Файл: Отчет по Производственная практика по получению первичных профессиональных умений и навыков.docx
Добавлен: 25.10.2023
Просмотров: 374
Скачиваний: 7
ВНИМАНИЕ! Если данный файл нарушает Ваши авторские права, то обязательно сообщите нам.
СОДЕРЖАНИЕ
ОАО "Стойленский горно-обогатительный комбинат". Производственная характеристика предприятия
.1 Существующая структура и технология производства
1.1.4 Цех хвостового хозяйства
1.1.5 Цех железнодорожного транспорта
1.1.7 Цех сетей подстанций и автоматизации
1.1.9 Ремонтно-механический завод
1.1.10 Ремонтно-строительный цех
.1.11 Цех подготовки производства и складского хозяйства
1.2 Перспектива развития предприятия
.2.1 Фабрика окомкования концентрата
1. ОАО "Стойленский горно-обогатительный комбинат". Производственная характеристика предприятия
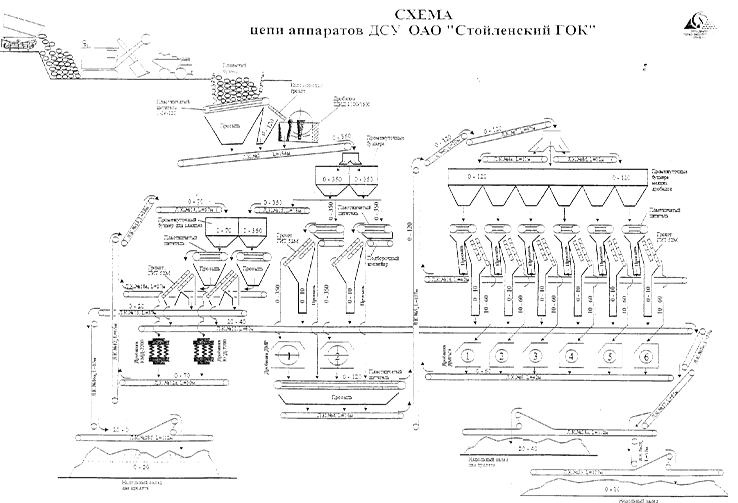
Участок дробления осуществляет работы по дроблению железистых кварцитов и транспортировку класса 15-0 мм на участок обогащения. Участок состоит из следующих подразделений:
Корпус крупного дробления (ККД);
Корпус среднего и мелкого дробления (КСМД).
Корпус крупного дробления
Кварцитовая руда крупностью 0-1200 мм и влажностью до 3% подается из карьера на ККД железнодорожным транспортом, где происходит ее выгрузка на 4-постах и дробление в 2-х конусных дробилках до крупности 350 - 0 мм. После чего, дробленая руда по 2-м системам ленточных конвейеров КЛ-1 и КЛ-2 подается на транспортерные ленты 1ПС-1 и 1ПС-2 и далее в Корпус среднего и мелкого дробления.
Узлы выгрузки и пересыпки руды оборудованы местными отсосами с очисткой ГВС от пыли в 2-х скоростных промывателях СИОТ (мокрая очистка газа).
Все просыпи руды с конвейеров, гидросмывом собираются в зумпфы, из которых с помощью грейфера подается на конвейеры, для их повторной переработки, а мелкие частицы (шлам) дренажными насосами сбрасываются в хвостохранилище.
Схема цепи аппаратов, корпуса крупного дробления
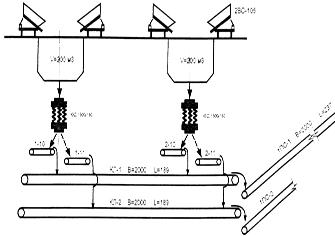
Корпус среднего и мелкого дробления (КСМД)
В корпусе производится дробление руды крупностью 0-350 мм до фракции 0-15 мм и последующая подача на участок обогащения.
Технологический процесс состоит из операций дробления руды на дробилках (2 стадии), с последующим просеиванием (грохочение). Линия мелкого дробления закольцована для повторного дробления до необходимой фракции.
Руда после крупного дробления (350-0 мм, влажностью 3%) ленточными конвейерами 1ПС-1; 1ПС-2 поступает на передвижные реверсивные ленточные конвейеры СМ-3; СМ-4 при помощи которых распределяется по бункерам (4 ед.) среднего дробления емкостью 4 000 тонн.
Разгрузка бункеров производится электровибрационными питателями ПЭР 28*15 и ленточными питателями на конвейеры СМ-7, СМ-8, СМ-9, пластинчатыми питателями 2-15-30 на конвейеры СМ-10 и СМ-10А. Конвейерами руда транспортируется в конусные дробилки среднего дробления (5 ед.), производительностью 800 - 1200 т/час. Дробленый продукт крупностью 80-0 мм подвергается грохочению на грохотах ГИСТ-72 (2 ед.) и LF3060D (3 ед.).
Подрешетный продукт (готовая фракция 0-15 мм) по конвейеру СМ20 (СМ-20А, СМ-20Б), 2ПС-1 и 2ПС-2 поступает на передвижные ленточные конвейеры ОБ-1, ОБ-2, с помощью автостелл распределяются по параболическому бункеру корпуса обогащения.
