Файл: Курсовой проект по мдк. 01. 02 Организация ремонтных работ промышленного оборудования и контроль за ними.doc
ВУЗ: Не указан
Категория: Не указан
Дисциплина: Не указана
Добавлен: 25.10.2023
Просмотров: 430
Скачиваний: 17
СОДЕРЖАНИЕ
1.3 Конструкция ремонтируемого механизма
1.4 Расшифровка химического состава и механических свойств материала ремонтируемой детали.
- коэффициент формы зуба, определяемый по приведенному числу зубьев шестерни:
- коэффициент перекрытия в торцовом свечении. Определяется по формуле:
- соответственно, числа зубьев шестерни и колеса;
“+”- для наружного зацепления;
“-”-.для внутреннего зацепления;
Определение цикла ремонтов и технических обслуживаний (Ц)
Определяем ЦКР - цикличность капитальных ремонтов.
ТКР – периодичность капитальных ремонтов оборудования
НГ – максимальная наработка оборудования в год, ч.
Определяем ЦТР - цикличность текущих ремонтов.
ТТР - периодичность текущего ремонта, ч.
НМ - максимальная наработка в месяц
Определяем ЦТО - цикличности технических обслуживаний.
ТТО - периодичность технического обслуживания, ч;
НМ - максимальная наработка в месяц;
Определение числа ремонтов и технических обслуживаний
Определяем число капитальных ремонтов (НКР).
Определяем число текущих ремонтов (НТР).
Определяем число технических обслуживаний (НТО).
НТО = ТКР / ТТО - НКР - НТР (6)
НТО = 34560 / 4320 - 1 - 3 = 4
2.3 Графическое изображение полей допуска сопрягаемых изношенных деталей.
3. Монтаж, техническое обслуживание и ремонт станка
2. Расчетный раздел
1. Кинематический расчет привода
Определяем диапазон регулирования привода главного движения по формуле:
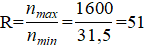
Определяем диапазон регулирования шпинделя при постоянной мощности по формуле:
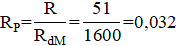
=1*1,15*1,3=1,5
=1*1,1*1,2=1,32
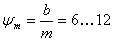




=1,9*108*1,2*1=2,28*108Па,
=9,5*108*1,4=13,3*108Па,
где



=1,9*108*1,2*1=2,28*108Па,
=9,5*108*1,4=13,3*108Па,
где 
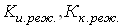
- коэффициент формы зуба, определяемый по приведенному числу зубьев шестерни:
=58
- угол наклона зубьев;
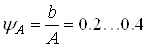






=0,93
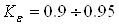

- коэффициент перекрытия в торцовом свечении. Определяется по формуле:
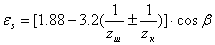
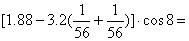
- соответственно, числа зубьев шестерни и колеса;
“+”- для наружного зацепления;
“-”-.для внутреннего зацепления;

Для обеспечения бесступенчатого регулирования частоты вращения шпинделя при постоянной мощности знаменатель ряда передаточных отношений передач коробки скоростей φ1 принимаю равным RдР. Требуемое число ступеней коробки скоростей:
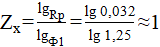
Определяют нормальный модуль


и округляют его до стандартного значения


и сравнивают его с подсчитанным по формуле:
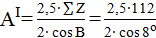
≈142 мм.
где

