ВУЗ: Не указан
Категория: Не указан
Дисциплина: Не указана
Добавлен: 24.10.2023
Просмотров: 125
Скачиваний: 4
ВНИМАНИЕ! Если данный файл нарушает Ваши авторские права, то обязательно сообщите нам.
общей формулы К+А. А" выбирают из галогенидов, нитрата, сульфата, фосфата, ацетата, тетрафтор- бората, гексафторфосфата, трифторацетата, трифлата, сульфониламида и др. К+выбирают из фосфония, аммония, сульфония, моно-, ди- и тетразамещённых на алкильный радикал с содержанием С от 1 до 30 атомов, например, бутилпи- ридиния, этилпиридиния, пиридиния, этилметилимидазолия, бутилметилими- дазолия, метилметилимидазолия и пр. Метод основан на удалении сера- и азот- содержащих соединений из углеводородной фазы в ИЖ с последующим разде- лением двухфазной системы декантацией и регенерацией ИЖ. Оптимизацию процесса осуществляют подбором времени, температуры, добавлением алкили- рующего агента общей формулы RX. R выбирают из радикалов алкил-, алкен-, арен-. X идентичен аниону ИЖ.
Данный способ применим для удаления меркаптанов, бензотиофенов, ди- бензотиофенов. Оптимизация позволяет повысить степень извлечения бутан- диола с 7,7% до 99%.
Недостатками данного способа являются использование инертной атмо- сферы (аргона) и длительность (до 10 часов). На основании примеров описыва- ется извлечение только бутандиола, и невозможно сделать однозначные выво- ды об эффективности заявленного способа для удаления остальных серасодер- жащих соединений.
В статье [14] рассматриваются различные современные технологии углубления переработки нефти и получения высококачественных топлив и пришли к выводу, что для рационального решения проблемы производства низкозастывающих сортов дизельных топлив целесообразно внедрение процес- са гидродепарафинизации, совмещенного с процессом гидроочистки.
Предлагается проводить процесс гидроочистки совместно с процессом гидродепарафинизации, совместно с включением в себя установку дополни- тельного реактора последовательно к существующему реактору гидроочистки и реконструкцию блока стабилизации, так как процесс гидродепарафинизации связан с гораздо более высоким выходом углеводородного газа и бензина. Эти
легкие продукты могут вносить большой положительный вклад в улучшение экономики работы и в более полное использование предприятием нефтяного сырья. Ключевым элементом любого каталитического процесса является ис- пользуемый в нем катализатор и связанная с ним технология. Поэтому очень важен правильный выбор оптимального катализатора и современной техноло- гии с тем, чтобы обеспечить эффективную работу процесса с самого начала эксплуатации.
Реакции гидрирования прямогонных фракций протекают с незначитель- ным тепловым эффектом, в результате чего температура на выходе из реактора может повышаться на 10–20 °С. Экзотермическое тепло реакции используется в продуктовых теплообменниках для повышения эффективности установки и увеличения срока службы катализаторов. После охлаждения происходят разде- ление газопродуктовой смеси в сепараторе высокого давления на циркулирую- щий ВСГ и нестабильный гидрогенизат и отстаивание кислой воды. Циркуля- ционный ВСГ очищается от сероводорода водным раствором амина. Жидкий продукт после сепарации ВСГ поступает в колонну стабилизации. В колонне происходят стабилизация гидрогенизата с выделением из него растворенных сероводорода, легких углеводородов и влаги и разделение стабильного гидро- генизата на боковой погон и стабильную дизельную фракцию. Стабильное гид- роочищенное дизельное топливо и бензин-отгон выводятся с установки. Угле- водородные газы, пройдя блок очистки раствором амина, направляются в топ- ливную сеть установки.
Таким образом, данный способ позволяет производить высококачествен- ные дизельные топлива с необходимыми показателями низкотемпературных свойств, а также выполнять экологические требования по содержанию серы в
товарных нефтепродуктах.
В патенте [15] предлагается комбинированный процесс гидроочистки, это позволяет получить более чистое дизельное топливо путем установки трех ре- акторов (рисунок 1.3).
