Файл: Растворитель используется в производстве эпоксидной смолы.docx
ВУЗ: Не указан
Категория: Не указан
Дисциплина: Не указана
Добавлен: 07.11.2023
Просмотров: 62
Скачиваний: 2
ВНИМАНИЕ! Если данный файл нарушает Ваши авторские права, то обязательно сообщите нам.
Барабанные
Барабанные мешалки (рисунок 4) состоят из двух цилиндрических колец, соединенных между собой вертикальными лопастями прямоугольного сечения. Высота мешалки составляет 1,5 -1,6 ее диаметра. Мешалки этой конструкции создают значительный осевой поток и применяются (при отношении высоты столба жидкости в аппарате к диаметру барабана не менее 10) для проведения газо - жидкостных реакций, получения эмульсий и взмучивания осадков.
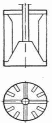
Рисунок 5 – Барабанная мешалка
[6,с.263]
Дисковые
Дисковые мешалки (рисунок 5) представляют собой один или несколько гладких дисков, вращающихся с большой скоростью на вертикальном валу. Течение жидкости в аппарате происходит в тангенциальном направлении за счет трения жидкости о диск, причем сужающиеся диски создают также осевой поток. Иногда края диски делают зубчатыми. Диаметр диска составляет 0,1 - 0,15 диаметра аппарата. Окружная скорость равна 5 - 35 м/с, что при небольших размерах диска соответствует очень высоким числам оборотов. Потребление энергии колеблется от 0,5 кВт для маловязких сред, до 20 кВт для вязких смесей. Дисковые мешалки применяют для перемешивания жидкостей в объемах до 4м3.
![]() Рисунок 6 – дисковая | |
[6,с.262]
Вибрационные мешалки имеют вал с закрепленными на нем одним или несколькими перфорированными дисками (рисунок 5). Диски совершают возвратно-поступательное движение, при котором достигается интенсивное перемешивание содержимого аппарата. Энергия, потребляемая мешалками этого типа, невелика. Они используются для перемешивания жидких смесей и суспензий преимущественно в аппаратах, работающих под давлением. Время, необходимое для растворения, гомогенизации, диспергирования при использовании вибрационных мешалок, значительно сокращается. Поверхность жидкости при перемешивании этими мешалками остается спокойной, воронки не образуется. Вибрационные мешалки изготовляются диаметром до 0,3 м и применяются в аппаратах емкостью не более 3

