Файл: Проектный и проверочный расчет цилиндрического одноступенчатого прямозубого редуктора.docx
Добавлен: 11.01.2024
Просмотров: 194
Скачиваний: 2
ВНИМАНИЕ! Если данный файл нарушает Ваши авторские права, то обязательно сообщите нам.
СОДЕРЖАНИЕ
Определение параметров передачи
3.2 Предварительные основные размеры колеса
3.4. Определяем число зубьев передачи
3.5 Фактическое передаточное число
3.6 Фактические основные геометрические размеры передачи
3.7 Пригодность заготовок шестерни и колеса
Окружная скорость зубчатых колёс
Проверка зубьев колеса по контактным напряжениям
Проверка зубьев колеса по контактным напряжениям
Контактная прочность зубьев является основным критерием работоспособности большинства зубчатых передач. При этом рассматривают соприкасание зубьев в полюсе, где происходит однопарное зацепление и возникает выкрашивание. При работе зубчатых передач в результате неточностей изготовления и сборки, деформации зубьев возникают дополнительные динамические нагрузки, влияние которых при расчёте на контактную прочность учитывается коэффициентом

Для прямозубой передачи при

-

-

Наибольшее контактное напряжение в зоне зацепления равно:

Влияние неравномерного распределения нагрузки по длине зуба при расчёте на контактную прочность зубьев учитывается коэффициентом



344,1<355 – контактная прочность зубьев обеспечивается.
Проверим нагруженность зубчатой передачи, учитывая расчетные данные через составленную пропорцию:
355 МПа – 100 %
344,1 МПа – х %
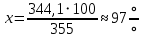
100 % –97%=3%
Недогрузка составляет 3%, контактная прочность зубьев обеспечивается.
-
Проверка зубьев колёс по напряжениям изгиба
Одним из основных критериев работоспособности зубчатых передач является прочность зубьев на изгиб. При этом зуб рассматривают, как консольную балку, нагруженную сосредоточенной силой Fn, приложенной к зубу в его вершине. Силой трения в зацеплении пренебрегают.
Определим коэффициент формы зуба в зависимости от числа зубьев.
Коэффициент формы зуба YF
Таблица 7
z | 17 | 20 | 22 | 24 | 26 | 30 | 35 | 40 | 50 | 80 | 100 | 180 |
YF | 4,27 | 4,07 | 3,98 | 3,92 | 3,88 | 3,8 | 3,75 | 3,7 | 3,65 | 3,6 | 3,62 | 3,63 |
Z1=30, что совпадает с табличным значением

Количество зубьев колеса Z2=90

Вся нагрузка зацепления передается одной парой зубьев, которая приложена к вершине зуба и направлена по нормали к его профилю. Фактически зуб представляет собой балку с изменяющейся формой. Это учитывается введением в расчетные формулы теоретических коэффициентов концентрации напряжений, неравномерности распределения нагрузки по ширине зубчатого венца и дополнительной динамической нагрузки в зацеплении. Наибольшее напряжение изгиба равно:

где



Для прямозубых передач при

-

-

Тогда напряжения изгиба для колеса равны:


59,02<164,8МПа, что значительно ниже допускаемых напряжений.
Для шестерни:


62,126<195,7МПа, что значительно ниже допускаемых напряжений.
Прочность зубьев на изгиб обеспечивается.
Произведем окончательную проверку прочности зубьев шестерни и колеса. Для этого необходимо сравнить значения

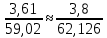

- 355>1 2 3 4 5 6 7 8 9 10 11
Ориентировочный расчёт валов
Зубчатые колёса, шкивы, звёздочки и другие вращающиеся детали машин устанавливают на валах или осях. Вал предназначен для поддержания сидящих на нём деталей и для передачи вращающего момента. При работе вал испытывает изгиб и кручение, а в отдельных случаях дополнительно растяжение и сжатие. Основными критериями работоспособности валов являются сопротивление усталости и жёсткость. Основными расчётными силовыми факторами являются крутящие Мк и изгибающие М моменты. Влияние растягивающих и сжимающих сил невелико и в большинстве случаев не учитывается.
Проектировочный расчёт валов производят на статическую прочность для ориентировочного определения диаметров. В начале расчёта известен только крутящий момент Мк.. Изгибающие моменты М оказывается возможным определить лишь после разработки конструкции вала, когда согласно чертежу, выявится его длина.
Конструктивные размеры зубчатой пары, диаметр внутреннего кольца и ширина подшипниказависят от диаметра вала. Обычно вначале определяют диаметр выходного конца вала, а затем по конструктивным соображениям назначают диаметры посадочных мест для зубчатых колёс и подшипников. Для последующего выполнения уточнённого расчёта вала надо будет установить расстояние между точками приложения сил, определить реакции подшипников, построить эпюры изгибающих моментов.
Известны активные силы, действующие на валы со стороны зубчатого зацепления. Диаметр выходного конца вала определяют приближённо из расчёта на прочность при кручении по пониженным допускаемым касательным напряжениям

Принимаем:


Примечание: в своей работе выбираете марки сталей, для изготовления валов, исходя из задания (они совпадают с материалами зубчатых колес)
8.1 Расчёт ведущего вала
Диаметр расчётного сечения вала определяем по формуле, известной из курса сопротивления материалов:

где Wp – полярный момент сопротивления сечения вала, мм3. Для вала сплошного круглого сечения

Из расчетов вращающий момент, передаваемый через шестерню на вал (см. п№3.1) равен М1=Мк1=129,75Нм=129750Нмм.
Решая проектную задачу сопромата определим требуемый диаметр вала:

При расчёте деталей машин полученные расчётом линейные размеры (диаметры, длины, высоты) необходимо округлять до предпочтительных.
Стандартные линейные размеры (ГОСТ 6636-69)
Таблица 8
Наименование ряда | Примеры нормальных линейных размеров, мм |
Ra 40 | 10;10,5;11;11,5;12;13;14;15;16;17;18;19;20;21;22;24;25;26;28;30;32;34;36;38;40;42;45;48;50;52;55;60;63;65;70;75;80;85;90;95;100;105;110;120;125;130;140;150;160; 170;180;190;200;…;500 |
Принимаем

Приступаем к определению ориентировочных диаметров ступеней вала.
Назначаем посадочные размеры под уплотнения и подшипники:
- принимаем диаметр вала под манжетное уплотнение


- диаметр вала под подшипник качения принимают с учетом размещения подшипников заданной долговечности в соответствии со стандартными диаметрами внутренних колец, которые оканчиваются на числа 0 и 5 (т.е. кратны 5). Принимаем