1 – первый реактор гидроочистки первого вида нефтяного сырья; 2 – второй реактор для второго вида нефтяного сырья; 3 – реактор совместной гидро-
очистки гидрогенизатов; 4 – сепаратор высокого давления; 5 – сепаратор низкого давления; 6 – ректификационная колонна стабилизации гидрогенизата; 7 – гидроочищенного продукта и циркулирующего газа
Рисунок 1.3 – Принципиальная схема гидроочистки нефтяного сырья [15]
Установка имеет три реактора: первый реактор - реактор гидроочистки первого нефтяного сырья, второй реактор - гидроочистка второго вида нефтя- ного сырья и третий реактор гидроочистки. Также установка включает в себя сепараторы высокого и низкого давления, ректификационную колонну, систему промывки от сероводорода, где третий реактор последовательно соединен с первым и вторым. В последнем реакторе происходит доочистка сырья. Комби- нированный способ позволяет получить более качественное топливо из-за мно- гоэтапности очистки.
Усовершенствование способа гидроочистки дизельного топлива в совре- менном мире очень актуальна, так как в современной нефтепереработке широко применяются различные модификации гидрогенизационных процессов: гидро- очистки, гидрокрекинга, гидродеалкилирования, гидрирования и гидроизоме-
ризации. В РФ из гидрогенизационных процессов наиболее распространена
именно гидроочистка.
Наиболее сложным оборудованием и аппаратурой оснащены реакторные блоки гидроочистки и риформинга, в которых наиболее важными аппаратами являются реакторы, а также многокамерные печи.
На рисунке 1.4 представлены схемы реакторов для проведения гетеро- генно-каталитических процессов с неподвижным слоем катализатора.
И – исходные вещества, П – продукты, Х – теплоноситель, Т- топливо, В
– воздух, ДГ – дымовые газы
Рисунок 1.4 – Схемы реакторов для гетерогенно-каталитических процессов с
неподвижным слоем катализатора
Особенностью работы оборудования и аппаратуры реакторных блоков являются высокие температура и давление, а также присутствие водорода при жестком режиме.
Реактор гидроочистки обычно представляет собой цилиндрический вер- тикальный сосуд с шаровыми днищами. При 525 °С и 2 – 4 МПа водород спо- собствует водородной коррозии металла, вызывающей его трещины и вздутия. Поэтому и для теплоизоляции изнутри металлическую стенку реактора защи- щают футеровкой из торкретбетона. Кроме того, внутри реактора устанавлива- ют стальной перфорированный стакан, между стенкой которого и стенкой ап- парата имеется газовый слой. Нарушение футеровки приводит к перегреву и разрушению стенки реактора. Поэтому необходимо постоянно контролировать при помощи наружных термопар температуру внешней поверхности металла (должна быть не более 150 °С). Для изготовления корпуса и днища реактора применяют сталь марки 09Г2ДТ со специальной закалкой поверхности аппара- та или сталь 12ХМ. Внутренняя арматура реактора и присоединительные фа- сонные патрубки изготовлены из легированных сталей.
На первых установках применяли реакторы с аксиальным (вдоль оси аппарата) движением газосырьевого потока (рисунок 1.5). Катализатор загру- жают в аппараты через верхний штуцер и выгружают через нижний. Каждый аппарат оборудован штуцерами для выхода паров при эжектировании системы во время регенерации катализатора. В связи с большим перепадом давления (1,3 - 1,5 МПа) в реакторах с аксиальным движением потока в последнее время стали применять реакторы с радиальным движением газосырьевого потока (ре- акционная смесь движется в реакторе через слой катализатора в радиальном направлении, а катализатор - вертикально).
Реакторы такого типа характеризуются малым гидравлическим сопро- тивлением (не более 0,8 МПа). Даже при большом отношении высоты к диа- метру можно обеспечить равномерное распределение катализатора при мини- муме внутренних устройств, так что истирание катализатора очень мало. По- этому старые реакторы переоборудуют с
аксиального ввода на радиальный, а
новые изготавливают только с радиальным вводом (рисунок 1.6).
На вновь проектируемых и строящихся установках корпус и днища ре- акторов выполняют из двухслойной стали (12ХМ+0Х18Н10Т), поэтому они не нуждаются в защитной футеровке.
