Файл: Оборудование, приспособления и инструмент для разборочносборочных работ.docx
ВУЗ: Не указан
Категория: Не указан
Дисциплина: Не указана
Добавлен: 08.11.2023
Просмотров: 518
Скачиваний: 7
ВНИМАНИЕ! Если данный файл нарушает Ваши авторские права, то обязательно сообщите нам.
В качестве обрабатывающего инструмента в этих станках применяется борштанга, представляющая собой вал с закрепленными на нем резцами. Борштанга кроме вращательного движения совершает поступательное перемещение на величину, превышающую длину обрабатываемых постелей.
Диаметры резания подобраны по диаметрам отверстий в блоках цилиндров. Для обеспечения необходимой жесткости инструмента борштанга опирается на дополнительные регулируемые опоры станка. Блок цилиндров закрепляется на станине также на жестких прецизионных опорах.
Вращение и подачу борштанге обеспечивает электромеханический привод с бесступенчатым регулированием скорости вращения и осевой подачи. Привод расположен в передней бабке станка.
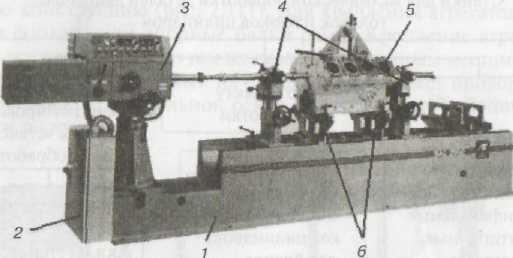
Рис. 2.113. Горизонтально-расточной станок ВАС 1500 для обработки постелей коленчатых и распределительных валов двигателей легковых автомобилей фирмы AZ MACHING TOOLS (Италия): 1— станина; 2— блок питания: 3 — передняя бабка; 4— регулируемые опоры бор-штанги; 5 — блок цилиндров; 6— опоры для установки изделия
В отдельных моделях станков на передней бабке располагается панель управления, в других моделях она вынесена в отдельный блок.
Вертикально-расточные станки для обработки блока цилиндров. Эти станки могут быть стационарными и переносными. Стационарные станки для обработки блока цилиндров отличаются от общепромышленных станков такого же типа только устройством станины, которая имеет специальную форму верхней платы для установки блока. Переносные станки разработаны специально для ПТС средней мощности, на которой применение дорогостоящего стационарного оборудования является экономически нецелесообразным.
Переносные расточные станки имеют обрабатывающую головку, которая может либо закрепляться непосредственно на блоке цилиндров, либо устанавливаться на легкую трехопорную тумбу (рис. 2.114).
Обрабатывающая головка имеет корпус, на котором закреплен электродвигатель привода шпинделя. Шпиндель вращается в подшипниках, установленных в подвижном корпусе. Корпус шпинделя посредством реечной передачи может перемещаться в вертикальном направлении вдоль оси шпинделя.
![]() ![]() Рис. 2.114. Переносные расточные станки для обработки блока цилиндров двигателей легковых и малотоннажных грузовых автомобилей фирмы KWIK-WAY(CLUA): а — FN — оснащен системой автоматического центрирования шпинделя по трем точкам относительно оси цилиндра, масса 105 кг; б— FWI1 — малогабаритный с рамным основанием, масса 89,5 кг; 1 — станина; 2— шпиндель; 3— электропривод; 4— коробка подач и скоростей; 5 — регулируемая подставка | ![]() ![]() Рис. 2.115. Прессы гидравлические фирмы ОМА (Италия): а — ОМА 660 — настольного исполнения с ручным насосом; б — ОМА 665 — напольного исполнения с электрогидравлическим приводом |
Перемещение корпуса шпинделя осуществляется вручную путем вращения маховика. Для станков, которые устанавливаются на блок цилиндров, предусмотрена автоматическая система центрирования шпинделя относительно оси цилиндра по трем точкам.
Прессы. На ПТС прессы применяются как на рабочих постах, так и на участках для работ, связанных с разборкой или сборкой сопряженных с натягом деталей типа «вал — втулка» или «втулка — втулка». Прессы для автосервиса выпускаются в настольном и напольном исполнении с ручным гидравлическим и электрогидравлическим приводами (рис. 2.115). Прессы имеют рамную станину с регулируемым по высоте рабочим столом.
