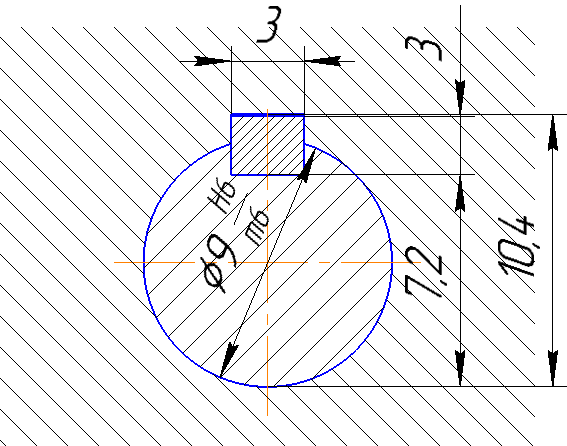