1 - зональная термопара; 2 - наружная термопара; 3 - футеровка; 4 -корпус;
5 -фарфоровые шары
Линии: I - сырье; II - продукты реакции; III - выгрузка катализатора; IV -вывод продуктов при во время регенерации катализатора
Рисунок 1.5 - Схемы каталитического реактора с аксиальным вводом
газосырьевой смеси
Катализатор размещается в стальном стакане реактора сплошным слоем. Над и под слоем находятся фарфоровые шарики диаметром 16 или 24 мм для предотвращения уноса катализатора. Нижний слой фарфоровых шариков лежит
на решетке дополнительно перекрытой металлической сеткой. Шары решетка и сетка защищают выходной штуцер реактора от попадания в него катализатора вместе с продуктами реакции. Внутри детали реактора выполняются из хромо- никелевой стали.
1 - корпус; 2 - футеровка; 3 - кожух
Данный способ применим для удаления меркаптанов, бензотиофенов, ди- бензотиофенов. Оптимизация позволяет повысить степень извлечения бутан- диола с 7,7% до 99%.
Недостатками данного способа являются использование инертной атмо- сферы (аргона) и длительность (до 10 часов). На основании примеров описыва- ется извлечение только бутандиола, и невозможно сделать однозначные выво- ды об эффективности заявленного способа для удаления остальных серасодер- жащих соединений.
В статье [14] рассматриваются различные современные технологии углубления переработки нефти и получения высококачественных топлив и пришли к выводу, что для рационального решения проблемы производства низкозастывающих сортов дизельных топлив целесообразно внедрение процес- са гидродепарафинизации, совмещенного с процессом гидроочистки.
Предлагается проводить процесс гидроочистки совместно с процессом гидродепарафинизации, совместно с включением в себя установку дополни- тельного реактора последовательно к существующему реактору гидроочистки и реконструкцию блока стабилизации, так как процесс гидродепарафинизации связан с гораздо более высоким выходом углеводородного газа и бензина. Эти
легкие продукты могут вносить большой положительный вклад в улучшение экономики работы и в более полное использование предприятием нефтяного сырья. Ключевым элементом любого каталитического процесса является ис- пользуемый в нем катализатор и связанная с ним технология. Поэтому очень важен правильный выбор оптимального катализатора и современной техноло- гии с тем, чтобы обеспечить эффективную работу процесса с самого начала эксплуатации.
Реакции гидрирования прямогонных фракций протекают с незначитель- ным тепловым эффектом, в результате чего температура на выходе из реактора может повышаться на 10–20 °С. Экзотермическое тепло реакции используется в продуктовых теплообменниках для повышения эффективности установки и увеличения срока службы катализаторов. После охлаждения происходят разде- ление газопродуктовой смеси в сепараторе высокого давления на циркулирую- щий ВСГ и нестабильный гидрогенизат и отстаивание кислой воды. Циркуля- ционный ВСГ очищается от сероводорода водным раствором амина. Жидкий продукт после сепарации ВСГ поступает в колонну стабилизации. В колонне происходят стабилизация гидрогенизата с выделением из него растворенных сероводорода, легких углеводородов и влаги и разделение стабильного гидро- генизата на боковой погон и стабильную дизельную фракцию. Стабильное гид- роочищенное дизельное топливо и бензин-отгон выводятся с установки. Угле- водородные газы, пройдя блок очистки раствором амина, направляются в топ- ливную сеть установки.
Таким образом, данный способ позволяет производить высококачествен- ные дизельные топлива с необходимыми показателями низкотемпературных свойств, а также выполнять экологические требования по содержанию серы в
товарных нефтепродуктах.
В патенте [15] предлагается комбинированный процесс гидроочистки, это позволяет получить более чистое дизельное топливо путем установки трех ре- акторов (рисунок 1.3).
