ВУЗ: Не указан
Категория: Не указан
Дисциплина: Не указана
Добавлен: 06.11.2023
Просмотров: 423
Скачиваний: 3
ВНИМАНИЕ! Если данный файл нарушает Ваши авторские права, то обязательно сообщите нам.
СОДЕРЖАНИЕ
Рисунок 4 – Схема закрепления кольца с некруглой
Рисунок 17--Схема образования погрешности закрепления
Поэтому и для технологической системы необходимо, чтобы
3.5.3 Задание к лабораторной работе
3.5.5 Методика и порядок выполнения лабораторной работы
4. Проников А.С. Надёжность машин. М. Маш. 1978. 591с.
5. Когаев В.П., Дроздов Ю.Н. прочность и износостойкость деталей машин. М. ВШ.1991.319с.
6. Аристов А.В. управление качеством. М. Инфра М. 2000. 238с.
3.6.2.2 Погрешности, связанные с тепловыми деформациями технологических систем
С имеет рассеяние прежде всего из-за колебаний твердости и шероховатости поверхностных слоев заготовки. Предельное рассеяние значение коэффициента С определяют по специальным формулам. Значение коэффициентов и показателей степеней содержится в справочной литературе.
Связь погрешности закрепления и точности размера показана на рисунке 17. Фрезерный станок предварительно настроен на размер С для выдерживания размера Н. После приложения к заготовке сил закрепления Q она переместится на величину
и измерительная база 1–2 займет новое положение. Так возникает погрешность закрепления.
Погрешностью закрепления
называется разность предельных положений измерительной базы относительно настроенного на размер инструмента, возникающая при действии сил закрепления.
Силы закрепления вызывают также отклонения формы. На рисунке 18 показаны четыре фазы (I…IV) состояние заготовки типа
кольца, установленного в трехкулачковый патрон для растачивания отверстия.
На рисунке 17 на первой фазе заготовка не деформирована, на второй ― и наружная, и внутренняя поверхности деформированы силами Q. После растачивания отверстия (третья фаза) отклонений формы не наблюдается. Точности размера и формы отверстия могут быть весьма высокими. Наружная поверхность деформирована. После раскрепления кольца (четвертая фаза) точность отверстия нарушена (показано утрированно), а наружная поверхность восстановила свою форму.
Рисунок 18 – Погрешности формы, вызываемые силами закрепления
Рациональное базирование и закрепление заготовок позволяют существенно повысить точность деталей. На рисунке 19,a показана деталь, на которой необходимо фрезеровать уступ с размерами 35 и 10 мм, а на рисунке 19,б-д―различные схемы установки заготовки с применением призм и приспособления со втулкой. Если определить по соответствующим формулам погрешности базирования и закрепления (при прочих равных условиях), суммировать эти погрешности, то можно убедиться в том, что наибольшую погрешность даст схема установки, приведенная на рисунке 19,в, а наименьшую ― схема на рисунке 19,д. Для последней εб = 0, так как измерительная и технологическая базы совмещены. Точность размера 35-0,1 будет определяться только погрешностью закрепления, т.е. деформацией технологической базы. Схема на рисунке 19д оказывается точнее схемы на рисунке 19,в примерно в 40 раз.
Третья составляющая часть погрешности установки ― погрешность εП, вызываемая применением приспособлений. Ее учитывают каждый раз особо. Возникновение этой погрешности связано с неточностью изготовления приспособлений, их установкой на станке, износом опор от многократного контактирования с заготовками.
При установке приспособлений на станки возникают различные перекосы, установочные элементы занимают положения, не соответствующие заданным. Например, обычные трехкулачковые патроны при каждом закреплении на шпинделях станков занимают новые положения. Рассеяние положений происходит в пределах зазора между шейкой шпинделя и отверстием в патроне, так как ось вращения шпинделя и ось патрона не совпадают. В другом случае зажимные элементы приспособлений в процессе закрепления заготовок перекашиваются в пределах зазора в направляющих и при этом увлекают за собой заготовку. Заготовку закрепляют каждый раз в новом положении.
Рисунок 19 – Варианты выбора рациональной схемы базирования
и закрепления заготовки
Износ приспособлений и, прежде всего, их установочных элементов может оказать существенное влияние на точность установок. Элементы изнашиваются неравномерно.
