Файл: Курсовой проект по мдк. 01. 01 Технология ремонта и техобслуживания пм. 01 Осуществление технического обслуживания рабочих эталонов и поверочного оборудования.docx
ВУЗ: Не указан
Категория: Не указан
Дисциплина: Не указана
Добавлен: 22.11.2023
Просмотров: 233
Скачиваний: 5
ВНИМАНИЕ! Если данный файл нарушает Ваши авторские права, то обязательно сообщите нам.
В настоящее время используют, как правило, трехуровневую систему ремонта средств измерений :
- на местах эксплуатации с помощью ремонтно-поверочных лабораторий измерительной техники,
- на ремонтных участках лабораторий измерительной техники,
- на ремонтных заводах.
Кроме того, средства измерений можно отремонтировать на заводах-изготовителях и на специализированных заводах приборостроительных министерств. Размещение ремонтно-технологического оборудования фактически определяет порядок ремонта средств измерений, т.е. виды и методы ремонта на различных уровнях системы ремонта и потребную квалификацию ремонтника.
В зависимости от характера отказов, степени выработки ресурса и трудоемкости восстановления различают текущий, средний и капитальный виды ремонта средств измерений. Такое разделение видов ремонта необходимо для планирования ремонтного производства. Сразу же следует отметить, что после ремонта средство измерений допускается к эксплуатации при проведении поверки, позволяющей удостовериться в соответствии его метрологических характеристик.
К текущему ремонту относят работы, связанные с устранением отдельных неисправностей средств измерений посредством замены комплектующих изделий и не
требующие сложного диагностического и технологического оборудования. К этому виду ремонта относят также несложные в технологическом отношении операции по регулировке средств измерений для доведения метрологических характеристик до нормируемых значений в случае забракования прибора при поверке.
При среднем ремонте помимо операций, выполняемых при текущем ремонте, проводятся трудоемкие операции по замене или восстановлению (реставрации) элементов и составных частей работы по частичному восстановлению ресурса средств измерений, контроль технического состояния всех составных частей прибора (помимо выработавших ресурс и отказавших) с устранением выявленных неисправностей, настройка (регулировка) прибора и его составных частей после ремонта.
При капитальном ремонте ресурс полностью или почти полностью восстанавливается: прибор фактически полностью разбирают и определяют техническое состояние каждой детали, элемента, несущих и базовых конструкций; устраняют тяжелые повреждения и отказы, требующие сложного диагностического оборудования, трудоемких и сложных технологических процессов по обнаружению, замене и восстановлению отказавших (поврежденных) элементов и составных частей (восстановление или нанесение гальванических покрытий, изготовление новых деталей взамен вышедших из строя, восстановление электрической схемы прибора согласно принципиальной схеме и т. п.); прибор в целом комплексно настраивают и регулируют; после ремонта его испытывают.
Анализ обязательных работ при капитальном ремонте позволяет сделать заключение о том, что средства измерений при этом виде ремонта должны быть подвергнуты технологическим операциям и испытаниям в объеме основного производства. Однако производственные возможности ведомственных ремонтных предприятий, как правило, не позволяют производить его в требуемом объеме и с должным качеством. В связи с этим в процессе эксплуатации наблюдается значительное увеличение интенсивности отказов средств измерений после капитального ремонта. Поэтому во многих случаях экономически капитальный ремонт средств измерений не оправдывает себя, так как затраты на него соизмеримы с затратами на приобретение новых средств измерений, а качество отремонтированных приборов существенно уступает новым. О нецелесообразности капитального ремонта свидетельствует и тот факт, что при достигнутых уровнях надежности моральный износ средств измерений наступает раньше физического. Для перспективного парка средств измерений с большим ресурсом и сроком службы целесообразно планировать только текущий и средний ремонт. И только в отдельных случаях при остром дефиците каких-либо типов средств измерений допустима организация их капитального ремонта.
Таким образом, при среднем и капитальном ремонте фактически восстанавливают основные потребительские свойства средств измерений, а при текущем ремонте поддерживают работоспособное состояние посредством устранения “текущих отказов, т.е. отказов, неизбежно встречающихся при эксплуатации любых технических изделий ввиду их ограниченной надежности.
Рассмотренные виды ремонта различаются сложностью и трудоемкостью. Поэтому для их реализации используют системы ремонта различного уровня.
Текущий ремонт обычно выполняет выездная группа специалистов ведомственной лаборатории измерительной техники, осуществляющая одновременно поверку средств измерений непосредственно на местах их эксплуатации. Текущий ремонт не требует сложного специального технологического оборудования и при наличии группового ЗИП и подготовленных специалистов может быть освоен в короткие сроки. При такой организации ремонта имеет место минимальное время изъятия средств измерений из сферы эксплуатации.
