Файл: Проектирование машиностроительных цехов и заводов. Основные стадии проектирования промышленного предприятия.doc
ВУЗ: Не указан
Категория: Не указан
Дисциплина: Не указана
Добавлен: 12.01.2024
Просмотров: 392
Скачиваний: 1
ВНИМАНИЕ! Если данный файл нарушает Ваши авторские права, то обязательно сообщите нам.
СОДЕРЖАНИЕ
Проектирование машиностроительных цехов и заводов.
Основные стадии проектирования промышленного предприятия.
Проектирование механических цехов.
Классификация механических цехов.
Основные этапы разработки проекта механического цеха.
Технико-экономические показатели проекта механического цеха
Проектирование сборочных цехов.
Проектирование внутризаводского транспорта.
Транспортная система на предприятии.
Основные виды подъемно-транспортного оборудования.
Расчет потребного количества подъемно-транспортного оборудования.
Задачей организации рабочего места является создание такой конструкции оснастки и такого расположения оборудования, заготовок, готовых деталей, при которых отсутствуют лишние и нерациональные движения и приемы (повороты, нагибания, приседания и т.д.), максимально сокращаются расстояния перемещения рабочего.
Схема организации рабочего места должна соответствовать характеру производства. В условиях единичного производства выполнение на рабочем месте большого числа разнообразных операций требует наличия всевозможных инструментов, приспособлений, а отсюда и соответствующего инвентаря для его хранения и расположения.
При переходе к серийному производству и специализации производственных участков число операций, выполняемых на рабочем месте, сокращается, начинается применение специализированного инструмента и приспособлений и соответственно меняется планировка и оснащение рабочего места.
Н

Рис. Пример планировки рабочего места токаря.
1 – инструментальный столик; 2 – решетка под ноги; 3 – приемный стол; 4 – тара с обрабатывемыми деталями; 5 – планшет для измерительного инструмента; 6 – подставка для чертежей; 7 – урна для мусора.
аиболее значительные изменения в организации рабочего места происходят под влиянием механизации и автоматизации производства. Так на рабочих местах автоматических и непрерывно-поточных линий никаких видов специального стационарного инвентаря, как правило не предусматривается.
При многостаночной работе планировка рабочего места должна обеспечивать наиболее удобное для рабочего расположение органов управления всех обслуживаемых станков и минимальную затрату времени на переходы от одного станка к другому.
Варианты рационального расположения станков при их обслуживании одним рабочим:

Рис. Расположение рабочего места при многостаночном обслуживании
Технико-экономические показатели проекта механического цеха
К числу основных показателей проекта механического цеха относятся:
А: Абсолютные показатели, характеризующие производственную мощность цеха:
-
Годовой выпуск изделий (комплектов, машин, узлов или деталей) включая запасные части, в штуках -
Годовой выпуск изделий по цеховой себестоимости в рублях, в т.ч. запасных частей. -
Годовой выпуск изделий в тоннах, в т.ч. запасных частей. -
Количество рабочих смен. -
Площадь цеха (м2) в т.ч. общая, и производственная. -
Количество производственного оборудования с указанием количества металлорежущих станков и автоматических линий. -
Количество работающих (производственных рабочих, вспомогательных рабочих, МОП, ИТР, служащих). -
Основные фонды (руб.), в т.ч. здания и сооружения; оборудование инструмент и приспособления; производственный и хозяйственный инвентарь. -
Годовой фонд заработной платы производственных рабочих и всех работающих. -
Установленная мощность электродвигателей (кВт).
Б: Относительные показатели, характеризующие технико-экономическую эффективность цеха:
-
Годовой выпуск продукции в руб. (по себестоимости), комплектах и тоннах:
а) на одного работающего и одного рабочего;
б) на единицу производственного оборудования;
в) на 1 м2 производственной площади в одну смену.