![]() | |
Рисунок 7 - Устройство дисков вибрационных мешалок
Выбор того или иного типа мешалок определяется целевыми назначением перемешивающих устройств и конкретными условиями протекания процесса. Какие-либо четкие рекомендации по этому вопросу не могут быть сформулированы. Поэтому при выборе того или иного типа перемешивающего устройства можно использовать ориентировочные характеристики условий целесообразного применения различных типов мешалок.
[6, с.262]
В процессе производства эпоксидной смолы основной продукт является маловязким, поэтому выбираем листовую мешалку. Но габариты аппарата составляют 6219 мм в высоту и 2600 мм в диаметре, поэтому устанавливаем трехъярусную листовую мешалку с отверстиями для снятия напряжения, которая обеспечивает эффективный массо- и теплообмен.
2 Описание конструкции разрабатываемого оборудования
2.1 Описание технологического процесса
Приготовление конденсационного раствора производится в растворителе (поз. Р), оборудованном мешалкой, рубашкой, обратным холодильником (поз. Т) , в межтрубное пространство которого подается холодная вода.
Перед загрузкой эпихлоргидрина в растворитель (поз. Р) подается холодная вода в межтрубное пространство обратного холодильника (поз.Т).
При приготовлении конденсационного раствора при производстве смолы марок ЭД-16, Э-40 эпихлоргидрин в растворитель сливается из мерника (поз. Е1) самотеком.
Загруженный эпихлоргидрин охлаждается до температуры не более 25 0С путем подачи холодной воды в рубашку растворителя (поз. Р). Затем при остановленной мешалке отбирается из растворителя проба эпихлоргидрина на определение показателей «плотности» и «массовая доля эпихлоргидрина». При получении удовлетворительного результата анализа производится загрузка дифенилолпропана из мерника (поз. Е2).
Содержимое растворителя (поз. Р) подогревается до температуры не более 80 0С при постоянном перемешивание в течение 30-60 минут для растворения дифенилолпропана, которая определяется визуальным осмотром пробы. Раствор должен быть прозрачным.
После выхода результата анализа по показателям «плотность» и «массовая доля эпихлоргидрина», производится расчет эпихлоргидрина для дозагрузки.
После расчета необходимого количества эпихлоргидрина производится дозагрузка до расчетного количества для смолы марки ЭД-16, Э-40 непосредственно в растворитель (поз. Р).
Готовый конденсационный раствор из растворителя (поз. Р) передается в мерник (поз. Е3), после чего с помощью насоса (поз. Н) передается в реактор.
[9]
2.2 Описание конструкции разрабатываемого оборудования
Назначение: растворитель эпоксидной смолы используется для взаимодействия исходных веществ с получением готового продукта.
Устройства: конструкция растворителя представляет собой вертикально расположенный аппарат, установленный в межэтажном перекрытии на опорах-лапах в количестве четырех штук. Состоит из цилиндрической обечайки, приваренного эллиптического днища и съемной эллиптической крышки на фланцевом соединении с уплотнительной поверхностью шип-паз, так как среда в аппарате коррозионная, ядовитая. Материал аппарата изготовлен из стали 08Х22Н6Т. Корпус заключен в рубашку, по которой идет теплоноситель(пар) с температурой 200 0C, используется для нагрева и поддержания температуры в аппарате.
Реактор снабжен перемешивающим устройством в виде трехъярусной листовой мешалки с отверстиями для увеличенного массообмена. Мешалки закреплены на валу с помощью шпоночного соединения. Вращение мешалки осуществляется с помощью электродвигателя через понижающий редуктор. В стойке привода установлены полумуфта, подшипники качения и сальниковое уплотнение. Полумуфта служит для соединения двух валов, расположенных на одной оси. Подшипники качения устанавливают парой, они обеспечивают вертикальность и центровку вала, а так же для сглаживания вращения. На входе вала обязательно предусматривают сальниковое уплотнение обеспечивающие герметичность. Вал закреплен на концевой опоре.
Для поддержания температуры внутри закреплен змеевик по которому идет теплоноситель, в качестве теплоносителя используется пар, при этом подача и вывод теплоносителя в змеевик осуществляется через штуцер, расположенный в крышке. На крышке аппарата для подачи опасных веществ установлен сифон, он предотвращает разбрызгивание вещества и накапливание статического электричества. Дополнительно на крышке расположены технологические штуцера для ввода и вывода вещества, люк для отбора проб, люк-лаз для проведения работ внутри аппарата.
3 Расчетная часть
3.1 Прочностные расчеты основных элементов оборудования
Исходные данные:
Материал аппарата
- корпуса сталь 08Х22Н6Т рубашки сталь 08Х22Н6Т
Рабочее давление
- в корпусе 0.1 МПа
- в рубашке 0.6 МПа
Рабочая температура
- в корпусе 60 °С
- в рубашке 200 °С
Среда в аппарате
- в корпусе ядовитая, пожароопасная
- в рубашке водяной пар
Диаметр аппарата
- в корпусе 2600 мм
- в рубашке 2800 мм
Высота аппарата 6219 мм
Коэффициент прочности сварного шва 0,9
Штуцера:
-Вход продукта Dy: 50 мм
-Выход продукта Dy: 100 мм
- Вход в змеевик Dy: 50 мм
- Выход из змеевика Dy: 50 мм
- Вход пара Dy: 80 мм
- Вход конденсата пара Dy: 32 мм
- Выход конденсата Dy: 80 мм
-Люк-лаз Dy: 450 мм
-Воздушник Dy: 100 мм
-Вакуум Dy: 100 мм
3.1.1 Расчет обечайки
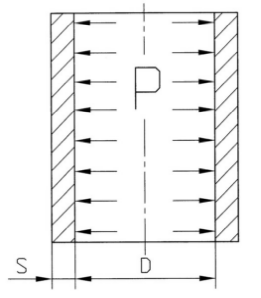
Рисунок 8 - Расчетная схема обечайки
Расчетная толщина стенки обечайки определяется по формуле
[4,с.103]
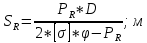
где D-внутренний диаметр аппарата, м;
PR-расчетное давление, МПа;
PR=Р + 0,2 МПа;
PR=0,1 + 0,2 = 0,3 МПа;
[σ]-допускаемое напряжение, МПа;
φ-коэффициент прочности сварного шва.
Определяем допускаемое напряжение по таблице 1.4
[4,с.12]
Значение температуры в таблице нет, поэтому пользуемся формулой интерполяции
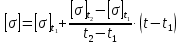
где: t = 60

