Добавлен: 08.11.2023
Просмотров: 280
Скачиваний: 4
ВНИМАНИЕ! Если данный файл нарушает Ваши авторские права, то обязательно сообщите нам.
Рис.6 Места повреждений и износов корпуса автосцепки трещины 4 в месте перехода головы к хвостовику и трещины 6 в стенке отверстия для клина тягового хомута.
Повреждения в этой зоне характеризуются хрупким разрушением и в большинстве своем происходят в результате" износа перемычки. Уменьшение толщины перемычки происходит в результате износа 7 упорной поверхности хвостовика от взаимодействия с упорной плитой и за счет износа и смятия 5 стенки отверстия от взаимодействия с клином хомута. Основной причиной износа этого отверстия является существенное увеличение продольных сил, действующих в большегрузных поездах, наибольшие значения которых превышают предел текучести используемого металла. Поэтому клиновое соединение в усиленных автосцепках заменяют более прочным - шарнирным; износы 2 тяговых и ударных поверхностей большого и малого зубьев существенно ухудшают продольную динамику вагонов и могут явиться причиной саморасцепов, износы 8 поверхностей корпуса в месте соприкосновения с поверхностями проема ударной розетки происходят в случае отклонения оси корпуса автосцепки в вертикальной и горизонтальной плоскостях. При проходе вагонов в кривых малого радиуса и особенно при сцеплении вагонов с разной длиной консольной части рамы оси автосцепки отклоняются и на первом этапе подвергаются износу вертикальные стенки корпуса автосцепки. При достижении определенного значения износа прочность стенок становится недостаточной, хвостовик начинает изгибаться в горизонтальной плоскости, и в этом месте появляются трещины. Аналогичное явление наблюдается в вертикальной плоскости, когда поезд проходит различные переломы профиля пути - возникает заклинивание автосцепок в контуре зацепления. В результате этого хвостовик автосцепки одного из вагонов упирается через тяговый хомут в верхнее перекрытие хребтовой балки и начинает поднимать вагон. Это приводит к изгибу хвостовика или изломам маятниковых подвесок смежной автосцепки.
Как показывает обследование корпусов автосцепок с трещинами и изломами хвостовика, у 60% корпусов автосцепок, кроме того, имели место дефекты технологического происхождения (разностенность хвостовика).
Износ поверхности 3 упора головы автосцепки в выступ ударной розетки происходит из-за недостаточной эффективности поглощающих аппаратов в определенных поездных ситуациях. После полного использования их энергоемкости избыточная часть кинетической энергии остается непогашенной поглощающим аппаратом и передается непосредственно от головы корпуса автосцепки на выступ розетки и раму вагона. Такая передача сил отрицательно влияет и на техническое состояние рамы вагона.
Вертикальные трещины в зеве со стороны большого зуба в углах разрешается заваривать при условии, что после разделки они не будут выходить на горизонтальные плоскости наружных ребер большого зуба. Трещины в углах проемов для замка и замкодержателя можно заваривать, если разделка трещин в верхних углах проема для замка не выходит на горизонтальную поверхность головы, в верхнем углу проема для замкодержателя не выходит за положение верхнего ребра со стороны большого зуба, а длина разделанной трещины в нижних углах проемов для замка и замкодержателя не превышает 20 мм.
Трещины в месте перехода головы к хвостовику можно заваривать, если при глубине их более 5 мм поперечное сечение стенок хвостовика после разделки не уменьшается более чем на 25%.
Заварка трещин в корпусах автосцепок из низколегированных сталей 20ГЛ-Б, 20ГФЛ должна производиться с использованием электродов типов Э42А, Э46А, Э50А, Для повышения качества заварки трещин целесообразно перед заваркой корпус автосцепки нагревать до температуры 250-300°С, что улучшит адгезию наплавленного металла и снизит остаточные термические напряжения.
Износы ударных и тяговых поверхностей большого и малого зубьев и ударной поверхности зева восстанавливают наплавкой при условии, что наплавляемый металл не должен доходить ближе 15 мм к закруглениям в углах и иметь твердость не менее НВ 250. Для получения твердости металла НВ 450 рекомендуется использовать электроды ОЗН-400, порошковую проволоку ПП-ТН500, пластинчатые электроды с легирующими присадками.
