Файл: Разработка технологического процесса изготовления колпачка из.docx
ВУЗ: Не указан
Категория: Не указан
Дисциплина: Не указана
Добавлен: 08.11.2023
Просмотров: 275
Скачиваний: 12
ВНИМАНИЕ! Если данный файл нарушает Ваши авторские права, то обязательно сообщите нам.
СОДЕРЖАНИЕ
1.4 Разработка вариантов технологии изготовления детали и выбор предпочтительного варианта
2 Анализ технологического процесса изготовления детали «Колпачок»
2.1 Расчет технологических параметров процесса разрезки
2.2 Расчет технологических параметров процесса вырубки
2.3 Расчет технологических параметров процесса вытяжки
3 Проектирование технологической оснастки для операции вытяжка
3.2 Назначение основных деталей штампа и выбор материалов для их изготовления
подставляя значения, получаем:
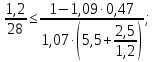

Условие выполняется, тем самым появляется возможность образования складок, из чего следует необходимость применения прижима.
2.3.4 Расчет исполнительных размеров рабочего инструмента
Основными исполнительными размерами пуансона и матрицы для вытяжки без утонения являются внутренний диаметр матрицы dм, наружный диаметр матрицы Dм, высота цилиндрического пояска матрицы hц, наружный диаметр пуансона dп.
Если допуск на размер изделия задан по его внутреннему размеру, то расчет исполнительных размеров диаметров инструмента определяется по формулам [2, стр.286]:
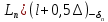

zвт = S + 0,07

где l – номинальный размер изделия;
Δ – допуск на размер изделия;
zвт – односторонний зазор при вытяжке;


zвт = 1,2 + 0,07



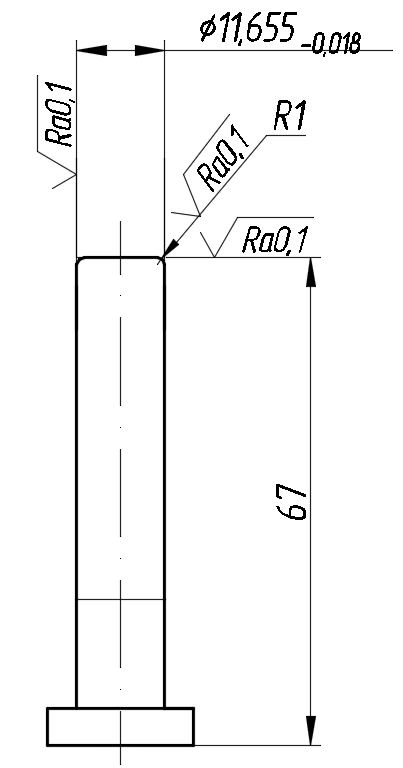
Рисунок 12 – Эскиз пуансона вытяжного
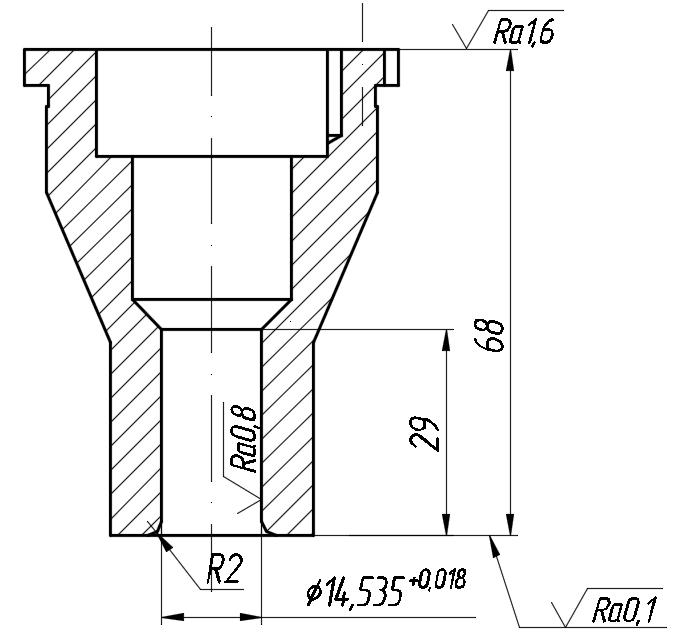
Рисунок 13 – Эскиз матрицы вытяжной
2.3.5 Расчет рабочего инструмента на прочность
2.3.5.1 Проверка пуансона на продольный изгиб
Условие прочности записывается в виде:



где P
max – максимальное технологическое усилие вырубки;
Kу – коэффициент запаса устойчивости (для закаленной стали принимается Ку = 2…3),
Pкр – критическая нагрузка;
Е – модуль упругости (для стали Е = 2,1∙105 МПа);
η – коэффициент, учитывающий влияние условий закрепления пуансона, характера нагружения и изменения сечения пуансона по длине на Pкр;
J – осевой момент инерции;
l – длина свободной, незакрепленной части пуансона
Пуансон изготовлен из материала У12А.
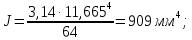
Принимаем η = 2,5; l = 50 мм, тогда

