Добавлен: 03.12.2023
Просмотров: 201
Скачиваний: 3
ВНИМАНИЕ! Если данный файл нарушает Ваши авторские права, то обязательно сообщите нам.
3.1.2 Химическая очистка деталей
Современные способы химической очистки деталей основаны на применении химического раствора для размягчения и растворения загрязнения, нарушения его сцепления с поверхностью металла и удержания во взвешенном состоянии в растворе.
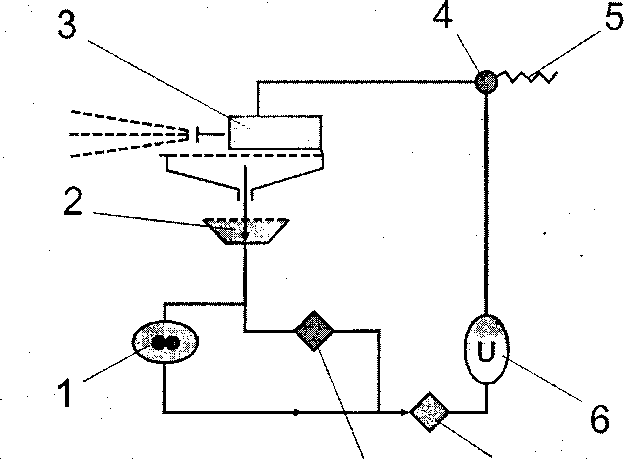
1 – насос; 2 – бак; 3 – сопло; 4 – клапан; 5 – пружина; 6 – воздушный гидравлический аккумулятор;7 – фильтр; 8 – предохранительный клапан.
Рисунок 3.7 – Схема установки для промывки каналов пульсирующим потоком жидкости
При химической очистке используют водные растворы: щелочные (каустическая и кальцинированная сода, едкий калий) для очистки обычного загрязнения, масляных отложений, нагара и кислотные (соляная, серная, фосфорная и другие кислоты) для удаления накипи, ржавчины, окислов. Кроме того, применяют органические растворители (осветленный керосин, бензин, ацетон, бензол, уайт-спирит, трихлорэтилен, четыреххлористый углерод и т.п.) для удаления загрязнений, не поддающихся очистке в щелочах, или там, где нельзя применять щелочи из-за их агрессивности.
В последнее время в ремонтной практике находят широкое применение различные поверхностно-активные вещества (ПАВ) в сочетании с неорганическими и органическими добавками. Такими эффективными моющими препаратами являются МЛ-51 и МЛ-52, представляющие собой смесь ПАВ с электролитами – натриевыми солями угольной, фосфорной и кремниевых кислот. Применяют эти препараты для очистки деталей, загрязненных масляными отложениями. Водный раствор препарата МЛ-51 (10÷20 г/л) рекомендуется для очистки струйным способом, а препарата МЛ-52 (25÷35 г/л) – способом погружения.
Эмульгаторы – активные вещества (жидкое стекло, мыло, тринатрийфосфат, поверхностно-активные вещества ОП-7, ОП-10 и т.п.), которые обволакивают капли масла особой пленкой, ослабляющей силу сцепления масла с металлом, и способствуют формированию мельчайших пузырьков масла в растворе, т.е. эмульсии. Присутствие в растворе эмульгаторов, а также хромпика или жирового солидола предохраняет детали от коррозии.
Циркуляция или возмущение раствора у очищаемой поверхности достигается пропусканием через раствор сжатого воздуха или пара, нагревом раствора до кипения, вращением небольших пропеллеров, перемещением деталей в растворе
, опрыскиванием, покачиванием раствора через изделие и, наконец, созданием быстрых колебаний раствора вибраторами или ультразвуком.
В зависимости от того, каким способом достигается перемещение раствора у поверхности очищаемой детали, физико-химическую очистку подразделяют на следующие способы: вываркой (погружением), струйным, принудительной циркуляцией раствора, парами растворителя и другие.
Технологический процесс химической очистки состоит из трех операций: сортировки, очистки, ополаскивания и сушки.
