Файл: 1. Исходная информация для проектирования 6 Базовая информация 6.docx
ВУЗ: Не указан
Категория: Не указан
Дисциплина: Не указана
Добавлен: 09.01.2024
Просмотров: 412
Скачиваний: 1
ВНИМАНИЕ! Если данный файл нарушает Ваши авторские права, то обязательно сообщите нам.
Оглавление
ВЕДЕНИЕ 4
1. Исходная информация для проектирования: 6
1.1. Базовая информация 6
1.2. Руководящая информация 6
1.3. Справочная информация 6
2. Технологический раздел: 7
2.1. Анализ технических требований на объект производства 7
2.2. Анализ технологичности конструкции детали 8
2.2. Определение типа производства 8
2.4. Технико – экономическое обоснование выбора заготовки 10
2.4.1. Анализ способов получения заготовки и выбор оптимального 10
2.4.2. Описание марки материала 13
2.4.3. Экономическое обоснование способа получения заготовки 14
2.4.4. Расчет припусков 16
2.5. Разработка технологического процесса механической обработки детали 19
2.5.1. Cоставление маршрута обработки 19
2.5.2. Выбор оборудования 23
2.6. Расчет и выбор режимов резания 29
2.7. Нормирование технологического процесса 40
2.8. Разработка технологической операции и фрагмента управляющей программы 42
3. Конструкторский раздел: 43
3.1. Расчет и конструирование станочного приспособления 43
4. Раздел Безопасность жизнедеятельности: 47
4.1. Анализ возможных опасных, вредных факторов и ЧС при работе на участке 47
4.2.Разработка мероприятий по снижению опасных и вредных факторов при работе на участке 49
4.3.Разработка мероприятий по снижению вредного воздействия техпроцесса на участке на природу 50
5. Экономический раздел 52
5.1. Расчет себестоимости изготовления продукции и технико-экономических показателей работы участка 52
5.2. Производственные расчёты 55
5.2.1. Расчёт количества, стоимости и коэффициента загрузки основного оборудования. Определение стоимости вспомогательного оборудования. 56
5.2.2. Расчёт численности работников по категориям 61
5.2.3. Расчёт площади производственного участка. 65
5.3. Экономические расчёты 67
5.3.1. Формирование сметы затрат на изготовление и реализацию всего объёма продукции 67
5.3.2. Расчёт затрат на основные материалы 68
5.3.3. Расчёт затрат на вспомогательные материалы 69
5.3.4. Определение фонда оплаты труда основных производственных рабочих 69
5.3.5. Расчёт отчислений страховых взносов на социальные нужды 72
5.3.6. Определение расходов на содержание и эксплуатацию оборудования 72
5.3.6.1. Затраты на амортизацию производственного оборудования участка 73
5.3.6.2. Затраты на обслуживание и текущий ремонт производственного оборудования 74
5.3.6.3. Расчёт затрат на электроснабжение 74
5.3.6.4. Расчёт затрат на инструменты и приспособления 76
76
5.3.7. Расчёт цеховых расходов 78
5.3.7.1. Расчёт затрат на амортизацию помещений здания производственного участка 79
5.3.7.2. Расчёт затрат на содержание зданий 79
5.3.7.3. Расчёт затрат на охрану труда. 80
5.3.7.4. Расчёт затрат на испытания, изобретательство и рационализаторство. 80
5.3.7.5. Расчёт затрат на оплату труда руководителей специалистов и служащих. 81
5.3.7.6. Расчёт прочих цеховых расходов 82
5.3.7.7. Сумма цеховых расходов. 82
5.3.8. Расчёт общезаводских (общехозяйственных) расходов 83
5.3.9. Расчёт производственной себестоимости изготовления объёма продукции 83
5.3.10. Расчёт внепроизводственных расходов 84
5.3.11. Расчёт непроизводственных расходов 84
5.3.12. Расчёт полной себестоимости изготовления объёма продукции 84
5.3.13. Оформление сметы затрат на изготовление годовой программы изделия «Фланец» по рассчитанным показателям 84
5. Формирование плановой калькуляции затрат на изготовление единицы продукции 85
5.4.1. Расчёт показателей величин затрат по статьям с 1 по 11 плановой калькуляции затрат на изготовление единицы продукции 85
5.4.2. Расчёт оптовой и отпускной цены на реализацию единицы продукции. 86
5.4.3. Оформление плановой калькуляции на производство и реализацию единицы продукции по рассчитанным показателям 87
5.5. Технико-экономические показатели эффективности работы участка при изготовлении и реализации продукции 87
5.5.1. Определение фондоотдачи, фондоёмкости и фондовооружённости производства 88
5.5.2. Определение рентабельности 89
5.5.3. Определение производительности труда основных рабочих производственного участка в стоимостном выражении 90
5.6. Формирование комплекса исходных и технико-экономических показателей работы участка по изготовлению изделия «Фланец» 90
ЗАКЛЮЧЕНИЕ 92
СПИСОК ЛИТЕРАТУРЫ 93
ВЕДЕНИЕ
Увеличение производительности труда разработчиков новых изделий, сокращение сроков проектирования, повышение качества разработки проектов – важнейшие проблемы, решение которых определяет уровень научно-технического процесса общества.
