Добавлен: 03.12.2023
Просмотров: 199
Скачиваний: 3
ВНИМАНИЕ! Если данный файл нарушает Ваши авторские права, то обязательно сообщите нам.

Рисунок 2.1 - Схема ремонтного цикла электровозов серий ВЛ10, ВЛ80
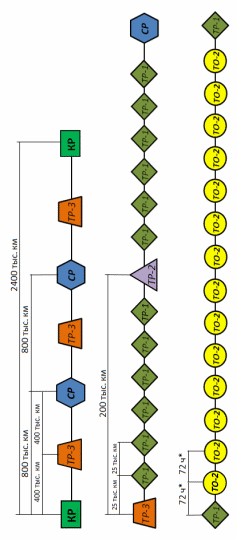
3 Способы очистки, осмотра и контроля
Научные исследования показали, что только благодаря качественной очистке сборочных единиц и деталей в процессе ремонта ресурс отремонтированных изделий повышается на 25-30%, а производительность ремонтников на 15-20%. Поэтому очистные работы при ремонте локомотивов имеют первостепенное значение.
Очистка в процессе ремонта преследует следующие цели:
-
обеспечение качества ремонта, высокой производительности труда работников, культуры производства и выполнение санитарно-гигиенических требований; -
подготовка деталей для их дефектации, контроля геометрических размеров и физико-химических параметров; -
исключение или значительное сокращение коррозии деталей в период нахождения изделий в ремонте; -
обеспечение требуемой чистоты поверхностей деталей при сборке агрегатов, узлов и систем.
При организации процесса очистки учитываются свойства материала деталей, поскольку эти свойства могут изменяться при использовании разных способов очистки, что может стать причиной коррозионного разрушения при воздействии агрессивных моющих и очищающих сред или при механическом повреждении поверхностей в результате соударения частиц твердой очищающей среды с поверхностями деталей.
Объект ремонта в процессе эксплуатации покрывается сухой или пропитанной влагой и маслом пылью; на поверхностях, охлаждаемых водой, появляется накипь, а на омываемых маслом – смолистые отложения и нагар. Металлические детали не только загрязняются, но и покрываются коррозией или окислами. Частицы загрязнения удерживаются на деталях или за счет молекулярного притяжения, или механическим сцеплением вследствие шероховатости поверхности. По своему составу и свойствам загрязнения представляют собой сложные продукты взаимодействия как органических, так и неорганических соединений, различных по природе образования и условиям формирования.
3.1 Классификация видов очистки
Существует такие виды очистки деталей как механическая, химическая, комбинированная (химико-механическая), термическая и ультразвуковая.
3.1.1 Механическая очистка деталей
К этому виду очистки условно отнесены: пневмоочистка (сдувание пыли сжатым воздухом), очистка механическим инструментом, абразивная, гидравлическая очистка.
Сдувание пыли сжатым воздухом с поверхности деталей эффективно лишь в том случае, когда очищаемые поверхности покрыты сухой пылью, т.е. когда загрязнение плохо сцеплено с поверхностью детали. Очистка ведется обычно в отдельном помещении или камере, которые оборудованы мощной вытяжной вентиляцией. В отдельных случаях воздух предварительно очищают от влаги и масла. Рекомендуемое давление воздуха 2,5÷3,5 кгс/см2.
К очистке механическим инструментом прибегают для удаления с поверхности деталей нагара, коррозии, старой краски, окислов. Для очистки используются щетки, скребки или шкурка (наждачная или стеклянная). Применяют круглые и торцовые щетки, сделанные из стальных и латунных проволочек (диаметром 0,05÷0,25 мм), волосяных и капроновых нитей. Щетки вращаются электродвигателем или пневматическими машинами. Чем меньше диаметр щетки, тем больше допустимая частота вращения. В процессе очистки металлические щетки к поверхности детали прижимают небольшим усилием, чтобы не изогнуть концы проволочек. Кроме того, твердая и толстая проволочка оставляет на очищаемой поверхности грубые царапины. Щетки из гофрированной проволоки более упруги и служат дольше.
При очистке абразивами загрязненную поверхность детали обрабатывают мягкими или твердыми абразивами, направляемыми струей воздуха или воды. Частицы абразива, ударяясь о поверхность детали, разрушают загрязненный слой и уносят с собой частицы грязи. К мягким абразивам относятся: измельченные кукурузные початки, порошок окиси алюминия, косточковая крошка (дробленая скорлупа ореха, косточек персика, абрикоса, алычи и т.д.). Мягкие абразивы используют главным образом для очистки деталей с электрической изоляцией от прочно приставшей тонкой пленки загрязнения и деталей из легких металлов от любых загрязнений.
