Добавлен: 08.11.2023
Просмотров: 281
Скачиваний: 4
ВНИМАНИЕ! Если данный файл нарушает Ваши авторские права, то обязательно сообщите нам.
Замок
Какие проблемы возникают с замком:
-
недостаточная толщина; -
изгиб сигнального отростка; -
излом направляющего выступа или предохранительного шипа; -
износ задней кромки овального отверстия.
Сюда же можно отнести проблемы с предохранителями и замкодержателями. Рекомендуется регулярно проверять работоспособность всего устройства.
Поможет ли ремонт автосцепного устройства?
Регулярный осмотр и своевременный ремонт автосцепного устройства вагонов помогают поддерживать высокий уровень безопасности на железной дороге. Можно менять отдельные детали или весь узел в сборке, если это необходимо. Обратите внимание: для запчастей, устройств и самих работ предусмотрены соответствующие ГОСТ.
В процессе эксплуатации в узлах автосцепного устройства вагонов возникают износы и различные повреждения отдельных деталей. Все дефекты должны быть своевременно выявлены и устранены, так как в пути следования любой из них может быть причиной саморасцепа автосцепок, обрыва поезда, падения деталей на путь.
Трещины в корпусе автосцепки в указанных на рис. 8.19 местах не допускаются. Признаками трещин могут быть заусенцы, ржавчина, разрыв слоя краски, валик пыли или льда.
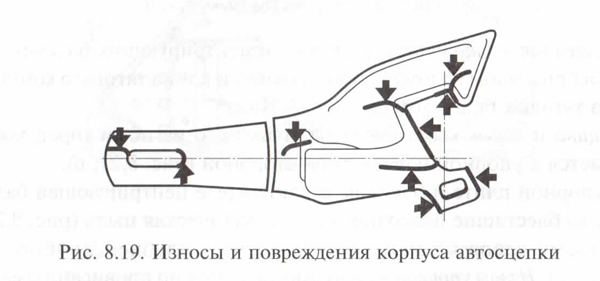
Провисание автосцепки более 10 мм происходит вследствие излома клина тягового хомута, разрыва соединительных планок или верхней тяговой полосы хомута (рис. 8.20, а, б).
Расстояние А (рис. 8.20, в) от упора головы автосцепки до ударной розетки (длина выступающей части 185 мм), составляющее более 90 мм или менее 60 мм, а для укороченных ударных розеток с длиной выступающей части 130 мм — более 150 мм или менее 110 мм, позволяет выявить изломы клина тягового хомута, упорной плиты.
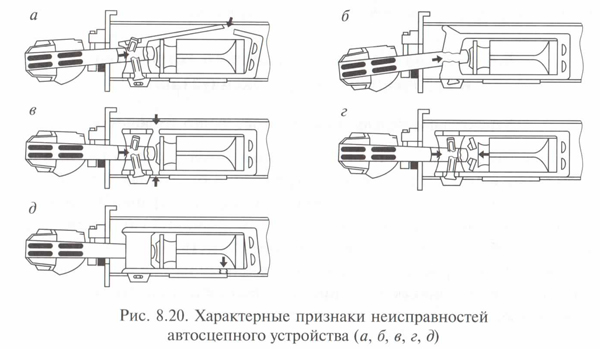
Разрывы тяговых полос хомута, потерю упругих свойств поглощающих аппаратов иллюстрирует рис. 8.20, в, г.
Наличие зазора между днищем корпуса поглощающего аппарата и тяговым хомутом указывает на разрыв нижней (рис. 8.20, д) и верхней тяговой полосы.
Сброшенные маятниковые подвески с центрирующих балочек могут являться признаком излома упорной плиты и клина тягового хомута или разрыва тяговых полос хомута (рис. 8.21, а).
Трещина и обрыв хвостовика вызывают его изгиб, и торец корпуса прикасается к упорной плите одной стороной (рис. 8.21, б).
На упорной плите и боковом ограничителе центрирующей балочки возможны блестящие поверхности и металлическая пыль (рис. 8.21, в).
Во время удара по изломанному клину слышен двойной звук (рис. 8.21, г). Излом упорной плиты определяется по провисанию ее нижних концов относительно нижней тяговой полосы (рис. 8.21, д). Наличие клинового зазора между упорами и упорной плитой указывает на ее излом (рис. 8.21, е).
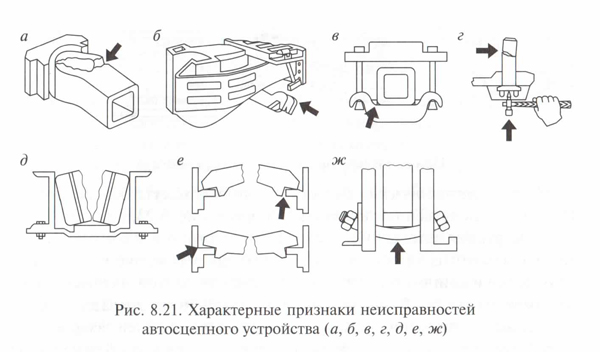
Изгиб болтов, поддерживающих клин тягового хомута, позволяет обнаружить разрыв верхней (изгиб переднего болта) или нижней (изгиб заднего болта) тяговой полосы (рис. 8.21, ж).
