Файл: 1 Технологический раздел 1 Описание сварной конструкции, ее назначение 5.doc
Добавлен: 18.01.2024
Просмотров: 186
Скачиваний: 3
ВНИМАНИЕ! Если данный файл нарушает Ваши авторские права, то обязательно сообщите нам.
Стенд предназначен для сборки на прихватках двутавровых балок длиной до 20 м, высотой 260 – 1000 мм, шириной пояса до 800 мм и толщиной пояса до 50 мм.
Стенд для сборки состоит из двух основных частей: стационарного стеллажа – стенда, на котором укладывается и собираются элементы балки, и передвижного портала с пневмоприжимами для сборки двутавра.
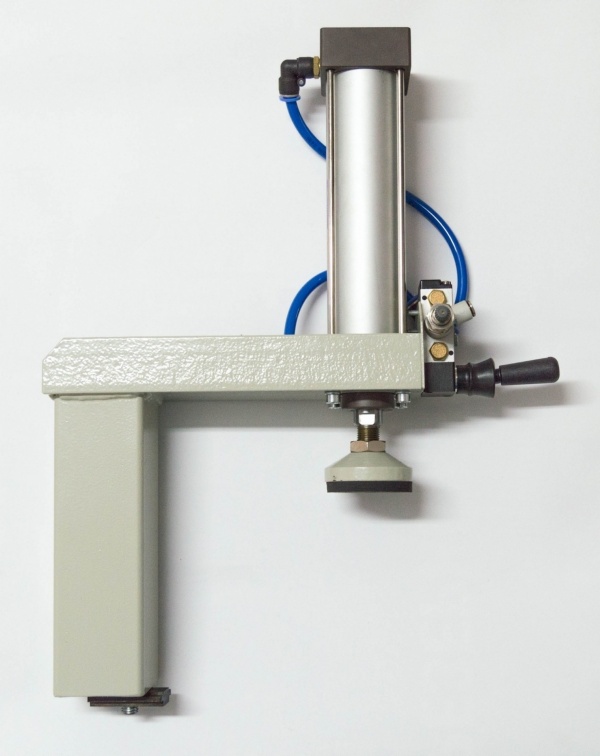
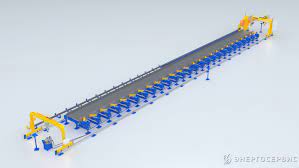
Рисунок 1.7.1 пневмоприжим Рисунок 1.7.2 Стенд
Установка для сборки балок
Для сборки двутавровой балки выбираю сборочную плиту. В проектируемом варианте сборку предполагается осуществлять на стенде с самоходным сборочным порталом оборудованном пневмоприжимами. Стенд предназначен для сборки на прихватках двутавровых балок длиной до 20 м, высотой 260 – 1000 мм, шириной пояса до 800 мм и толщиной пояса до 50 мм. Стенд для сборки состоит из двух основных частей: стационарного стеллажа – стенда, на котором укладываются и собираются элементы балки. При изготовлении сварных балок в цехах целесообразно сначала сварить стыки поясов и стенки, так как стыковые швы являются наиболее ответственными, поэтому для уменьшения остаточных напряжений варить их следует при отсутствии закреплений в свариваемых листах. При сборке пояса или стенки необходимо, чтобы продольные оси стыкуемых листов легли по одной прямой линии, смещение стыкуемых кромок из плоскости листов не выходило за пределы допустимых отклонений и чтобы зазор был выдержан согласно чертежу.
Правильное положение осей стыкуемых листов проверяют обычно длинной линейкой, приложенной к оси или к боковым кромкам листов. Смещение кромок устраняют обычно клином, а требуемый зазор устанавливают при помощи болтовой стяжки или сборочной планки. Собранный стык сваривается вручную высококачественными электродами, полуавтоматом или автоматом под флюсом. При сварке под флюсом необходимо приставить входные и выходные планки и принять меры против протекания расплавленного металла и шлака. После сварки проверяют качество шва и зачищают торцы шва и усиления. Сваренные пояса и стенка поступают на сборку балки. Способ сборки балки зависит от характера и конструкции применяемых приспособлений и запроектированного метода сварки поясных швов.
В настоящее время сварку длинных поясных швов выполняют преимущественно автоматами под флюсом. Балку собирают из трех ее основных элементов (поясов и стенки), сваривают поясные швы автоматом, а затем устанавливают поперечные ребра жесткости и приваривают их полуавтоматом или вручную.