Твердость частиц HRC56÷62.Твердые абразивы применяют для удаления нагара, коррозии, окислов и старой краски с поверхности деталей из черных и цветных металлов. На рисунке 3.1 показана схема очистки деталей с электрической изоляцией крупными и мелкими абразивами.
Для очистки деталей локомотивов косточковой крошкой применяют установки А 231.05, как показано на рисунке 3.2. Установка имеет три основные части: камеру, циклонный фильтр с отстойником и вентилятор. Камера в свою очередь состоит из рабочей части, бункера и круглого вращающегося стола для укладки очищаемых деталей. Косточковую крошку засыпают через дверцы камеры 1 в верхнюю часть бункера 8, откуда она через клапан 7, величина
открытия которого регулируется ножной педалью, поступает в нижнюю часть бункера и далее к смесителю 6. Сжатый воздух, подаваемый в смеситель, увлекает абразив и через сопло 10, направляемое рукой рабочего, с силой выбрасывает его на поверхность очищаемой детали. Отработавшая крошка скапливается в верхней части бункера и в дальнейшем после промывки может быть использована повторно.
Воздух, загрязненный пылью косточковой крошки и различными взвешенными частицами (нагара, ржавчины, грязи), пройдя циклонный фильтр 3, очищается и вентилятором 2 выбрасывается в атмосферу. Задержанные фильтром частицы опускаются в отстойник 4 с водяной пленкой. За процессом очистки наблюдают через смотровое стекло. Камера освещается двумя лампами. Продолжительность очистки, зависит от размеров очищаемой детали и характера загрязнения.
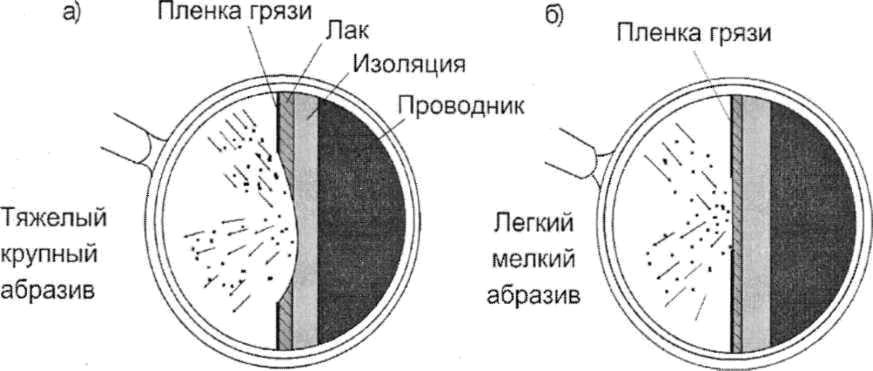
а – тяжелым крупным абразивом; б – легким мелким абразивом
Рисунок 3.1 – Очистка деталей с электрической изоляцией
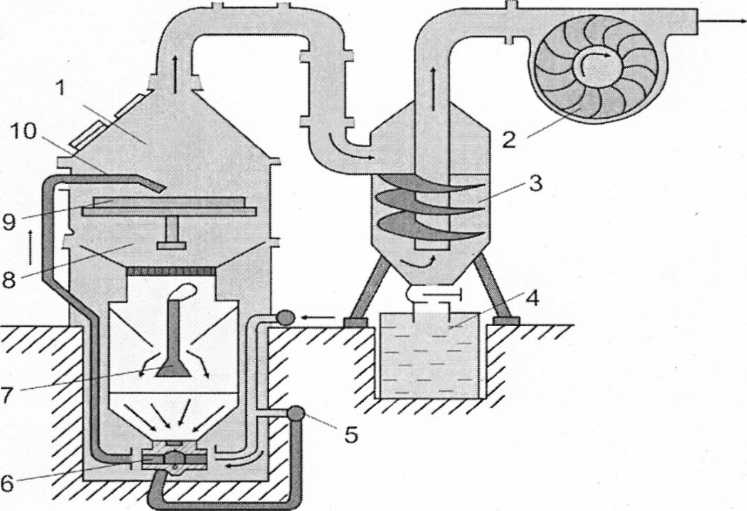
1 – рабочая часть камеры; 2 – вентилятор; 3 – циклонный фильтр; 4 – водяной; отстойник;
5 – вентиль; 6 – смеситель; 7 – клапан; 8 – бункер; 9 – стол; 10 – сопло
Рисунок 3.2 – Схема установки типа А231.05 для очистки деталей косточковой крошкой
Для очистки деталей металлической крошкой используют установку А 512, а для очистки кварцевым песком, установку П 20-55. На рисунке 3.3 показана пескоструйная установка.
При очистке деталей сухими абразивами выделяется много пыли. Поэтому абразивную очистку желательно вести в отдельных, хорошо вентилируемых помещениях. Чтобы абразивная пыль не попадала в легкие и глаза, рабочий обслуживающий установку, должен иметь респиратор и очки. После очистки твердыми абразивами детали, омываемые маслом, подлежат тщательному ополаскиванию.
