Файл: Реферат выпускная квалификационная работа выполнена на.docx
Добавлен: 26.10.2023
Просмотров: 292
Скачиваний: 4
ВНИМАНИЕ! Если данный файл нарушает Ваши авторские права, то обязательно сообщите нам.
| |||||||||
| Максимальный размер области реконструкции, мм | 256 по горизонтали×256 по глубине | | ||||||
Рабочие частоты, МГц | 1,0; 1,5; 1,8; 2,0; 2,5; 3,0; 4,0; 5,0 | ||||||||
Тип дисплея | TFT SVGA (640х480) | ||||||||
Размер дисплея | 5,7'' | ||||||||
Диапазон рабочих температур | от –30°С до +45°С | ||||||||
Питание | встроенный аккумулятор /сетевое 110-240В | ||||||||
Память | Встроенная флэш память на 8 Гб | ||||||||
Разъемы для подключения антенных решеток и преоб- разователей | LEMO | ||||||||
Разъем для связи с персональным компьютером | USB | ||||||||
Время непрерывной автономной работы, ч | не менее 8 | ||||||||
Габаритные размеры, мм | 258 × 164 × 110 | ||||||||
Масса электронного блока, кг | 2,7 | ||||||||
Не допускаются внутренние дефекты сварных швов газовые и шлаковые включения, трещины, непровары, смещения. Изделия имеющие дефекты переда- ются на стенд исправления дефектов с последующим повторным контролем. – Гидравлическими испытаниями; При этом методе испытания в сосуде после наполнения его водой или дру- гой жидкостью с помощью насоса или гидравлического пресса создают избыточ- ное давление. Давление при испытании обычно в 1,1 ... 1,5 раза больше рабочего. Давление определяют по проверенному и опломбированному манометру. Испы- тываемый сосуд под давлением выдерживают в течение 5 ... 10 мин. За это время швы осматривают на отсутствие подтекания, капель и отпотеваний. Испытания наливом воды выполняют для открытых сосудов, резервуаров для хранения нефти, газгольдеров. Время выдержки емкости, заполненной водой, до начала осмотра от 1 ... 2 ч и более. Подтекание воды обнаруживают по струй- кам и отпотеванию, а также по снижению уровня воды. Испытание проводят по- вышением давления до 1,27 МПа, при этом баллон не должен деформироваться. Объём баллона проверяют наполнением водой до основания при вертикаль- ном положении баллона и определяют объём или массу (с последующим пересчё- том в объём) воды. После испытания баллон просушивают. Если при испытании используют воду с температурой не ниже 60С, процесс сушки не обязателен. | |||||||||
| | | | | ДП44.03.04.605ПЗ | Лист | |||
| | | | | 51 | ||||
Изм. | Лист | № документа | Подпись | Дата |
Допускается определять объём баллона другими способами, обеспечивающими необходимую точность. В основе радиографического метода выявления дефектов лежат законы ослабления ионизирующего излучения веществом и способы регистрации интен- сивности излучения объектом, который просвечивается. Радиографический контроль проводится с целью выявления в сварных со- единениях внутренних дефектов (трещин, непроваров, пор, шлаковых включений и т.п.). Контроль сварных соединений узлов нефтепровода выполняет только спе- циалист, который прошел специальную теоретическую подготовку и практиче- ское обучение, а также – аттестацию в установленном порядке. Среди всех возможных разновидностей, радиографический контроль свар- ных соединений является одним из самых точных. Он очень востребован в про- фессиональной сфере, где производятся качественные изделия, рассчитанные на большую нагрузку. В них, как правило, не допускается наличие каких-либо не- проваренных мест, микротрещин, раковин, пор и прочих видов брака. Далеко не все из них можно выявить визуально, поэтому, применяется именно такой способ контроля качества. Он относится к неразрушающему типу, поэтому, изделия по- сле осмотра можно вводить в эксплуатацию. Рисунок 1.18 - Радиографический контроль сварных соединений Радиографический контроль сварных соединений основан на принципе прохождения гамма лучей, а также рентгеновского излучения сквозь твердые по- | ||||||
| | | | | ДП44.03.04.605ПЗ | Лист |
| | | | | 52 | |
Изм. | Лист | № документа | Подпись | Дата |
