Файл: Описание ремонтируемого оборудования. 1 Общие сведения.docx
ВУЗ: Не указан
Категория: Не указан
Дисциплина: Не указана
Добавлен: 25.10.2023
Просмотров: 210
Скачиваний: 1
ВНИМАНИЕ! Если данный файл нарушает Ваши авторские права, то обязательно сообщите нам.
Проверить размер (ОТК, шаблон).
Наварить зуб по шаблону (сварочный трансформатор ТС-500, электрод).
Снять защиту и медный шаблон (верстак, слесарный инструмент).
Проверить размер (ОТК, Зубомер).
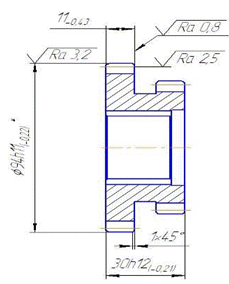
Рис.8 Эскиз базовой детали - блок-шестерни.
.3.3 Ремонт вала
Дефектом вала является износ шлицев на 10%.
Метод хромирования позволяет увеличить срок службы детали и её износостойкость во много раз больше, чем осталивания.
Хромирования - процесс электромагнитного наращивания металла на ремонтированные детали. Он осуществляет в обогреваемой ванне наполненной электролитом. Электролит представляет собой раствор, состоящий из хромового ангидрида, серной кислоты и дистиллированной воды. Восстанавливаемую деталь подвешивают в ванне на специальную подвеску, подсоединяют к отрицательному полюсу источника постоянного тока. В ванне вместе с деталью подвешивается определённое количество пластин из сплава свинца и сурьмы, присоединенных к положительному полюсу источника тока. Таким образом, пластина, общая площадь которых должна быть в 2-5 раз больше, чем покрываемая хромом площадка детали, пластины служат анодам. Не подлижащие хромированию места изолируют, покрывая смолой или лаком. Толщина хромированного слоя 0,25.
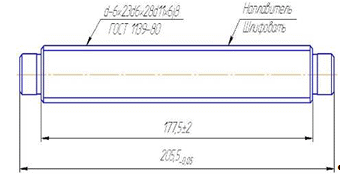
Рис.9 Эскиз базовой детали - вал.
Перед ремонтом шлицевого вала его необходимо промыть, очистить от пыли, грязи в моечной ванне. Затем производим шлифование на станке 3М151 кругом ГОСТ 4785-84 до выведения следов износа. Подготовить шлицевый вал к хромированию, все поверхности, не подлежащие
хромированию, покрытию, покрывают бумагой. Хромирование поверхность шлицев в гальванической ванне с электролитом. После хромирования убирают бумагу и проверить толщину покрытия микрометром МК-I. Шлифовать шлицы на станке 3М151 шлифовальным кругом Гост 4785-84, выдерживая размеры согласно чертежу, и производим проверку шлицев шлицевым кольцом.
.3.4 Ремонт втулки
Дефектом втулки является износ отверстия корпуса под подшипник 0,25мм.
При ремонте втулки его необходимо промыть, очистить от пыли, грязи в моечной ванне. Затем произвести наплавку электродуговую УОНИ 13/15. На токарно-винторезном станке 16К20 сверлим отверстие сверлом


ГОСТ 2092-77, производим закалку ТВЧ и проверяем все размеры штангенциркулем ШЦ-II-125 ГОСТ 166-89.
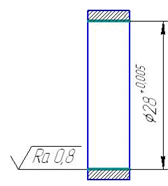
4. Конструкторская часть
.1 Расчет и проектирование приспособления
Универсальный съёмник предназначен для снятия шкивов, шестерен и подшипников диаметром от 70 до 200 мм
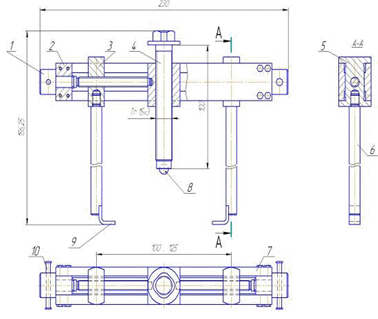
)Винт
)Упор
)Направляющая
)Болт
)Гайка
)Стержень
)Планка
)Шарик
)Лапки
) Стержень
.2 Разработка схемы строповки
Величина натяжения каждой ветви каната определяется в зависимости от числа ветвей, на которых подвешен груз и угла наклона к вертикали.