Каждая из причин возникновения погрешностей, связанных с применением приспособлений, должна быть рассмотрена особо. Некоторые погрешности (например, перекос при установке приспособления) следует рассматривать как постоянные, действие которых одинаково для всех заготовок в партии, другие же имеют случайный характер (например, погрешность положения заготовок в процессе их закрепления).
Рассмотренные погрешности, как составные части погрешности установки, необходимо суммировать. Поскольку все они все имеют случайный характер, то суммировать их следует по закону теории вероятности. Погрешности необходимо рассматривать после рассеяния случайных величин, распределение которых в первом приближении подчиняется закону Гаусса. Тогда
Нужно стремиться к сокращению всех погрешностей, стоящих под знаком корня.
Наследственные связи не могут быть реализованы вне контактов заготовок как твердых тел с элементами технологических систем. В первую очередь, такими элементами являются технологические базы. В условиях, когда используется принцип постоянства технологических баз, что приводит к повышению точностных характеристик, проявление взаимодействия баз с заготовками сказывается особенно наглядно. Вазовые поверхности сами имеют погрешности. Контактирование заготовок с такими базами непременно влияет на характер наследования.
Технологические базы заготовок всегда имеют отклонения размера, формы и расположения поверхностей контакта с приспособлением или оборудованием. Эти отклонения наследуются на обрабатываемых поверхностях. Так, погрешность, возникшая, например, в начале технологического процесса, может устойчиво сохраняться вплоть до стадии эксплуатации детали. Особенно трудно бороться с малыми по величине отклонениями (погрешностями). Рассмотрим типовой пример.
Рисунок 20 – Схема наследования погрешностей технологических баз
Центровое отверстие ("гнездо" на деталях, например, типа валов (рисунок 20,а)) имеет номинально коническую форму и контактирует с конической формой центра, который играет роль приспособления. Однако детальное рассмотрение формы технологической базы ― центрового отверстия ― позволяет убедиться в том, что на его конической поверхности имеются характерные выступы (волны). Если посмотреть на центровое отверстие (рисунок 20,б), то наличие волн на уже контактировавшем с центром валу можно обнаружить по характерным блестящим полоскам. Чаще всего на центровых отверстиях наблюдают 2, 3 или 5 волн. Наиболее отчетливо эти волны можно зафиксировать с помощью кругломера.
Когда происходит обработка наружной поверхности вала методом шлифования и на заготовку действует сила постоянного направления, условия контакта выступов центрового отверстия и центра постоянно изменяются. Изменяется по углу поворота заготовки и жесткость сопряжения «центр-отверстие». В результате этого на наружной обрабатываемой поверхности возникает соответствующая волнистая поверхность (рисунок 20,в). Если на центровом отверстии были две волны, то и наружная поверхность детали также будет иметь две волны. При контакте центра станка с тремя выступами отверстия на обрабатываемой поверхности возникнет также три волны и т.д. Высота волн может быть малой и фиксируется при соответствующем увеличении на кругломере. Так, на финишной операции возникают погрешности, причина которых была создана еще на начальной операции центрования заготовок. Наследственная погрешность устойчиво сохранилась на протяжении всего технологического процесса.
Трудно себе представить элемент технологического процесса или технологическую операцию, где не проявлялось бы технологическое наследование. Закономерности наследования объективны. Практическое же их проявление отчетливо видно на стадии эксплуатации изделия. Это положение покажем на примере рисунка 21.
В корпусную деталь изделия поставлен стакан, в котором установлен подшипник качения (рисунок 21,а). Сила Р, действующая на вал и подшипник, вызывает упругое перемещение всего соединения. Такое перемещение зависит от величины приложенной силы. Картина нагружения показана на графике 1 (рисунок 21,б).
Рисунок 21 – Проявление технологической наследственности
в ходе эксплуатации изделий
Упругое перемещение элементов конструкции растет по мере возрастания силы Р. При силе Р=8000Н характер упругих перемещений изменяется и на графике наблюдается излом. В этом элементарном эксперименте ничего особенного, казалось бы, нет. Однако, если повернуть стакан на 90° и собрать снова всю конструкцию с новым положением стакана, упругие перемещения могут существенно измениться (рисунок 21,б, график 2). Теперь при той же силе нагружения упругие перемещения стали значительно меньше. Кроме этого нет и излома на графике. Это обстоятельство должно найти соответствующее объяснение, поскольку решающим образом влияет на показатели качества всего изделия. При этом речь не идет о данном, конкретном изделии, а обо всей партии изделий. Объяснение может и не быть найдено, если не использовать закономерности технологического наследования. Необходимо детально проанализировать всю технологическую цепочку изготовления деталей и их сборки, анализу должна быть подвергнута и производственная среда.
