Добавлен: 03.12.2023
Просмотров: 202
Скачиваний: 3
ВНИМАНИЕ! Если данный файл нарушает Ваши авторские права, то обязательно сообщите нам.
Установка для очистки деталей парами растворителя, как показано на рисунке 3.11, состоит из моечной камеры с принудительной вентиляцией, устройства для очистки загрязненного растворителя и напорной магистрали нижней части смонтирован паровой змеевик для нагрева растворителя. Верхняя часть камеры открытая, ее горловина окружена змеевиком для циркуляции холодной воды.
Установка работает следующим образом. Включается нижний (паровой) змеевик 10, вентиляция и верхний (охлаждающий) змеевик 2. Образующиеся при кипении растворителя пары устремляются вверх, достигнув холодного пространства камеры, т.е. зоны верхнего змеевика 2 начинают конденсироваться и в виде капель падать вниз. Конденсат, образующийся на поверхности верхних труб змеевика, стекает в лоток 13 и далее в отстойник 4. Часть пара, не успевшая превратиться в конденсат, отсасывается вентилятором 15. Когда в камеру с горячими испарениями помещают в подвешенном состоянии холодную деталь, например якорь, то его поверхность сразу покрывается конденсатом, который, стекая, увлекает с собой частицы загрязнения. Местные, более крупные отложения грязи, оставшиеся на поверхности детали, удаляют струей чистого растворителя, подаваемого, насосом 3 через резиновый шланг и наконечник. Загрязненный растворитель отсасывается из ванны насосом 8, пропускается через очистительное устройство 6 и накапливается в запасном баке 5. В качестве растворителя применяют трихлорэтилен и перхлорэтилен, температура кипения, которых соответственно 87 и 121 °С. Желательно применять растворы, имеющие температуру кипения выше, чем у воды. Тогда отпадает необходимость сушки изоляции якорей и катушек после очистки.
При работе на этой установке нужно, во-первых, строго контролировать температуру нагревания раствора. При чрезмерном нагревании раствора может произойти его разложение и образование опасных химических соединений. Во- вторых, время выдержки деталей в камере должно быть не более времени, необходимого для растворения грязи. Особенно это касается деталей с электрической изоляцией, изготовленных на основе различных кремниевых соединений. Эти соединения при продолжительном нахождении в парах растворителя могут сами начать растворяться, т.е. вместе с грязью незаметно может быть снята и изоляционная лаковая пленка. Время выдержки в камере устанавливают опытным путем. Преимуществами этого способа очистки являются: быстрота и эффективность очистки всегда чистым растворителем; отсутствие необходимости сушки в печи якорей, катушек и других деталей с электрической изоляцией.
В ремонтной практике получило распространение удаление загрязнений с поверхностей узлов электрических машин и аппаратов органическими растворителями.
3.1.3 Термическая очистка
Термический способ очистки основан на удалении загрязнений их нагревом до температуры сгорания или разрушения (отслоения от детали). Существует очистка открытым огнем (кислородно-ацетиленовое или керосиновое пламя) и погружением в расплавы солей и щелочей, а также обжигая детали в термопечи.
Открытым огнем очищают от смолистых отложений и нагара глушитель шума выпуска, выпускные коллекторы и патрубки дизеля. К очистке деталей в расплавах солей и щелочей прибегают для удаления нагара и накипи. Очистка и обезжиривание деталей в расплавах солей и щелочей происходят
эффективно и довольно быстро. Однако тому способу присущи следующие недостатки: очистка оказывает влияние на свойства металла; быстро загрязняется расплав, исключается очистка деталей сложной формы и тонкостенных деталей из-за возможности их деформации. Схема термической очистки показана на рисунке 3.12. Процесс очистки сложен и малопроизводителен, требует ручного труда. Термохимический способ применяют для удаления нагара и накипи с деталей из черных металлов. На этой стадии очистки происходит выгорание и химическое взаимодействие расплава с отложениями. После 5÷10-минутной выдержки в расплаве детали промывают водой.
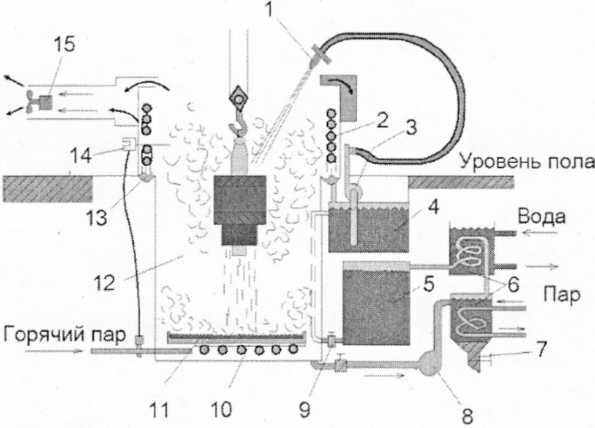
1 – напорная магистраль; 2, 10 – охлаждающий и паровой змеевики; 3,8 – насосы; 4 – отстойник; 5 – запасной бак; 6 – очистительное устройство; 7 – воронка для спуска отстоя; 9 – вентиль; 11 – ванна с растворителем; 12 – моечная камера; 13 – лоток; 14 – термостат, управляющий процессом нагрева; 15 – вентилятор
Рисунок 3.11 – Схема испарительной установки для очистки парами растворителя
Бурное парообразование способствует разрушению остатков отложений и растворению щелочного расплава.