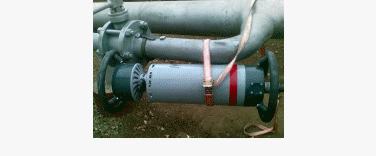
верхности. При прохождении лучи сталкиваются с материалом и лишь часть из них проходит. Если в сварном шве есть поры, раковины и прочие дефекты, со- здающие неоднородность структуры, то в них будет проходить большее количе- ство лучей, чем в остальных участках. Это помогает точно выявить не только наличие брака, но и его размеры, тип и место расположения. Фиксируются ре- зультаты на специальной пленке, что является еще одним преимуществом данно- го метода. Данная процедура проводится по ГОСТ 7512-86. Преимущества: Один из самых точных методов неразрушимого контроля; Позволяет выявлять скрытые дефекты; Благодаря ему, можно точно определить размеры и место расположения проблемного участка; Проводится за относительно короткий промежуток времени, так что не нужно будет долго ждать результатов; Радиографический метод сварных соединений является самым современ- ным способом проведения контроля, который предназначен для ответственных объектов. Рисунок1.19 - РАП 160-5 - переносной рентгеновский аппарат | ||||||
| | | | | ДП44.03.04.605ПЗ | Лист |
| | | | | 53 | |
Изм. | Лист | № документа | Подпись | Дата |
Основным назначением переносного рентгеновского аппарата РАП-160-5 является неразрушающий контроль изделий, материалов, сварных соединений направленным пучком рентгеновского излучения. Кроме этого, аппарат может быть использован и для других целей, где требуется пучок рентгеновского излу- чения с максимальной энергией до 160 кВ. Аппарат может использоваться как в стационарных, так и нестационарных условиях (производственные цеха, строи- тельные и монтажные площадки, полевые условия). Аппарат имеет санитарно- эпидемиологическое заключение №77.99.24.427.Д.008991.07.07 от 31.02.2007г. Проверкаквалификациисварщиков Квалификацию сварщиков проверяют при установлении разряда, при до- пущении к выполнению ответственных работ. В каждом случае проверяют как теоретические задания, так и практические навыки. Разряд усиливают согласно требованиям, предусмотренным тарифно- квалификационными справочниками. Испытания сварщиков производят по пра- вилам аттестации специальной комиссии, создаваемой на заводе. Сварщику вы- дают удостоверение, в котором указывают конструкции, которые может свари- вать сварщик. Контрольтехнологическогопроцессасварки Перед тем, как приступить к сварке, сварщик знакомиться с технологиче- скими картами. Несоблюдение порядка наложения швов может вызвать значи- тельную деформацию изделия, трудно устранимую в последствии. Не менее важным является соблюдение режима сварки. После окончания сварки швы за- чищают от шлака, наплывов, а поверхность узла – от брызг металла [24]. Каждый производственный процесс предполагает определенные отклоне- ния от требований технический норм. Если такие отклонения выходят за преде- лы установленных допусков для конкретного изделия — это брак, дефект, кото- рый должен быть устранен. Если устранение дефекта невозможно, изделие не может быть принято к эксплуатации. В сварочном производстве изделием явля- ется правильно сваренное изделие, узел, конструкция. В изделиях, выполненных | ||||||
| | | | | ДП44.03.04.605ПЗ | Лист |
| | | | | 54 | |
Изм. | Лист | № документа | Подпись | Дата |
сваркой, дефекты различаются по месту их расположения и по причинам воз- никновения. Рассмотрим их. Причины возникновения дефектов — это те, воз- никновение которых связано с неправильной подготовкой и сборкой элементов, нарушением режима сварки, неисправностью оборудования, небрежностью и низкой квалификацией сварщика и другими нарушениями технологического процесса. К дефектам этой группы относятся: Несоответствие швов расчетным размерам; Непровары; Подрезы; Прожоги; Наплывы; Не заваренные кратеры. Дефекты по причинам их возникновения связаны с явлениями, происхо- дящими в процессе кристаллизации и формирования самой сварочной ванны и окончательного формирования шва. Это и трещины в самом шве и в околошов- ной зоне, шлаковые включения, поры. Дефекты по месту их расположения — это трещины и поры, выходящие на поверхность металла, непровары, прожоги, подрезы, наплывы — все они отно- сятся к наружным дефектам и могут быть обнаружены внешним осмотром, как показано на рисунке 26. К внутренним дефектам относятся те же трещины, не- провары, включения и поры, но находящиеся внутри шва и не выходящие на по- верхность. Их обнаруживают только методами неразрушающего контроля. | ||||||