Поверхность перемычки хвостовика со стороны прилегания клина тягового хомута и с торца хвостовика можно наплавлять, если толщина изношенной перемычки составляет не менее 40 мм для автосцепок СА-3 и не менее 44 мм для СА-ЗМ. Для восстановления этих поверхностей рекомендуется использовать электроды марки УОНИ 13/85.
Разработана технология восстановления перемычки хвостовика автосцепки СА-3 электрошлаковой сваркой на установке Т 682. Такая технология позволяет восстанавливать хвостовики корпуса автосцепки с любыми трещинами, разрывами и износами при толщине перемычки менее 40 мм. Ремонт состоит в полной вырезке перемычки термическим или механическим способом, в заплавке проема и в последующей термической обработке корпуса автосцепки.
Установка получает питание от отдельного фидера для предотвращения перерыва подачи электроэнергии при заварке перемычки. При сварке используют легированную сварочную проволоку марки Св-08Г2С диаметром 4 мм и плавящийся мундштук - цельнотянутая труба из стали 20 длиной около 500 мм, наружным диаметром 15 мм, внутренним 5 мм. Сварку ведут под слоем флюса марки АК-8. Установка работает от сети напряжением 380 В с частотой 50 Гц. Напряжение дуги 50-52 В. Для облегчения возбуждения дуги вначале на дно основания кокиля укладывают отрезок стального прута диаметром 20-25 мм, длиной 20-30 мм и засыпающего дробленой стальной стружкой слоем около 15 мм. Плавящийся трубчатый мундштук располагают на расстоянии 40 - 50 мм от дна кармана, засыпав зазор флюсом. Процесс сварки при сварочном токе около 800 А длится 18-20 мин. Общее время на восстановление перемычки составляет около 45 мин.
Для снятия внутренних напряжений и улучшения структуры металла хвостовик" автосцепки подвергают термообработке: нормализация с нагревом детали до температуры 920°С, выдержкой в течение 3 ч и охлаждением на воздухе до температуры 300°С; высокотемпературный отпуск с нагревом до температуры 640 - 650°С, выдержкой при этой температуре до 4 ч и охлаждением на воздухе.
Для восстановления изношенных поверхностей корпуса автосцепки применяют полуавтоматические и автоматические сварочные установки, а также метод наплавки лежачим пластинчатым электродом.
Технология наплавки деталей автосцепки лежачим пластинчатым электродом состоит в том, что на наплавляемую поверхность 9 (рис.7) насыпают слой гранулированного флюса 8, толщина которого определяет длину электрической дуги (примерно 4 мм).
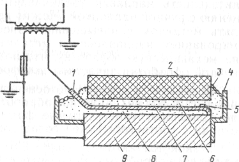
Рис.7 Схема наплавки лежачим пластинчатым электродом
Наплавляемую поверхность располагают горизонтально или с уклоном 2-3° в сторону от начала наплавки для предотвращения короткого замыкания, когда расплавленный металл может подтечь под электрод.
На флюс укладывают электрод 7, представляющий стальную пластинку, форма и размеры которой соответствуют контуру наплавляемой поверхности. Один конец пластинчатого электрода с помощью держателя соединяют с проводом источника сварочного тока, а другой (обратный) провод этого источника через специальные сварочные столы или стенды - с наплавляемой деталью.
На пластинчатый электрод насыпают флюс 6 той же марки количестве, необходимом для создания в процессе наплавки шлаковой ванны, обеспечивающей нормальное протекание процесса наплавки и защиту расплавленного металла от окисления кислородом воздуха (примерная толщина слоя 12-мм).
С целью улучшения качества формирования наплавочного валика особенно при наплавке широких поверхностей, сверху флюса укладывают прижимную медную или графитовую пластину, которая давит на ванну расплавленного металла и флюса.
Дуга возбуждается от пластинчатого электрода, соприкасающегося с наплавляемой поверхностью детали в зоне 5 или с помощью металлических опилок или стружек, подсыпаемых при укладке электрода между наплавляемой деталью с пластинчатым электродом в этой зоне. При замыкании цепи сварочного тока опилки расплавляются, и электрическая дуга возбуждается. Перемещаясь по кромке электрода, дуга расплавляет его и флюс. После расплавления горизонтальной части электрода процесс продолжается на его отогнутом конце 1. В комплект технологической оснастки входит флюсоудерживающее приспособление 4для создана стабильной прослойки флюса 3.
