Файл: Разработка технологического процесса изготовления колпачка из.docx
ВУЗ: Не указан
Категория: Не указан
Дисциплина: Не указана
Добавлен: 08.11.2023
Просмотров: 269
Скачиваний: 12
ВНИМАНИЕ! Если данный файл нарушает Ваши авторские права, то обязательно сообщите нам.
СОДЕРЖАНИЕ
1.4 Разработка вариантов технологии изготовления детали и выбор предпочтительного варианта
2 Анализ технологического процесса изготовления детали «Колпачок»
2.1 Расчет технологических параметров процесса разрезки
2.2 Расчет технологических параметров процесса вырубки
2.3 Расчет технологических параметров процесса вытяжки
3 Проектирование технологической оснастки для операции вытяжка
3.2 Назначение основных деталей штампа и выбор материалов для их изготовления
1.4 Разработка вариантов технологии изготовления детали и выбор предпочтительного варианта
Принимаем вырубку и вытяжку и механическую обработку внутреннего диаметра.
Варианты технологических процессов могут отличаться по виду проката, виду исходной штучной заготовки, по способу получения исходных заготовок, по виду раскроя.
Вариантов по прокату два - горячекатаный или холоднокатаный, прочностные характеристики одинаковые, относительное удлинение у холоднокатаного немного больше, выбираем холоднокатаный прокат.
По технологии изготовления: отдельная вырубка, а затем вытяжка. Детали мелкие, можно сделать вырубку сразу 2-3 деталей из одной полосы. Но потом придется вставлять в вытяжной штамп мелкие кружки – очень неудобно.
Выбираем совмещенный штамм одновременно с вырубкой и вытяжкой.
Таблица 6 – Варианты технологических маршрутов изготовления детали
№ | Варианты технологических маршрутов | Вид проката | Последовательность технологических операций |
1 | 2 | 3 | 4 |
1 | Технологический маршрут детали «колпачок» с отдельной вырубкой и вытяжкой на двух штампах с последующей механической обработкой | полоса | 1.Резка листа на полосы 2.Вырубка круга 3.Вытяжка без утонения с прижимом 4.Обрезка кромки 5.Зенкерование 6.Предварительное развертывание 7. Окончательное развертывание |
2 | Технологический маршрут детали «колпачок» с совмещенной вырубкой и вытяжкой с последующей механической обработкой | полоса | 1.Резка листа на полосы 2.Вырубка с вытяжкой 3.Обрезка кромки 4.Зенкерование 5.Предварительное развертывание 6. Окончательное развертывание |
Таблица 7– Принятый технологический маршрут детали «Колпачок»
Метод обработки | Вид операции | Технологическая схема процесса | Позиции на технологической схеме | Эскиз получаемой детали после операции |
Холодная пластическая деформация | Разрезка на полосы | ![]() | 1. Нож гильотины 2. Лист | ![]() |
Холодная пластическая деформация | Вырубка кружка, вытяжка без утонения | ![]() | Полуфабрикат
| ![]() |
Механическая обработка | Обрезка кромки | ![]() | Резец подрезной | ![]() |
Механическая обработка | Зенкерование и развертывание отверстия | ![]() | 1. Зенкер 2. Развертка 3.Развертка окончательной обработки | ![]() |
Механическая обработка | Точение (снятие) фаски | ![]() | Резец подрезной | ![]() |
Выводы
-
Деталь «колпачок» является деталью широкого применения. -
Проанализированы рациональные технологии изготовления изделия. -
Оценка ТКИ детали «колпачек» окончательно будет дана после всех расчетов
Цели и задачи работы
Целью работы является “Разработать технологический процесс изготовления изделия «Колпачок» ”
Задачи работы:
-
Выбор оптимальной технологии изготовления изделия. -
Разработать технологию изготовления изделия. -
Расчет технологических параметров. -
Расчет рабочего инструмента. -
Подбор прессового оборудования для выбранной технологии изготовления.
2 Анализ технологического процесса изготовления детали «Колпачок»
2.1 Расчет технологических параметров процесса разрезки
Схема технологического процесса резки листа на полосы представлена на рисунке 3.
Усилие отрезки


где s – толщина материала, мм;



Расчет усилия отрезки:

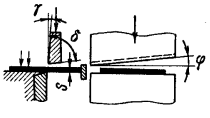
Рисунок 3 – Гильотинные ножницы с наклонным ножом
Выбираем гильотинные ножницы НД3316Г:
наибольшая толщина разрезаемого листа: δ = 4,0 мм;
наибольшая ширина разрезаемого листа: В = 2000 мм;
наибольшая длина разрезаемой полосы: L = 630 мм;
угол наклона подвижного ножа α = 1°19';
число ходов ножа n = 65 мин-1;
мощность привода N = 5,6 кВт;
масса m = 3,25 т.
Величина усилия, создаваемого кривошипным прессом, переменна на протяжении хода пресса, достигая наибольшего (номинального) значения в конце рабочего хода.
Паспортные данные приводят номинальное усилие кривошипных прессов, создаваемое при угле α = 20÷30°. Это необходимо учитывать в случае операций, требующих большой величины в начале операции.
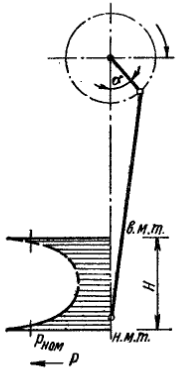
Рисунок 4 – Усилие, создаваемое кривошипным прессом на протяжении рабочего хода
Для совмещенных операций – вырубки и вытяжки, возможна перегрузка пресса, так как вырубной переход выполняется задолго до достижения допустимого усилия номинальной величины.
На рисунке 5 приведен такой случай: кривая 2, соответствующая операции вырубки, выходит за пределы допустимого усилия пресса при данном повороте угла кривошипа.
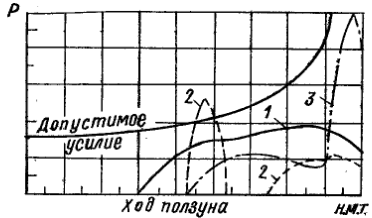
Рисунок 5 – Наложение рабочих диаграмм на диаграмму допустимого усилия пресса: 1 – вытяжка; 2 – вырубка и вытяжка; 3 – гибка с калибровкой
Номинальное усилие пресса устанавливается по прочности коленчатого вала и обычно берется равным усилию, создаваемому при угле поворота кривошипа α = 20÷30°, что соответствует величине рабочего хода ползуна: hα=(0,05÷0,07)·Н.
Ход пресса: обычно величина хода пресса для вытяжки берется в 2,5 раза больше высоты вытягиваемой детали, чтобы обеспечить удобство установки заготовки и удаления полуфабриката и готовой детали.
Высота готовой детали hд = 13,2 мм. Следовательно, ход первого пресса должен быть приблизительно равным: Н1 = 13,2 · 2,5 = 33 мм. Выбираем пресс для вырубки - вытяжки:
КД2116А, ГОСТ 9408 номинальное усилие Рн = 0,04 МН.
ход ползуна регулируемый, не менее S = 45 мм;
число ходов ползуна непрерывных не регулируемых, не более n = 200 мин-1;
число ходов ползуна непрерывных регулируемых, от n = 170 - 300 мин-1;
число ходов ползуна одиночных, не менее n = 63 мин-1;
размеры стола L x B = 315 х 250 мм;
размеры отверстия в столе: D = 90 мм;
наибольшее расстояние между столом и ползуном в его нижнем положении при наибольшем ходе: Н = 190 мм.
мощность привода главного движения N = 0,6 кВт;
масса m = 0,5 т.
2.2 Расчет технологических параметров процесса вырубки
2.2.1 Характеристика процесса вырубки
Вырубка – процесс полного отделения части заготовки по замкнутому контуру путем сдвига. Процесс вырубки относится к процессам разделительной листовой штамповки. Схема напряженно-деформированного состояния соответствует сдвигу на срединных (по толщине) поверхностях.
Первая стадия – упругая деформация и начало пластической и начало пластической деформации; пуансон вначале производит сжатие металла, появляется упругий прогиб, и металл слегка выдавливается в отверстии матрицы.
Вторая стадия – развитие пластической деформации; вблизи режущих кромок пуансона и матрицы создается концентрация напряжений, которая вызывает течение металла и образования зоны смятия. Это местное смятие будет развиваться до тех пор, пока по всей толщине металла не возникнут напряжения, достаточные для возникновения линий скольжения, которые, в свою очередь, образуют узкую пластическую зону в виде параллелепипеда (при отрезке) или объемное кольцо (при вырубке круглых деталей). В результате этих явлений развивается деформация сдвига, сопровождаемая изгибом и растяжением волокон, особенно при большом зазоре (свыше 20% для материалов толщиной до 10 мм), вплоть до начала образования скалывающих трещин.