Для нейтрализации остатков щелочи детали промывают сначала в кислом растворе (раствор фосфорной кислоты 85 г/л с добавлением хромового ангидрида 125 г/л), а затем горячей водой или моющим раствором на основе синтетических моющих средств.
Этот способ обычно применяют на специализированных ремонтных заводах. Для удаления накипи и продуктов коррозии, кроме перечисленных способов, используют воздействие ингибированной соляной кислоты, обрабатывая детали в 10÷12% растворе при температуре 75÷85 °С в течение 20÷25 минут. После обработки в кислом растворе их ополаскивают в растворе кальцинированной соды 5 г/л и тринатрийфосфата 2 г/л.
3.1.4 Ультразвуковая очистка
Ультразвуковая очистка – способ очистки поверхности твердых тел, основанный на возбуждении в моющем растворе колебаний ультразвуковой частоты. Это сложный процесс, сочетающий кавитацию с действием акустических течений, акустокапиллярным эффектом, радиационным давлением, что приводит кразрушению загрязнений и отделению их от поверхности очищаемого тела. Под действием ультразвука в растворе образуются области сжатия и разряжения, распространяющиеся по направлению ультразвуковых волн. В зоне разрежения, на границе между поверхностью детали и жидкостью образуется полость С (рисунок 3.13), куда под действием местного давления из пор Ж капилляров К выталкивается раствор и загрязнение. Через полпериода колебаний в том же месте образуется область сжатия, в результате пузырек «схлопывается» и происходит гидравлический удар, способный создавать большое мгновенное местное давление, намного превышающее исходное, вызванное распространением ультразвуковых колебаний.
Это явление сопровождается характерным шумом. При этом способе у очищаемых поверхностей деталей создается интенсивное колебание раствора за счет ударных волн, возникающих при пропускании через раствор ультразвука.
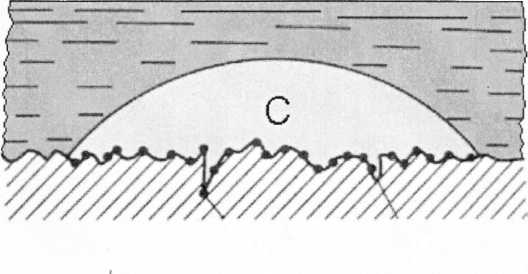
Рисунок 3.12 – Схема термической очистки
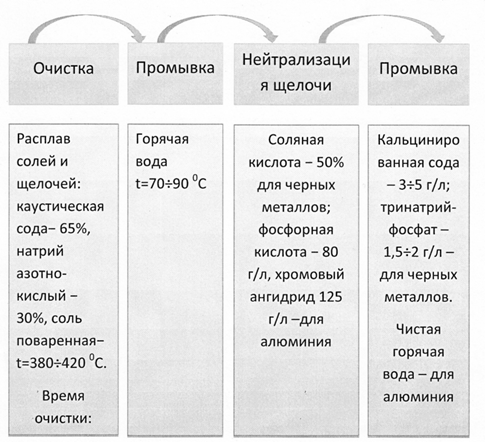
Рисунок 3.13 – Схема образования полости в растворе под действием ультразвуковых волн
Под действием ультразвука в растворе образуются области сжатия и разрежения, распространяющиеся по направлению ультразвуковых волн. Благодаря большой частоте ультразвуковых колебаний процессы повторяются до 20000 раз в 1 с. Под действием раствора и гидравлических ударов жировая пленка на поверхности детали разрушается, загрязнения превращаются в эмульсию и уносятся вместе с раствором. Скорость и качество ультразвуковой очистки зависят от химической активности и температуры раствора, а также удельной мощности ультразвука.
Температура раствора 50÷60 С, удельная мощность ультразвука 1,5÷2 Вт на 1см2 очищаемой поверхности. В промышленности, как правило, ультразвуковой способ применяют для очистки мелких деталей. В последнее время его начинают внедрять и при ремонте тепловозов, например, для очистки фильтров.
Важнейшим физическим эффектом, вызывающим интенсивную очистку очищаемых тел, является кавитация.