Текущий и частично средний ремонт проводят в лабораториях измерительной техники предприятий и ведомств, средний и капитальный
– в специализированных цехах (участках) ведомственных ремонтных заводов.
На время и стоимость ремонта существенно влияют методы ремонта, среди которых различают детальный и агрегатный.
При детальном методе ремонта отказавшие средства измерений восстанавливают на уровне комплектующих элементов. Основными недостатками этого метода являются: большее время ремонта, особенно сложных радиоизмерительных приборов; сложность диагностического оборудования; высокие требования к квалификации ремонтника; необходимость в тщательно отработанной ремонтной документации с описанием методов поиска и устранения отказов до комплектующего электрорадиоэлемента. С учетом все возрастающей сложности парка средств измерений детальный метод ремонта приводит к значительным трудозатратам и увеличению времени отсутствия средств измерений на местах использования.
Суть агрегатного метода ремонта заключается в замене отказавших агрегатов (узлов, блоков, плат) новыми или отремонтированными. Основными преимуществами данного метода ремонта являются минимальное время ремонта, простота технологического оборудования, невысокие требования к квалификации ремонтного персонала, относительная простота ремонтной документации. Однако агрегатный метод ремонта требует блочно-модульного построения средств измерений. Особенно эффективен он при текущем ремонте. Анализ характера отказов средств измерений показал, что до 80% для восстановления работоспособности требует ремонта в объеме текущего. Поэтому агрегатный метод представляется перспективным в плане сокращения времени восстановления.
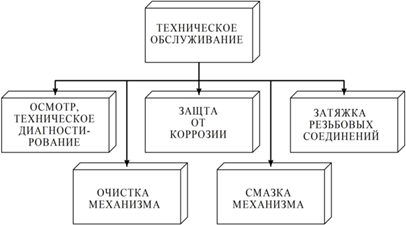
Рисунок 4 – Система технического обслуживания
2.3 Микрометрический глубиномер состоит из таких элементов:
-
основание; -
продольная шкала (стебель); -
измерительный стержень; -
микрометрическая головка (барабан); -
фрикцион; -
стопорный винт.
Принцип действия микрометрической головки основан на перемещении винта вдоль оси при вращении его в неподвижной гайке. Перемещение пропорционально углу поворота винта вокруг оси. Полные обороты отсчитываются по шкале, нанесенной на стебле микрометрической головки, а доли оборота по круговой шкале, нанесенной на барабане.
Характеристики:
Тип | микрометрический |
Длина, см | 170 |
Ширина, см | 115 |
Высота, см | 48 |
Диапазон измерений | 100 |
Цена деления. мм | 0.01 |
Класс | 1 |
| |
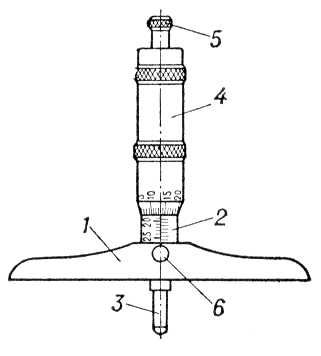
Рисунок 5 - Микрометрический глубиномер
1 —основание; 2 —стебель; 3 —измерительный стержень; 4 —барабан; 5 —трещотка; 6 —стопор.
Микрометрический глубиномер предназначен для измерения глубин отверстий, канавок, уступов, пазов. Инструмент состоит из основания и микрометрической головки.
Пример условного обозначения микрометрического глубиномера с диапазоном измерения 0-100 мм и значением цены деления 0,01 мм: Микрометрический глубиномер ГМ-100-0,01.
2.4. Разработка годового графика
На основании образца представлена в приложении Д
Приложение Д
Таблица 1 - ППР СИиА на 2022 г.