При анализе можно установить, что во время токарной или шлифовальной обработок стаканов последние закреплялись в трехкулачковых патронах. Такое закрепление вызывает, естественно, деформирование заготовок стаканов. Следовательно, поверхности сопряжении стаканов с другими деталями будут иметь столько крупных волн, сколько кулачков было у патронов. Эта погрешность формы является наследственной. Она зародилась еще на стадии токарной обработки одной из деталей (стакана), всей конструкции. Форма контактной поверхности стаканов условно показана пунктирной линией на графике.
Если причина анализируемого явления установлена, то необходимо принимать меры к устранению ее соответствующей технологической операцией процесса. Если же обнаруженная причина положительно сказывается на качественных показателях детали или изделия, соответствующие условия обработки необходимо сохранять и способствовать их развитию.
Уже разработаны необходимые для практики методические положения, позволяющие облегчить анализ наследственных связей и установить количественные соотношения. Однако объективное существование наследственных связей не означает, что во всех случаях их необходимо учитывать. Если, например, речь идет об изготовлении машиностроительных изделий нормальной точности, наследственная доля погрешности может оказаться сравнительно малой. Основными могут оказаться традиционные погрешности, характерные для большинства технологических процессов изготовления машин. В тех же случаях, когда допустимые погрешности должны быть малыми по величине и их устранение представляется весьма сложной технологической задачей, наследственная доля допуска может не только быть соизмеримой с самим допуском, но и превосходить его. Следовательно, закономерности технологического наследования необходимо использовать, прежде всего, в прецизионном машиностроении.
Связь погрешности закрепления и точности размера показана на рисунке 17. Фрезерный станок предварительно настроен на размер С для выдерживания размера Н. После приложения к заготовке сил закрепления Q она переместится на величину
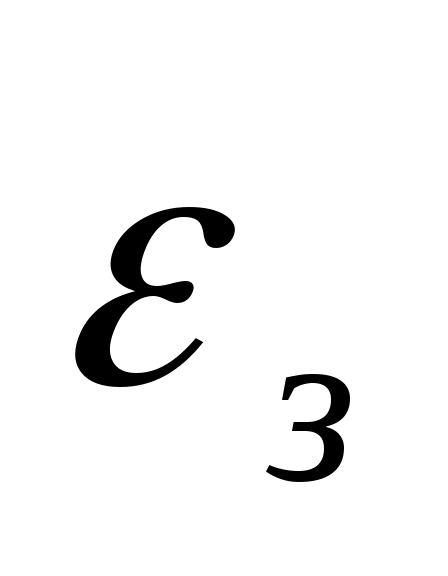
Погрешностью закрепления
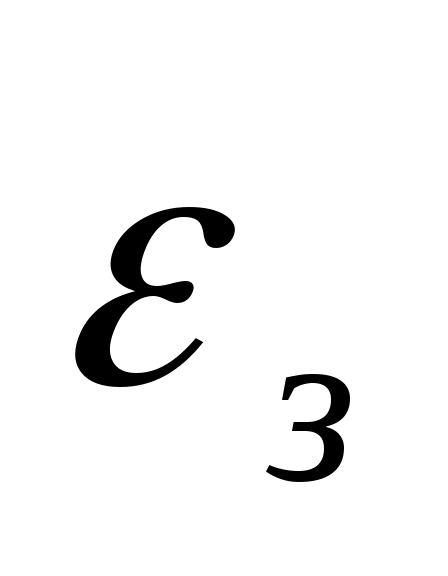
Силы закрепления вызывают также отклонения формы. На рисунке 18 показаны четыре фазы (I…IV) состояние заготовки типа
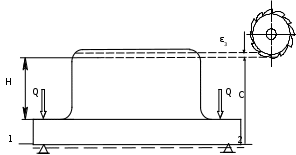

ε3
Рисунок 17--Схема образования погрешности закрепления
кольца, установленного в трехкулачковый патрон для растачивания отверстия.
На рисунке 17 на первой фазе заготовка не деформирована, на второй ― и наружная, и внутренняя поверхности деформированы силами Q. После растачивания отверстия (третья фаза) отклонений формы не наблюдается. Точности размера и формы отверстия могут быть весьма высокими. Наружная поверхность деформирована. После раскрепления кольца (четвертая фаза) точность отверстия нарушена (показано утрированно), а наружная поверхность восстановила свою форму.