где, G-вес груза; m=3005 кг; g=10



где, к- число ветвей каната=20; cos- угол наклона ветвей каната=20

Определяем коэффициент запаса прочности


Определяем разрывное усилие


По разрывному усилию подбираем канат ГОСТ 2688-80
Канат тип ТК 19+1 ОС
Предел временной прочности материальной поверхности
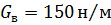
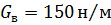
Диаметр каната


А=260 мм
Напряжение материальной поверхности
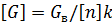



=27
Принимаем канат типа ТК 19+1 Ос, он удовлетворяет условиям прочности, так как


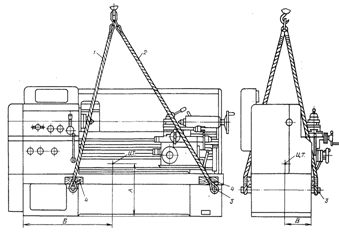
5. Организационная часть
.1 Организация рабочего места слесаря-ремонтника
В ремонтном цехе обычно устанавливаются многоместные верстаки с расстояниями между тисками 1,2 м, а для ремонта громоздких изделий устанавливаются металлические столы.
Инструмент и детали должны размещаться на рабочем месте так, чтобы рабочий не совершал лишних движений. На верстаке укладываются только те предметы, которые требуются для выполнения данной работы: с левой стороны кладется инструмент, который берется левой рукой, а с правой который берется правой рукой; посередине верстака укладывается измерительный инструмент; вся документация помещается на видном месте для удобства пользования. Плита для правки деталей устанавливается с правой стороны верстака, а для контроля с левой стороны на столе верстака. Заготовки укладываются с левой стороны тисков, а обработанные детали с правой стороны. Стеллажи для хранения деталей и узлов устанавливаются так, чтобы рабочему не приходилось затрачивать лишнее время на переходы от стеллажа к верстаку.
Рабочее место слесаря-ремонтника должно хорошо освещаться, содержаться в чистоте и оснащаться необходимыми грузоподъемными механизмами. Сжатый воздух для распылителя жидкого металла подается в пистолет из компрессора через воздухосборник.
.2 Организация технического контроля при ремонте
Как было показано выше
, диагностирование состояния конструкций производственных оборудования промышленных предприятий, по своей сути, является процессом определения их технического состояния и включает в себя поиск дефектов, технический контроль диагностических признаков; анализ и обработку результатов контроля. При этом каждое оборудование рассматривается как сложная техническая система с заранее заданными эксплуатационными качествами, которые контролируются в процессе изготовления конструкций, деталей и узлов; монтажа; при приемке и в ходе эксплуатации; а также перед постановкой объекта на капитальный ремонт, реконструкцию или списание. Только на основе такого полного технического контроля процесс эксплуатации объекта становится управляемым.
.3 Техника безопасности и противопожарные мероприятия
Перед началом работы на токарном станке следует произвести его внешний осмотр и проверить состояние направляющих; правильность регулировки клиньев; состояние зажимов подвижных исполнительных органов; убедиться в отсутствии повреждений на пульте управления и других узлах; проверить систему смазывания станка. Включить насосы смазки и гидростанцию станка на 15...20 мин для прогрева масла. Убедиться в соответствии перемещений исполнительных органов положениям органов управления на пульте в наладочных режимах. Проверить правильность перемещений исполнительных органов от переключателей и кнопок ручного управления на всех режимах. Опробовать работу станка в автоматическом режиме. Первый рабочий ход должен быть вспомогательным (без обработки заготовки). Заготовку установить в приспособление, а режущий инструмент в шпиндель станка. Убедиться, что заготовка и приспособление не заденут при работе выступающие части станка. Установить требуемую частоту вращения шпинделя. Переключать скорости шпинделя на ходу запрещается. Гильзу шпинделя следует зажимать одной рукояткой. Второй зажим (гаечным ключом) используют при тяжелых режимах работы. Зажим стола используют только для его неподвижной фиксации. Выбрать направление вращения шпинделя. Нажать на кнопку «Общий пуск», далее на кнопку «Шпиндель пуск», затем на кнопку «Воспроизведение». После нажатия на кнопку «Общий стоп» (для повторного запуска станка) нужно нажать на кнопку «Подать напряжение» на пульте станка. При переходе на различные режимы работы необходимо следить за правильной установкой переключателя режимов работы.