-
Годовой выпуск продукции в рублях (по себестоимости) на 1 рубль основных фондов. -
Основные промышленные фонды на 1 рубль выпуска. -
Общая и производственная площадь на единицу производственного оборудования, м2. -
Средний коэффициент загрузки оборудования (по времени) в %. -
Коэффициент сменности. -
Средняя установленная мощность одного станка, кВт. -
Средняя установленная мощность станочного оборудования (кВт), на одного производственного рабочего в наибольшую по количеству работающих смену (энерговооруженность). -
Трудоемкость и станкоемкость одного комплекта деталей, одной машины, одной тонны продукции в человеко-часах и станко-часах. -
Коэффициент использования металла. -
Отношение цеховых расходов к основной зарплате производственных рабочих, %. -
Уровень механизации и автоматизации производства.
Проектирование сборочных цехов.
Сборочные работы являются заключительным этапом в производственном процессе, где из отдельных деталей и узлов собираются готовые изделия, качество сборочных работ значительно влияет на эксплуатационные свойства машин, их надежность и долговечность. Даже при точном изготовлении деталей и некачественной сборке машина не будет обладать необходимыми качествами.
Трудоемкость сборочных работ составляет:
-
в сельскохозяйственном машиностроении – 20 – 30 % -
в автомобилестроении – 20 – 25 % -
в тяжелом машиностроении – 25 – 35 %
Сборочный цех проектируется для выполнения узловой и общей сборки, производства испытаний, окраски и упаковки изделий.
Сборочные цеха различают по типу производства, общей площади цеха и грузоподъемности подъемно-транспортных средств.
Основой для проектирования сборочного цеха является его производственная программа, включающая:
-
спецификации поступающих в цех узлов и деталей; -
сборочные чертежи и технические условия на приемку и испытание изделий.
Организационные формы сборки.
Проектирование сборочных цехов также, как и механических, ведется по точной, приведенной или условной программе.
Проектирование цехов массового и крупносерийного производства ведется по точной программе.
Проектирование сборочных цехов мелкосерийного и серийного производства при разнообразной и обширной номенклатуре ведется по приведенной программе, для составления которой все подлежащие сборке машины распределяются на группы по конструктивной и технологической однородности. В каждой группе есть типовой представитель, на который разрабатывается техпроцесс с нормированием каждой операции.
Различают две основные организационные формы сборки: стационарную и подвижную. Стационарная сборка изделия может осуществляться последовательно или параллельно. В последнем случае весь объем сборочных работ расчленяется по узлам, собираемым параллельно на разных рабочих местах, с последующей сборкой всего изделия из деталей и узлов.
При подвижной сборке собираемый объект перемещается от одного сборочного места к другому, причем за каждым рабочим местом закрепляются определенные операции и рабочие. Эти основные формы сборки делятся еще на поточные и непоточные.
Поточная сборка может осуществляться как при неподвижном объекте сборки, так и при подвижном.
При неподвижном объекте поточная сборка выполняется на расположенных в линию неподвижных стендах. Каждый рабочий (или бригада рабочих) в соответствии с установленным тактом сборки выполняет одну и ту же, твердо закрепленную за ним операцию, переходя от одного стенда к другому. Такая сборка обычно применяется в условиях мелкосерийного производства или при сборке крупногабаритных изделий (тяжелые станки, двигатели и пр.) и когда такт сборки достаточно велик.
Поточная сборка при подвижном объекте может осуществляться несколькими способами:
-
на непрерывно движущемся конвейере, скорость перемещения которого обеспечивает возможность выполнения сборочных операций на протяжении каждого рабочего места; -
на конвейере с пульсирующим (периодическим) движением, когда сборка производится в периоды остановки объекта; -
с перемещением собираемого объекта от одного рабочего места к другому вручную (по рольгангу, на рельсовых и безрельсовых тележках и др.) или с помощью специальных механических транспортирующих средств.
Основной расчетной величиной при поточной сборке является «такт сборки», определяющий период времени равномерного выпуска собранных изделий или узлов.