Моделирование технологических процессов интересная и сложная задача, решение которой имеет большое практическое значение. Построение модели технологического процесса с возможностью проигрывания и изменением технологических характеристик модели дает мощный инструмент в области исследования технологических процессов, как уже действующих на предприятиях, так и проектируемых, с целью улучшения их экономических показателей.
Создание моделей технологических процессов служит основой для:
-
проектирования новых технологических производств; -
выдача задания на проектирования оборудования; -
разработки бизнес-планов, с высокой надежностью полученных в них показателей.
В настоящее время в ведущих странах мира ведутся серьезные исследования в области моделирования технологических процессов. Разрабатываются новые подходы к созданию моделей и возможности получения на их основе качественной информации по экономике технологических процессов.
Автоматизация технологического процессов включает в себя два этапа:
-
моделирование технологического процесса; -
экономическое обоснование моделирования. Для внедрения разработанных технологических моделей необходимо их экономическое обоснование, т.е. выгодно ли будет предприятию их внедрение и если нет, то как можно их оптимизировать.
За сравнительно короткий срок станки с ЧПУ зарекомендовали себя как эффективное автоматизированное оборудование, позволяющее достигнуть высоких технических и экономических показателей, решить ряд важных социальных задач. Основные преимущества производства с помощью станков с ЧПУ по сравнению с производством, использующим универсальные станки с ручным управлением, следующие:
-
сокращение основного и вспомогательного времени изготовления деталей; -
повышение точности обработки; -
простота и малое время переналадки; -
возможность использования менее квалифицированной рабочей силы и сокращение потребности в высококвалифицированной рабочей силе; -
возможность применения многостаночного обслуживания; -
снижение затрат на специальные приспособления; -
сокращение цикла подготовки производства новых изделий и сроков их поставки; -
концентрация операций, что обеспечивает сокращение оборотных средств в незавершенном производстве, а также затрат на транспортирование и контроль деталей; -
уменьшение числа бракованных изделий по вине рабочего.
Опыт показывает, что наибольший экономический эффект дает изготовление на станках с ЧПУ сложных деталей, в том числе из труднообрабатываемых материалов, повышенной точности, требующих выполнения многих технологических операций.
Качество работы, выполненной продукции зависит от правильной эксплуатации и качественного ремонта электрооборудования.
Исходя из выше сказанного деталь «Фланец» целесообразно обрабатывать с использованием станков с ЧПУ.
Целью курсового проекта является разработка технологического процесса изготовления детали «Фланец» с использованием современного оборудования высокопроизводительной оснастки с целью снижения себестоимости и улучшения организации труда.
1. Исходная информация для проектирования:
1.1. Базовая информация
-
Базовый технологический процесс изготовления детали «Фланец». -
Рабочие чертежи детали «Фланец». -
Режим работы цеха – двусменный. -
Материал детали –сталь 35 ГОСТ1050-2016г. -
Годовая программа выпуска N=4000 шт.
1.2. Руководящая информация
Стандарты ЕСКД; ЕСТПП; ЕСТД.
1.3. Справочная информация
-
Вид исходной заготовки – прокат. -
Имеющееся в наличии оборудование. -
Нормативные данные по выбору заготовки, припусков, режимов резания, нормированию и т.д. -
Справочная литература.