Для гидроабразивного вида очистки деталей, особенно от нагара, применяют установку, работающую по принципу раздельной подачи песка и воды, показанную на рисунке 3.4. Основные элементы установки: двухкамерный пескоструйный аппарат со смесителями, аккумулятор воды и сопла. Давление воздуха в камерах песка и аккумуляторе воды поддерживается в пределах 4-5 кгс/см
2.
Песок из нижней камеры 4 под давлением воздуха поступает в смеситель 2, где подхватывается воздухом и по резиновому шлангу поступает к центральному каналу сопла 1. Одновременно к соплу подводится под давлением вода. При выходе из сопла струи смешиваются. Образующаяся смесь воды и песка с силой
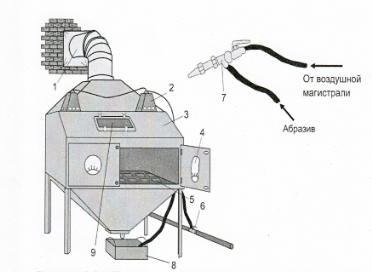
1 – вентиляционная труба; 2 – фонари; 3 – кожух; 4 – защитный рукав; 5 – решетка;
6 – кран воздушной магистрали; 7 – смеситель; 8 – ящик с абразивом;
9 – смотровое окно
Рисунок 3.3 – Пескоструйная установка
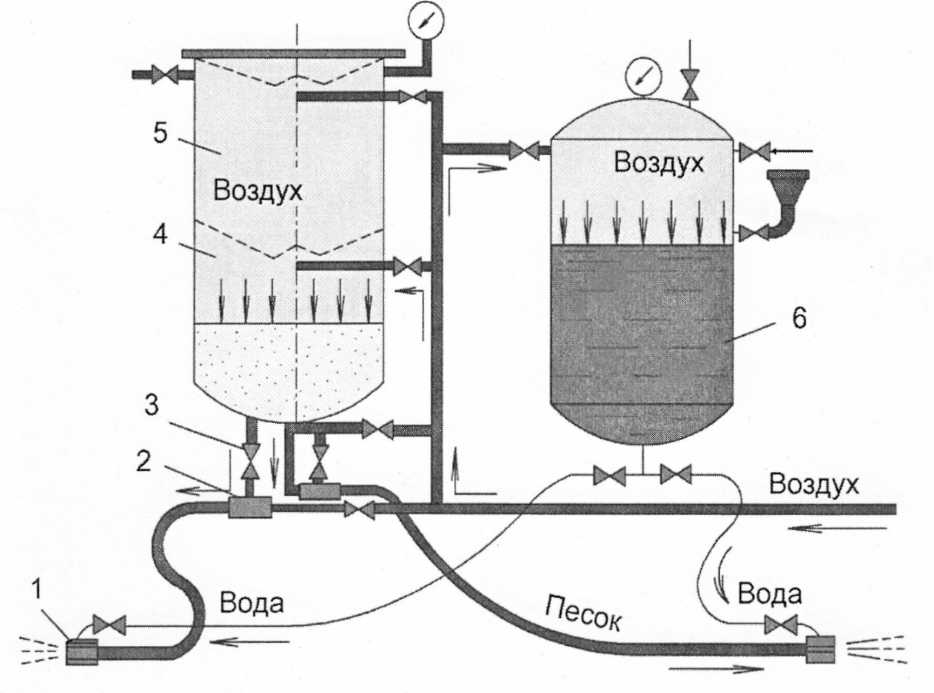
1 – сопло; 2 – смеситель; 3 – вентиль; 4 – нижняя камера для песка; 5 – верхняя камера для песка; 6 – аккумулятор воды
Рисунок 3.4 – Схема установки для гидроабразивной очистки
подается на очищаемую поверхность. Перекрыв вентиль 3, можно поверхности, подвергнутые очистке, промыть водой и продуть сжатым воздухом. В воду добавляют антикоррозионные присадки нитрит натрия 0,3÷0,4%, эмульсон 0,5-1% или ингибиторы. В качестве абразива применяют кварцевый песок.
Виброабразивный способ очистки деталей от нагара – один из механических. Виброабразивная очистка заключается в следующем: в контейнер, которому вибратором сообщается колебательное движение, загружают очищаемые детали и подают моющую жидкость с содержанием мелкозернистого абразива высокой твердости. Вследствие колебаний контейнера очищаемые детали и абразивные частицы прижимаются друг к другу, совершают поступательное и вращательное движения. Механическим воздействием зерен абразива разрушаются твердые загрязнения. Моющая жидкость интенсифицирует это разрушение и удаление загрязнений. Процесс виброабразивной очистки проходит три стадии: грубое шлифование (снятие нагара и лакового слоя пленки), тонкое шлифование (снятие остатков нагара), полирование (до чистоты поверхности 8÷9 класса). Виброабразивная обработка повышает также микротвердость обрабатываемой поверхности деталей. Этот способ весьма эффективен.
