ВУЗ: Не указан
Категория: Не указан
Дисциплина: Не указана
Добавлен: 04.12.2023
Просмотров: 193
Скачиваний: 1
СОДЕРЖАНИЕ
1.1. Планово-предупредительная система и виды технического
1.2. Необходимость совершенствования технического обслуживания
1.3. Методы организации труда при выполнении технического
обслуживания и ремонта автомобилей
1.5 Организация периодического ТО.
1.6 Организация безразборной проверки техсостояния машин
1.7 Совершенствование планирования ТО
2.1 Расчет количества ТО автомобилей
2.2 Расчет трудоемкости профилактических работ
2.3 Распределение технического обслуживания по методам проведения
2.4. Расчет годовой трудоемкости и количестварабочих дней
2.5. Годовой план загрузки мастерской
2.6. Определение количества рабочих в мастерской
2.8. Расчет размеров и подбор оборудования
2.9. Расчёт площадей мастерских
2.10. Расчет искусственного освещения
2.11. Расчет приточно-вытяжной вентиляции
3.1. Общие требования охраны труда
3.2. Требования охраны труда во время работы
3.3. Требования безопасности к инструменту
3.4. Требования охраны труда по окончании работы
1.4 Организация работы ЕТО
Основным назначением ежедневного обслуживания является общий контроль за состоянием узлов и систем, обеспечивающих безопасность движения и поддержание надлежащего внешнего вида. Организация ежедневного обслуживания включает контроль технического состояния, уборку, мойку и заправку автомобилей топливом, маслом и т.д. Перед выездом на линию и при возвращении контроль технического состояния подвижного состава осуществляется механиком контрольно-технического пункта (КТП), механиком автоколонны и водителем, а при работе на линии водителем. При этом проверяется комплектность автомобиля, внешний вид, действие приборов освещения и сигнализации, тормозов и рулевого управления, крепление колес, давление воздуха в шинах, количество топлива, токсичность отработавших газов.
1.5 Организация периодического ТО.
Техническое обслуживание № 1 (ТО-1) предназначено для поддержания автомобилей в технически исправном состоянии, выявления и предупреждения отказов и неисправностей, а также снижения интенсивности изнашивания деталей, узлов и механизмов путем проведения установленного комплекса работ:
- контрольно-смотровых и диагностических;
- крепежно-регулировочных;
- смазочно-очистительных;
- электротехнических;
Технологическая карта ТО-1 автомобиля КАМАЗ-5320. Таблица 3.
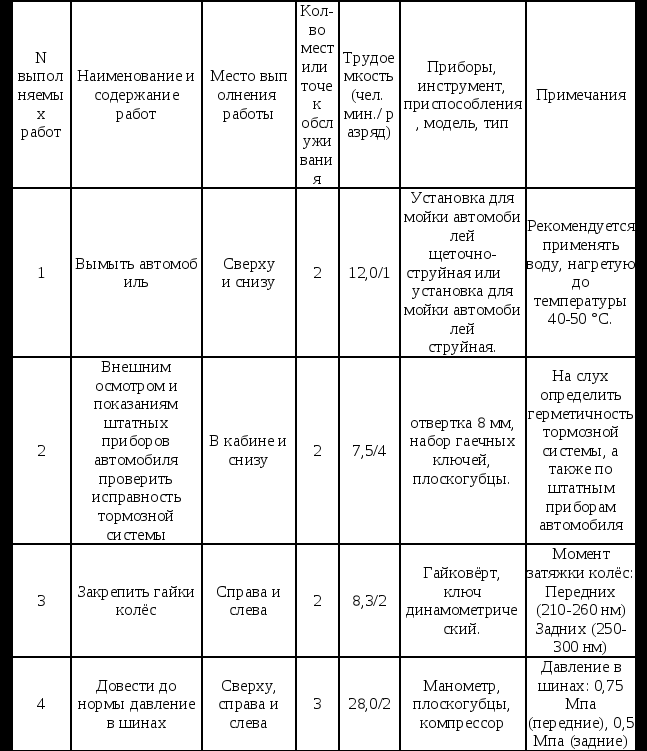
Техническое обслуживание № 2 (ТО-2) имеет то же назначение, что и ТО-1, но проводится в большем объеме, с проведением углубленной проверки параметров работоспособности автомобиля (и не только в целях выявления различных неисправностей, но и для определения возможного ресурса пробега без проведения текущего ремонта по ходу дальнейшей эксплуатации автомобиля), а также устранения обнаруженных неисправностей путем замены неисправных легкодоступных деталей и даже узлов (не допускается лишь замена основных агрегатов). Причем замена деталей и узлов не считается обслуживанием – этот процесс при ТО-2 называется
сопутствующим ремонтом (СР).На него отводится дополнительная трудоемкость и соответственно увеличивается количество необходимых рабочих на его проведение.
Технологическая карта ТО-2 автомобиля КАМАЗ-5320. Таблица 4.