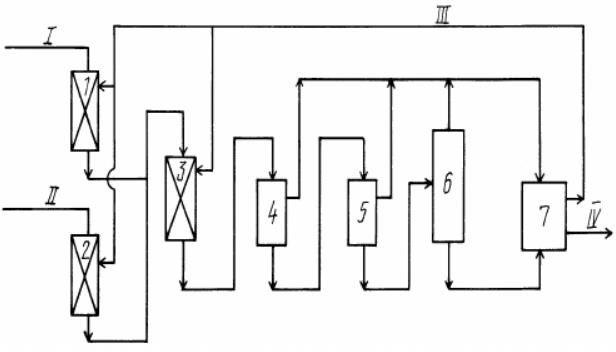
1 – первый реактор гидроочистки первого вида нефтяного сырья; 2 – второй реактор для второго вида нефтяного сырья; 3 – реактор совместной гидро-
очистки гидрогенизатов; 4 – сепаратор высокого давления; 5 – сепаратор низкого давления; 6 – ректификационная колонна стабилизации гидрогенизата; 7 – гидроочищенного продукта и циркулирующего газа
Рисунок 1.3 – Принципиальная схема гидроочистки нефтяного сырья [15]
Установка имеет три реактора: первый реактор - реактор гидроочистки первого нефтяного сырья, второй реактор - гидроочистка второго вида нефтя- ного сырья и третий реактор гидроочистки. Также установка включает в себя сепараторы высокого и низкого давления, ректификационную колонну, систему промывки от сероводорода, где третий реактор последовательно соединен с первым и вторым. В последнем реакторе происходит доочистка сырья. Комби- нированный способ позволяет получить более качественное топливо из-за мно- гоэтапности очистки.
Усовершенствование способа гидроочистки дизельного топлива в совре- менном мире очень актуальна, так как в современной нефтепереработке широко применяются различные модификации гидрогенизационных процессов: гидро- очистки, гидрокрекинга, гидродеалкилирования, гидрирования и гидроизоме-
ризации. В РФ из гидрогенизационных процессов наиболее распространена
именно гидроочистка.
Наиболее сложным оборудованием и аппаратурой оснащены реакторные блоки гидроочистки и риформинга, в которых наиболее важными аппаратами являются реакторы, а также многокамерные печи.
На рисунке 1.4 представлены схемы реакторов для проведения гетеро- генно-каталитических процессов с неподвижным слоем катализатора.
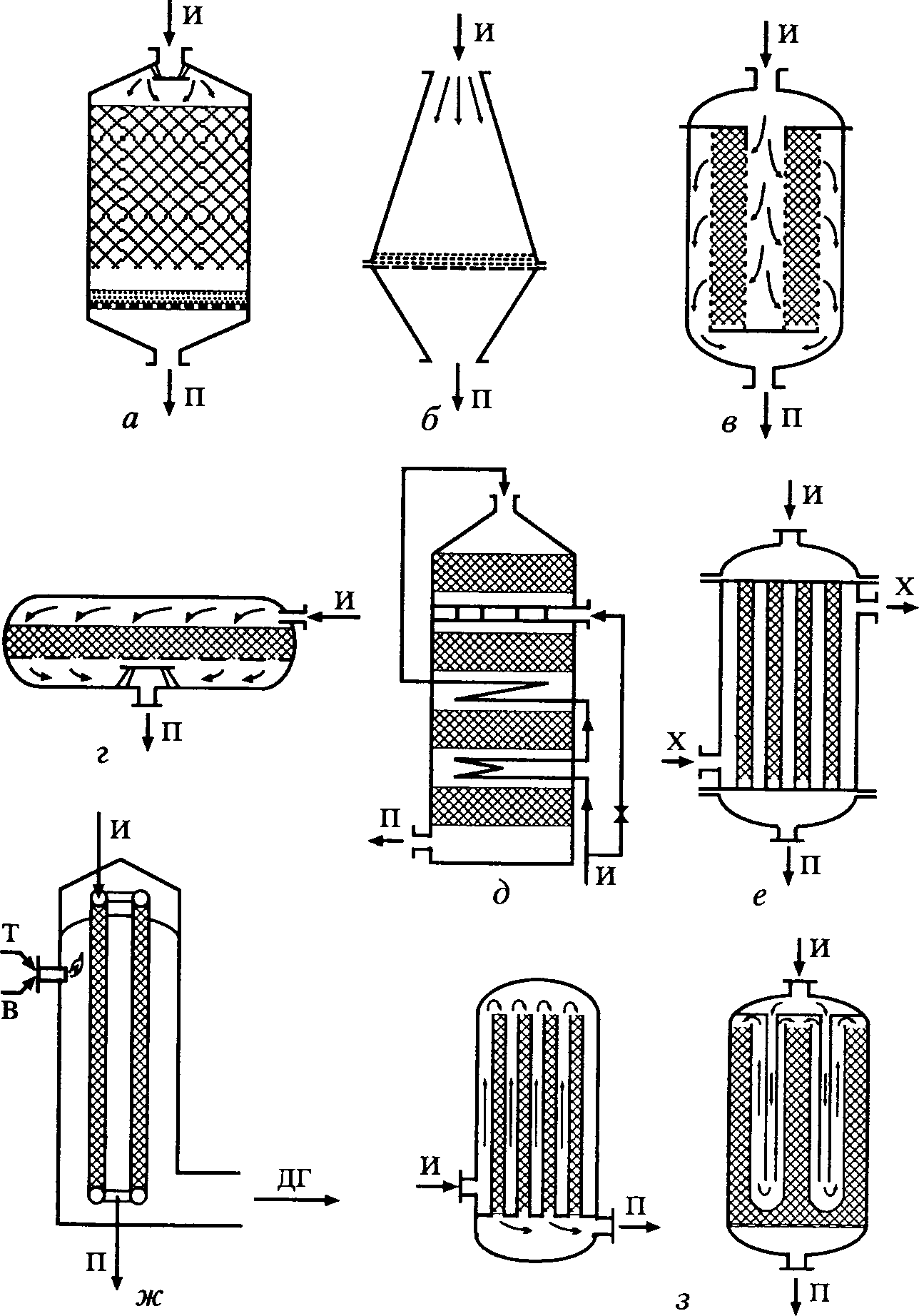
И – исходные вещества, П – продукты, Х – теплоноситель, Т- топливо, В
– воздух, ДГ – дымовые газы
Рисунок 1.4 – Схемы реакторов для гетерогенно-каталитических процессов с
неподвижным слоем катализатора
Особенностью работы оборудования и аппаратуры реакторных блоков являются высокие температура и давление, а также присутствие водорода при жестком режиме.