Сборку сварных балок выполняют при помощи хомутов и прихваток или в специальном кондукторе. При сборке балки с помощью хомутов на стеллаже или горизонтальной плите укладывают нижний пояс. На середине пояса параллельно его оси наносят две риски, расстояние между которыми равно толщине вертикальной стенки. По рискам на расстоянии 1-1.5 м друг от друга устанавливают и прикрепляют струбцинами или прихватками сборочные уголки, между которыми устанавливается вертикальная стенка. В местах, где вертикальная стенка значительно искривлена, для совмещения ее с рисками на поясе можно пользоваться скобой и клиньями. Для уничтожения зазора между вертикальной стенкой и поясом пользуются хомутом. Затем накладывают верхний пояс, проверяют правильность положения стенки и верхнего пояса, зажимают собранную балку хомутами и ставят прихватки. Потом освобождают собранную балку от хомутов и подают на автоматическую сварку под флюсом поясных швов. Наилучший провар поясных швов получается при автоматической сварке "в лодочку". При сварке поясных швов двумя автоматами "в угол" при горизонтальном положении вертикальной стенки, производительность сварочных работ возрастает, причем искривление продольной оси балки будет небольшое, так как горизонтальный прогиб, вызванный наложением первой пары швов, будет почти ликвидирован обратным прогибом от сварки второй пары. При сварке двумя автоматами в угол при вертикальном положении стенки остаточный прогиб будет заметный по вогнутости балки в сторону пояса, на котором выполнялась первая пара швов. После сварки поясных швов размечают и выставляют поперечные ребра жесткости и приваривают их вручную или полуавтоматами. Приварку ребер следует вести от середины балки к ее концам, попеременно с обеих сторон.
Если поясные швы собираемой балки будут выполняться вручную, то описанный порядок сборки балки следует изменить. В этом случае после установки вертикальной стенки на нижний пояс ставят ребра жесткости, прихватывают их, а потом устанавливают верхний пояс и зажимают собранную балку хомутами. Дальше собранная балка идет на ручную или полуавтоматическую сварку поясных швов и приварку ребер жесткости. При горизонтальном положении стенки сварку ведут от середины балки к ее концам. При серийном и массовом производстве сборку балок производят в кондукторах, конструкции которых позволяют значительно уменьшить трудоемкость рабочих операций по укладке и закреплению поясов и стенки балок в требуемом положении. Для повышения механизации трудоемких сборочно-сварочных операций и увеличения производительности применяют для изготовления балок специализированные кондукторы-кантователи. Сборка в специализированных кондукторах-кантователях не требует постановки прихваток, так как собранные элементы надежно удерживаются в требуемом положении быстродействующими фиксирующими и закрепляющими устройствами. В настоящее время строят механизированные поточные линии для массового изготовления сварных двутавровых балок с предварительным растяжением вертикальной стенки во избежание ее выпучивания от действия остаточных напряжений сжатия. Сборка двутавровой балки производится на прихватках. Основные параметры наложения прихваток берутся из справочных данных. Прихватки проставляются РДС. Сборка на прихватках должна обеспечивать транспортировку балки к месту сварки без изменения взаимного расположения свариваемых деталей. Сварка поясных швов балки производится механизированной сваркой под флюсом. При выполнении поясного шва его начало и конец выводятся на выводные планки, удаляемые после сварки кислородной резкой. Положение свариваемых конструкций должно обеспечивать наиболее удобное и безопасное условие для работы сварщика и получение надлежащего качества швов. Исходя из этого, сварка поясных швов производится в положении “лодочка”
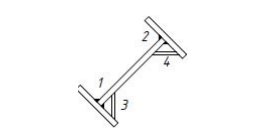
Рисунок 1.7.3 – Порядок наложения поясных швов
Для уменьшения деформаций от сварки необходимо при сварке балки выполнять сварные швы в определенной последовательности. Вводные и выводные планки вырезаются на гильотинных ножницах, кислородной резкой, в моем случае машиной термической резки, в ходе раскроя листов. Планки изготавливают из деловых отходов той же марки стали.
После сборки и сварки двутавровой балки выполняются отделочные операции. Механическая обработка сварных швов после сварки позволяет удалить оставшийся шлак и убедиться в качестве соединения. Оставшийся шлак может стать причиной возникновения коррозионных процессов. Для очистки металла от шлака будет применяться угловая шлифовальную машинку Rupes BA 225N. Угловая зачистная минимашинка Rupes BA 225N для зачистки и обдирки, защитный кожух и стопор диска, Ш диска 125 мм, мощность 950 Вт, частота вращения 8500 об/мин, вес 1,8 кг.
Таблица 1.7.1 Технические характеристики Rupes ВА 225N
| | |
Диаметр диска | 125 мм | |
Частота вращения | 8500 об/мин | |
Мощность | 950 Вт | |
Вес | 1,8 кг | |
Кнопка блокировки вала | есть | |
Боковая рукоятка | есть | |
Защитный кожух | есть | |
1.8 Методы борьбы со сварочными деформациями
При сварке металл сварного шва и около шовной зоны нагревается до высоких температур, в результате наблюдается расширение и удлинение свариваемой детали, особенно по оси шва. Одновременно, со стороны менее нагретых частей на разогретую до высоких температур зону воздействует усилия, вызывающие в нагретой зоне деформации укорочения. Значительная часть этой деформации в зоне прилегающей к сварному шву переходит в пластическую деформацию, которая затем, при остывании металла, становится источником возникновения остаточных растягивающих напряжений. Эти напряжения формируют в металле скрытый запас энергии, который способен провоцировать разрушение металла около шовной зоны. и способствует активизации процесса коррозии.
