Файл: Курсовой проект по дисциплине "Режущий инструмент и инструментальное обеспечение автоматизированного производства".docx
ВУЗ: Не указан
Категория: Не указан
Дисциплина: Не указана
Добавлен: 26.10.2023
Просмотров: 227
Скачиваний: 4
СОДЕРЖАНИЕ
1 Разработка инструментальной наладки
1.2 Разработка маршрутной технологии
1.3 Выбор режущего инструмента
1.4 Выбор вспомогательного инструмента
1.6 Настройка инструментального блока вне станка
2 Разработка конструкции дискового долбяка
2.1 Патентно-информационный поиск. Назначение, типы, описание конструкции долбяков
2.2 Расчет геометрических и конструктивных параметров дискового долбяка
3 Разработка конструкции сборного проходного резца с СМП
3.1 Патентно-информационный поиск. Назначение, типы, описание конструкции токарных резцов
3.2 Расчет геометрических и конструктивных параметров
4 Разработка конструкции сверла с СМП
4.1 Патентно-информационный поиск. Назначение, типы, описание конструкции сверл
4.2 Расчет геометрических и конструктивных параметров сверла
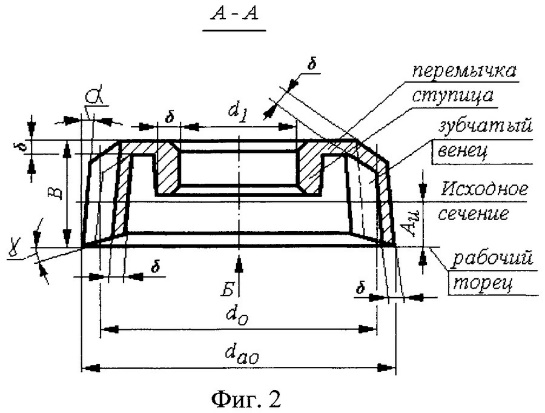
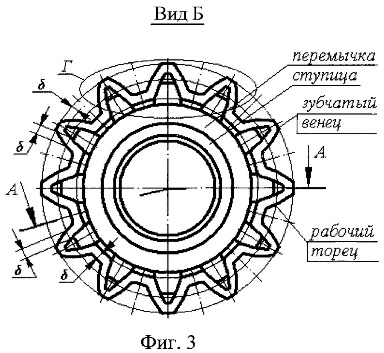
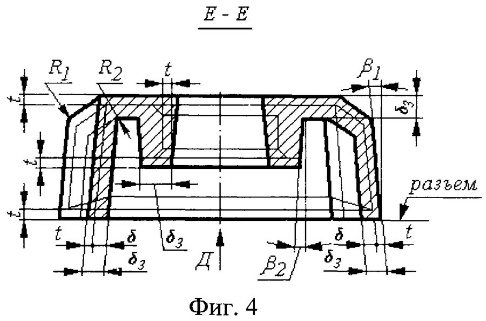
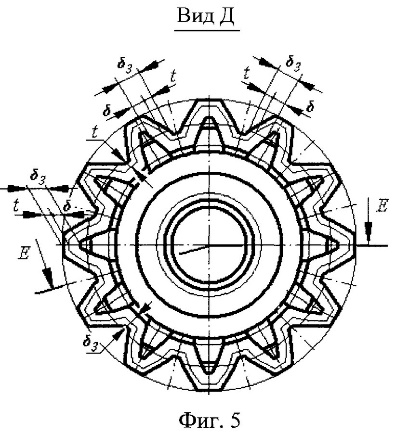
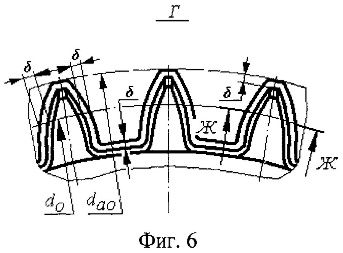