Реактор гидроочистки обычно представляет собой цилиндрический вер- тикальный сосуд с шаровыми днищами. При 525 °С и 2 – 4 МПа водород спо- собствует водородной коррозии металла, вызывающей его трещины и вздутия. Поэтому и для теплоизоляции изнутри металлическую стенку реактора защи- щают футеровкой из торкретбетона. Кроме того, внутри реактора устанавлива- ют стальной перфорированный стакан, между стенкой которого и стенкой ап- парата имеется газовый слой. Нарушение футеровки приводит к перегреву и разрушению стенки реактора. Поэтому необходимо постоянно контролировать при помощи наружных термопар температуру внешней поверхности металла (должна быть не более 150 °С). Для изготовления корпуса и днища реактора применяют сталь марки 09Г2ДТ со специальной закалкой поверхности аппара- та или сталь 12ХМ. Внутренняя арматура реактора и присоединительные фа- сонные патрубки изготовлены из легированных сталей.
На первых установках применяли реакторы с аксиальным (вдоль оси аппарата) движением газосырьевого потока (рисунок 1.5). Катализатор загру- жают в аппараты через верхний штуцер и выгружают через нижний. Каждый аппарат оборудован штуцерами для выхода паров при эжектировании системы во время регенерации катализатора. В связи с большим перепадом давления (1,3 - 1,5 МПа) в реакторах с аксиальным движением потока в последнее время стали применять реакторы с радиальным движением газосырьевого потока (ре- акционная смесь движется в реакторе через слой катализатора в радиальном направлении, а катализатор - вертикально).
Реакторы такого типа характеризуются малым гидравлическим сопро- тивлением (не более 0,8 МПа). Даже при большом отношении высоты к диа- метру можно обеспечить равномерное распределение катализатора при мини- муме внутренних устройств, так что истирание катализатора очень мало. По- этому старые реакторы переоборудуют с
аксиального ввода на радиальный, а
новые изготавливают только с радиальным вводом (рисунок 1.6).
На вновь проектируемых и строящихся установках корпус и днища ре- акторов выполняют из двухслойной стали (12ХМ+0Х18Н10Т), поэтому они не нуждаются в защитной футеровке.