2. Расчет ремонтного цикла
Периодичность ремонта (Т):
ТТО = 4320 ч.
ТТР = 8640 ч.
ТКР = 34560 ч.
Продолжительность простоя (П)
ПТО = 4 ч.
ПТР = 48 ч.
ПКР = 96 ч.
Трудоемкость
ТО- 8 чел.-ч.
ТР- 8 чел.-ч.
КР- 48 чел.-ч.
Периодичность ремонтов (Т):
ТТО=1440 ч.
ТТР = 8640 ч.
ТКР = 43200 ч.
Продолжительность простоя (П)
ПТО = 3 ч.
ПТР = 35 ч.
ПКР = 229 ч.
Трудоемкость
ТО-6 чел.-ч.
ТР-24 чел.-ч.
КР-210 чел.-ч.
Определение цикла ремонтов и технических обслуживаний (Ц)
Определяем ЦКР - цикличность капитальных ремонтов.
Ц = ЦКР= ТКР / НГ, где (1)
ТКР – периодичность капитальных ремонтов оборудования
НГ – максимальная наработка оборудования в год, ч.
Ц = ЦКР= 34560 /
Определяем ЦТР - цикличность текущих ремонтов.
ЦТР = ТТР/ Нм, где (2)
ТТР - периодичность текущего ремонта, ч.
НМ - максимальная наработка в месяц
ЦТР = 8640 /
Определяем ЦТО - цикличности технических обслуживаний.
ЦТО = ТТО/ Нм, где (3)
ТТО - периодичность технического обслуживания, ч;
НМ - максимальная наработка в месяц;
ЦТО = 4320/
Определение числа ремонтов и технических обслуживаний
Определяем число капитальных ремонтов (НКР).
НКР = ТКР / ТКР (4)
НКР = 34560 / 34560 = 1
Определяем число текущих ремонтов (НТР).
НТР = ТКР / ТТР - НКР (5)
НТР = 34560 / 8640 - 1 = 3
Определяем число технических обслуживаний (НТО).
НТО = ТКР / ТТО - НКР - НТР (6)
НТО = 34560 / 4320 - 1 - 3 = 4
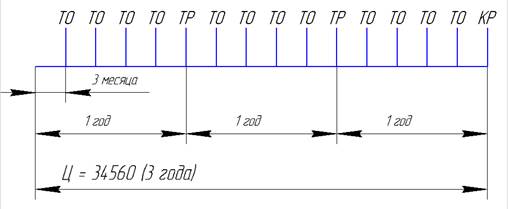
2.3 Графическое изображение полей допуска сопрягаемых изношенных деталей.
Износ на участке I кривой ОА1 характеризуется быстрым нарастанием износа ОК за сравнительно малый период работы ОА. Он выражает начальную работу сопряжения — период приработки деталей. Износ и степень интенсивности изнашивания в этот период во многом зависят от качества поверхности деталей, условий смазки и нагрузки. С увеличением шероховатости рабочей поверхности, а также с увеличением нагрузки в начальный период работы износ деталей значительно повышается. Участок II кривой А1В1, наибольший по протяженности, характеризует нормальную работу детали или сопряжения. За время нормальной эксплуатации АВ износ деталей нарастает постепенно, часто с небольшой равномерной интенсивностью, и увеличивается на небольшое значение КК1. Износ на этом участке носит название естественного износа.
Его значение во многом зависит от условий эксплуатации, а также от своевременности и качества проводимого технического обслуживания. Участок Ш за точкой B1 характеризуется интенсивным нарастанием износа деталей и резким увеличением зазоров в сопряжениях.
Работа сопряжений с износами деталей, превышающими значение ОК1, как правило, сопровождается нарушением условий смазки, перегревом деталей, появлением шумов и стуков и часто заканчивается аварийным разрушением.
Такие износы называют предельными. Детали с предельными износами требуется восстановить или заменить.
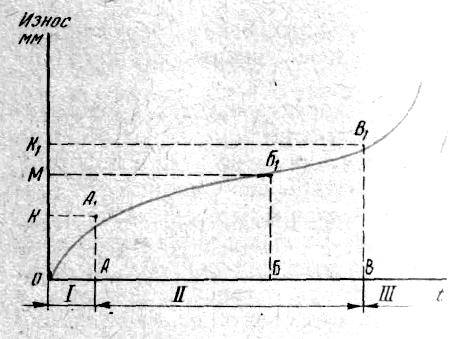