Файл: Учебное пособие по курсу Иностранный язык Казань 2007 удк 804. 37. 022 М90 Мулюков И. М., И. А. Абдуллин Английский язык для технических специальностей Учебное пособие для студентов технических вузов. Казань Казан гос энерг унт, 2007.doc
ВУЗ: Не указан
Категория: Не указан
Дисциплина: Не указана
Добавлен: 22.11.2023
Просмотров: 410
Скачиваний: 14
ВНИМАНИЕ! Если данный файл нарушает Ваши авторские права, то обязательно сообщите нам.
In the 1970s the NHTSA required that cars be constructed so that passengers could survive 48-km/h impacts against immovable barriers. A “passive restraint” standard was proposed that would require manufacturers to devise automatic passenger restraint systems. Air bags that, upon impact, automatically inflate in a fraction of a second were developed as one solution, but automakers resisted installing them because of high costs and concern over reliability. A second solution was “passive” seat belts that do not require passengers to fasten the belts themselves. In 1984, after years of debate over regulatory proposals, the Department of Transportation mandated the phasing in of automatic crash protection for American-built cars to begin in 1986; by 1989, unless states representing two-thirds of the populace made the wearing of seat belts mandatory, all cars would have to be equipped with the automatic devices. Improved automotive safety features, improved highways, and a national speed limit of 88 km/h helped reduce the nation's highway fatality rate from 5.21 per 100 million mi driven in 1969 to 3.46 a decade later.
UNIT 3
Text A
Iron and Steel Manufacture
Iron and Steel Manufacture is a technology related to the production of iron and its alloys, particularly those containing a small percentage of carbon. The differences between the various types of iron and steel are sometimes confusing because of the nomenclature used. Steel in general is an alloy of iron and carbon, often with an admixture of other elements. Some alloys that are commercially called iron contain more carbon than commercial steels. Open-hearth iron and wrought iron contain only a few hundredths of 1 percent of carbon. Steels of various types contain from 0.04 percent to 2.25 percent of carbon. Cast iron, malleable cast iron, and pig iron contain amounts of carbon varying from 2 to 4 percent. A special form of malleable iron, containing virtually no carbon, is known as white-heart malleable iron. A special group of iron alloys, known as ferroalloys, is used in the manufacture of iron and steel alloys; they contain from 20 to 80 percent of an alloying element, such as manganese, silicon, or chromium.
Exercise 1
Ответьте на следующие вопросы:
-
What technology is used in the production of iron and its alloys? -
What is the main element which influences the difference between the various types of iron and steel? -
What materials are used in production of steel? -
How do we call an alloy of iron and carbon? -
What is the difference between commercial steels and iron? -
What is the average content of a carbon in different types of steel? -
What metallic materials contain carbonwithin the range of 2 to 4 percent? -
What is the content of a carbon in white-heart malleable iron? -
What special group of iron alloys is used in the manufacture of iron and steel alloys?
Exercise 2
Заполните пропуски недостающими по смыслу словами, используя текст:
-
Iron and Steel Manufacture is a technology used in the production of … and its alloys. -
Various types of iron and steel are sometimes confusing because of the … used. -
Steel is an alloy of… …, with an admixture of… . -
Some alloys that are commercially called iron contain more … than commercial … . -
Open-hearth iron contain only a few hundredths of 1 percent of … . -
Steels of various types contain from 0.04 percent to 2.25 percent of … . -
Pig iron contain amounts of … varying from 2 to 4 percent. -
Iron, containing virtually no carbon, is known as … . -
Ferroalloys are used in the manufacture steel … .