2. Технологический раздел:
2.1. Анализ технических требований на объект производства
В качестве исходного чертежа для курсового проекта предложен чертеж детали «Фланец».
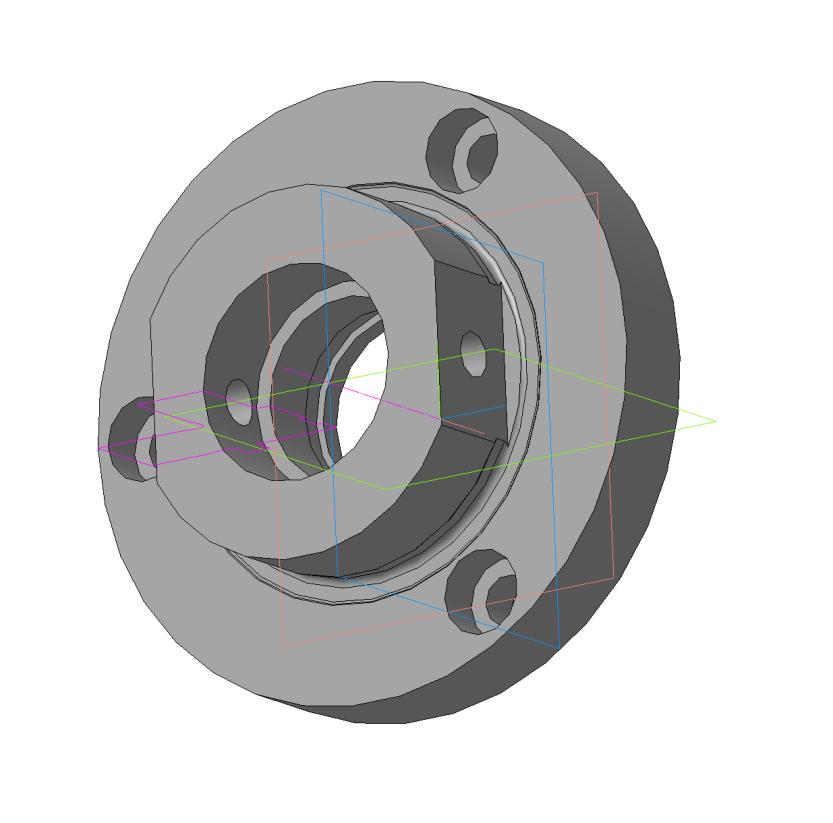
Рисунок 1- Фланец
Для того, чтобы проанализировать чертеж данной детали необходимо провести анализ ее конструкции, охарактеризовать материал заготовки, проверить деталь на технологичность. Произвести качественный и количественный анализ.
Деталь «Фланец» представляет собой тело вращения типа «фланец», со ступенчатой наружной поверхностью и центральным ступенчатым отверстием. Наружные ступени с двух сторон имеют поверхности ⌀55h7мм, с классом шероховатости Ra1,6 и фланцевую часть ⌀80мм с 3 отверстиями под крепежный элемент ⌀6,6Н12мм –сквозное и ⌀11мм, глубиной 6мм на делительном диаметре 66мм. Центральное отверстие имеет ступени ⌀48мм глубиной 3мм, ⌀24Н9мм, глубиной 3мм и канавкой для выхода шлифовального круга шириной 4мм и ⌀26мм, следующая ступень М24х2-7Н, глубиной 8мм и последняя ступень ⌀28мм, глубиной 12мм с фаской 2х45ᵒ. Шероховатьсть поверхностей соответственно Ra1,6, Ra6,3. На ⌀48h8мм детали выполнены симметричные лыски на растоянии 43мм относительно центра, глубиной 15мм. на лысках расположено сквозное отверстие М6-7Н, с осью, перпендикулярной центральной. Остальные размеры выполнены по классу точности H14, h14. Деталь выполнена из конструкционной качественной стали марки 35 ГОСТ 1050-2013, которая обладает достаточно высокими прочностными свойствами, хорошо обрабатывается режущими инструментами, принимает закалку в широком диапазоне твердости при охлаждении в воде или масле.