| | | | | ДП44.03.04.605ПЗ | Лист |
| | | | | 55 | |
Изм. | Лист | № документа | Подпись | Дата |
1− Непровар; 2 − Трещины; 3 − Несплавления; 4 − Шлак; 5 − Поры; 6 − Непровар; 7 − Подрезы; 8 − Трещины; 9 − Поры; 10 − Наплыв; 11 − Шов неравномерной формы; 12 − Прожог; 13 − Кратер Рисунок 1.20 − Внутренние (А) и наружные (Б) дефекты сварных швов Следующая разновидность дефекта — неравномерность шва. Появляется дефект по причине неустойчивого режима сварки, неточного направления элек- трода. Если это автоматизированная сварка, то причины в колебании напряжения в сети, проскальзывание проволоки в подающих роликах, протекание жидкого металла в зазоры, неправильный угол наклона электрода Наплывы образуются в результате натекания жидкого металла на кромки холодного основного металла. Наплывы образуются чаще всего при выполнении горизонтальных швов на вертикальной плоскости. Причиной их может быть большой сварочный ток, слишком длинная дуга, неправильный наклон электрода, большой угол наклона изделия при сварке на спуск. Подрезы представляют собой продолговатые углубления-канавки, образо- вавшиеся в основном металле вдоль края шва. Они возникают в результате боль- шого сварочного тока и длинной дуги, так как при этом возрастает ширина шва и | ||||||
| | | | | ДП44.03.04.605ПЗ | Лист |
| | | | | 56 | |
Изм. | Лист | № документа | Подпись | Дата |
сильнее оплавляются кромки. При выполнении угловых швов нельзя допускать смещения электрода в сторону вертикальной стенки. Непроваром называется местное не сплавление кромок основного металла. А также несплавление между собой отдельных швов при многослойной сгарке. Причинами образования непрваров являютсяшлохая зачистка металла от окали- ны, ржавчины и грязи, малый зазор при сборке малый угол скоса кромок, боль- шая скорость сварки. При автоматической сварке под флюсом непровары, как правило, образуются в начале шва, когда основной металл еще недостаточно про- грет. Поэтому сварку надо начинать со специальных выводных планках. Трещины являются наиболее опасными дефектами швов. Они могут возни- кать как в самом шве, так и в околошовной зоне. Причинами их образования яв- ляются внутренние напряжения, возникающие в процессе сварки. На образование трещин влияет повышенное содержание углерода, способствующего закалке, а также серы и фосфора. Сера увеличивает склонность металла к образованию го- рячих трещин, а фосфор – холодных. Шлаковые включения образуются в результате плохой зачистки кромок де- талей и поверхности сварочной проволоки от окалины, ржавчины и грязи. Шла- ковые включения ослабляют сечение шва и уменьшают его прочность. Газовые поры появляются в швах вследствие того, что газы, растворенные в жидком ме- талле, при быстром охлаждении шва не успевают выйти наружу и остаются в нем в виде пузырьков. Для исключения этого дефекта нельзя допускать использова- ния влажного или отсыревшего флюса, наличия ржавчины, масла и краски на кромках основного металла и сварочной проволоки, большой скорости сварки. К дефектам микроструктуры относятся: повышенное содержание оксидов и различных неметаллических включений, микропоры, крупнозернистость, пере- грев, пережог. Причиной образования пережога является плохая защита свароч- ной ванны от кислорода воздуха, а также сварка на чрезвычайно большом сва- рочном токе. | ||||||
| | | | | ДП44.03.04.605ПЗ | Лист |
| | | | | 57 | |
Изм. | Лист | № документа | Подпись | Дата |