Сортировка деталей перед очисткой ведется по следующим признакам: по размерам, характеру загрязнения, чистоте обработки поверхностей, материалу, из которого изготовлены детали, материалу покрытия. Детали с высокой чистотой обработки поверхностей (подшипники качения, прецизионные детали и т.п.) желательно очищать в растворах с органическими растворителями, так как при очистке в щелочных растворах с их поверхности смывается тонкая жировая пленка, которая предохраняет детали от ржавления на открытом воздухе.
Очистка деталей от нагара и накипи в расплаве солей и щелочи заключается в следующем. Под действием раствора, нагретого до температуры 80÷90 °С, загрязнение размягчается. Масляная' пленка, расширяясь, разрушается; на поверхности детали образуются мельчайшие капли масла с грязевыми частицами. Однако сила сцепления масла и металла продолжает удерживать эти капли на поверхности детали. Для снижения силы сцепления в состав раствора вводят эмульгаторы, а чтобы ускорить отрыв капель, раствор заставляют интенсивно перемещаться в очищаемой поверхности.
Ополаскивание деталей водой – операция заключительная. Она необходима для удаления с поверхности деталей следов щелочи или кислоты, опасных в отношении коррозии металла, а также вредно влияющих на кожу рук. Если мойка ведется холодной водой, деталь после этого сушат, а если горячей, то процесс сушки отпадает.
Очистка вываркой (погружением). Этим простейшим способом чаще всего пользуются для очистки громоздких деталей, а также мелких деталей, загружаемых в ванну с раствором или в расплав солей и щелочи в сетчатых корзинах.
Установка для очистки блока или картера дизеля, рамы тележки в растворе имеет обычно два отделения. Одно заполняется раствором, подогреваемым паром, который поступает в змеевик, а другое наполняется проточной горячей водой. Ток горячей воды создается насосом. Для удаления пара, поднимающегося с поверхности раствора или воды, над ванной имеется кожух, соединенный с вытяжной вентиляцией. Детали после очистки в растворе в течение 10÷15 минут помещают в горячую воду для ополаскивания.
Установка для очистки нагара и накипи вываркой (выжиганием) в растворе солей и щелочи, как показано на рисунке 3.8, состоит из четырех ванн. Первая (из нержавеющей стали) заполняется раствором солей и щелочи (в процентном отношении по массе): каустическая сода – 65, натрий азотнокислый – 30, соль поваренная – 5. Температура расплава 380÷420 °С. Детали из черных металлов выдерживают 5÷15 минут, а из алюминиевых сплавов – 3÷5 минут, затем их перегружают в сетчатой корзине 5 в ванну 2 и промывают водой. Для нейтрализации остатков щелочи детали погружают в ванну 3, заполненную 50%-м раствором ингибированной соляной кислоты (для деталей из черных металлов) или водным раствором фосфорной кислоты (85 г/л) и хромового ангидрида (125 г/л) – деталей из алюминиевых сплавов. Окончательно детали из черных металлов промывают в четвертой ванне с горячим водным раствором кальцинированной соды (3÷5 г/л) и тринатрийфосфата (1,5÷2 г/л), а детали из алюминиевых сплавов - в чистой горячей воде.
Недостаток очистки детали вываркой (погружением) – быстрое загрязнение раствора (или расплава) и, следовательно, необходимость частой её заменой.
Однако очистка и обезжиривание деталей происходят хорошо и довольно быстро, особенно в расплаве солей и щелочи.
Очистка струйным (душевым) способом выгодно отличается от очистки вываркой тем, что химическое действие раствора сочетается с динамическим воздействием его струи. Кроме того, можно применять растворы меньшей концентрации.