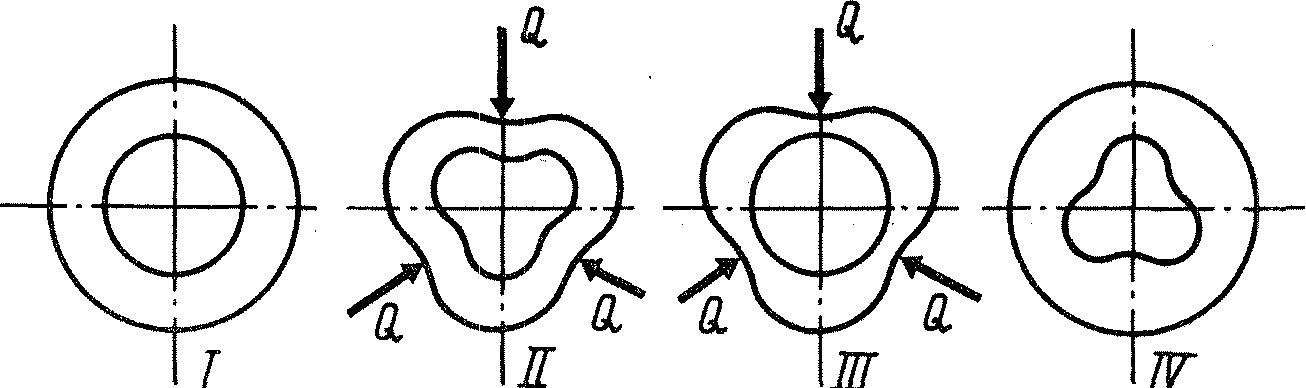
Рисунок 18 – Погрешности формы, вызываемые силами закрепления
Рациональное базирование и закрепление заготовок позволяют существенно повысить точность деталей. На рисунке 19,a показана деталь, на которой необходимо фрезеровать уступ с размерами 35 и 10 мм, а на рисунке 19,б-д―различные схемы установки заготовки с применением призм и приспособления со втулкой. Если определить по соответствующим формулам погрешности базирования и закрепления (при прочих равных условиях), суммировать эти погрешности, то можно убедиться в том, что наибольшую погрешность даст схема установки, приведенная на рисунке 19,в, а наименьшую ― схема на рисунке 19,д. Для последней εб = 0, так как измерительная и технологическая базы совмещены. Точность размера 35-0,1 будет определяться только погрешностью закрепления, т.е. деформацией технологической базы. Схема на рисунке 19д оказывается точнее схемы на рисунке 19,в примерно в 40 раз.
Третья составляющая часть погрешности установки ― погрешность εП, вызываемая применением приспособлений. Ее учитывают каждый раз особо. Возникновение этой погрешности связано с неточностью изготовления приспособлений, их установкой на станке, износом опор от многократного контактирования с заготовками.
При установке приспособлений на станки возникают различные перекосы, установочные элементы занимают положения, не соответствующие заданным. Например, обычные трехкулачковые патроны при каждом закреплении на шпинделях станков занимают новые положения. Рассеяние положений происходит в пределах зазора между шейкой шпинделя и отверстием в патроне, так как ось вращения шпинделя и ось патрона не совпадают. В другом случае зажимные элементы приспособлений в процессе закрепления заготовок перекашиваются в пределах зазора в направляющих и при этом увлекают за собой заготовку. Заготовку закрепляют каждый раз в новом положении.
