Файл: Оборудование, приспособления и инструмент для разборочносборочных работ.docx
ВУЗ: Не указан
Категория: Не указан
Дисциплина: Не указана
Добавлен: 08.11.2023
Просмотров: 512
Скачиваний: 7
ВНИМАНИЕ! Если данный файл нарушает Ваши авторские права, то обязательно сообщите нам.
разборку топливного насоса, форсунок, масляного фильтра, масляного насоса системы смазки или гидросистемы, гидрораспределителя, турбокомпрессора, генератора, стартера, реле-регулятора и т. п. выполнять после предварительного испытания на стендах;
для разборки резьбовых соединений применять инструмент, обеспечивающий сохранность крепежных деталей: накидные, торцовые и т. п. ключи, ключи для выворачивания шпилек, механизированный инструмент и т. д.;
избегать вывертывания шпилек, если они не мешают выполнению последующих ремонтных операций;
перед разборкой резьбовых соединений, при необходимости, Очистить и смазать свободную часть резьбы;
·не допускать разукомплектовывания крепежных деталей;
·для обеспечения сохранности деталей при разборке соединений с гарантированным натягом (втулок, подшипников качения, шестерен и т. д.) применять гидравлические (винтовые) съемники и прессы, а так же вспомогательные приспособления – наставки, оправки и т. п.;
·не допускается разукомплектовывание деталей, работающих в паре: шатун-крышка, крышка коренного подшипника - гнездо коренного подшипника, гильза - поршень (если не подлежат замене), шестерни главной передачи, плунжерные пары, золотник – корпус гидрораспределителя и т. п.;
перед демонтажем отмечать положение деталей в узлах вращения (муфта сцепления, карданная передача и др.) для сохранения балансировки при сборке;
при текущем ремонте сохранять работающие в паре детали (если они соответствуют техническим требованиям) и при помощи меток обеспечивать сохранность их первоначального взаимного расположения (шлицевые валы и шестерни, грузы регулятора и др.)
перед разборкой сопряжений, подлежащих регулировке при эксплуатации (конические подшипники, конические пары шестерен, червяк и ролик рулевого механизма и др.) для контроля пригодности деталей убедиться в возможности выполнения ее в дальнейшем (наличие запаса регулировки);
·при разборке подшипниковых узлов, усилие прилагать к тому кольцу, которое установлено с натягом (на валу или в отверстии);
демонтированные детали укладывать на стеллажи, подставки, контейнеры и др. тару;
для предупреждения дефектов (вмятин, царапин и т. п.) запрещается
Укладывать детали в тару навалом.(Приложение 4.)
Особенности сборки типовых сопряжений и узлов.
Технологическим процессом, предшествующим сборке, является комплектование.
Комплектование – Это подбор деталей по номенклатуре (перечню), количеству, размерам и массе. Для определения номенклатуры и количества деталей могут быть использованы: комплектовочные карты или спецификации, а так же каталог деталей и сборочных единиц машины.
При комплектовании наиболее "ответственных" соединений, с целью повышения ресурса их работы применяется Селективный метод. Для этого поля допусков сопрягаемых деталей разбивают на несколько размерных групп и внутри них проводят комплектование (рис.2).
Таким способом комплектуются гильзы с поршнями, поршневые пальцы с отверстиями в бобышках поршней, золотниковые пары распределителей гидросистем, плунжерные пары топливных насосов высокого давления и др.
Сборка – соединение деталей в пары, которые образуют сопряжения. Из сопряжений и крепежных деталей собирают узлы и сборочные единицы.
Сборочные единицы установленные на раму или соединенные между собой образуют машину.
Так при сборке коробки перемены передач валы и подшипники, валы (оси) и шестерни, подшипники и корпус образуют сопряжения. Валы и оси в сборе с подшипниками и шестернями образуют узлы: первичный, вторичный, промежуточный вал. Первичный, вторичный, промежуточный вал, блок шестерен заднего хода, механизм переключения передач, установленные в корпус образуют сборочную единицу – коробку перемены передач.(Приложение 5)
Качество сборки определяется следующими основными факторами:
тщательность очистки (мойки) деталей, используемых при сборке;
соответствие геометрических параметров, шероховатости, поверхности, массы, неуравновешенности (несбалансированности) деталей и узлов параметрам, заданным технической документацией;
качество комплектования сопряжений и узлов;
использование рекомендованных смазочных, лакокрасочных, прокладочных и др. материалов, уплотняющих и стопорных элементов и т. п.;
соблюдение регламентированных технологических режимов.