Exercise 3
Соответствуют ли данные предложения содержанию текста:
-
Iron and Steel Manufacture is a production of iron and its alloys. -
Iron and Steel Manufacture is a production of alloys containing large percentage of carbon. -
The differences between the various types of iron and steel depend on the country they are produced in. -
Pig iron in general is an alloy of ferroalloys and carbon, often with an admixture coal and gas. -
Some alloys that are commercially called commercial steels contain more carbon than iron. -
Open-hearth iron and wrought iron contain from 1 to 4 percent of carbon. -
Steels of various types contain from 2 percent to 4 percent of carbon. -
Cast iron and pig iron contain amounts of carbon varying from 0,4 to 2,22 percent. -
Ferroalloys are used in the manufacture of iron and steel alloys. -
Ferroalloys contain from 20 to 80 percent of an alloying element, such as manganese, silicon, or chromium
Exercise 4
Используя текст, составьте высказывания с данными словами и выражениями:
Iron and steel - production of iron – alloy – carbon - admixture of elements - commercial steel - open-hearth iron - wrought iron - cast iron - pig iron – ferroalloy - alloying element – manganese – silicon - chromium.
Exercise 5
Кратко передайте содержание каждого абзаца.
Exercise 6
Выделите пять основных идей текста.
Exercise 7
Составьте предложения, используя данные выражения:
-
Iron and Steel technology; computing technology; advanced technology; power production technology. -
Alloy; casting alloy (литейный сплав); hard facing alloy (твердый сплав); non-ferrous alloy (сплав цветных металлов); alloyage (легирование); alloyed (легированный); alloying (легирующий,легирование). -
Pig iron (чугун в чушках); open-heath iron (мартеновский чугун); foundry iron (литейный чугун);common iron (обыкновенный переплавленный чугун); malleable cast iron (ковкий чугун); wrought iron (пудлинговое железо).
Exercise 8
Переведите на русский язык следующие предложения:
-
Iron and Steel Manufacture technology is highly developed in Russia. -
Iron and steel factories are engaged in the production of steel and its alloys. -
The quality of steel produced depends on the content of carbon in it. -
The less the carbon content in iron the better is the quality of steel. -
Production of iron and its alloys at Iron and Steel mills require huge amounts of power. -
High quality steel is an alloy of iron and carbon with an admixture of ferroalloys. -
Commercial steels contain less carbon and more admixtures of ferroalloys such as: ferromanganese, ferrosilicon and others. -
Tool steels contain up to 0, 05 % of carbon. -
Alloying elements of ferroalloys are: manganese, silicon, or chromium.
Exercise 9
Переведите на английский язык:
-
Сталь это сплав чугуна и углерода с примесью других элементов. -
Чугун, произведенный в мартеновской печи, содержит очень небольшой процент углерода. -
Углерод практически отсутствует в закаленном ковком чугуне, -
Ферросплавы используются в производстве сплавов чугуна и стали. -
Ферромарганец - это сплав стали и марганца. -
Содержание легирующих элементов, таких как кремний, марганец и хром, в сплавах стали составляет от 20 до 80 процентов. -
Металлургическое производство – это технология, связанная с производством чугуна, стали и их сплавов.
Exercise 10
Текст на самостоятельный перевод:
History of Iron production
The exact date at which people discovered the technique of smelting iron ore to produce usable metal is not known. The earliest iron implements discovered by archaeologists in Egypt date from about 3000 BC, and iron ornaments were used even earlier; the comparatively advanced technique of hardening iron weapons by heat treatment was known to the Greeks about 1000 BC.
The alloys produced by early iron workers, and, indeed, all the iron alloys made until about the 14th century AD, would be classified today as wrought iron. They were made by heating a mass of iron ore and charcoal in a forge or furnace having a forced draft. Under this treatment the ore was reduced to the sponge of metallic iron filled with a slag composed of metallic impurities and charcoal ash. This sponge of iron was removed from the furnace while still incandescent and beaten with heavy sledges to drive out the slag and to weld and consolidate the iron. The iron produced under these conditions usually contained about 3 percent of slag particles and 0.1 percent of other impurities. Occasionally this technique of iron making produced, by accident, a true steel rather than wrought iron. Ironworkers learned to make steel by heating wrought iron and charcoal in clay boxes for a period of several days. By this process the iron absorbed enough carbon to become a true steel.