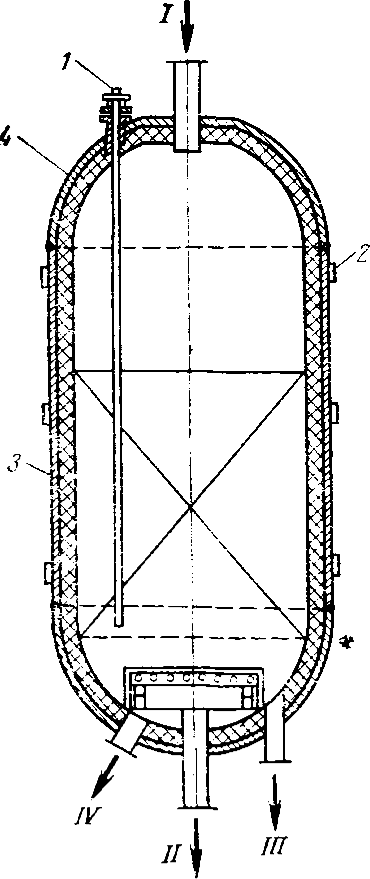
1 - зональная термопара; 2 - наружная термопара; 3 - футеровка; 4 -корпус;
5 -фарфоровые шары
Линии: I - сырье; II - продукты реакции; III - выгрузка катализатора; IV -вывод продуктов при во время регенерации катализатора
Рисунок 1.5 - Схемы каталитического реактора с аксиальным вводом
газосырьевой смеси
Катализатор размещается в стальном стакане реактора сплошным слоем. Над и под слоем находятся фарфоровые шарики диаметром 16 или 24 мм для предотвращения уноса катализатора. Нижний слой фарфоровых шариков лежит
на решетке дополнительно перекрытой металлической сеткой. Шары решетка и сетка защищают выходной штуцер реактора от попадания в него катализатора вместе с продуктами реакции. Внутри детали реактора выполняются из хромо- никелевой стали.
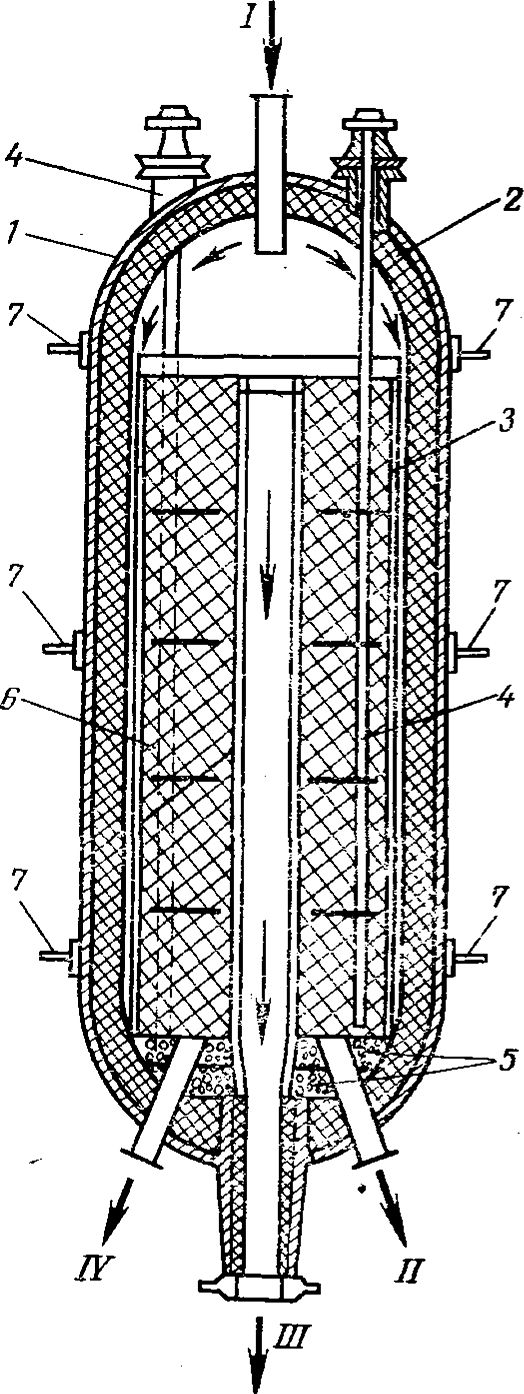
1 - корпус; 2 - футеровка; 3 - кожух