Требований к сборке: усилия и последовательность затяжки резьбовых соединений, температура деталей при сборке, направление усилий, прилагаемых к деталям при запрессовывании и др.
Типовыми сопряжениями являются:
- резьбовые соединения,
- подвижные соединения (сопряжения с зазором),
- неподвижные соединения (сопряжения с натягом или прессовые),
- зубчатые передачи,
- цепные и ременные передачи,
- шпоночные и шлицевые соединения,
- конусные соединения,
- сопряжения валов (осей) с самоподжимными сальниками,
- шарнирные соединения,
- соединения при помощи заклепок.
Сборка резьбовых соединений - 25 – 30 % от общей трудоемкости сборочных работ.
Условия качества:
- соосность осей болтов, шпилек, винтов и резьбовых отверстий,
- требуемая плотность посадки в резьбе,
- отсутствие перекоса торца гайки или головки болта относительно поверхности сопрягаемой детали,
- соблюдение последовательности и величины усилий затягивания группы креплений (головка цилиндров, фланец трубного соединения, крышки корпусов редукторов и др.
- использование регламентированных способов стопорения соединений.
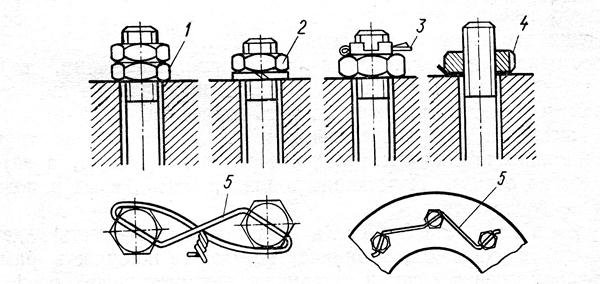
Рис. 3. Способы стопорения резьбовых соединений: 1 – контргайкой; 2 – пружинной шайбой; 3 – шплинтом; 4 – замковой шайбой; 5 – шплинтовочной проволокой.
Если резьбовое соединение стопорится контргайкой, гайку затягивают в два-три приема до отказа, затем ослабляют ее на 1/3 оборота и повторно затягивают до отказа. Затем, придерживая ключом гайку, затягивают контргайку до отказа.
При стопорении соединения пружинной шайбой гайку затягивают в два-три приема. После затяжки гайки пружинная шайба должна прилегать к детали и гайке по всей окружности. Зазор в разрезе шайбы должен быть 1...2 мм.
При стопорении гайки деформированной (замковой) шайбой один выступ шайбы отгибают на грань гайки, а второй — за кромку корпуса.
При стопорении гайки шплинтом, гайку затягивают до отказа, вставляют в отверстие вала (стержня) шплинт, концы шплинта разводят по оси вала: один — на вал (стержень болта), а другой — на плоскость гайки. Шплинт не должен выступать над плоскостью корончатой гайки.
Если группа болтов стопорится проволокой, то болты затягиваются до отказа в два-три приема, шплинтовочную проволоку в отверстия головок болтов вводят крест-накрест таким образом, чтобы после стягивания концов проволоки создавался момент, действующий в направлении закручивания болтов. Концы проволоки после шплинтования туго скручивают вместе и обрезают на расстоянии 5...7 мм от начала скрутки.
Шпильки в чугунные детали закручивают на глубину не менее 1,1, а в стальные — на 0,8 диаметра резьбы. Нарезанный конец шпильки (болта) должен выступать из гайки (контргайки) на две-три нитки резьбы.
В многоболтовых соединениях, чтобы избежать деформации деталей, гайки (болты) затягивают постепенно в два-три приема в последовательности, указанной на рис. 4.
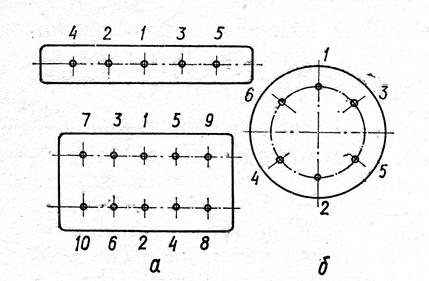
Рис. 4. Последовательность затяжки многоболтовых резьбовых соединений: а – прямоугольных; б – круглых.
Максимально допустимый момент затяжки Н м, можно определить по формуле:
Ммах = 10-3 d3σв,
где d – наружный диаметр резьбы, мм,
σв – предел прочности материала болта (шпильки), МПа.