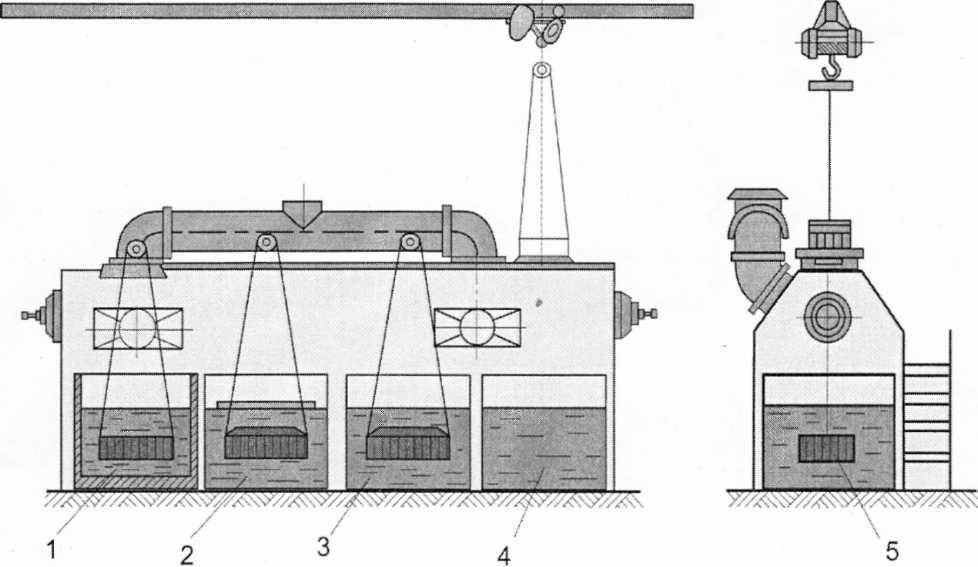
Рисунок 3.8 – Установка для очистки деталей от нагара и накипи в расплаве солей и щелочей
Струйная очистка осуществляется в одно-, двух- и многокамерных машинах тупикового или проходного типа. Для очистки деталей длиной до 9 м, шириной до З м и высотой до 1,4 м служит моечная машина тупикового типа модели ММД-13Б (типа А74). Моечная камера, как показано на рисунке 3.9, имеет систему принудительной вентиляции для отсоса паровоздушной смеси и сушки детали, два бака (для раствора и воды) с паровым подогревом, а также душевую систему 2 и трубопроводы. Детали, подлежащие очистке, укладывают: крупногабаритные – на тележку 3, а мелкие – на ту же тележку, но в сетчатых корзинах.
Моечная камера с одного торца имеет глухую стенку, а с другого – дверь, через которую загруженная деталями тележка механизмом передвижения со скоростью 4,5 м/мин вкатывается в моечную камеру. После закрытия двери включается одновременно душевая система и механизм передвижения тележки. Тележка в течение всего процесса очистки совершает возвратно-поступательное движение внутри моечной камеры со скоростью 0,78 м/мин. Ход тележки 3,9 метров. Очистка горячим раствором продолжается 15÷25 минут, а затем в течение 7 минут детали ополаскивают горячей водой.
Раздельный слив раствора и воды обеспечивается перекидным сливным лотком, размещенным на полу моечной камеры. После ополаскивания душевую систему отключают и тележку останавливают. Для ускорения сушки деталей открывают боковые двери. Раствор разогревается паровым змеевиком, а вода - насыщенным паром.
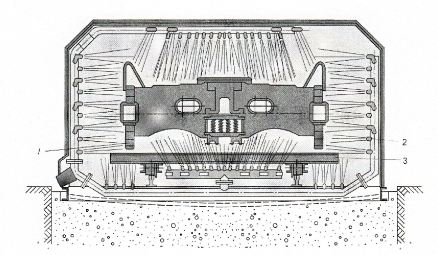
Рисунок 3.9 – Моечная камера машины ММД-13Б
На рисунке 3.10 показана моечная машина А328 для очистки мелких деталей щелочными или органическими растворами. Она состоит из моечной камеры 2 с патрубком 1, вытяжной вентиляции и душевой системы, бака для раствора с паровым змеевиком и барботером. Последние служат для разогрева раствора.