Надрешетный продукт (фракция более 15 мм) конвейерами СМ-19 (СМ-19А, СМ-19Б), ЗПС-1 и ЗПС-2, 2ПУ1 и 2ПУ-2, СМ-1 и СМ-2, передвижными реверсивными конвейерами СМ-5 и СМ-6 распределяются по бункерам (8 ед.) мелкого дробления емкостью 8 000 тонн.
Руда из бункеров через реечные затворы поступает на ленточные конвейеры СМ-11 - СМ-18 и далее в дробилки мелкого дробления (10 ед.), производительностью до 1000 т/час, где производится дробление до фракции 0-30 мм.
Дробленый продукт крупностью 0-30 мм подвергается грохочению на грохотах ГИСТ-72 (1 ед.) и LF3060D (9 ед.). Подрешетный продукт (готовая фракция 0-15 мм) по конвейеру СМ20 (СМ-20А, СМ-20Б), 2ПС-1 и 2ПС-2 поступает на передвижные ленточные конвейеры ОБ-1, ОБ-2 и распределяется по параболическому бункеру корпуса обогащения. Надрешетный продукт (фракция более 15 мм) по конвейерам трактов возврата СМ-19 (СМ-19А, СМ-19Б), ЗПС-1 и ЗПС-2, 2ПУ1 и 2ПУ-2, СМ-1 и СМ-2, повторно поступает на дробилки мелкого дробления.
Узлы пересыпки (перегрузки) руды оборудованы местными отсосами с очисткой ГВС от пыли в установках мокрой очистки. Все просыпи руды с конвейеров, гидросмывом собираются в зумпфы, из которых с помощью грейфера подается на конвейеры, для их повторной переработки, а мелкие частицы (шлам) дренажными насосами сбрасываются в хвостохранилище.
На участке производится измельчение и обогащение дробленой руды с получением железорудного концентрата с содержанием железа 66,4%, крупностью до 1 мм, который отгружается в ж/д транспорт. Побочным продуктом обогащения является щебень.
Основной принцип обогащения основан на различии в магнитных свойствах железосодержащих минералов и вмещающих пород.
На участке используется сухая и мокрая магнитная сепарация.
Отходами производства являются хвосты: суспензия (пульпа), содержащая 4-5% твердого. Твердая составляющая используется в технологии складирования отходов для намывки и складирования. Осветленная вода, является оборотной и используется в технологии обогащения.
Технология обогащения состоит из следующих основных этапов:
мокрая магнитная сепарация:
3 стадии мокрого измельчения;
гидравлическую классификацию в классификаторах и гидроциклонах;
5 стадий магнитной сепарации;
2 стадии обесшламливания;
уплотняющую магнитную сепарацию;
усреднение;
Обезвоживание на вакуум-фильтрах с получением конечного продукта- концентрата.
сухая магнитная сепарация:
просеивание;
магнитное сепарирование;
В состав участка входят следующие отделения:
- 4 технологические секции;
- ремонтные площадки;
слесарные мастерские;
механическая мастерская;
Технологическая схема секций № 1-3
Технологическая схема мокрого обогащения на технологических секциях № 1-3 абсолютно аналогична и технология производства приведена для 1 секции.
Дробленая руда крупностью 15-0 мм из параболического бункера через телескопические течки разгружается на конвейеры ОБ-3 - ОБ-11.
Дробленая руда из бункеров конвейерами транспортируется в мельницы МШЦУ 5565 (2 ед.), работающие в замкнутом цикле с двухспиральными классификаторами 2КСН 3,017,2. Слив спиральных классификаторов самотеком поступает на магнитные сепараторы (5 ед.) 1-й стадии обогащения, которое осуществляется в сепараторах ПБМ 120300 и ПБМ 150200 с противоточной ванной. Хвосты сепараторов поступают в хвостовой лоток, а магнитный продукт (промпродукт) поступает в зумпф №2, откуда насосами ГРТ 1250/71 подается на классификацию в гидроциклоны ГЦ-650 (16 ед.). Пески гидроциклонов поступают во вторую стадию измельчения в мельницы МШЦ 5565, а слив на 1-ю стадию обесшламливания в дешламаторе МД-12.
Измельченный продукт 2-й стадии самотеком поступает на 3-ю стадию обогащения в сепараторы ПБМ 120300 (ПБМ 150х200) с полупротивоточной ванной. Промпродукт 3-й стадии обогащения объединяется с концентратом 1-й стадии ММС в зумпфе №2 и возвращается в цикл второй стадии измельчения, а хвосты самотеком направляются в хвостовой лоток.
Сгущенный продукт после первой стадии обесшламливания насосами ГРК 1600/56 (зумпф №5) подается на четвертую стадию обогащения в барабанные сепараторы ПБМ-ПП 120300 и ПБМ-ПП 150200.