After the 14th century the furnaces used in smelting were increased in size, and increased draft was used to force the combustion gases through the “charge,” the mixture of raw materials. In these larger furnaces, the iron ore in the upper part of the furnace was first reduced to metallic iron and then took on more carbon as a result of the gases forced through it by the blast. The product of these furnaces was pig iron, an alloy that melts at a lower temperature than steel or wrought iron. Pig iron (so called because it was usually cast in stubby, round ingots known as pigs) was then further refined to make steel.
Modern steelmaking employs blast furnaces that are merely refinements of the furnaces used by the old ironworkers. The process of refining molten iron with blasts of air was accomplished by the British inventor Sir Henry Bessemer who developed the Bessemer furnace, or converter, in 1855. Since the 1960s, several so-called minimills have been producing steel from scrap metal in electric furnaces. Such mills are an important component of total U.S. steel production. The giant steel mills remain essential for the production of steel from iron ore.
Text B
Pig-Iron Production
The basic materials used for the manufacture of pig iron are iron ore, coke, and limestone. The coke is burned as a fuel to heat the furnace; as it burns, the coke gives off carbon monoxide, which combines with the iron oxides in the ore, reducing them to metallic iron. This is the basic chemical reaction in the blast furnace; it has the equation: Fe2O3 + 3CO = 3CO2 + 2Fe. The limestone in the furnace charge is used as an additional source of carbon monoxide and as a “flux” to combine with the infusible silica present in the ore to form fusible calcium silicate. Without the limestone, iron silicate would be formed, with a resulting loss of metallic iron. Calcium silicate plus other impurities form a slag that floats on top of the molten metal at the bottom of the furnace. Ordinary pig iron as produced by blast furnaces contains iron, about 92 percent; carbon, 3 or 4 percent; silicon, 0.5 to 3 percent; manganese, 0.25 to 2.5 percent; phosphorus, 0.04 to 2 percent; and a trace of sulfur. A typical blast furnace consists of a cylindrical steel shell lined with a refractory, which is any nonmetallic substance such as firebrick. The shell is tapered at the top and at the bottom and is widest at a point about one-quarter of the distance from the bottom. The lower portion of the furnace, called the bosh, is equipped with several tubular openings or tuyeres through which the air blast is forced. Near the bottom of the bosh is a hole through which the molten pig iron flows when the furnace is tapped, and above this hole, but below the tuyeres, is another hole for draining the slag. The top of the furnace, which is about 27 m in height, contains vents for the escaping gases, and a pair of round hoppers closed with bell-shaped valves through which the charge is introduced into the furnace. The materials are brought up to the hoppers in small dump cars or skips that are hauled up an inclined external skip hoist. The raw material to be fed into the furnace is divided into a number of small charges that are introduced into the furnace at 10- to 15-min intervals. Slag is drawn off from the top of the melt about once every 2 hr, and the iron itself is drawn off or tapped about five times a day.
The air used to supply the blast in a blast furnace is preheated to temperatures between approximately 540° and 870° C. The heating is performed in stoves, cylinders containing networks of firebrick. The bricks in the stoves are heated for several hours by burning blast-furnace gas, the waste gases from the top of the furnace. Then the flame is turned off and the air for the blast is blown through the stove. The weight of air used in the operation of a blast furnace exceeds the total weight of the other raw materials employed. An important development in blast furnace technology, the pressurizing of furnaces, was introduced after World War II. By “throttling” the flow of gas from the furnace vents, the pressure within the furnace may be built up to 1.7 atm or more. The pressurizing technique makes possible better combustion of the coke and higher output of pig iron. The output of many blast furnaces can be increased 25 percent by pressurizing. Experimental installations have also shown that enriching the air blast with oxygen can increase the output of blast furnaces.