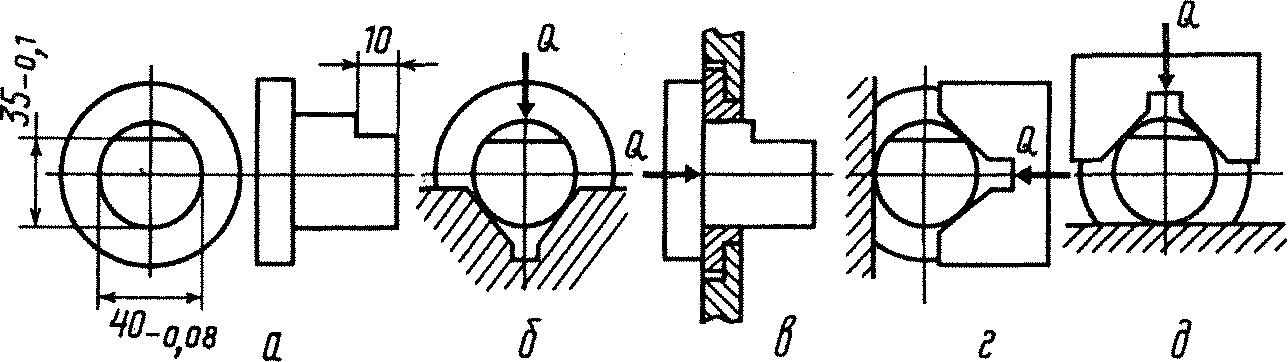
Рисунок 19 – Варианты выбора рациональной схемы базирования
и закрепления заготовки
Износ приспособлений и, прежде всего, их установочных элементов может оказать существенное влияние на точность установок. Элементы изнашиваются неравномерно.
Каждая из причин возникновения погрешностей, связанных с применением приспособлений, должна быть рассмотрена особо. Некоторые погрешности (например, перекос при установке приспособления) следует рассматривать как постоянные, действие которых одинаково для всех заготовок в партии, другие же имеют случайный характер (например, погрешность положения заготовок в процессе их закрепления).
Рассмотренные погрешности, как составные части погрешности установки, необходимо суммировать. Поскольку все они все имеют случайный характер, то суммировать их следует по закону теории вероятности. Погрешности необходимо рассматривать после рассеяния случайных величин, распределение которых в первом приближении подчиняется закону Гаусса. Тогда
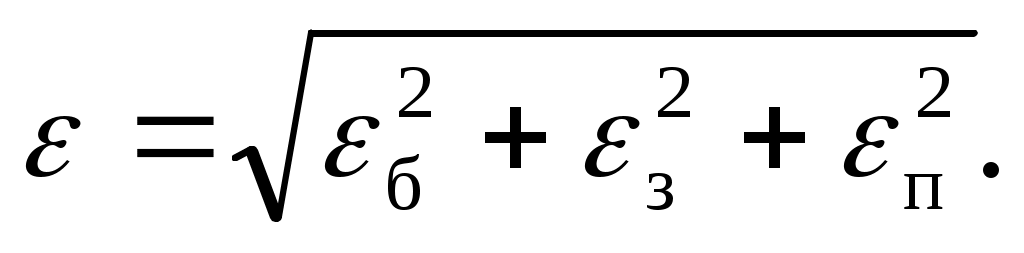
Нужно стремиться к сокращению всех погрешностей, стоящих под знаком корня.
Наследственные связи не могут быть реализованы вне контактов заготовок как твердых тел с элементами технологических систем. В первую очередь, такими элементами являются технологические базы. В условиях, когда используется принцип постоянства технологических баз, что приводит к повышению точностных характеристик, проявление взаимодействия баз с заготовками сказывается особенно наглядно. Вазовые поверхности сами имеют погрешности. Контактирование заготовок с такими базами непременно влияет на характер наследования.
Технологические базы заготовок всегда имеют отклонения размера, формы и расположения поверхностей контакта с приспособлением или оборудованием. Эти отклонения наследуются на обрабатываемых поверхностях. Так, погрешность, возникшая, например, в начале технологического процесса, может устойчиво сохраняться вплоть до стадии эксплуатации детали. Особенно трудно бороться с малыми по величине отклонениями (погрешностями). Рассмотрим типовой пример.