В верхней части станины на траверсе закреплен силовой цилиндр, соединенный гидравлическими шлангами высокого давления с насосной установкой. Гидравлическая схема пресса с электроприводом насоса дана на рис. 2.116. Максимальное давление насоса Н ограничивается предохранительным клапаном А77, который настроен на заводе — изготовителе насосной станции. Настройка пресса на определенное усилие осуществляется в условиях эксплуатации по требованиям технологического процесса регулированием давления в напорной магистрали с помощью реле давления РД и контролем его по манометру М. Управление движением рабочего органа пресса производится посредством переключения нагнетательной магистрали с одной полости гидроцилиндра на другую с помощью распределителя Р1, действующего от рукоятки.
Приспособления для сборочно-разборочных работ
С целью ускорения технологического процесса разборки (сборки) и предохранения деталей от повреждений применяют приспособления различных конструкций. Для выпрессовки деталей широко применяют универсальные и специальные съемники. Универсальные съемники предназначены для выпрессовки ряда деталей, отличающихся размерами и конструкцией, а специальные— лишь для определенной детали.
Съемники могут быть с винтовым, гидравлическим или пневматическим приводом. В ремонтных мастерских большое распространение получили винтовые съемники, а на крупных специализированных заводах — съемники с пневмо- и гидроприводом.
Наиболее трудоемкими операциями являются разборка и сборка резьбовых соединений (они составляют около 70% всех соединений в конструкции автомобиля), особенно тех, которые были в эксплуатации и подвергались воздействию агрессивных веществ окружающей среды. Единственный путь повышения производительности труда на этих работах — максимально возможная механизация. К сожалению, в настоящее время она составляет не более 10—15% от общего объема работ данного вида.
Применение гайковертов, винтовертов, шпильковертов и т. п. позволяет повысить качество работы и значительно облегчить условия труда. Все большее распространение получают ударные гайковерты (рис. 2.66). Отсутствие реактивного момента при работе с ними позволяет использовать их для разборки-сборки резьбовых соединений большого диаметра. Они также имеют меньшую массу по сравнению с гайковертами вращательного действия.
Наибольшее распространение в АТП нашли гайковерты с пневматическим и электрическим приводом. Вместо гайковертов с электрическим приводом при напряжении 220 В и частоте 50 Гц (с коллекторным двигателем) чаще используют гайковерты с асинхронными двигателями ввиду более безопасного напряжения 36—42 В и частоте 220 Гц.
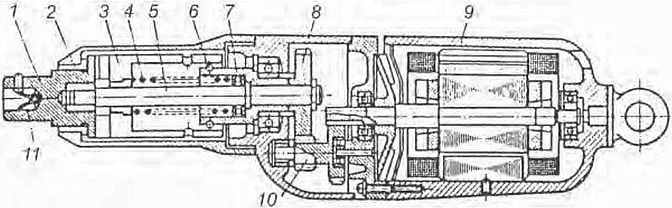
Рис. 2.66. Ударно-импульсный электрогайковерт: 1 — рабочий наконечник; 2 — втулка; 3 — ведомая полумуфта; 4,11 — пружины; 5 — шпиндель; 6 — шарики; 7 — ведущая полумуфта; 8,10 — зубчатые колеса; 9 — корпус
Пневматические гайковерты (ПГВ) имеют меньшую массу и габариты по сравнению с предыдущими, однако КПД их ниже, чем у электрических. Кроме того, требуется специальная аппаратура для очистки сжатого воздуха, а учитывая, что в АТП часто меняется давление воздуха в магистралях, могут значительно меняться рабочие параметры ПГВ (усилие затяжки и т.д.); кроме того, при увеличении нагрузки они резко теряют обороты, снижая производительность.
Несмотря на указанные недостатки, ПГВ нашли широкое распространение благодаря простоте конструкции. Торможение при их работе практически безвредно для механизма ПГВ, вплоть до полной остановки при работе.
Электрические ручные машины при работе создают меньше шума, не нуждаются в сложной подводящей сети сжатого воздуха, но в отличие от ПГВ электродвигатели гайковертов чувствительны к перегрузкам и при многократном их повторе быстро выходят из строя.
В
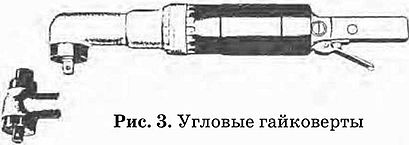
Большинство гайковертов ударного действия обеспечивают 20—40 ударов в секунду, но используются и гайковерты редкоударные — до 3 ударов в секунду. Они имеют более высокий КПД и дают более точную (тарированную) затяжку резьбовых соединений.
