Файл: Проектирование машиностроительных цехов и заводов. Основные стадии проектирования промышленного предприятия.doc
ВУЗ: Не указан
Категория: Не указан
Дисциплина: Не указана
Добавлен: 12.01.2024
Просмотров: 387
Скачиваний: 1
ВНИМАНИЕ! Если данный файл нарушает Ваши авторские права, то обязательно сообщите нам.
СОДЕРЖАНИЕ
Проектирование машиностроительных цехов и заводов.
Основные стадии проектирования промышленного предприятия.
Проектирование механических цехов.
Классификация механических цехов.
Основные этапы разработки проекта механического цеха.
Технико-экономические показатели проекта механического цеха
Проектирование сборочных цехов.
Проектирование внутризаводского транспорта.
Транспортная система на предприятии.
Основные виды подъемно-транспортного оборудования.
Расчет потребного количества подъемно-транспортного оборудования.
Классификация цехов по характеру конструкции и весу изделий.
I класс – изделия с черным весом до 100 кг.
-
металлорежущие станки для часовой промышленности и инструментального производства; -
нормальный металлорежущий и измерительный инструмент; -
подшипники качения; -
спец. приборы;
II класс – изделия с черным весом до 2 т.
-
металлорежущие и деревообрабатывающие станки; -
двигатели, дизели, компрессоры; -
сельскохозяйственные машины, электродвигатели средней мощности.
III класс – изделия с черным весом до 15 т (изделия тяжелого машиностроения):
-
тяжелые металлорежущие и деревообрабатывающие станки; -
кузнечные молоты, прессы; -
водяные и паровые турбины; -
дорожные машины;
IV класс – изделия особо тяжелого машиностроения (черный вес более 15 тонн).
Классификация по количеству металлорежущих станков.
Класс цеха | I | II | III | IV |
Малый цех | до 150 | до 125 | до 75 | до 40 |
Средний цех | 150 – 300 | 125 – 250 | 75 – 125 | 40 – 75 |
Крупный цех | свыше 300 | свыше 250 | свыше 125 | свыше 75 |
Основные этапы разработки проекта механического цеха.
-
Разработка задания для проектирования цеха, исходя из производственной программы завода, чертежей, описаний конструкций, технических условий на изготовление изделий. -
Определение типа производства. -
Разработка технологического процесса механической обработки в зависимости от типа производства и его организационной формы. -
Определение количества станков и коэффициента их загрузки. -
Определение потребности цеха в электроэнергии, газе, паре, воде, сжатом воздухе. -
Определение необходимого рабочего состава цеха и его численности. -
Разработка плана расположения оборудования и определение производственной площади. -
Определение количества оборудования и площадей вспомогательных отделений служебных и бытовых помещений. -
Выбор типа транспортных и грузоподъемных средств и определение их количества. -
Компоновка цеха, определение основных размеров. -
Разработка схемы организации, управления и технического руководства.
Определение типа производства: через Кзо – см курс ТМС (там же расчет величины партии)
Фонды рабочего времени
В процессе проектирования машиностроительных заводов различают календарный, номинальный и действительный фонды времени работы оборудования и рабочих.
Календарный годовой фонд времени: 24 365 = 8760 часов
Номинальный годовой фонд времени работы (41 рабочий час в неделю):
-
Рабочих Фкр = 2070 часов -
Оборудования: 1 сменная работа – 2070 час; 2-х сменная – 4140 часов; 3-х сменная – 6210 часов;
Действительный годовой фонд времени: состоит из номинального фонда времени за исключением неизбежных потнрь (отпуска, болезни, декретные отпуска и т.д.)
15 дней отпуска Фдр = 1860 часов;
18 дней отпуска Фдр = 1840 часов;
24 дня отпуска Фдр = 1820 часов.