t1 = 20

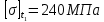
t2 = 100

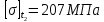

Определяем расчетную толщену стенки по формуле (1)
SR =
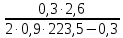
Исполнительная толщина стенки определяется по формуле 6.2
[4,с.103]

где SR-расчетная толщина стенки корпуса, м;
с-суммарная прибавка на коррозию, м;

с1 – коэффициент прибавки на коррозию, м
с1=0,001м
с2 – технологическая прибавка, м
с2=0,005мм
с3 – прибавка на минусовой допуск, м
с3=0мм
с=0,001+0,005+0=0,006мм
Определяем исполнительную толщину стенки по формуле (3):
S=0,00194+0,006=0,00794 м
С учетом осевой сжимающий нагрузки принимаем: S=0,08 м
По производственным данным принимаем: SД=0,018 м
Проверочный расчет на допускаемое внутреннее давление определяется по формуле 6.3
[4,с.103]
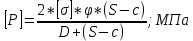


1,8 МПа ˃ 0,1 МПа- Условие прочности выполняется.
3.1.2 Расчет эллиптического днища
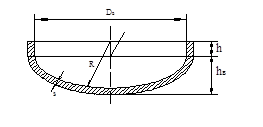
Рисунок 9 - Расчетная схема эллиптического днища
Расчетная толщина днища определяется по формуле 7.1
[4,c.132]
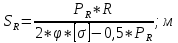
где: R=D-радиус кривизны в вершине днища, м

Исполнительная толщина стенки днища определяется по формуле 7.2
[4,c.132]

Sд=0,00193+0,006=0,00793 м
Исходя из осевой нагрузки принимаем: SД=0,08 м
По производственным данным принимаем: SД=0,018 м
Проверочный расчет на допускаемое внутренне давление определяется по формуле 7.3
[4,c.132]
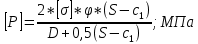


1,8 МПа ˃ 0,1 МПа - Условие прочности выполняется.
3.1.3 Расчет обечайки рубашки

Рисунок 10 - Расчетная схема обечайки рубашки
Расчетная толщина стенки обечайки определяется по формуле (1)

где D-внутренний диаметр аппарата, м;
PR-расчетное давление, МПа;
PR=Р + 0,2 МПа;
PR=0,6 + 0,2 = 0,8 МПа;
[σ]-допускаемое напряжение, МПа;
φ-коэффициент прочности сварного шва.
Определяем допускаемое напряжение по таблице 1.4
[4,с.14]
Допускаемое напряжение для марки стали 08Х22Н6Т при заданной температуре 200CO равно 193 МПа.
Определяем расчетную толщену стенки по формуле (1)
SR =
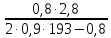
Исполнительная толщина стенки определяется по формуле (2)

где SR-расчетная толщина стенки корпуса, м;