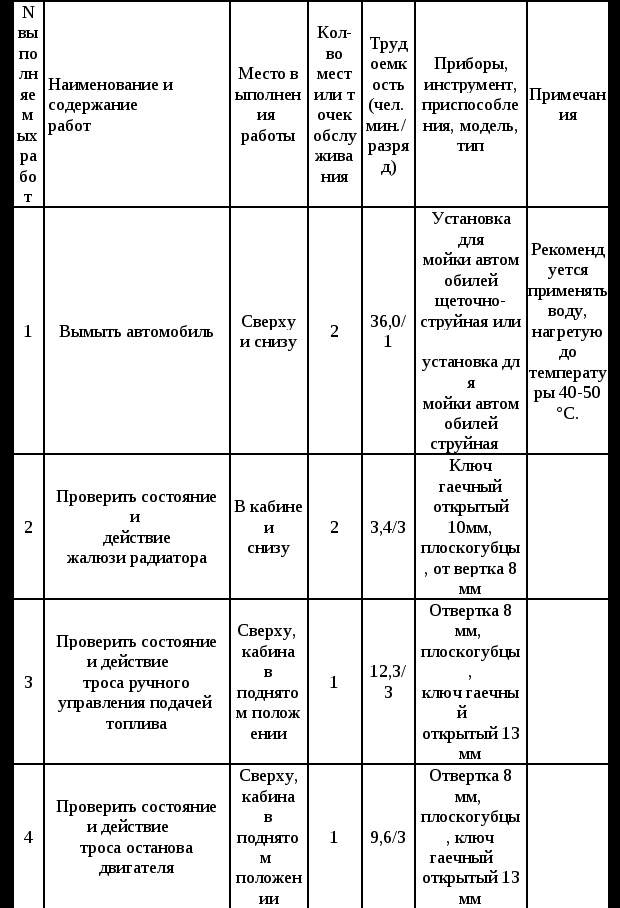
1.6 Организация безразборной проверки техсостояния машин
Перечень операций при безразборной проверки техсостояния
автомобиля КАМАЗ 5320
Таблица 5.
№ операции | Содержание работ и технические условия | Оборудование |
1 | Установить автомобиль передними колесами на ролики стенда СТМ 16000.01, заглушить двигатель. Колеса не должны касаться отбойных роликов | СТМ 16000.01 |
2 | Проверить состояние шин и давление воздуха в них. При необходимости довести давление в шинах до нормы, используя воздухораздаточную колонку (компрессор'). Не допускается наличие посторонних предметов в протекторе шины, вспучивание, глубокие порезы. Выступы на протекторе не менее 1 мм | |
3 | Проверить состояние и натяжение приводных ремней водяного насоса. Генератора компрессора насоса гидроусилителя руля. При необходимости отрегулировать натяжение, используя устройство КИ-13918 (КИ-8920), набор инструмента 2446. Ремни должны быть сухими и не иметь расслоений. Прогиб ремней посередине ветви при усилении 40Н не более 15…20 мм. Негодный ремень заменить | устройство КИ-13918 (КИ-8920), набор инструмента 2446 |
4 | Проверить свободный ход педали сцепления. При необходимости отрегулировать, используя устройство КИ-8929, набор инструмента 2446. Заедание педали не допускается. Свободный ход 30…42 мм | устройство КИ-8929 набор инструмента 2446 (Либо, более современные аналоги) |
5 | Проверить свободный ход педали тормоза. При необходимости отрегулировать. Заедание педали не допускается. Свободный ход педали тормоза для КамАЗов 23…30 мм. | |
6 | Проверить давление воздуха в пневмосистеме, падение давления при одном нажатии на педаль тормоза, используя штатный манометр автомобиля. Давление воздуха должно быть в пределах 0,5…0,8 Мпа | |
7 | Проверить силу сопротивления качению колес переднего моста. Шины и тормозные накладки колес должны быть сухими. Без нажатия на педаль тормоза при вращении колес отклонение стрелки прибора от начальной отметки не должно превышать 5 делений. Проверить тормозную силу на колесах. Плавным торможением при давлении воздуха в приводе 0,7 Мпа зафиксировать максимальную силу на каждом колесе, которая должна быть (не менее): для КамАЗов – 8200. Н Проверить время срабатывания тормозов. Разность тормозных сил левого и правого колес не должна превышать 20% от максимальной. Установить задатчик тормозных сил в положение, соответствующее ближайшему меньшему значению тормозной силы, определенной на стенде. Выполнить аварийное торможение. Допустимое время срабатывания тормозов не более 0,6 с, а разница срабатывания тормозов колес одной оси не более 0,12с. Проверить деформацию тормозных барабанов, используя устройство КИ-12372. Разница в показаниях устройства не более 0,15 мм. Предельная деформация 1,3 мм для КамАЗов; | |
8 | Проверить ход штоков тормозных камер, используя линейку. Ход штока 15…25 мм – для КамАЗов | |
9 | При необходимости отрегулировать тормоза на максимальную силу торможения и минимальную одновременность срабатывания, используя набор инструмента 2446. Регулировка производится червяком регулировочного рычага. Зазор между колодкой и тормозным барабаном для КамАЗов – 0,4 мм у разжимного кулака и 0,2 мм у осей колодок | набор инструмента 2446 |
10 | Проверить тормозные качества средних колес и отрегулировать тормоза (по параметрам операции 7). Максимальная сила торможения для КамАЗов – 5000 Н | |
11 | Проверить ход штоков тормозных камер (см. операцию 8). Время срабатывания тормозов средних и задних колес должно отличаться от времени срабатывания передних не менее чем на 10% | |
12 | Проверить люфт рулевого колеса, используя прибор К-402 или К-187. Проворачивать рулевое колесо с усилием 10 Н сначала влево, затем вправо при работающем двигателе. Допустимый люфт не более 25° | используя прибор ИСЛ-М |
13 | Проверить визуально состояние и действие фар, световой и звуковой сигнализации. При необходимости отрегулировать фары. При необходимости заменить лампы. Отрегулировать звуковой сигнал | |
1.7 Совершенствование планирования ТО