Действительный фонд рабочего времени оборудования, включая потери от простоя оборудования в планово-предупредительном ремонте (3 – 4 %) и составляет (4029 – 4015 часов) для обычного оборудования; и 3904 (6% потерь) – для уникального оборудования.
В серийном производстве запуск и выпуск готовой продукции происходит партиями:
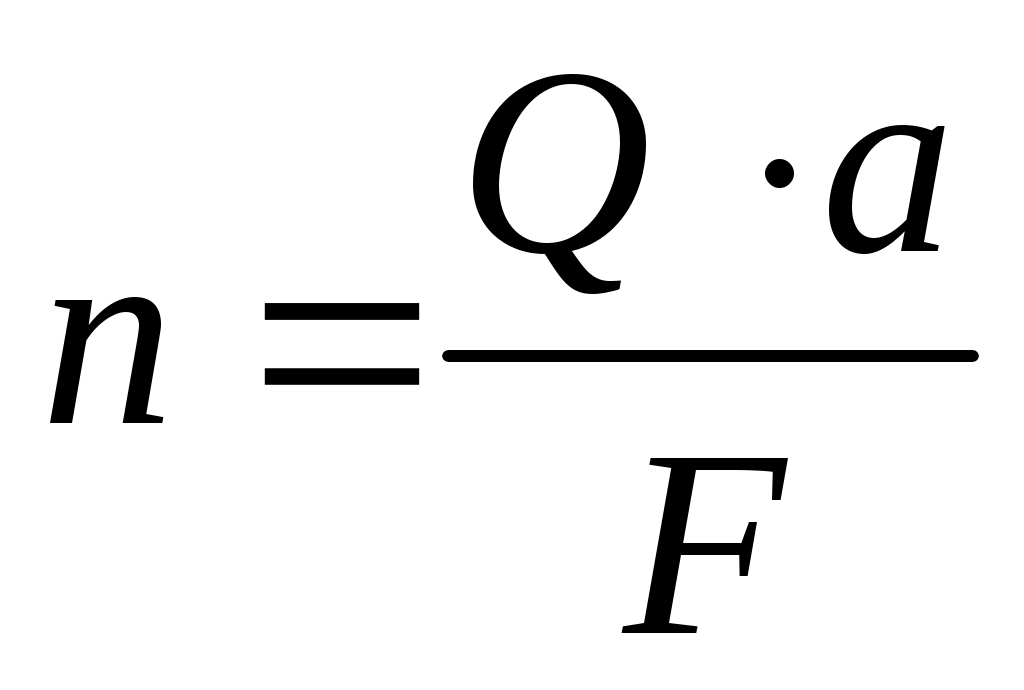
где F – число рабочих дней в году (254 дня).
а – число дней, на которое необходимо иметь запас деталей.
Производственная программа цеха.
Основой для проектирования цеха является его производственная программа, составленная исходя из производственной программы завода. В зависимости от типа производства, характера выпускаемой продукции и стадии проектирования производственная программа может быть точной, приведенной и условной.
Производственная программа называется точной, когда номенклатура всех подлежащих изготовлению изделий и деталей (включая запчасти) точно установлена и обеспечена рабочими чертежами, спецификациями, ТУ. Проектирование предусматривает подробную разработку технологических процессов, маршрутных, операционных карт, эскизов и схем, технического контроля, нормирования операций. Этот вид проектирования применяется для массового и крупносерийного производства, где требуется большая точность.
Образец ведомости точной подетальной производственной программы предприятия:
№ п/п | Наименование детали | № дет по чертежу | Материал (наименование и марка по ГОСТ) | Количество деталей на годовую программу с учетом запчастей) | Вес 1 детали | Вес всех деталей на год. программу | ||
черный | чистый | черный | чистый | |||||
1. 2. 3. | … | | | | | | | |
Для единичного, мелкосерийного и серийного производства программа составляется в виде перечня изготовленных в цехе изделий или узлов с указанием их количества и массы. При этом подетальная ведомость составляется только для типового изделия. Все остальные изделия, входящие в программу, приводятся к типовым. В этом случае нет необходимости иметь полный перечень обрабатываемых деталей. Чертежи, как правило, имеются только на изделия-представители, по которым ведутся расчеты. Такая производственная программа называется приведенной.