Промпродукт 4-й стадии обогащения поступает в зумпф №3, откуда насосами ГРТ 1250/71 подается на классификацию в гидроциклоны ГЦ-650. Пески гидроциклонов поступают на 3-ю стадию измельчения в мельницы МШЦ 5565, а слив на вторую стадию обесшламливания в дешламаторы МД-12.
Продукт измельчения 3-й стадии самотеком поступает на 2-ю стадию мокрой магнитной сепарации и после обогащения возвращается в зумпф №3, образуя замкнутый цикл, откуда насосами ГРТ 1250/71 подается на классификацию в гидроциклоны ГЦ-650.
Сгущенный продукт 2-й стадии обесшламливания насосами подается на 5-ю стадию ММС в сепараторы ПБМ-ПП-120300, ПБМ-ПП-150/200, концентрат которых является конечным продуктом схемы обогащения. Хвосты 5-й стадии самотеком транспортируются в хвостовой лоток.
Технологическая схема секции № 4
Дробленая руда крупностью 15-0 мм из бункера системой конвейеров ОБ-12, ОБ-13, ОБ-14, ОБ-25, ОБ-26 поступает в мельницы 1-й стадии обогащения. Мельницы МШЦУ 55х65А 1-й стадии измельчения, работают в замкнутом цикле с двухспиральным классификатором 2КСН 3,0х17,2. Слив классификатора поступает на 1 стадию ММС в магнитные сепараторы ПБМ-П-150/200 с противоточной ванной. Концентрат 1-й стадии обогащения самотеком поступает в зумпфы № 1, и №4 откуда насосами подается на вторую стадию классификации в гидроциклоны ГЦ 650 (с углом конусности 12о), а хвосты самотеком направляются в сборный хвостовой лоток.
Пески гидроциклонов поступают в мельницы 2-й стадии измельчения МШЦ 55х65. Измельченный продукт 2-й стадии измельчения поступает самотеком на 2-ю стадию обогащения в сепараторы ПБМ-П-150/200 с противоточной ванной. Концентрат 2-й стадии обогащения самотеком поступает в зумпфы №2 и № 15, затем насосами подается на 3-ю стадию классификации в ГЦ-650, объединенные в батареи из 5-и гидроциклонов. Пески гидроциклонов возвращаются в цикл 2-й стадии измельчения. Слив гидроциклонов 2-й и 3-й стадии классификации в ГЦ-650 самотеком направляется в дешламаторы МД-12 для обесшламливания и сгущения.
Сгущенный продукт обесшламливания (пески) поступает в зумпфы № 5 и № 6, откуда насосами ГРК 900/67 подается на 3-ю стадию обогащения в двухбарабанные сепараторы ПБМ-ПП-150/200 с полупротивоточной ванной. Слив дешламаторов самотеком направляется в сборный хвостовой лоток.
Концентрат 3-й стадии обогащения поступает в зумпф №7 и насосами направляется на грохоты тонкого грохочения STАСK SIZER. Подрешетный продукт грохотов поступает в зумпф № 12, откуда насосами подается на 4-ю стадию ММС в сепараторы ПБМ-П-150/200, магнитный продукт которых поступает в зумпф № 10. Немагнитный продукт самотеком направляется в зумпф № 9.
Надрешетный продукт грохотов поступает в зумпф № 11, откуда насосами подается на сепараторы ПБМ-П-150/200 пятой стадии, исполняющие роль уплотняющих агрегатов, магнитный продукт которых поступают в 3-ю стадию измельчения в мельницу МШЦ 55х65, хвосты в сборный хвостовой лоток. Измельченный продукт 3-й стадии измельчения самотеком поступает в зумпф №9, откуда насосами подаются в гидроциклоны ГЦ-650, работающие в замкнутом цикле с мельницей 3-й стадии. производственный шахта рудоуправление фабрика
Слив гидроциклонов поступает на 2-ю стадию обесшламливания в дешламатор МД-12, сгущенный продукт которого поступает в зумпф № 8 и насосами транспортируется на 6-ю стадию ММС в сепараторы ПБМ-П-150/200. Магнитный продукт 6-й стадии ММС самотеком поступает в зумпф № 10, где объединяется с магнитным продуктом 4-й стадии ММС. Объединенный продукт является конечным концентратом т.с. №4.
Технологическая схема обезвоживания, складирования и отгрузки концентрата
Концентрат секций № 1-4 насосами транспортируется на уплотнение в сепараторы ПБМ-ПП-120300, ПБМ-ПП-150/200, хвосты которых поступают в хвостовой лоток технологических секций №1 и №2. Сгущенный концентрат после уплотнения поступает в перемешиватели МП-15 для усреднения и насосами подается в пульподелители вакуум-фильтров ДШ-100-2,5. Перелив вакуум-фильтров возвращается на уплотняющую сепарацию, фильтрат возвращается в технологический процесс в зумпфы технологической секции №1 и №2.
Товарный концентрат после обезвоживания поступает на склад концентрата или на погрузку в ж/д транспорт.
Транспортировка концентрата на отгрузку осуществляется по двум трактам: системой конвейеров непосредственно на загрузку в вагоны и системой конвейеров со склада концентрата.