Низкий уровень специализации ремонтных работ приводит к тому, что на ряде крупных машиностроительных заводов 50-60 % общего объема капитального ремонта производится децентрализовано в цеховых ремонтных базах с изготовлением большей части запасных деталей на низком техническом уровне. Децентрализация ремонтного хозяйства приводит к тому, что ремонт одномодельного оборудования осуществляется параллельно в нескольких цеховых мастерских одного и того же завода. При этом цеховые механики вынуждены выполнять техническую подготовку одних и тех же работ в различных вариантах. В результате стоимость изготовления запасных частей намного дороже, чем в станкостроении, а ремонт оборудования в ряде случаев оказывается экономически невыгодным.
Основными направлениями совершенствования ремонтного хозяйства являются:
Организация централизованного ремонта оборудования. Например, в Чехии капитальный ремонт почти всего оборудования осуществляется на централизованных ремонтных предприятиях, в результате чего стоимость капитального ремонта не превышает 60-80 % стоимости нового станка;
Создание ремонтных баз на предприятиях-изготовителях оборудования, что повышает заинтересованность в качестве своего оборудования;
Организация специализированного производства запасных частей к оборудованию. Так, отечественное станкостроение выпускает только 2% запасных деталей от стоимости оборудования, в то время как в США их выпуск достигает более 20 %;
Централизация ремонта и обслуживания оборудования непосредственно на промышленных предприятиях. Она предусматривает подчинение главному механику всех ремонтных баз предприятия и ликвидацию двойного подчинения цеховых баз главному механику и начальнику цеха, повышение ответственности главного механика за качественное состояние оборудования, за выполнение плана ремонта и экономические показатели ремонтного хозяйства;
Проведение организационной реструктуризации машиностроительных предприятий, предполагающей выделение ремонтного хозяйства в самостоятельное малое предприятие, специализирующееся на ремонте технологического оборудования для нужд данного машиностроительного и других предприятий. Это позволит значительно повысить эффективность ремонтного производства в целом;
Механизация ручных ремонтных работ, особенно слесарных. Оснащение ремонтно-механических цехов высокопроизводительным универсальным и специальным оборудованием, обеспечение ремонтных бригад подъемно-транспортным оборудованием. Это направление особенно важно, так как на ремонтных работах все еще низок уровень механизации и высок уровень ручного труда, что требует больших затрат труда и высокой квалификации ремонтных рабочих;
Применение современных средств технической диагностики состояния оборудования. Так, повреждения станков с ЧПУ диагностирует сама ЭВМ;
Внедрение прогрессивных методов, технологических процессов и организационных форм выполнения ремонтных работ. К числу прогрессивных методов ремонта в первую очередь относится узловой и последовательно-узловой;
Организация восстановления деталей и узлов. Восстановление деталей позволяет добиться сокращения расхода металла при ремонте деталей до 60-90 %. Себестоимость восстановленных деталей нередко составляет 10-25 % стоимости новой детали. Наиболее целесообразна организация специализированных баз восстановления при ремонтных заводах;
Совершенствование технической подготовки ремонта, включающей разработку типовых технологических процессов, а также материальное обеспечение;
Эффективное использование специализированных ремонтных бригад по ремонту и межремонтному обслуживанию оборудования, за которыми закреплены отдельные участки или группы оборудования независимо от цеховой принадлежности. Такие бригады создаются в составе от 5 до 10 человек слесарей и одного станочника на каждые 1000-2000 р. Е. установленного оборудования при его работе в две смены. Эти бригады входят в состав корпусных ремонтных баз (КРБ);
2. Расчётная часть
В дальнейшем я рассмотрел возможность проведения ТО
для 15 автомобилей КАМАЗ
2.1 Расчет количества ТО автомобилей
Определение количества ТО для автомобилей