Сборка сопряжений с зазором или натягом. При сборке подвижных (сопряжения с зазором) и неподвижных соединений (сопряжения с натягом или прессовые) точности сборки (величины зазоров и натягов) достигают предварительным измерением сопрягаемых деталей и, при необходимости, подгонкой их друг к другу различными слесарными способами или на металлорежущих станках. Например, направляющую втулку стержня клапана развертывают под стержень клапана и т. п.
В некоторых механизмах, узлах величину зазора или натяга обеспечивают регулировочными компенсаторами (винтами, гайками, прокладками, кольцами и т. п.). Так, зазор (размер замыкающего звена размерной цепи «кулачок—толкатель—штанга— коромысло—торец стержня клапана») между торцом стержня клапана и бойком коромысла устанавливают регулировочным винтам, а натяг в сопряжении «рычаг-конус шарового пальца рулевого управления» — гайкой.
В подавляющем большинстве сопряжений нормальные посадки обеспечиваются без подгонки и регулировки, за счет групповой (селективной), частичной или полной взаимозаменяемости. Например, по методу селективной сборки собирают сопряжения «поршневой палец-отверстия бобышек поршня» (детали рассортированы на размерные группы).
Частичная взаимозаменяемость может быть в сопрягаемых деталях, изготовленных по стандартным ремонтным размерам (шейки коленчатого вала — вкладыши; гильза — поршень и т. п.).
Полная взаимозаменяемость обеспечивает нормальные посадки деталей в сопряжении (зацеплении, соединении) не зависимо от партии деталей. По методу полной взаимозаменяемости собирают сопряжения «вал—подшипник качения»; посадочное место корпусной детали—подшипник качения; зубчатые, цепные и ременные передачи; резьбовые, шлицевые и шпоночные соединения, самоподжимные сальниковые уплотнения и т. п.
Перед сборкой тщательно осматривают сопрягаемые поверхности, при наличии заусенец, забоин, коррозии их удаляют, острые кромки притупляют. Затем очищенные поверхности смазывают машинным (моторным) маслом (в неподвижных сопряжениях эту операцию выполняют, если обе сопрягаемые детали стальные). Шероховатость поверхностей в неподвижных сопряжениях должна быть не болеее Ra= 2,5...1,25 мкм, в противном случае произойдет смятие неровностей и уменьшится натяг. Усилие запрессовки Р3:
Рз =0,02 N b
где N — Величина натяга (принимается по техническим требованиям на сборку данной машины или сборочной единицы), мм; b — ширина (длина) посадочного места (принимают по чертежу), мм.
При сборке сопряжений с большими натягами охватывающую деталь нагревают, а охватываемую — охлаждают.
Температуру нагрева или охлаждения в °С:
Т = (1,2…1,3) N / α d,
где α — коэффициент линейного расширения металла нагреваемой (охлаждаемой) детали; d — Номинальный диаметр сопрягаемых деталей, мм.
Температура нагрева детали не должна превышать 500 °С, в противном случае деталь потеряет первоначальную прочность.
Нагревают деталь (перед запрессовкой) в масле, в расплавленном свинце или открытым способом, а охлаждают сжиженными газами, воздухом, азотом или сухим льдом (твердой двуокисью углерода).
Чтобы избежать перекосов при запрессовке, применяют различные оправки и наставки, равномерно распределяющие усилия по сопрягаемым поверхностям.
Сборка узлов с подшипниками качения. Подшипники промыть в 8... 10%-ном растворе машинного масла в бензине.
Посадочные места вала и корпуса протереть чистой ветошью и смазать машинным маслом.
Использовать пресс или винтовые приспособления, подкладные кольца, монтажные трубки, оправки (см. рис. 5).
![]() |
Рис. 5. Схема монтажа подшипников качения с применением: А- подкладочного кольца; Б – монтажной трубки; В – втулки; Г – специальной оправки; Д – гайки конусной разрезной: 1 – втулка; 2 – корпус; 3 - подшипник; 4 – гайка; 5 – вал; Е – монтажного валика: 1 – корпус; 2 – деталь; 3 – валик; 4 – ось; 5 – иголки (ролики); 6 – шайба.
При напрессовке подшипника на вал:
- рекомендуется нагреть в машинном масле до температуры 80... 100°С, - установить на центрирующую фаску и запрессовать до упора в буртик или заплечик, - усилие прикладывать к внутреннему кольцу (рис. 5, б).