Если в качестве моющей жидкости применяют керосин, через змеевик пропускают холодную воду для его охлаждения. Внутри камеры смонтирован круглый стол диаметром 900 мм, который соединен через редуктор 5 с электродвигателем. Давление жидкости в душевой системе создается насосом 3, приводимым в действие электродвигателем 4. Загружают камеру через дверку 6. Детали на столе располагают на некотором расстоянии друг от друга. Чтобы удержать на столе, их обтягивают сеткой. Плотно закрыв дверку 6, включают последовательно привод стола и душевую систему (21 сопло с отверстиями диаметром 2 мм).
Стол совершает сложное вращательное движение (3,6 об/мин). После 10÷15 минут очистки прекращается подача раствора и, не выключая привод стола, открывают вентиль для обдувки деталей сжатым воздухом до их высыхания. После этого детали извлекают из камеры. Для обдувания в камере имеется трубка с отверстиями.
Очистка принудительной циркуляцией раствора применяют для очистки внутренних полостей деталей: секций холодильника, теплообменника, крышек цилиндров и т.п. Раствор для очистки внутренних поверхностей трубок и вода для наружной мойки секций холодильника залиты в баки, емкостью каждый 2,4 м3. Раствор нагревают теплообменником, а воду – паром, выходящим из отверстий барботера. Внутри камеры укрепляют шесть секций и через них прокачивают раствор каустической соды при очистке масляных секций и раствор соляной кислоты – водяных секциях сначала в одном, а затем в противоположном направлении. После очистки раствором, которая продолжалась примерно 75 минут, секции промывают, прокачивая через них в течение 15 минут воду.
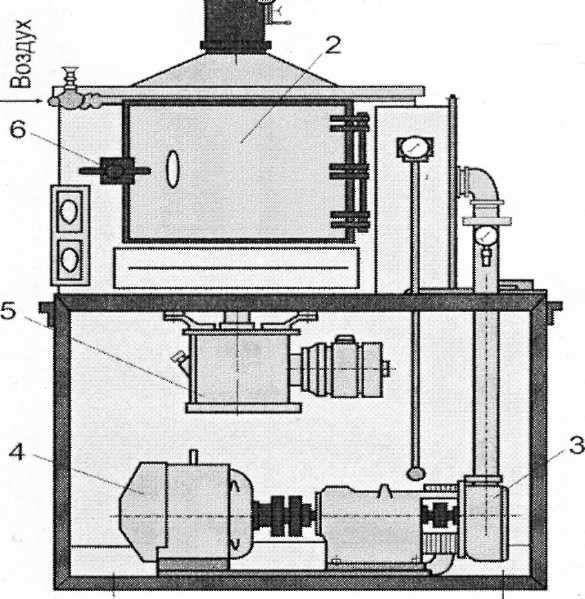
1 – патрубок; 2 – моечная камера; 3 – насос; 4 – электродвигатель; 5 – редуктор; 6 – дверка
Рисунок 3.10 – Моечная машина типа А328 для очистки мелких деталей
Температуру раствора и воды поддерживают в пределах 80+95°С. В случае очистки секций раствором с поверхностно-активным веществом их не промывают водой, а пропаривают, для чего на нижнем коллекторе предусмотрен паровой вентиль. Длительность промывки секций зависит от состава и температуры раствора, а также от степени загрязненности секций. Наружную поверхность секций обмывают горячей водой при закрытых дверях камеры и при включенном вентиляторе отсоса пара. Общее число сопел с отверстиями 2 мм для наружной мойки 1320 штук. Производительность насоса 120 м3/ч.
Сущность этого способа очистки парами растворителя состоит в следующем: в паровое облако достаточно сильного растворителя помещают холодную деталь, которая быстро покрывается конденсатом растворителя; растворитель стекая с поверхности детали, уносит с собой частицы грязи. Процесс продолжается до тех пор, пока деталь не нагреется до температуры паров. Чаще всего этот способ применяют для удаления прочно приставшей пленки грязи с поверхности деталей с электрической изоляцией, т. е. с якорей и катушек полюсов электрических машин.