Ослабление крепления и изгиб поддерживающей планки — признак разрыва верхней полосы хомута (рис. 8.22, позиция 1). Зазор между поддерживающей планкой и полкой швеллера — обрыв нижней тяговой полосы или разрушение поглощающего аппарата (рис. 8.22, позиция 2).
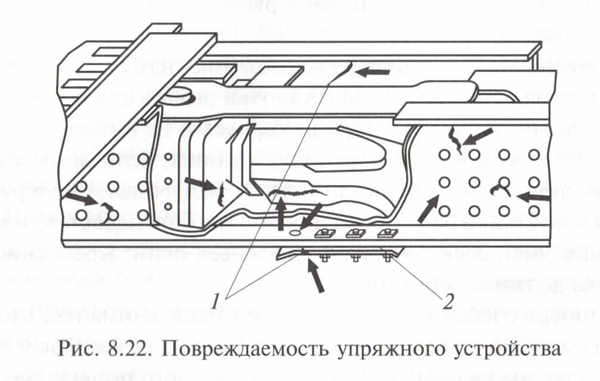
Наличие полосы с металлическим блеском на тяговом хомуте или на хвостовике автосцепки около центрирующей балочки размером более 150 мм является признаком неисправного поглощающего аппарата ( на рис. 8.23 показано позицией 1).
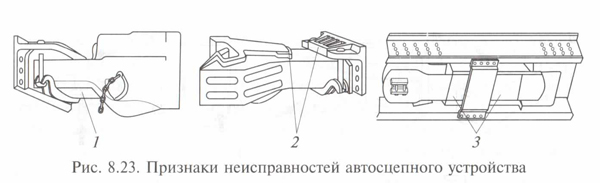
Следы ударов на упоре головы автосцепки и розетке — поглощающий аппарат потерял упругие свойства (рис. 8.23, позиция 2).
Полоса с металлическим блеском на тяговом хомуте больше нормы 150 мм — неисправен поглощающий аппарат (рис. 8.23, позиция 3).
Конструкция автосцепного устройства такова, что в контуре зацепления сцепленных автосцепок, а также между перемычкой хвостовика автосцепки и клином тягового хомута, упорной плитой, тяговым хомутом имеются зазоры. В новом автосцепном устройстве эти зазоры в сумме составляют примерно 40 мм, а по мере износа деталей зазор в автосцепном устройстве может достигать 100 мм, что вызовет резкие удары между вагонами при их перемещении.
Цепь расцепного привода должна иметь незначительное провисание. Для регулирования цепи автосцепку устанавливают так. Чтобы расстояние корпуса до розетки было (75 + 5) мм, а у восьмиосных вагонов — (120 ± 5) мм. Затем расцепной рычаг ставят на полочку кронштейна (проверка на буфер).
При невозможности установить в положение «на буфер» гайку и контргайку отвинчивают до свободной установки рычага в положение «на буфер». Если замок утопится в карман корпуса и не выйдет за плоскость ударной стенки зева — цепь нормальной длины. Если замок выступает за ударную стенку зева — цепь длинная, ее укорачивают подкручиванием гайки и контргайки регулировочного болта. При недостаточной длине резьбы болта уменьшают количество звеньев цепи. Крепление валика подъемника должно быть типовым.
При осмотре расцепного привода обращают внимание, чтобы державка и кронштейн не имели трещин, изломов или изгибов и были надежно закреплены на вагоне. Рукоятка расцепного рычага должна быть в вертикальном положении, рычаг должен входить в паз кронштейна. При сцепе вагонов с общим грузом рычаги должны быть прикручены к кронштейнам проволокой. У вагонов скоростного поезда ставят предохранитель, который для расцепления вагонов надо повернуть на 180°,
предварительно ослабив гайку его крепления. Излом и трещины не допускаются.
2. Ремонт корпуса автосцепки и деталей механизма.
Автосценные устройства при работе испытывают значительные динамические нагрузки, действующие в различных плоскостях, большие перепады температур. Кроме того, на их работу отрицательно влияет незащищенность сопряженных деталей от попадания з зоны трения абразивных частиц.
Сложное конструктивное исполнение деталей и их геометрических форм требует повышения уровня технологии изготовления, ремонта, системы контроля и испытаний.
Значительные продольные и поперечные нагрузки на автосцепку появляются при входе состава в кривые участки пути или выходе из них, при переломах профиля железнодорожного полотна. на сортировочных станциях и горках, при трогании с места и торможениях.
Перегрузки в материале деталей автосцепки также возникают от несинхронности колебаний сочлененных вагонов. При этом особенно сильно и часто этот эффект возрастает, когда неисправны гасители колебаний как гидравлического, так и фрикционного типа. Тогда все основные детали не только перегружаются, но и интенсивно изнашиваются. Возможны даже саморасцепы вагонов, появление деформаций в отдельных деталях устройства, отколов, трещин и других повреждений, включая разрушения.