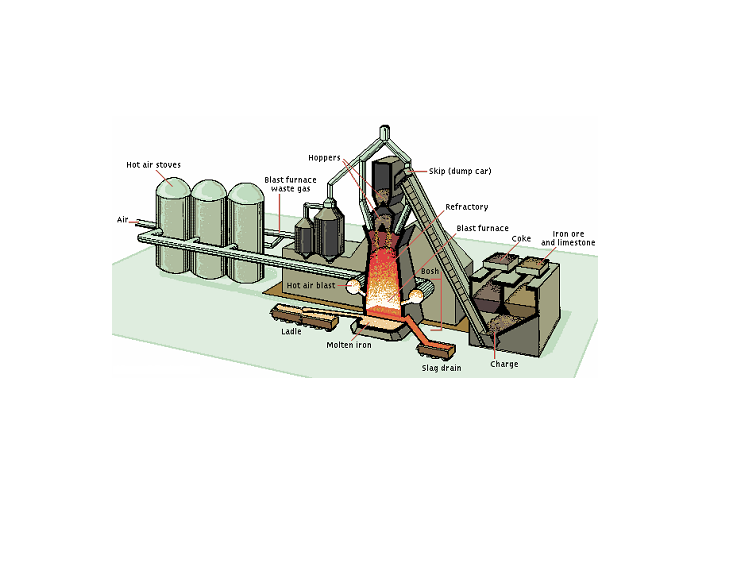
Modern-day blast furnaces are operated in conjunction with basic oxygen furnaces and sometimes the older open-hearth furnaces as part of a single steel-producing plant. In such plants the molten pig iron is used to charge the steel furnaces. The molten metal from several blast furnaces may be mixed in a large ladle before it is converted to steel, to minimize any irregularities in the composition of the individual melts.
Words and expressions
pig iron - чугун
iron ore - железная руда
coke - кокс
limestone - известняк
blast furnace - доменная печь
charge (мет) - загрузка, засыпка, завалка, шихта
slag - шлак
steel shell - стальной кожух
bosh - заплечики доменной печи
tuyere - фурма
hopper - бункер; воронка загрузочная
dump car - думпкар; опрокидывающаяся вагонетка;
самосвал
skip - скип; ковш; бадья; вагонетка (опрокидная)
open-hearth furnace - мартеновская печь
melt - плавка
Exercise 1
Ответьтенаследующиевопросы:
-
What basic materials are used in pig iron manufacture? -
What is burned as a fuel to heat the blast furnace? -
What is used in the blast furnace process as an additional source of carbon monoxide? -
Does ordinary pig iron produced by blast furnaces contain 50% of iron? -
What does a typical blast furnace consist of? -
Is raw material to be fed into the furnace charged in one big portion? -
Is air used in a blast furnace preheated to temperatures between approximately 200° and 470° C.? -
Is the weight of air used in operation of a blast furnace less than the total weight of other raw materials employed? -
When pressurizing of blast furnaces was introduced? -
What process can increase the output of blast furnaces?
Exercise 2
Заполните пропуски недостающими по смыслу словами, используя текст:
-
The basic materials used for the manufacture of … are iron ore, coke, and limestone. -
Ordinary pig iron as produced by blast furnaces contains about 92 percent of … . -
A typical blast furnace is lined by … bricks. -
The height of the blast furnace is about … meters. -
The air used to supply the blast in a blast furnace is … to temperatures between approximately 540° and 870° C. -
The heating of air supplied to blast furnace is performed in stoves, cylinders containing networks of …. -
The … in the stoves are heated for several hours by burning blast-furnace gas, the waste gases from the top of the furnace. -
The weight of … used in the operation of a blast furnace exceeds the total weight of the other raw materials employed. -
The pressurizing technique makes possible better combustion of the … and higher output of … iron. -
The output of many blast furnaces can be … 25 percent by pressurizing.
Exercise 3
Соответствуют ли данные предложения содержанию текста: