Добавлен: 09.11.2023
Просмотров: 90
Скачиваний: 3
ВНИМАНИЕ! Если данный файл нарушает Ваши авторские права, то обязательно сообщите нам.
Базированием называют придание заготовки или изделию требуемого положения относительно выбранной системы координат. Базы - это поверхности, оси или точки деталей, относительно которых ориентируется, другие поверхности.
Технологические базы - это поверхности определяющие положения деталей в процессе их изготовления. При назначении технологических баз необходимо руководствоваться принципами:
-
Принцип единства баз. -
Принцип постоянства баз. -
Правило 6 точек.
Измерительной базой называют поверхность, определяющую относительное положение детали или сборочной единицы и средств измерения.
Установочные базы также относят к технологическим.
Установочная база-это поверхности, которыми деталь устанавливается на приспособление или стол станка.
-
Проектирование варианта технологического маршрута механической обработки детали.
№ оп. | Наименование операции | Новое оборудование | Т шт н/ч. | Разряд рабочего |
000 | Входной контроль | Контрольный стол | 0,18 | 3 |
005 | Заготовительная | - | - | - |
010 | Токарная | DMG CTX gamma 2000 TC | 1,49 | 4 |
015 | Токарная | DMG CTX gamma 2000 TC | 1,49 | 4 |
020 | Токарная | DMG CTX gamma 2000 TC | | 4 |
025 | Токарная | DMG CTX gamma 2000 TC | 4,5 | 4 |
030 | Программно-комбинированная | DMG CTX gamma 2000 TC | | 4 |
035 | Внутришлифовальная | BDU80 | 1,15 | 4 |
040 | Круглошлифовальная | 3М152ВМ | 0,35 | 4 |
045 | Слесарная | Контрольный стол | 0,05 | 3 |
050 | Промывка | - | - | - |
055 | Окончательный контроль | Контрольный стол | 0,16 | 4 |
Итого | 9,34 | |
В результате введения новшеств (современное оборудование) в технологический процесс механической обработки детали «Воронка сливная» - снижено время обработки на 7,41 н/ч. и повышено качество обработки поверхности детали и улучшено условие труда.
-
Выбор оборудования и его обоснование
Выбирая тип оборудования, учитывают его производительность и проектную мощность цеха, проверяют использование оборудования по времени работы и его мощности.
Выбор станка должен основываться на следующих правилах:
-
Мощность, производительность и точность должны быть минимальными, но достаточно для выполнения требования предоставляемых к операции -
Обеспечение концентрации производства с целью уменьшения числа операций, количества оборудования, повышения производительности и точность за счет уменьшения числа переустановок заготовки -
Предпочтение отдавать отечественным станкам (они дешевле и сделаны по нашим стандартам) -
В среднесерийном производстве следует применять высокопроизводительные станки-автоматы, агрегатные станки, станки с ЧПУ -
Оборудование должно отвечать требования безопасности, Эргономики и экологии.
В проектируемом варианте вместо универсальных токарно-винторезных станков 16К20 и вертикально-фрезерного станка 6Р12 будем использовать токарно-фрезерный станок станок с ЧПУ модели DMG CTX gamma 2000 TC. Выбор данного оборудования значительно сократит время изготовления детали, повышения качества и улучшения условия работы.
-
Выбор станочных приспособлений.
Важнейшим вопросом при проектировании технологических процессов является технологически и экономически обоснованный выбор приспособлений.
Приспособления предназначены для установки и закрепления изделий при их изготовлении. Приспособления могут быть станочные и сборочные.
Станочные приспособления (СП) применяют для установки и закрепления заготовок на металлообрабатывающих станках.
Сборочные приспособления (СбП) используют для установки и закрепления изделий при их сборке.
Станочные приспособления по своей универсальности делятся на три вида:
-
специальные, предназначенные для конкретных заготовок; -
специализированные, предназначенные для определенного типа (класса) заготовок; -
универсальные, предназначенные для различных заготовок.
По конструкции и компоновке к настоящему времени сформировано семь стандартных систем станочных приспособлений:
-
универсально-сборные (УСП); -
сборно-разборные (СРП); -
универсальные безналадочные (УБП); -
неразборные специальные (НСП); -
универсальные наладочные (УНП); -
специализированные наладочные (СНП); -
универсально-сборные переналаживаемые (УСПП).
По точности станочные приспособления подразделяются на классы:
-
нормальной точности (Н); -
повышенной точности (П); -
высокой точности (В); -
особо высокой точности (А).
-
Выбор режущего инструмента и контрольно-измерительных средств
При разработке технологического процесса механической обработки заготовки необходимо правильно выбрать режущий инструмент и его вид. Конструкции инструмента и размеров в значительной мере предопределяется методами обработки, свойствами обрабатываемого материала, требуемой точностью обработки и качества обрабатываемых поверхностей.
На токарных операциях используются токарные резцы различного типа с напаянными пластинами из быстрорежущей стали, а так же применяются резцы с механическим креплением пластинок из твердого сплава. Для обработки точных отверстий используются сверла и расточные резцы.
На программно-комбинированных операциях используются концевые фрезы, а так же специальные фрезы. Для получения отверстий применяются спиральные свёрла и расточные резцы.
При обработке титанового сплава в качестве материала режущей части инструмента для всех применяемых резцов используются пластины из твёрдого сплава ВК8. Осевой инструмент применяется из быстрорежущей стали Р6М5. Фрезы изготовлены также из быстрорежущих сталей марок Р6М5.
Измерительный инструмент, используемый в данном технологическом процессе, в основном ГОСТированный (штангенциркули, пробки, скобы, шаблоны, глубиномеры), а так же специальный (калибры для контроля расположения отверстий и т.д.).
-
Разбивка операций на переходы и проходы; установление межоперационных припусков и допусков по ОСТ 141512-86 на отверстие ø9,0Н9(+0,036) мм и отверстие ø72JS7(±0,015) мм
Установление межоперационных припусков и допусков по ОСТ 141512-86 для поверхности ø9,0Н10(+0,036) мм.
№ п/п | Переход | Норм. размер | Ном. припуск | Max припуск | Min припуск |
1 | Заготовительная | - | 9 | 9,036 | 9 |
2 | Сверление | 8,2Н12(+0,13) | 8,2 | 8,33 | 8,2 |
3 | Зенкерование | 9Н9(+0,018) | 0,8 | 0,836 | 0,67 |
-
Определяем максимальные и минимальные размеры заготовки и детали:
Сверление:


Зенкерование:


-
Определяем межоперационные припуски и межоперационные размеры:


Установление межоперационных припусков и допусков для отверстия ø72JS7(±0,015) мм
№ п/п | Переход | Норм. размер | Ном. припуск | Max припуск | Min припуск |
1 | Заготовительная | - | 72 | 72,015 | 71,985 |
2 | Растачивание черновое | 65,8Н12(+0,3) | 65,8 | 66,1 | 65,8 |
3 | Растачивание чистовое | 70Н8(+0,046) | 70 | 70,046 | 70 |
4 | Шлифование | 72JS7(±0,015) | 2 | 2,015 | 1,94 |
-
Определяем величину минимального и максимального размеров детали заготовки:
Растачивание черновое:


Растачивание чистовое:


Шлифование:


-
Определим межоперационные припуски и межоперационные размеры:

;



-
Расчет режимов резания для одной операции.
Сверлить 3 отв. Ø9,0 мм на длину 4 мм в детали из материала 38ХА-СШ. Сверление будет производиться на станке 2Н125.
Инструмент: сверло-зенкер ø8,2/ø9,0 -0,01.
Материал инструмента: быстрорежущая сталь Р18 по ГОСТ 19265-80.
-
Определяем глубину резания:


-
Определяем подачумм/об, для сверления отверстия в заготовке сверлом Р18

Принимаем

-
Корректируем полученное значение по паспорту станка.
-
Определяем скорость резания при сверлении υ, м/мин:
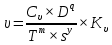
-
Значение коэффициентов и показателей степени приведены в литературе (стр. 278 табл. 28)
где




-
Общий поправочный коэффициент на скорость резания , учитывающий фактические условия резания
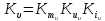
где



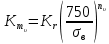