При поточной сборке с регламентированными перерывами на обслуживание рабочих мест, отдых и т.д. пользуются «действительным тактом сборки»
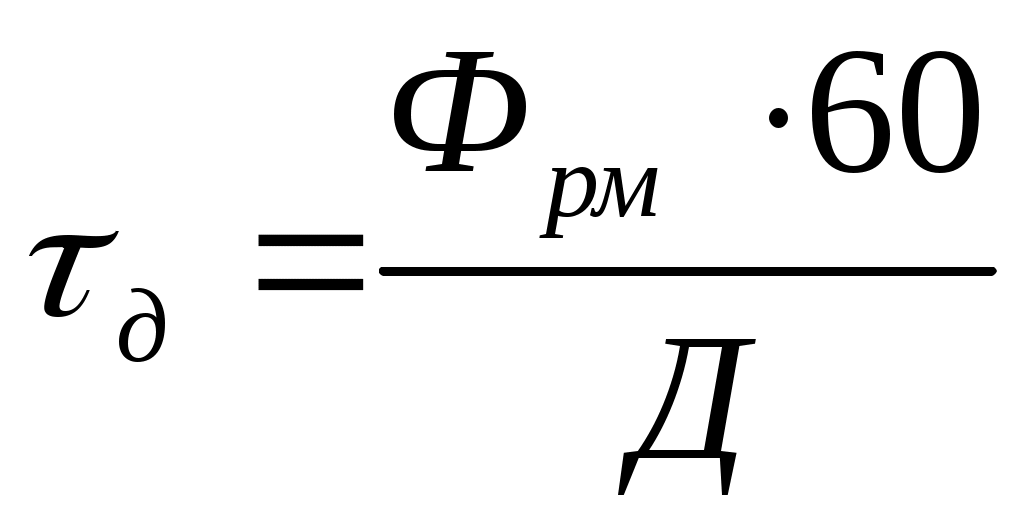
где Фрм - действительный годовой фонд времени работы сборочного оборудования рабочего места за вычетом годовых потерь времени на регламентированные перерывы на обслуживание рабочих мест, отдых и прочее в часах;
Д – годовой выпуск изделия или узла, шт.
В проектных организациях техпроцесс сборки разрабатывается по картам или маршрутным ведомостям. Для определения последовательности операций сборки составляют технологическую схему сборки.
При разработке по картам тех. процесс разбивают на операции и переходы, указывают оборудование, инструмент, приспособление, норму времени и количество рабочих, необходимых для выполнения каждой операции.
В единичном и мелкосерийном производстве тех. процесс сборки обычно разрабатывается по маршрутным ведомостям. Техпроцесс разбивается только на операции.
Определение трудоемкости сборки.
Трудоемкость сборочных работ определяется следующими методами:
-
по технологическому процессу -
методом сравнения (по производственной программе); -
по данным заводов; -
по укрупненным показателям.
По технологическому процессу – трудоемкость определяется путем нормирования операций и переходов на основе известных структурных формул:
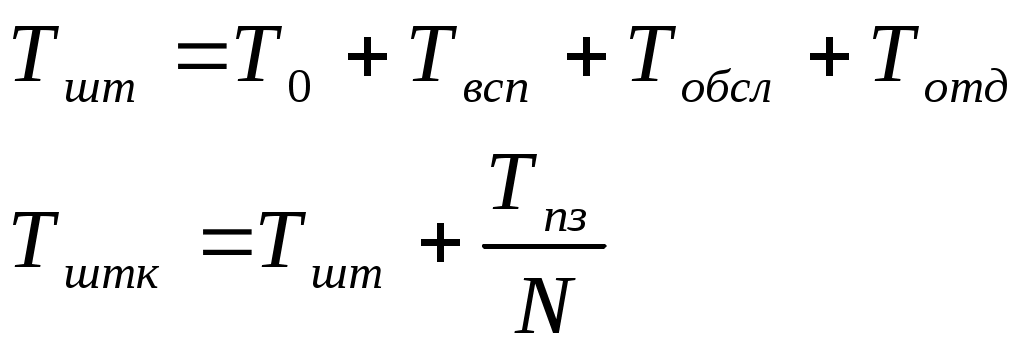
Определение Тшт и Тштк производится по общемашиностроительным нормативам на слесарно-сборочные работы, разработанные для соответствующих видов производства. Т.к. при сборке основное и вспомогательное время является ручным, то их объединяют в оперативное время:
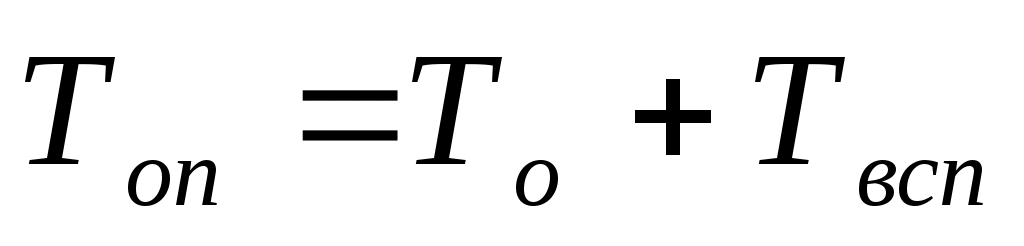
Трудоемкость может быть определена также и другими методами, которые рассмотрены при проектировании механических цехов. Общую трудоемкость сборки машины подразделяют а трудоемкость слесарно-пригоночных работ Тсл, узловой сборки Тузл, и общей сборки - Тобщ.
Таблица
Соотношение трудоемкости видов сборочных работ, %.
Вид сборочных работ | Тип производства | ||||
Единичн. | М/серийн. | Серийное | Кр/серийн. | Массовое | |
Слесарно- пригоночные | 25 – 30 | 20-25 | 15-20 | 10-15 | - |
Узловая сборка | 5-10 | 10-15 | 20-30 | 30-40 | 45-60 |
Общая сборка | 60-70 | 60-70 | 50-65 | 45-60 | 40-55 |
Определение количества рабочих мест и оборудования.
Количество рабочих мест определяется по трудоемкости сборки, рассчитанной одним из рассмотренных выше способов.
Для непоточного производства при точном проектировании:
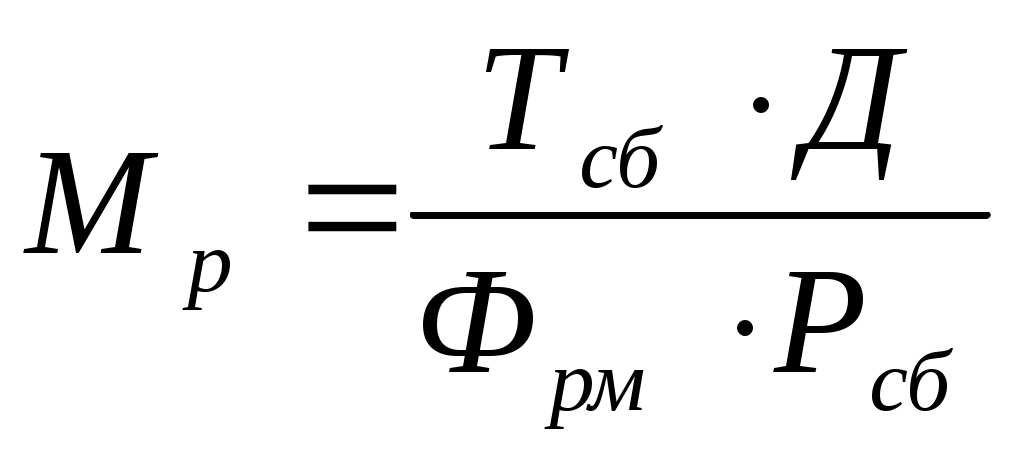
где Тсб