При проектировании цехов для обработки деталей изделий, конструкции которых еще не разработаны и точная номенклатура изготовляемых цехом изделий неизвестна (экспериментальные цехи), выбираются условные представители, по которым можно с достаточным приближением получить необходимые исходные данные. По принятым условным представителям и ведется проектирование. В этом случае программа является условной.
Приведенная программа определяется следующим образом:
-
вся номенклатура изделия разбивается на группы, в каждую из которых входят изделия, сходные по конструкции и технологии изготовления; -
в каждой группе намечается типовое изделие представитель, по которому ведутся все расчеты; -
все другие изделия группы приводятся по трудоемкости к изделию представителю с учетом их различия в массе, серийности программы и сложности механической обработки. Эти различия оцениваются коэффициентом приведения:

где Км – коэффициент приведения по массе;
Ксер – коэффициент приведения по серийности;
Ксл – коэффициент приведения по сложности.
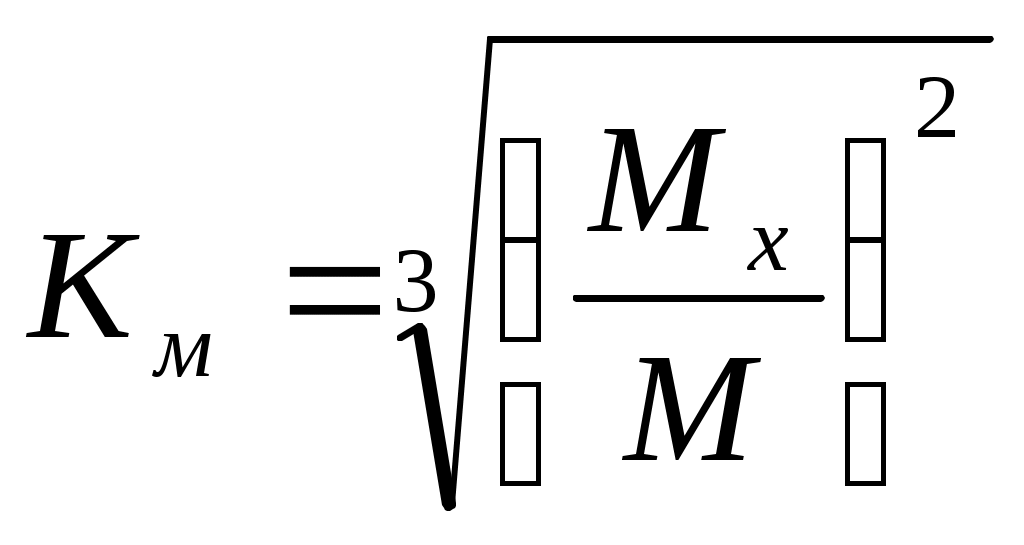
где Мх – масса приводимого изделия,
М – масса изделия представителя.