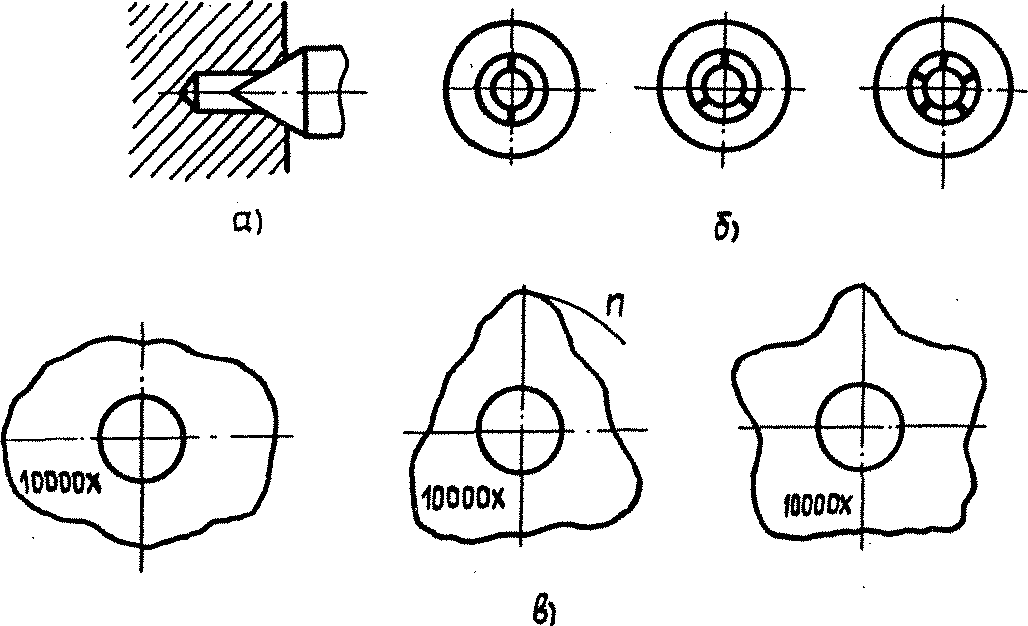
Рисунок 20 – Схема наследования погрешностей технологических баз
Центровое отверстие ("гнездо" на деталях, например, типа валов (рисунок 20,а)) имеет номинально коническую форму и контактирует с конической формой центра, который играет роль приспособления. Однако детальное рассмотрение формы технологической базы ― центрового отверстия ― позволяет убедиться в том, что на его конической поверхности имеются характерные выступы (волны). Если посмотреть на центровое отверстие (рисунок 20,б), то наличие волн на уже контактировавшем с центром валу можно обнаружить по характерным блестящим полоскам. Чаще всего на центровых отверстиях наблюдают 2, 3 или 5 волн. Наиболее отчетливо эти волны можно зафиксировать с помощью кругломера.
Когда происходит обработка наружной поверхности вала методом шлифования и на заготовку действует сила постоянного направления, условия контакта выступов центрового отверстия и центра постоянно изменяются. Изменяется по углу поворота заготовки и жесткость сопряжения «центр-отверстие». В результате этого на наружной обрабатываемой поверхности возникает соответствующая волнистая поверхность (рисунок 20,в). Если на центровом отверстии были две волны, то и наружная поверхность детали также будет иметь две волны. При контакте центра станка с тремя выступами отверстия на обрабатываемой поверхности возникнет также три волны и т.д. Высота волн может быть малой и фиксируется при соответствующем увеличении на кругломере. Так, на финишной операции возникают погрешности, причина которых была создана еще на начальной операции центрования заготовок. Наследственная погрешность устойчиво сохранилась на протяжении всего технологического процесса.
Трудно себе представить элемент технологического процесса или технологическую операцию, где не проявлялось бы технологическое наследование. Закономерности наследования объективны. Практическое же их проявление отчетливо видно на стадии эксплуатации изделия. Это положение покажем на примере рисунка 21.
В корпусную деталь изделия поставлен стакан, в котором установлен подшипник качения (рисунок 21,а). Сила Р, действующая на вал и подшипник, вызывает упругое перемещение всего соединения. Такое перемещение зависит от величины приложенной силы. Картина нагружения показана на графике 1 (рисунок 21,б).
