ВУЗ: Не указан
Категория: Не указан
Дисциплина: Не указана
Добавлен: 24.10.2023
Просмотров: 121
Скачиваний: 4
ВНИМАНИЕ! Если данный файл нарушает Ваши авторские права, то обязательно сообщите нам.
и глубже обессеривать сырье. Свежий катализатор должен иметь индекс активности не ниже 95 %. Если ак-
тивность свежего катализатора не достигает максимальной величины, катализа- тор активируют в течение нескольких часов при температуре более 500 ºС. Со временем активность катализатора падает за счет отложений кокса на поверх- ности катализатора. Для восстановления активности катализатор подвергается паровоздушной регенерации.
Гидроочистка дизельного топлива осуществляется целым комплексом оборудования и часто состоит из нескольких стадий. Совершенствование уста- новки гидроочистки в большинстве случаев сводится к совершенствованию ре- актора гидроочистки.
Рассмотрим различные способы гидроочистки дизельного топлива то нежелательных примесей - серы, азота, металлов, кислорода.
В патенте [10] описан способ гидроочистки дизельного топлива. Задача данного способа - снизить энергозатраты на подготовку сырья гидроочистки, а также сформировать оптимальной границы деления исходного сырья на легкую и тяжелую фракции с уменьшением объема катализатора в реакторах.
Сначала сырьевой поток прямогонной дизельной фракции по трубопро- воду подается в ректификационную колонну для разделения дизельного топли- ва на легкую и тяжелую фракции. Легкая фракция дизельного топлива по тру- бопроводу отводится в первый реактор, который заполнен катализатором, при этом, легкая фракция объединяется с потоком водородосодержащего газа (ВСГ), поступающего на установку по трубопроводу. Тяжелая фракция дизель- ного топлива из нижней части ректификационной колонны отводится во вто- рой реактор, также объединяясь с ВСГ.
Прямогонное дизельное топливо фракционируют на легкую и тяжелую фракции на установке первичной переработки, выводя легкую и тяжелую
фракции боковыми погонами из ректификационной колонны с дальнейшей их раздельной подачей на установку гидроочистки, для сокращения энергетиче-
ских и капитальных затрат на подготовку сырья гидроочистки для каждого из реакторов (рисунок 1.1).
I, II – реактор; III – сепаратор; IV – ректификационная колонна; 1-11 - трубопроводы
Рисунок 1.2 –Установка гидроочистки дизельного топлива [10]
Сырьевой поток прямогонной дизельной фракции, поступающий с уста- новки первичной переработки, по трубопроводу 1 подается в ректификацион- ную колонну IV для разделения на легкую и тяжелую фракции дизельно- го топлива с границей деления, определенной путем покомпонентного анализа количества индивидуальных сераорганических соединений исходного сырья. Легкая фракция дизельного топлива из верхней части ректификационной ко- лонны IV по трубопроводу 3 отводится в первый реактор I, заполненный ката- лизатором гидроочистки, объединяясь при этом с потоком водородсодержаще- го газа (ВСГ), поступающим на установку по трубопроводу 2. Тяжелая фрак- ция дизельного топлива из нижней части ректификационной колонны IV по трубопроводу 4 отводится во второй реактор II, заполненный катализато- ром гидроочистки, также объединяясь при этом с потоком ВСГ, поступающим на установку по трубопроводу 2. Реакционный процесс осуществляют при тем- пературе 280-400 °С и давлении 4-6 МПа в избытке ВСГ 300-700 нм3/м3 с объ- емной скоростью подачи сырья 1,5-6,0 ч-1.
Недостатком способа является необходимость двукратного фракциони-
рования дизельного топлива на установке первичной переработки нефти и на установке гидроочистки, что увеличивает энергозатраты на подготовку сы- рья гидроочистки, а также жесткая граница деления легкой
и тяжелой фрак- ций дизельного топлива ,не позволяющая учитывать реальное распределение сераорганических соединений (моноциклических сульфидов и тиофенов, би- циклических тиофенов и сопутствующих им сульфидов), которые имеют раз- личные константы скоростей гидрообессеривания, что приводит к различному времени реакции для достижения необходимой глубины очист- ки дизельного топлива в целом.