Возникновение знакопеременных нагрузок приводит к развитию трещин, изломам. В отдельных случаях встречаются хрупкие разрушения, что определяется как неблагоприятным сочетанием действующих сил, климатических и других факторов, так и внутренними отклонениями и пороками кристаллической структуры.
Сложный профиль многих деталей также является естественным источником концентрации внутренних напряжений, особенно в переходных поверхностях.
Основной причиной ремонта и замены деталей при плановых и текущих ремонтах является износ.
В отдельных случаях, например при появлении местных, односторонних износов деталей, при существенных изменениях в высотах расположения головок смежных автосцепок по отношению к уровню рельса, а также при резких изменениях силовых эксплуатационных факторов возможны заклинивание, излом или иное повреждение рабочих элементов.
При этом трущиеся поверхности могут получить задиры в локальных областях, значительно увеличивающих в дальнейшем интенсивность изнашивания сопряжений.
Повреждения механизма автосцепки и поглощающего аппарата увеличиваются при вождении сверхтяжелых поездов, а также на сортировочных горках в случае низкой эффективности работы вагонных замедлителей.
Автосцепные устройства при работе испытывают значительные динамические нагрузки, действующие в различных плоскостях, большие перепады температур. Кроме того, на их работу отрицательно влияет незащищенность сопряженных деталей от попадания в зоны трения абразивных частиц.
Сложное конструктивное исполнение деталей и их геометрических форм требует повышения уровня технологии изготовления, ремонта, системы контроля и испытаний.
Значительные продольные и поперечные нагрузки на автосцепку появляются при входе состава в кривые участки пути или выходе из них, при переломах профиля железнодорожного полотна, на сортировочных станциях и горках, при трогании с места и торможениях. Перегрузки в материале деталей автосцепки также возникают от несинхронности колебаний сочлененных вагонов. При этом особенно сильно и часто этот эффект возрастает, когда неисправны гасители колебаний как гидравлического, так и фрикционного типа. Тогда все основные детали не только перегружаются, но и интенсивно изнашиваются. Возможны даже саморасцепы вагонов, появление деформаций в отдельных деталях устройства, отколов, трещин и других повреждений, включая разрушения.
Возникновение знакопеременных нагрузок приводит к развитию трещин, изломам. В отдельных случаях встречаются хрупкие разрушения, что определяется как неблагоприятным сочетанием действующих сил, климатических и других факторов, так и внутренними отклонениями и пороками кристаллической структуры.
Сложный профиль многих деталей также является естественным источником концентрации внутренних напряжений, особенно в переходных поверхностях.
Основной причиной ремонта и замены деталей при плановых и текущих ремонтах является износ.
В отдельных случаях, например при появлении местных, односторонних износов деталей, при существенных изменениях в высотах расположения головок смежных автосцепок по отношению к уровню рельса, а также при резких изменениях силовых эксплуатационных факторов возможны заклинивание, излом или иное повреждение рабочих элементов. При этом трущиеся поверхности могут получить задиры в локальных областях, значительно увеличивающих в дальнейшем интенсивность изнашивания сопряжений.
Повреждения механизма автосцепки и поглощающего аппарата увеличиваются при вождении сверхтяжелых поездов, а также на сортировочных горках в случае низкой эффективности работы вагонных замедлителей.
Дефекты и повреждения деталей автосцепного устройства выявляются как визуально, так и с использованием вспомогательных средств контроля, например лупы, дефектоскопа, шаблонов и др.
По характерным внешним признакам, например, таким, как развитие местной коррозии, скопление в виде тонкой полоски валика из пыли, грязи, инея, уже до очистки и обмывки деталей можно определить места возможного расположения трещин, которые должны быть впоследствии тщательно осмотрены и всесторонне проверены.
Так, после расчистки зон повреждения головы корпуса автосцепки их обследуют с использованием лупы. Выявленные трещины вырубают на всю глубину залегания и на 15-20 мм далее видимых границ начала и конца. Разделка кромок трещины может производиться с помощью ручного или пневматического зубила, строганием на станке, электродуговой или газокислородной резкой.
К основным неисправностям корпуса автосцепки (рис.6) относятся: трещины 1 в углах, образованных ударной стенкой зева и боковой стенкой большого зуба, а также между этой стенкой и тяговой стороной большого зуба; трещины в углах проемов для замка и замкодержателя. Эти трещины образуются в результате влияния концентрации напряжений в зонах перехода от одной поверхности к другой, так как при изготовлении часто уменьшаются радиусы сопряжений стенок контура изделия против установленных. Эксплуатация показывает, что 42,5% корпусов автосцепки бракуют из-за наличия трещин в этих зонах;
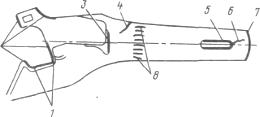