Проверка условия


2.3.5.2 Проверка пуансона на сжатие
Условие прочности записывается в виде:

где σсж – сжимающее напряжение, действующее в пуансоне;
Fоп – площадь опасного сечения пуансона; [σсж] – допустимое сжимающее напряжение.
Допустимое значение сжимающих напряжений для стали У12А [σсж] = 1600 МПа.
Величину σсж определяют так:


Таким образом

условие выполняется.
2.3.5.3 Расчет буферного устройства
Методики расчета и выбора буферов изложены в ГОСТ 22188-83-22202-83.
Усилие зажима при вытяжке:

По ГОСТ 22191 выбираем по усилию пружины при наибольшей рабочей деформации (сжатию) Р2 = 2400 Н (240 кгс) и по усилию пружины при максимальной деформации Р3 = 2940 Н (294 кгс).
Пример условного обозначения буфера с резиновыми пружинами усилием Р2 = 2400Н, размерами D = 58 мм, h2 = 36 мм, d = М12.
Диаметр резиновой пружины D = 45 мм, d = 13 мм; Н0 = 40 мм, деформация нагружения F1 = 12,0 мм; F1 = 14,0 мм.
Пример условного обозначения резиновой пружины размером D = 45 мм:
Пружина 1085-2637/001 ГОСТ 22191-83.
Материал – пластина резиновая маслобензостойкая подгруппы 4.8 по ГОСТ 7338-77.
Твердость резины – 50…70 по Шору А.
Конструктивно диаметр верхней шайбы должен быть ø58-60 мм. Выбираем 1085-2743 диаметром ø 58 мм по ГОСТ 22194-83.
Усилие резинового буфера определяется по формуле:

где F – площадь контактной поверхности кольца, см2.
Площадь поверхности кольца:


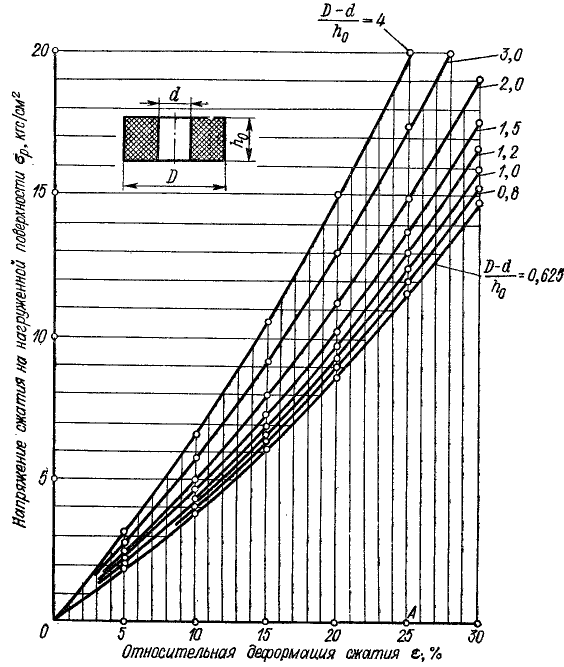
Рисунок 14 – Диаграмма для определения напряжений сжатия резины твердостью 50 (модуль упругости Е = 30 кгс/см2)
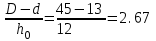

Усилие буфера:

3 Проектирование технологической оснастки для операции вытяжка
-
Классификация проектируемого штампа
Согласно разработанной на кафедре Е4 классификации штампов по основным техническим признакам штампа вырубки можно классифицировать следующим образом [9]:
По виду исходной заготовки и схеме напряженного состояния – для листовой штамповки;
По способу действия – комбинированного;
По характеру выполняемых работ – разделительные, формоизменяющие;
По виду операций – вырубные, вытяжные;
По виду направляющих узлов – с направляющими колонками и втулками;
По способу подачи – ручное;
По способу крепления штампа – болтовое;
По виду движения – простого одностороннего.
В данной работе представлен штамп совмещенного действия для вырубки, вытяжки.
Эскиз вырубного штампа в сборе представлен на рисунке 6.
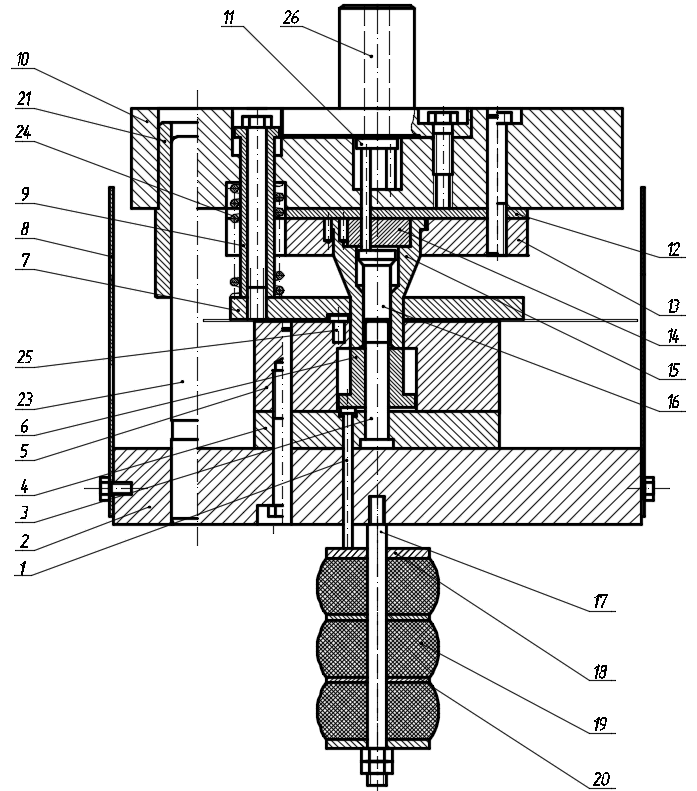
Рисунок 15 – Эскиз штампа совмещенного действия для вырубки и вытяжки.
В разработанном штампе вытяжная матрица поз.15 является одновременно и вырубным пуансоном. В нижней части штампа кроме обычного вытяжного пуансона поз.3 и выталкивателя поз.6, перемещающегося от буферного устройства при помощи толкателей поз.1, помещается вырубная матрица поз.5.
Полоса подается справа до упоров поз.25 (второй не показан), верхняя часть штампа начинает опускается, сначала полоса прижимается съемником поз.7, который висит на пружинах 24. Для ограничения хода съемника применены болты с втулками поз.9.
При дальнейшем опускании верхней части штампа пуансон-матрица 15 вырубает круг и при дальнейшем опускании вытягивает заготовку по пуансону поз.3. При этом пуансон-матрица давит на выталкиватель поз.6, который в свою очередь давит через толкатели поз.1 на буферное устройство поз. 17, 18, 19, 20.
При обратном ходе пуансон-матрица поз.15 прекращает давить на выталкиватель поз.6, буфер разжимается и давит на выталкиватель вверх. Верхняя часть штампа продолжает подниматься со съемником поз.7, а выталкиватель снимаем с пуансона поз.3 готовую деталь.
С пуансон-матрицы поз.15 полоса снимается съемником поз. 7.
Чтобы деталь не осталась в пуансон-матрице поз.15, в конце обратного хода деталь выбрасывается из нее с помощью выбрасывателей поз.16, на которые через диск поз.11 действует стержень от пресса.
3.2 Назначение основных деталей штампа и выбор материалов для их изготовления
Стали, применяемые для изготовления рабочих частей штампов делятся на группы:
-
Углеродистые инструментальные стали небольшой прокаливаемости (диаметром до 25 мм): У8А, У10А, У8, У10. -
Легированные стали повышенной прокаливаемости (диаметром до 40-50 мм): Х (ШХ15), Х09, 9Х, 9ХС, 9ХФ, ХВГ, 9ХВГ, ХГСВФ. -
Высокохромистые стали высокой прокаливаемости (диаметром до 80 мм), высокой износоустойчивости, мало деформируемые при закалке: Х12Ф1, Х12Ф, Х12М, Х12, Х6ВФ и ХГ3СВФ. -
Легированные стали повышенной вязкости (при твердости НRС 56-58): 4ХС, 6ХС, 4ХВ2С, 5ХВ2С, 5ХВГ.
Углеродистые инструментальные стали после правильной выполненной термической обработки обладают такой же твердостью как и многие легированные стали. Наиболее пригодны стали марок У10А и У10 (простая форма и до диаметра 25 мм), имеющие более высокую прочность на изгиб, чем другие марки (σиз = 200÷230 кгс/мм2 при HRC 59-60).
Легированные инструментальные стали повышенной прокаливаемости применяются до толщины 40 мм, σиз = 250 кгс/мм2.
Для вытяжных штампов рекомендуется применять стали Х12, Х12Ф1 с азотирование поверхности при твердости наружного слоя HRC 68-69 и твердости закаленного подслоя HRC 58. Стали этой группы подвергаются закалке с нагревом до высоких температур (Х12М, Х12Ф, х12 – 1020-1040°С; Х12Ф1 – 1070-1090°С) и низкому отпуску (150-170°С), твердость HRC 61-63.
Плиты штампов изготавливаются из Стали 40 и 50.
Хвостовики – Сталь 35, 40.
Колонки направляющие, втулки направляющие – Сталь 20: цементировать на глубину 0,5-1 мм, калить HRC 58-62; Стали 45, 50 – калить HRC 45-50.
Пуансонодержатели – Стали 35 и 45.
Подкладки под пуансоны – Сталь 45: калить HRC 40-45.
Съемники – Ст.3 (Сталь 25).
Прижимы, направляющие планки, выталкиватели – Стали 40 и 45: калить HRC 50-54.
Упоры – Сталь 45: калить HRC 50-54.
Ловители – У8А (У7А): калить HRC 50-54.
Штифты – Сталь У8А (Ст.6): калить HRC 45-50.
Пружины – Стали 65Г и 60С2 (Стальная проволока II класаа): калить HRC 40-48.
Хорошим материалом для изготовления вытяжных матриц являются также алюминиевые бронзы типа БрАЖН-10-4-6, весьма устойчивые против налипания при вытяжке нержавеющей стали.