Отечественная промышленность выпускает гайковерты как с высокой частотой ударов (мод. ИЭ3114А, мод. ИЭ3117 и т. д.), так и редкоударные (мод. ИЭ3112, ИЭ3115А и др.).
В АТП находят также применение гайковерты мод. ИЭ-3106 (мощность электродвигателя — 240 Вт, Мкр — 6,3 кгм), мод. ИЭ-3111 (мощность электродвигателя — 400 Вт, Мкр — 25 кгм). ПГВ отечественного производства представлены моделями ИП3112 (Мкр— 10 кгм, максимальный диаметр резьбы — 14 мм), ИП3113 (Мкр — 25 кгм, максимальный диаметр резьбы — 18 мм), более новая модель — 1111-16 (реверсивный, Мкр — 26 кгм, максимальный диаметр резьбы — 18 мм).
Инструмент для сборочно-разборочных работ
Наиболее часто применяемыми для разборочно-сборочных работ являются: наборы гаечных ключей различных типов (накладные, открытые, глухие, трещоточные, торцовые, Г-образные для круглых гаек и т. д.), ключи для шпилек (роликовые, эксцентриковые), молотки слесарные простые и с медными головками, отвертки, пассатижи и т. п.
Динамометрический ключ состоит из упругого стального стержня, головки, стрелки и шкалы. В головку вставляются гаечные ключи. Шкала, укрепленная на стержне, и стрелка дают возможность контролировать крутящий момент в процессе затяжки гайки или болта.
Во время разборки (сборки) резьбовых соединений применяют трещеточные, фрикционные и коловоротные ключи со сменными головками, механизированный инструмент — гайковерты, шуруповерты и шпильковерты.
Применение механизированного инструмента позволяет увеличить производительность разборочно-сборочных работ примерно в 5 раз по сравнению с работой вручную. Гайковерты подразделяют на ручные, подвесные, переносные и стационарные.
Раздел 2. Технологический процесс и техническое обслуживание
2.1) Организация рабочих мест
При организации рабочих мест слесарей при разборке (сборке) следует учитывать условия и материальное оснащение, которые должны способствовать рациональному использованию рабочего времени и оборудования. Рабочие места должны быть оснащены современным, высокопроизводительным оборудованием, приспособлениями и инструментом.
При планировке рабочего места оборудование необходимо располагать так, чтобы рабочему было удобно работать (разбираемый агрегат, инструмент, тара находились в зоне действия рук рабочего), чтобы рабочее место было достаточно освещено. Для удобства выполнения работ механизированный инструмент подвешивают над рабочим местом на различных подвесках.
Детали разобранных агрегатов, узлов необходимо укладывать в тару или на стеллажи. Корпусные детали (блоки цилиндров, картеры коробок передач и др.) следует укладывать на деревянные настилы. На участках разборки целесообразно разбираемые детали, идущие в дальнейшем на участок мойки, укладывать в специальную решетчатую тару, имеющую малую массу и относительно высокую прочность.
Для обтирочного материала необходимо устанавливать металлические ящики с откидными крышками. Для установки, снятия и перемещения крупногабаритных деталей при разборке (сборке) агрегатов и машин рабочие места необходимо оборудовать грузоподъемными механизмами.
2.2) Технологические процессы разборки и сборки машин
Разборку выполнять после мойки или очистки. Последовательность разборки:
на отдельные сборочные единицы и узлы - на детали;
в тех пределах, которые необходимы для ремонта;
в последовательности, указанной в технологической схеме или карте (см. рис.1);
общая последовательность разборки.
Обеспечения доступа к узлам и деталям: капоты, кабина, ограждения, топливные и другие баки, двигатель, механизмы управления и силовой передачи, ходовая часть.
Технология разборки. Определяется техническими требованиями и указаниями. изложенными в технологических картах и другой технической документации.
Технологическое обеспечение – Перечень инструмента, приспособлений, стендов, подставок, грузоподъемных механизмов и другого оборудования, указанный в технологических картах.
Общие особенности и рекомендации:
разборку сборочных единиц (двигатель, топливный, масляный, водяной насосы, стартер, генератор и т. п.) выполнять на участках или рабочих местах, предназначенных для их ремонта;