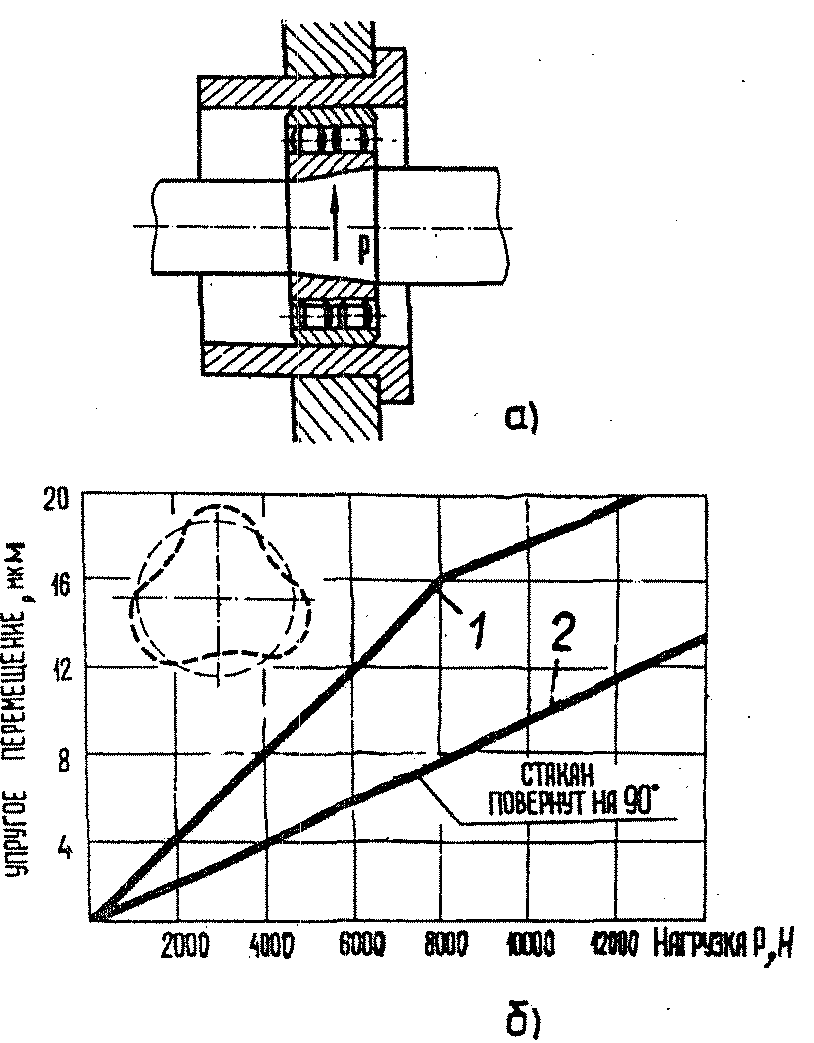
Рисунок 21 – Проявление технологической наследственности
в ходе эксплуатации изделий
Упругое перемещение элементов конструкции растет по мере возрастания силы Р. При силе Р=8000Н характер упругих перемещений изменяется и на графике наблюдается излом. В этом элементарном эксперименте ничего особенного, казалось бы, нет. Однако, если повернуть стакан на 90° и собрать снова всю конструкцию с новым положением стакана, упругие перемещения могут существенно измениться (рисунок 21,б, график 2). Теперь при той же силе нагружения упругие перемещения стали значительно меньше. Кроме этого нет и излома на графике. Это обстоятельство должно найти соответствующее объяснение, поскольку решающим образом влияет на показатели качества всего изделия. При этом речь не идет о данном, конкретном изделии, а обо всей партии изделий. Объяснение может и не быть найдено, если не использовать закономерности технологического наследования. Необходимо детально проанализировать всю технологическую цепочку изготовления деталей и их сборки, анализу должна быть подвергнута и производственная среда.
При анализе можно установить, что во время токарной или шлифовальной обработок стаканов последние закреплялись в трехкулачковых патронах. Такое закрепление вызывает, естественно, деформирование заготовок стаканов. Следовательно, поверхности сопряжении стаканов с другими деталями будут иметь столько крупных волн, сколько кулачков было у патронов. Эта погрешность формы является наследственной. Она зародилась еще на стадии токарной обработки одной из деталей (стакана), всей конструкции. Форма контактной поверхности стаканов условно показана пунктирной линией на графике.
Если причина анализируемого явления установлена, то необходимо принимать меры к устранению ее соответствующей технологической операцией процесса. Если же обнаруженная причина положительно сказывается на качественных показателях детали или изделия, соответствующие условия обработки необходимо сохранять и способствовать их развитию.
Уже разработаны необходимые для практики методические положения, позволяющие облегчить анализ наследственных связей и установить количественные соотношения. Однако объективное существование наследственных связей не означает, что во всех случаях их необходимо учитывать. Если, например, речь идет об изготовлении машиностроительных изделий нормальной точности, наследственная доля погрешности может оказаться сравнительно малой. Основными могут оказаться традиционные погрешности, характерные для большинства технологических процессов изготовления машин. В тех же случаях, когда допустимые погрешности должны быть малыми по величине и их устранение представляется весьма сложной технологической задачей, наследственная доля допуска может не только быть соизмеримой с самим допуском, но и превосходить его. Следовательно, закономерности технологического наследования необходимо использовать, прежде всего, в прецизионном машиностроении.