Процесс наплавки этим методом автоматизирован полностью. Вручную выполняют только вспомогательные операции. Производительность наплавки увеличивается примерно на 22% по сравнению с ручной наплавкой. Можно изношенные поверхности наплавлять металлом с повышенной износостойкостью, с хорошим формированием наплавленного металла и незначительным припуском на механическую обработку, что позволяет заменить операции станочной обработки зачисткой шлифовальным кругом.
Поверхности корпуса автосцепки, наплавленные другими способами требуют механической обработки. Для этого на заводах и в депо применяют универсальные фрезерные, строгальные, долбежные станки с соответствующей оснасткой.
Станок-полуавтомат (рис.8) позволяет с одной установки корпуса обрабатывать поверхности контура зацепления, отверстие для валика подъемника, стенки отверстия под клин, перемычку и торец хвостовика. На таком станке можно обработать 14 поверхностей.
Станок имеет станину 12; устройства: 21для обработки поверхностей контура зацепления,19 - отверстий валика подъемника,14-отверстия под клин тягового хомута и торцовую часть хвостовика; насосные станции для подачи охлаждающей эмульсии и масла в системе станка при его работе. Станина станка является одновременно и установочным кондуктором для корпуса автосцепки.
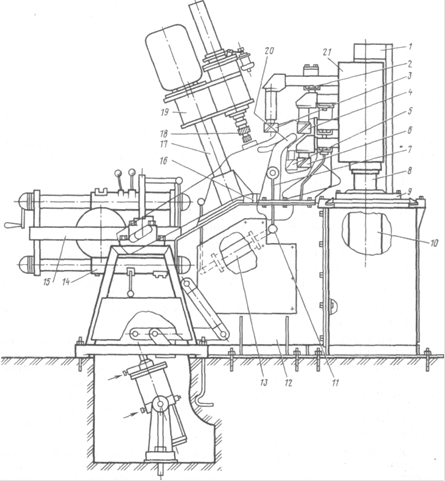
Рис.8 Станок-полуавтомат для обработки корпуса автосцепки
На горизонтальной поверхности станины размещена двухопорная жесткая рама являющаяся технологической базой, определяющей правильную установку корпуса автосцепки относительно режущих головок устройств.
С помощью подвижной шаровой опоры 16, рычагов 7, приводимых в действие винтовыми парами 11 и силовым пневмоцилиндром 13, корпус автосцепки надежно закрепляется на станине в необходимом для обработки положении.
Устройство для обработки рабочих поверхностей контура зацепления представляет собой агрегат, имеющий привод от электродвигателя. Коробка скоростей 10приводит во вращение вертикальный раздаточный вал 8, закрепленный одним концом (нижним) на плите-опоре 9, а вторым (верхним) - в кронштейне 1. Раздаточный вал2 имеет четыре раздельные режущие головки 3, 4, 5 и 6, необходимые для обработки рабочих поверхностей контура зацепления. Режущие головки выполнены в виде ригеля, один конец которого оснащен фрезой, а второй находится в зацеплении с шестерней раздаточного вала.
Устройство для обработки отверстий под валик подъемника состоит из специального блока, закрепленного на стойке 17, который может поворачиваться из нерабочего в рабочее положение. В шпиндель блока вставляется оправка с двумя фрезами 18. Устройство для обработки поверхности отверстия перемычки и торцовой части хвостовика состоит из кольцеобразного незамкнутого люнета 15, шарнирно закрепленного на станине по центру торцовой части хвостовика. Режущая головка с фрезой может перемещаться по отверстию хвостовика корпуса как в продольном направлении, так и по радиусу торца хвостовика.
В последние годы значительно увеличивается количество корпусов автосцепки, имеющих уширение зева головы и деформации хвостовика. Уширение зева определяется соответствующим шаблоном. Проверку производят по всей высоте носка большого зуба. Для этого шаблон прикладывают одним концом к углу малого зуба, а другой подводят к носку большого зуба. Если кромка шаблона пройдет мимо носка большого зуба в зев, значит зев расширен.
При обнаружении уширения зева или изгиба хвостовика автосцепки в вертикальной или горизонтальной плоскости, превышающего 3 мм от продольной оси, корпус необходимо править с предварительным подогревом до температуры 800-850°С с выдержкой в печи в течение 1 ч для равномерного прогрева корпуса по сечению. Если на корпусе автосцепки в зонах деформаций обнаружены