Рисунок 2.3 – Иллюстрации к патенту № 2443518
2.1.2 Назначение, типы, описание конструкции долбяков
Зуборезный долбяк представляет собой совокупность большого количества элементарных зубчатых колес с бесконечно малой шириной обода, имеющих соответственно положительную, нулевую и отрицательную коррекцию, закрепленных на одной оси и имеющих передние и задние углы. Каждое из этих элементарных колес образовано огибающим движением рейки с профильным углом а, и поэтому любое сечение долбяка, перпендикулярное к его оси, имеет один и тот же эвольвентный профиль. По мере переточки долбяка по передней поверхности в работу резания и в зацепление с нарезаемым колесом вступает одно из этих бесконечно тонких зубчатых колес с соответствующей величиной смещения контура. Поэтому колеса, сформированные различными сечениями долбяка, будут иметь один и тот же эвольвентный профиль.
По конструкции долбяки делятся на дисковые, чашечные и хвостовые. Для нарезания прямозубых колес применяются прямозубые долбяки, для косозубых и шевронных — косозубые. Применяются долбяки для нарезания зубьев на блочных колесах и на колесах с буртами, колес внутреннего зацепления, шевронных колес с непрерывным зубом без канавки для выхода инструмента, точных зубчатых реек методом огибания.
В соответствии с ГОСТ 9323-79 изготавливаются долбяки следующих типов (рис. 2.4):
-
дисковые прямозубые классов точности АА, А и В; -
дисковые косозубые классов точности А и В с номинальными углами наклона зубьев 15° и 23°; -
чашечные прямозубые классов точности АА, А и В с номинальными делительными диаметрами 80,100 и 125 мм, а также классов точности А и В с номинальным делительным диаметром 50 мм; -
хвостовые прямозубые классов точности А и В; -
хвостовые косозубые классов точности В с номинальными углами наклона зубьев 15° и 23°.
Долбяки класса точности АА предназначены для нарезания колес 6-й степени точности, а классов А и В — соответственно для колес 7-й и 8—11-й степеней точности.
Рекомендации по выбору основных конструктивных элементов чистовых долбяков приведены в табл. 10.40 – 10.44 [1].
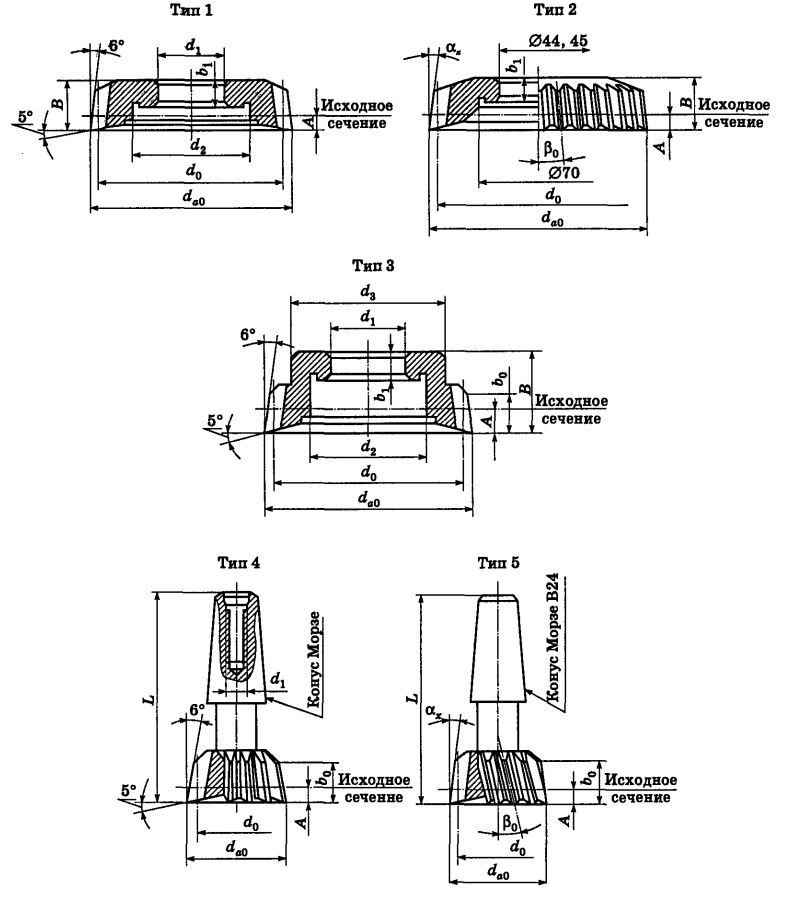
Рисунок 2.4 – Конструктивные разновидности долбяков
2.2 Расчет геометрических и конструктивных параметров дискового долбяка
Исходные данные:
Угол зацепления =20;
Модуль m=3.5 мм;
Номинальный делительный диаметр d0ном=75 мм;
Число зубьев нарезаемого колеса z1=34;
Число зубьев сопряженной шестерни z2=54;
Колесо прямозубое =0, зацепление наружное;
Степень точности колеса – 8;
Коэффициент высоты головки зуба ha*=1;
Коэффициент радиального зазора с*=0.25;
Коэффициент смещения исходного контура x1=x2=0.
Расчет основных параметров нарезаемых шестерни и колеса [1, с.816]:
1. Делительный диаметр:
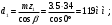
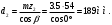
2. Высота головки зуба:

3. Диаметр окружности вершин зубьев:


4. Коэффициент радиального зазора:

5. Высота ножки зуба:

6. Высота зуба:


7. Диаметр окружности впадин зубьев:


8. Толщина зуба на делительном диаметре:

Расчет долбяка[1, 1. 900-909]:
1. Так как нарезаемое колесо имеет 8-ую степень точности, то по ГОСТ 9323-79 выбираем класс точности долбяка – B. Материал режущей части – сталь Р6М5 по ГОСТ 19265-73.
2. Число зубьев долбяка
Делительный диаметр долбяка d0ном=75 мм.
Тогда

Примем z0=23.
3. Уточненный делительный диаметр

4. Передний угол долбяка примем a
=5.
5. Задний угол по ГОСТ 9323-79 примем a=6.
6. Фактический угол профиля долбяка:


7. Боковой задний угол в сечении по делительному цилиндру:


Задний угол на боковых сторонах зубьев в нормальном сечении:


8. Основной диаметр долбяка:

Определение размеров долбяка в исходном сечении:
9. Толщина зуба долбяка на делительной окружности:

где sy=0.1 – величина утолщения зубьев долбяка для образования бокового зазора при чистовой обработке нарезаемых колес.
10. Высота головки зуба:

11. Высота ножки зуба:

12. Диаметр окружности выступов долбяка в исходном сечении:

13.Толщина зуба долбяка на наружном диаметре в исходном сечении:
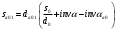



14. Минимально допустимая по условию механической прочности толщина зуба нового долбяка на наружном диаметре:

15. Исходное расстояние, обеспечивающее заданную толщину зуба sa0 на вершине

где x*0 – коэффициент смещения исходного контура долбяка. По ГОСТ 9323-79 принимаем x*0=0.1 мм.
Тогда

Принимаем А=3.3 мм.
16. Принятое значение исходного расстояния проверяется на отсутствие интерференции с переходными кривыми колеса и шестерни.
Проверка долбяка с выбранным исходным расстоянием на отсутствие интерференции с переходными кривыми у нарезаемых им колес выполняется только для шестерни.
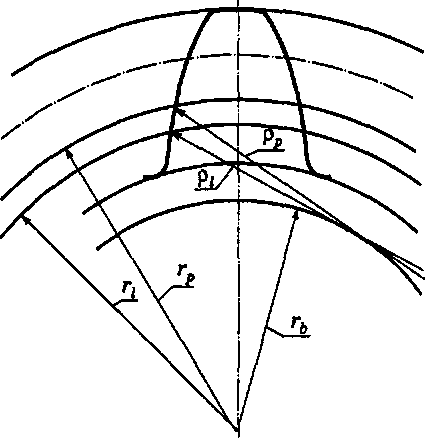
Рисунок 2.5 - Схема для определения радиусов кривизны профиля
зуба шестерни
Интерференция отсутствует, если выполняется условие ρр1>ρn (рис. 2.5),
где ρр1 — радиус кривизны активного профиля зуба шестерни в нижней начальной контактной точке при внешнем зацеплении ее с колесом:

rb2 - радиус основной окружности колеса

ρl1 - радиус кривизны эвольвентного профиля зуба шестерни в точке начала переходной кривой при нарезании ее долбяком (рис. 2.4)
Межосевое расстояние в зубчатой передаче

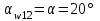
Угол профиля зуба долбяка в точке на окружности выступов

Для шестерни

где r2 — радиус делительной окружности колеса,

ra2 — радиус окружности вершин колеса.



Тогда

Величина ρl1 определяется следующим образом

где rb0 — радиус основной окружности долбяка,
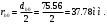
Угол зацепления в станочном зацеплении определяется по формуле
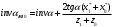
где x1*и x0* - коэффициенты смещения соответственно для шестерни и долбяка. При