В патенте [11] предлагается более эффективная установка, позволяющая получить бензин, керосин, а также малосернистое дизельное топливо с высоким выходом продукта, но при более низком давлении водорода, а также обеспе- чить большую степень обессеривания конечного продукта.
Реакция гидрогенизации проводится в три стадии. Первая стадия - это стадия глубокого обессеривания, протекающая в двух последовательно уста- новленных реакторах. Вторая стадия - депарафинизация - процесс, направлен- ный на удаление нормальных парафиновых углеводородов из керосино- газойлевых и масляных фракций нефти. Третья стадия - гидрирование олифи- нов и образование меркаптанов, в результате протекания побочных реакций в верхней части третьего реактора – депарафинизации и гидроочистки.
Результат обеспечивается тем, что в установке для получения моторных топлив, включающей в себя последовательно установленные реакторы гидро- генизации, сепараторы, колонну стабилизации гидрогенизата и ректификаци- онную колонну, а они, в свою очередь, связаны между собой трубопроводами, установленными между реакторами гидрогенизации и сепараторами использу- ются совмещенные реактор депарафинизации и гидроочискти.
Для обеспечения более высокое разделение моторных топлив и углеводо- родных газов, использользуется совокупность колонны стабилизации и слож- ной ректификационной колонны с боковыми отборами, чтобы в колонне стаби- лизации через печь рециркулировал стабильный гидрогенизат
из кубовой части
колонны.
На рисунке 1.2. представлена схема установки.
1 - деаэратор; 2 – теплообменник; 3 – реактор гидрогенизации (реактор А); 4 – реактор гидрогенизации (реактор В); 5 – совмещенный реактор депарафинизации и гидроочистки (реактор С); 6 – система подачи
квенч-водородосодержащего газа; 7 – печь; 8 – сепаратор; 9 – колонна стабилизации; 10 – конденсатор-холодильник; 11 – сепаратор; 12 – печь; 13 – колонна ректификации; 14 – печь
Рисунок 1.2 – Установки для получения моторных топлив [11]
Процесс реализуется так. В деаэраторе 1 происходит отдув водосодержа- щим газом, который поддается со щита сброса, растворенного в сырье кислоро- да, из-за которого образуются твердые отложения в теплообменной аппаратуре. Газосырьевая смесь поступает в теплообменник 2, где нагревается при помощи тепла газопродуктовой смеси, затем догревается в печи 7 до нужной температу- ры , после чего поступает в последовательно соединенные реактора гидрогени- зации 3 и 4, а также гидродепарафинизации 5.
В реакторах А и В на катализаторе гидроочистки происходит гидрирова- ние соединений, которые содержат серу, азот, кислород с образованием аммиа- ка, воды и сероводорода. Между первым и вторым реакторами предусмотрена установка подачи системы квенч-водородосодержащего газа 6 с нагнетания
компрессора. Для регулирования температуры на входе в реактор С предусмот- рено охлаждение газосырьевой смеси подачей квенча между реакторами А и В, если температура на входе в реактор С слишком высокая или нагрев в печи 7, а также если температура на выходе из реактора В недостаточно высокая для процесса депарафинизации. Так как в реакторе депарафинизации 5 образуются олефины, которые могут взаимодействовать с сероводородом с получением меркаптанов ,в нижнюю часть реактора С засыпается катализатор
гидроочист- ки для удаления олефинов и образовавшихся сернистых соединений. Газопро- дуктовая смесь из реактора С отдает тепло на нагрев газосырьевой смеси в теп- лообменник 2 и поступает в сепаратор 8 , где разделяется на парогазовую смесь и нестабильный гидрогенизат. Он, в свою очередь, отправляется на смешение с бензином-отгоном со смежных установок гидроочистки и далее в колонну ста- билизации 9. В колонне 9 происходит стабилизация гидрогенизата с выделени- ем из него растворенных легких углеводородов, влаги и сероводорода. Легкие углеводороды из верхней части колонны 9 конденсируются и охлаждаются в конденсаторе-холодильнике 10 соответственно и поступают в сепаратор 11, где происходит их разделение на углеводородный газ и легкий бензин. Легкий бен- зин из сепаратора 11 насосами подается на орошение колонны 9, а балансовое количество выводится с установки. Стабильный гидрогенизат из нижней части колонны 9 под собственным давлением нагревается в печи 12 и поступает в ко- лонну ректификации 13. В сложной колонне ректификации 13 происходит раз- деление стабильного гидрогенизата на следующие фракции: бензин, керосин 180-240 °C, дизельная фракция 240-340 °C и фракция, выкипающая при темпе- ратуре более 340 °C.