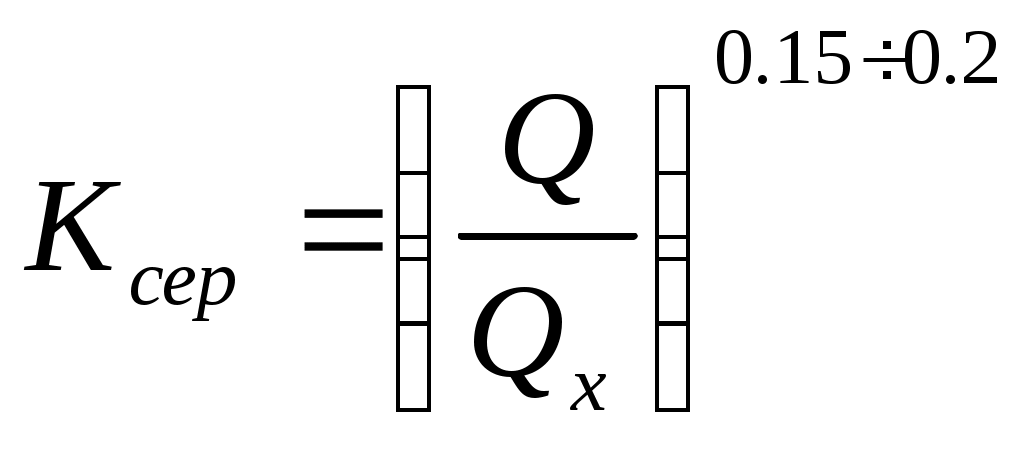
где Q – годовой выпуск изделия представителя;
Qx – годовой выпуск приводимого изделия.
Показатель степени выбирается равным 0,15 для среднего и мелкого машиностроения и 0,2 – для тяжелого.
Ксл – учитывает различие в сложности конструкций изделий и является в значительной степени субъективным. Для механических цехов при определении Ксл учитывают главным образом различие в точности и чистоте обработки.
В проектных организациях:
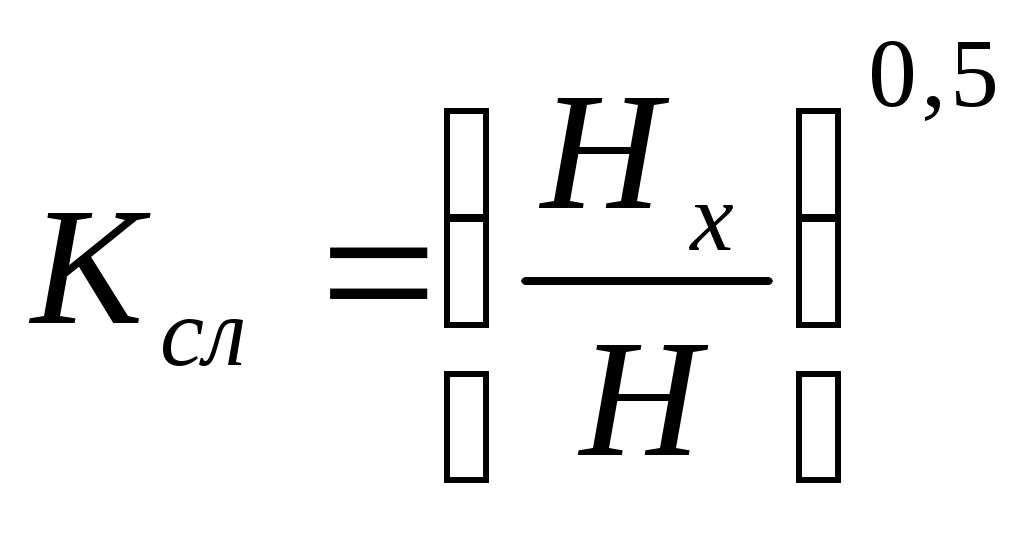
где Нх – число оригинальных деталей в приводимом изделии
;
Н – число оригинальных деталей в изделии-представителе.
Наименование изделия | Заданная программа | Приведенная программа | Приведенное количество изделий на годовую программу | ||||||
Годовое кол-во шт., комплектов | Масса в т | Наименование базового изделия | Коэффициент приведения | ||||||
одного изделия | годовой программы | по массе | по серийности | по сложности | общий | ||||
Изд. А Изд. Б Изд. В | 400 200 100 | 0,8 0,8 0,4 | 320 160 40 | Изд. А | 1,0 1,0 0,63 | 1,0 1,12 1,22 | 1,0 1,3 1,5 | 1,0 1,46 1,16 | 400 292 116 |
Всего: | 700 | - | 520 | Всего: | 808 |