Для снятия остаточных напряжений после сварки проводят термообработку. Применяют как общий нагрев конструкции (отпуск или отжиг), так и местный неравномерный нагрев.
В моем случае для устранения деформация рекомендую способ механической правки, позволяющий получить требуемую геометрию изделия и одновременно снять часть остаточных напряжений за счет реализации скрытой потенции металла (за счет остаточных напряжений) конструкции к деформированию. Дефекты устраняют термическим с местным или общим нагревом, холодным механическим, термомеханическим способами. Для правки термическим методом с полным отжигом конструкцию закрепляют в устройстве, которое создает давление на искривленный участок, затем нагревают в печи. Способ локального нагрева основан на сжимании металла при остывании. Для исправления дефектов искривленное место греют горелкой или сварочной дугой. Так как прилегающие участки остаются холодными, зона нагрева не может значительно расшириться. После охлаждения растянутый участок выпрямляется. Термическим способом выправляют любые виды деформаций, однако при работе с тонкостенным металлом следует учитывать его особенности:
тепло при местном нагреве тонких стальных листов быстро распространяется по всей площади, поэтому величина усилия сжатия оказывается недостаточной для исправления дефекта;
температура локального нагрева тонкостенного металла не должна превышать 600 — 650⁰C, поскольку при увеличении температуры начнется образование пластических деформаций даже при отсутствии напряжения.
При механической правке растянутые участки деформируются внешними нагрузками в обратном направлении. Дефекты устраняют применением изгибания, вальцовки, растяжения, ковкой, прокаткой роликами.
Термомеханическую правку проводят с подогревом растянутого участка до 700 — 800⁰C и внешнего воздействия. Для выправления участков с большим растяжением сначала из избытков металла холодной рихтовкой формируют выступы в форме куполов. Затем по отдельности нагревают и резко охлаждают. Способы снятия напряжений, минимизации деформаций и правки выбираю в зависимости от размеров и формы деталей, сложности конструкции. При этом учитывают эффективность метода, трудоемкость, величину финансовых затрат.
-
Выбор методов контроля качества готовой продукции
Сварные швы контролируются визуально-измерительным методом при помощи универсального шаблона сварщика УШС-3, лупы 4х -10х , мерительных инструментов, стандартных образцов.
Строительные балки относятся к категории ответственных изделий, поэтому для выполнения операции неразрушающего контроля качества протяженных сварных швов возможен выбор рентгенографического или ультразвукового методов контроля. Ультразвуковой метод контроля требует особой подготовки– зачистку зоны контроля. Радиографический способ требует наличия специального помещения.
Детали затрудняет применение радиографического контроля, поэтому использую ультразвуковой метод. Предварительную подготовку поверхности выполним еще перед сваркой, во время механической обработки свариваемых поверхностей под сварку. Сварка под флюсом исключает появление брызг, поэтому остывшее изделие может быть подвержено УЗ - контролю после зачистки сварных швов.
Для осуществления контроля выбираю ультразвуковой дефектоскоп «ТОМОГРАФИК УД4-Т»
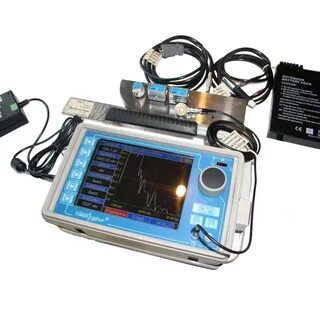
Рисунок 1.9.1 Дефектоскоп «ТОМОГРАФИК УД4-Т»
Технические характеристики:
-
Диапазон рабочих частот, мГц: 0,2 – 0,10; -
Диапазон измеряемых глубин, мм: 0,5 – 5000; -
Динамический диапазон, дБ: 140; -
Глубина временной регулировки чувствительности, дБ: 80; -
Длительность развертки, мкс: 8 - 1600 -
Построение кривой ВРЧ: ручное и автоматическое до 256 точек; -
Погрешность измерения координат дефекта, мм: не более 0,1 -
Погрешность измерения эквивалентной площади, %: не более 10 -
Погрешность измерения временных интервалов, мкс: не более 0,025; -
Встроенный архив результатов контроля, записей : 500; -
Встроенных архив настроек, записей : 500.
Ультразвуковой дефектоскоп УД4-Т «Томографик» предназначен для поиска дефектов в сварных швах и изделиях из металлов. Диапазон измеряемых глубин: от 0,5 до 5 000 мм. Работает в режиме дефектоскопа, толщиномера, тензометра.
Дефектоскоп проводит автоматическую настройку ВРЧ, измеряет параметры каждого применяемого ПЭП. Измеряет эквивалентную площадь дефекта, оценивает его конфигурацию и размеры. Измеряет акустические свойства материалов без использования дополнительного оборудования.