Установка позволяет получать экологически чистые моторные топлива, соответствующие нормам Евро-5, с выходом около 96%, что существенно пре- вышает результаты, получаемые при использовании аналогичных промышлен- но используемых установок.
В патенте [12] описан способ, позволяющий повысить степень очистки дизельного топлива. Задачей изобретения является создание эффективного спо-
соба очистки моторных топлив, включающего экстракцию серосодержащих со- единений из топлива в ионную жидкость, их парциальное окисление под дей- ствием катализатора и достижение, таким образом, более полного удаления се- росодержащих органических веществ.
Авторы патента [13] предлагают способ удаления сера- и азотсодержащих соединений из углеводородов с использованием ИЖ
тивность свежего катализатора не достигает максимальной величины, катализа- тор активируют в течение нескольких часов при температуре более 500 ºС. Со временем активность катализатора падает за счет отложений кокса на поверх- ности катализатора. Для восстановления активности катализатор подвергается паровоздушной регенерации.
-
Патентный обзор
Гидроочистка дизельного топлива осуществляется целым комплексом оборудования и часто состоит из нескольких стадий. Совершенствование уста- новки гидроочистки в большинстве случаев сводится к совершенствованию ре- актора гидроочистки.
Рассмотрим различные способы гидроочистки дизельного топлива то нежелательных примесей - серы, азота, металлов, кислорода.
В патенте [10] описан способ гидроочистки дизельного топлива. Задача данного способа - снизить энергозатраты на подготовку сырья гидроочистки, а также сформировать оптимальной границы деления исходного сырья на легкую и тяжелую фракции с уменьшением объема катализатора в реакторах.
Сначала сырьевой поток прямогонной дизельной фракции по трубопро- воду подается в ректификационную колонну для разделения дизельного топли- ва на легкую и тяжелую фракции. Легкая фракция дизельного топлива по тру- бопроводу отводится в первый реактор, который заполнен катализатором, при этом, легкая фракция объединяется с потоком водородосодержащего газа (ВСГ), поступающего на установку по трубопроводу. Тяжелая фракция дизель- ного топлива из нижней части ректификационной колонны отводится во вто- рой реактор, также объединяясь с ВСГ.
Прямогонное дизельное топливо фракционируют на легкую и тяжелую фракции на установке первичной переработки, выводя легкую и тяжелую
фракции боковыми погонами из ректификационной колонны с дальнейшей их раздельной подачей на установку гидроочистки, для сокращения энергетиче-
ских и капитальных затрат на подготовку сырья гидроочистки для каждого из реакторов (рисунок 1.1).