Вначале под кавитацией подразумевали разрыв жидкости при создании в ней отрицательных давлений. Под кавитацией в настоящее время подразумевают не истинный разрыв жидкости, а пульсацию, рост, расщепление и другие типы движения уже присутствующих в жидкости пузырьков, а также их взаимодействие, когда в жидкостях создается пониженное, а затем повышенное давление. В отличие от движения обычных, равновесных пузырьков (они могут вводиться извне или образовываться спонтанно при кипении, дегазации, протекании химической реакции и т.д.), для движения кавитационных пузырьков должна существовать фаза их расширения и последующего сжатия.
Диапазон частот ультразвуковых аппаратов для очистки лежит в пределах 20÷40 кГц; интенсивность ультразвуковых колебаний обычно составляет 0,5÷5 Вт/см2. Выбор оптимальной интенсивности имеет существенное значение для ультразвуковой очистки.
Важным фактором, способствующим ультразвуковой очистке, является значительная интенсификация физико-химических процессов в жидкости под действием ультразвуковых колебаний, в частности, процесса растворения, что напрямую связано с выбором состава моющей жидкости.
Моющая жидкость должна обладать как можно большей химической активностью по отношению к загрязнениям, но в тоже время быть нейтральной по отношению к материалу очищаемого изделия. Обычно чистую воду применять для ультразвуковой очистки нецелесообразно. Более эффективны водные растворы щелочей, кислот, солей с добавлением поверхностно-активных веществ.
Наиболее высокая растворяющая способность наблюдается у органических растворителей. Органические растворители хорошо проникают в зазоры, щели, отверстия, растворяя в них загрязнения. Недостатком этих растворителей является необходимость их частой регенерации, так как загрязненность их маслами в значительной степени отражается на качестве очистки.
Интенсивность очистки зависит от температуры жидкости. С одной стороны, повышение температуры приводит к увеличению давления насыщенных паров в пузырьках, препятствующего сжатию пузырьков, а, следовательно, и возникновению ударных волн и кумулятивных струй, что снижает эффективность воздействия отдельного кавитационного пузырька.
С другой стороны, при повышении температуры жидкости уменьшается растворимость газов, что приводит к увеличению количества кавитационных пузырьков. Эти противоположно действующие факторы и обусловливают оптимальный температурный интервал воздействия кавитации на очистку. Экспериментально установлено, что наиболее благоприятной для эффективного растворяющего действия и воздействия ультразвуковой кавитации является температура моющей жидкости 20÷25 °С. Отмечено, что понижение температуры ниже 18÷20 °С нецелесообразно ввиду того, что на поверхности может конденсироваться влага, способная вызвать коррозию. В некоторых случаях, например, при очистке шлифованных деталей от жидких масел оптимальной является температура 40÷50 °С, а при очистке деталей от полировочной пасты температуру растворителя целесообразно выбирать в районе 60 °С.
Ультразвуковая установка для очистки деталей, как показано на рисунке 3.14, работает следующим образом.
Источник питания преобразует переменное напряжение промышленной частоты 50 Гц в постоянное напряжение от 100 до 310 В, которым питаются генераторы. Генераторы представляют собой полупроводниковые преобразователи постоянного тока в переменный ток ультразвуковой частоты. Количество генераторов равно числу ультразвуковых излучателей.
Система излучателей – это емкость с установленными на ней ультразвуковыми излучателями. Ультразвуковые излучатели могут быть двух типов – магнитострикционные и пьезоэлектрические. В последнее время магнитострикционные излучатели практически не применяются из-за их низкого КПД.
Количество и конфигурация размещения ультразвуковых излучателей в емкости зависят от типа очищаемых деталей. Очищаемая поверхность детали должна находиться напротив излучателя, но не соприкасаться с ним. Как правило, излучатели устанавливаются на дно технологической емкости, но могут устанавливаться и сбоку, дорабатываемую деталь подвешивают или помещают в сетку.

Рисунок 3.14 – Схема ультразвуковой установки для очистки деталей
В настоящее время ультразвуковая очистка получила широкое распространение. С помощью ультразвука можно чистить как крупногабаритные детали, так и мелкие детали. Важнейшим достоинством ультразвуковой очистки является возможность очистки деталей сложной формы, в том числе, с полостями и отверстиями различной формы и размеров. При этом качество очистки внутренних полостей такое же, как и открытой поверхности.
Ультразвуковая очистка легко встраивается практически в любой технологический процесс, в частности, при конвейерном ремонте деталей. Поскольку в процессе ультразвуковой очистки не используется ручной труд, его несложно автоматизировать.
Технология ультразвуковой очистки реализуется с помощью ультразвуковых диспергаторов и ультразвуковых ванн.
4 Технология ремонта быстродействующего выключателя
Разборку быстродействующих выключателей (далее БВ) начинают после их продувки сжатым воздухом под давлением 300 кПа. Выключатель протирают салфетками, снимают дугогасительную камеру, веерные полюсы, изоляционную плиту с дугогасительным устройством, блокировочное устройство, пневматический привод, якорь с подвижным контактом, индуктивный шунт, размагничивающий виток, удерживающую катушку, магнитопровод, изоляционные стержни.