В качестве разновидности виброабразивной очистки может быть рекомендована обработка мелких деталей (например, клапанов, толкателей и др.) во вращающемся барабане с жидким наполнителем (керосин, дизельное топливо, МС-8, лабомид-203). Барабан загружают на 75% его объема и вращают с частотой 16÷17 об/мин.
Обработка деталей абразивами очень эффективна. Однако при неумелом использовании этого способа вместо пользы можно получить вред. Например, при обработке деталей, покрытых электрической изоляцией, крупными абразивами с чрезмерно высоким давлением воздуха вместе с пленкой грязи можно легко удалить и изоляционный слой. Чтобы этого не случилось, нужно заранее опытным путем подбирать размер частиц абразива и давления воздуха. Особенно это важно для очистки деталей, покрытых электрической изоляцией и полудой.
Гидравлическая очистка подразделяется на гидродушевую и гидроциркуляционную. Гидродушевая очистка в сочетании с набором щеток широко используется для наружной мойки локомотивов (рисунок 3.5).
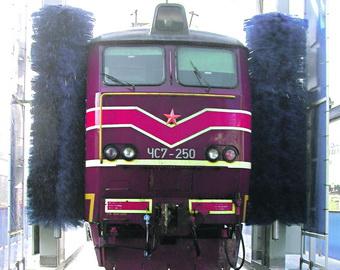
Рисунок 3.5 – Гидродушевая очистка в сочетании с набором щеток
Гидроциркуляционную очистку обычно применяют для очистки внутренних поверхностей трубопроводов, секций холодильников и теплообменников путем принудительной циркуляции водяного раствора под определенным давлением, как показано на рисунке 3.6.
Для очистки водой секций холодильников, кроме гидроциркуляционной, используют и гидродинамическую очистку, при которой водовоздушная смесь с большой скоростью прогоняется через трубки, создавая в них импульсные удары, способствующие отслаиванию накипи. Стенд для гидродинамической очистки состоит из двух подвижных коллекторов с зажимами для секций, эжектора и пульсатора.
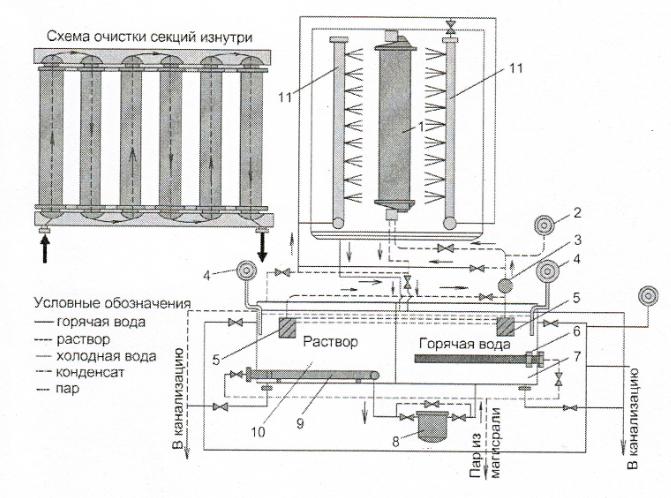
1 – секции холодильника; 2 – манометр; 3 – водяной насос; 4 – термометр; 5 – фильтр;
6 – барботер; 7 – бак для горячей воды; 8 – конденсационный горшок; 9 – теплообменник;
10 – бак для раствора; 11 – душевая система
Рисунок 3.6 – Схема установки для очистки внутренних и наружных поверхностей секций
холодильника.
Секции очищают в следующем порядке: предварительно секцию заполняют водой, а затем импульсами продолжительностью 1÷2 с подают сжатый воздух. Для повышения эффективности очистки водовоздушную смесь сначала подают с одной стороны секции, а затем с противоположной.
На крупных ремонтных заводах для очистки масляных каналов в блоке цилиндров и коленчатого вала двигателей после общей мойки применяют дополнительную обработку в установке с пульсирующим потоком жидкости (рисунок 3.7).
Принцип действия установки следующий: насос 1 подает жидкость через фильтр 7 в воздушно-гидравлический аккумулятор 6, где она скапливается и поступает затем через клапан 4 и сопло 3 определенными порциями в промываемые каналы детали. Остатки жидкости собираются в баке 2. Под действием пульсирующего потока посторонние частицы, находящиеся в каналах, деталей, отрываются и выбрасываются наружу.