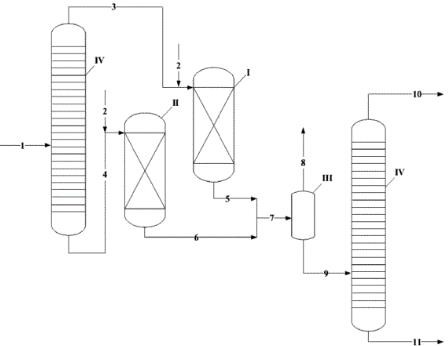
I, II – реактор; III – сепаратор; IV – ректификационная колонна; 1-11 - трубопроводы
Рисунок 1.2 –Установка гидроочистки дизельного топлива [10]
Сырьевой поток прямогонной дизельной фракции, поступающий с уста- новки первичной переработки, по трубопроводу 1 подается в ректификацион- ную колонну IV для разделения на легкую и тяжелую фракции дизельно- го топлива с границей деления, определенной путем покомпонентного анализа количества индивидуальных сераорганических соединений исходного сырья. Легкая фракция дизельного топлива из верхней части ректификационной ко- лонны IV по трубопроводу 3 отводится в первый реактор I, заполненный ката- лизатором гидроочистки, объединяясь при этом с потоком водородсодержаще- го газа (ВСГ), поступающим на установку по трубопроводу 2. Тяжелая фрак- ция дизельного топлива из нижней части ректификационной колонны IV по трубопроводу 4 отводится во второй реактор II, заполненный катализато- ром гидроочистки, также объединяясь при этом с потоком ВСГ, поступающим на установку по трубопроводу 2. Реакционный процесс осуществляют при тем- пературе 280-400 °С и давлении 4-6 МПа в избытке ВСГ 300-700 нм3/м3 с объ- емной скоростью подачи сырья 1,5-6,0 ч-1.
Недостатком способа является необходимость двукратного фракциони-
рования дизельного топлива на установке первичной переработки нефти и на установке гидроочистки, что увеличивает энергозатраты на подготовку сы- рья гидроочистки, а также жесткая граница деления легкой
и тяжелой фрак- ций дизельного топлива ,не позволяющая учитывать реальное распределение сераорганических соединений (моноциклических сульфидов и тиофенов, би- циклических тиофенов и сопутствующих им сульфидов), которые имеют раз- личные константы скоростей гидрообессеривания, что приводит к различному времени реакции для достижения необходимой глубины очист- ки дизельного топлива в целом.
В патенте [11] предлагается более эффективная установка, позволяющая получить бензин, керосин, а также малосернистое дизельное топливо с высоким выходом продукта, но при более низком давлении водорода, а также обеспе- чить большую степень обессеривания конечного продукта.
Реакция гидрогенизации проводится в три стадии. Первая стадия - это стадия глубокого обессеривания, протекающая в двух последовательно уста- новленных реакторах. Вторая стадия - депарафинизация - процесс, направлен- ный на удаление нормальных парафиновых углеводородов из керосино- газойлевых и масляных фракций нефти. Третья стадия - гидрирование олифи- нов и образование меркаптанов, в результате протекания побочных реакций в верхней части третьего реактора – депарафинизации и гидроочистки.
Результат обеспечивается тем, что в установке для получения моторных топлив, включающей в себя последовательно установленные реакторы гидро- генизации, сепараторы, колонну стабилизации гидрогенизата и ректификаци- онную колонну, а они, в свою очередь, связаны между собой трубопроводами, установленными между реакторами гидрогенизации и сепараторами использу- ются совмещенные реактор депарафинизации и гидроочискти.
Для обеспечения более высокое разделение моторных топлив и углеводо- родных газов, использользуется совокупность колонны стабилизации и слож- ной ректификационной колонны с боковыми отборами, чтобы в колонне стаби- лизации через печь рециркулировал стабильный гидрогенизат
из кубовой части
колонны.
На рисунке 1.2. представлена схема установки.