Наименование СИ | Тип | Заводской номер | Переодичность и виды работ | ||||||||||||
| | | 1 | 2 | 3 | 4 | 5 | 6 | 7 | 8 | 9 | 1 | 1 | 12 | |
Глубиномер микрометрический | ГМ-100 | В06373 | | | | | + | | | | | | | | |
Глубиномер микрометрический | ГМ-100 | В06373 | | | + | | | | | | | | | | |
Глубиномер микрометрический | ГМ-100 | В06373 | | | + | | | | | | | + | | | |
Глубиномер микрометрический | ГМ-100 | В06373 | | + | | | | | | | | | | | |
Глубиномер микрометрический | ГМ-100 | В06373 | | | | | + | | + | | | | | | |
Глубиномер микрометрический | ГМ-100 | В06373 | | | | | | + | | | | | | | |
Глубиномер микрометрический | ГМ-100 | В06373 | | | | | | | | | | | + | | |
Глубиномер микрометрический | ГМ-100 | В06373 | + | | | | | | | | | | | | |
Глубиномер микрометрический | ГМ-100 | В06373 | | | | | | | | + | | | | | |
Глубиномер микрометрический | ГМ-100 | В06373 | | | | + | | | | | | | | | |
Глубиномер микрометрический | ГМ-100 | В06373 | | | | | | | | | | | | + | |
Глубиномер микрометрический | ГМ-100 | В06373 | | + | | | | | | | | | | | |
Глубиномер микрометрический | ГМ-100 | В06373 | | | | | | | | | + | | | | |
Глубиномер микрометрический | ГМ-100 | В06373 | | | | | | + | | | | | | | |
Глубиномер микрометрический | ГМ-100 | В06373 | | | | | | | | + | | | | | |
Глубиномер микрометрический | ГМ-100 | В06373 | + | | | | | | | | | | | | |
Глубиномер микрометрический | ГМ-100 | В06373 | | | | | + | | | | | | | | |
Глубиномер микрометрический | ГМ-100 | В06373 | | | | | | | | | | + | | | |
Глубиномер микрометрический | ГМ-100 | В06373 | | | + | | | | | | | | | | |
Глубиномер микрометрический | ГМ-100 | В06373 | | | | | | | | | | | | + | |
Глубиномер микрометрический | ГМ-100 | В06373 | | | | | | | | | + | | | | |
Глубиномер микрометрический | ГМ-100 | В06373 | | + | | | | | | | | | | | |
Глубиномер микрометрический | ГМ-100 | В06373 | | | | | | + | | | | | | | |
Глубиномер микрометрический | ГМ-100 | В06373 | | | | | | | | | | | + | | |
Глубиномер микрометрический | ГМ-100 | В06373 | | | | + | | | | | | | | | |
Глубиномер микрометрический | ГМ-100 | В06373 | | | | | | | | + | | | | | |
Глубиномер микрометрический | ГМ-100 | В06373 | + | | | | | | | | | | | | |
Глубиномер микрометрический | ГМ-100 | В06373 | | | | | | | | | | + | | | |
Глубиномер микрометрический | ГМ-100 | В06373 | | | + | | | | | | | | | | |
Глубиномер микрометрический | ГМ-100 | В06373 | | | | | | | + | | | | | | |
Глубиномер микрометрический | ГМ-100 | В06373 | | + | | | | | | | | | | | |
Глубиномер микрометрический | ГМ-100 | В06373 | | | | | + | | | | | | | | |
Глубиномер микрометрический | ГМ-100 | В06373 | | | | | | | | | | + | | | |
Глубиномер микрометрический | ГМ-100 | В06373 | | | + | | | | | | | | | | |
Глубиномер микрометрический | ГМ-100 | В06373 | | | | | | | | + | | | | | |
Глубиномер микрометрический | ГМ-100 | В06373 | | + | | | | | | | | | | | |
Глубиномер микрометрический | ГМ-100 | В06373 | | | | | | | | | | | | + | |
Глубиномер микрометрический | ГМ-100 | В06373 | + | | | | | + | | | | | | | |
Глубиномер микрометрический | ГМ-100 | В06373 | | | | + | | | | | | | | | |
Глубиномер микрометрический | ГМ-100 | В06373 | | | + | | | + | | | | | | |
2.5. Технические характеристики
Глубиномеры следует изготовлять в соответствии с требованиями настоящего стандарта по конструкторской документации, утвержденной в установленном порядке.
Предел допускаемой погрешности глубиномеров (в пределах перемещения микрометрического винта) при температуре окружающей среды (20±5) °С и нормируемом измерительном усилии, а также при зажатом или отпущенном стопоре должен соответствовать указанному в табл.2
Таблица 2 – Пределы допускаемой погрешности
| | |
Диапазон измерений, мм | Предел допускаемой погрешности, мкм, глубиномеров классов точности | |
| 1 | 2 |
0-25 | ±2 | ±4 |
25-50 | ±3 | |
50-100 | | ±5 |
100-150 | ±4 | ±6 |
150-200 | - | ±8 |
200-250 | | ±9 |
250-300 | | ±10 |
Для микрометрических глубиномеров, ГОСТ 7472-92 определяет технические условия исполнения прибора. Согласно, этого ГОСТа, длина основания должна быть 100 мм, а ширина не больше 25 мм. Измерительный стержень изготавливается диаметром 5 мм.
Приборы 1-го класса точности выпускаются с диапазоном измерения до 150 мм, при этом погрешность составит 4 мкм. Инструменты 2-го класса, способны производить измерения до 300мм, а погрешность составит 10 мкм. Края основания могут иметь закругление, но не больше 1мм.Зачастую, поверхность измерительного стержня скруглена радиусом 5 мм, а смещение от центра допускается до 0,3 мм. Однако иногда, по специальному заказу, рабочая поверхность стержня, может быть прямоугольной.