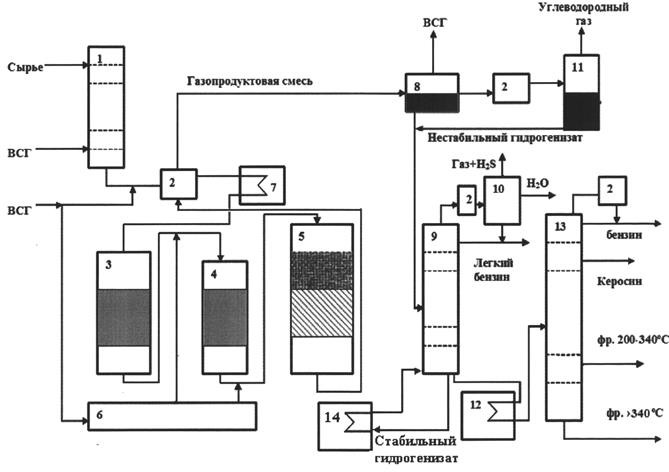
1 - деаэратор; 2 – теплообменник; 3 – реактор гидрогенизации (реактор А); 4 – реактор гидрогенизации (реактор В); 5 – совмещенный реактор депарафинизации и гидроочистки (реактор С); 6 – система подачи
квенч-водородосодержащего газа; 7 – печь; 8 – сепаратор; 9 – колонна стабилизации; 10 – конденсатор-холодильник; 11 – сепаратор; 12 – печь; 13 – колонна ректификации; 14 – печь
Рисунок 1.2 – Установки для получения моторных топлив [11]
Процесс реализуется так. В деаэраторе 1 происходит отдув водосодержа- щим газом, который поддается со щита сброса, растворенного в сырье кислоро- да, из-за которого образуются твердые отложения в теплообменной аппаратуре. Газосырьевая смесь поступает в теплообменник 2, где нагревается при помощи тепла газопродуктовой смеси, затем догревается в печи 7 до нужной температу- ры , после чего поступает в последовательно соединенные реактора гидрогени- зации 3 и 4, а также гидродепарафинизации 5.
В реакторах А и В на катализаторе гидроочистки происходит гидрирова- ние соединений, которые содержат серу, азот, кислород с образованием аммиа- ка, воды и сероводорода. Между первым и вторым реакторами предусмотрена установка подачи системы квенч-водородосодержащего газа 6 с нагнетания
компрессора. Для регулирования температуры на входе в реактор С предусмот- рено охлаждение газосырьевой смеси подачей квенча между реакторами А и В, если температура на входе в реактор С слишком высокая или нагрев в печи 7, а также если температура на выходе из реактора В недостаточно высокая для процесса депарафинизации. Так как в реакторе депарафинизации 5 образуются олефины, которые могут взаимодействовать с сероводородом с получением меркаптанов ,в нижнюю часть реактора С засыпается катализатор
гидроочист- ки для удаления олефинов и образовавшихся сернистых соединений. Газопро- дуктовая смесь из реактора С отдает тепло на нагрев газосырьевой смеси в теп- лообменник 2 и поступает в сепаратор 8 , где разделяется на парогазовую смесь и нестабильный гидрогенизат. Он, в свою очередь, отправляется на смешение с бензином-отгоном со смежных установок гидроочистки и далее в колонну ста- билизации 9. В колонне 9 происходит стабилизация гидрогенизата с выделени- ем из него растворенных легких углеводородов, влаги и сероводорода. Легкие углеводороды из верхней части колонны 9 конденсируются и охлаждаются в конденсаторе-холодильнике 10 соответственно и поступают в сепаратор 11, где происходит их разделение на углеводородный газ и легкий бензин. Легкий бен- зин из сепаратора 11 насосами подается на орошение колонны 9, а балансовое количество выводится с установки. Стабильный гидрогенизат из нижней части колонны 9 под собственным давлением нагревается в печи 12 и поступает в ко- лонну ректификации 13. В сложной колонне ректификации 13 происходит раз- деление стабильного гидрогенизата на следующие фракции: бензин, керосин 180-240 °C, дизельная фракция 240-340 °C и фракция, выкипающая при темпе- ратуре более 340 °C.
Установка позволяет получать экологически чистые моторные топлива, соответствующие нормам Евро-5, с выходом около 96%, что существенно пре- вышает результаты, получаемые при использовании аналогичных промышлен- но используемых установок.
В патенте [12] описан способ, позволяющий повысить степень очистки дизельного топлива. Задачей изобретения является создание эффективного спо-
соба очистки моторных топлив, включающего экстракцию серосодержащих со- единений из топлива в ионную жидкость, их парциальное окисление под дей- ствием катализатора и достижение, таким образом, более полного удаления се- росодержащих органических веществ.
Авторы патента [13] предлагают способ удаления сера- и азотсодержащих соединений из углеводородов с использованием ИЖ