Добавлен: 08.11.2023
Просмотров: 279
Скачиваний: 4
ВНИМАНИЕ! Если данный файл нарушает Ваши авторские права, то обязательно сообщите нам.
незаваренные или ранее заваренные трещины, то такой корпус бракуется.
Корпусы автосцепки необходимо нагревать в печах с восстановительной или нейтральной атмосферой для того, чтобы избежать выгорание углерода и легирующих присадок в процессе нагрева, а правку заканчивать при температуре выправляемой зоны не менее 650°С для предотвращения образования остаточных термических напряжений и трещин.
Правка деформированного зева и хвостовиков на многих предприятиях производится под обычными прессами. Эта правка малоэффективна и недостаточна. Разработана и внедрена более совершенная конструкция пресса, который состоит из станины, установочных кондукторов и нажимных копиров, имеющих конфигурацию корпуса автосцепки, гидронасосной станции с приводом и приборами управления.
После закрепления нагретого корпуса включают гидравлическую систему и штоки цилиндров с закрепленными на них нажимными копирами одновременно перемещаются по направлению к установочным кондукторам. При движении копиры встречаются с поверхностями корпуса, самоустанавливаются соответственно их поверхностям и производят правку. Предварительно в зев корпуса автосцепки вставляют планку-ограничитель, исключающую сужение зева больше нормы.
После разборки механизма сцепления автосцепки все его детали измеряют проходными и непроходными шаблонами. По результатам измерений устанавливают объем ремонта. Повреждения деталей механизма сцепления и износы поверхностей устраняют сваркой и наплавкой. Для повышения износостойкости и твердости наплавляемого слоя рекомендуется использовать полуавтоматическую наплавку порошковой проволокой ПП-ТН350 и ПП-ТН500, а также наплавку лежачим пластинчатым электродом.
Этот метод целесообразно использовать при восстановлении замыкающей поверхности 1 замка (рис.9, а). Остальные изношенные поверхности 3, 5, 6 замка, имеющие небольшие площади и достаточно сложную форму, наплавляют обычно вручную. При изломе сигнального отростка 4 приваривают встык новый, заранее отштампованный, а при изломе шипа 2 для предохранителя рассверливают отверстие в замке и в него вставляют новый шип. По скошенным кромкам отверстия с обеих сторон замка обваривают новый шип.
Рис.9 Зоны износов и повреждений на деталях механизма сцепления
Наплавленную поверхность замыкающей части замка обрабатывают в основном на вертикально-фрезерных станках, так как они наиболее производительны, или с помощью шлифовально-пневматической машинки. Обработка поверхности замыкающей части замка представляет определенную сложность, так как эта поверхность имеет уклон 5° (от кромки к середине замка). Поэтому для обработки таких поверхностей разработано специальное приспособление, устанавливаемое на столе фрезерного станка.
Погнутые замкодержатели выправляют нагретыми до температуры 820-900°С в специальном штампе, позволяющем значительно снизить трудоемкость правки при высоком качестве выполнения операции.
Заварку трещин 7, 11 (рис.9, б) и наплавку изношенных поверхностей 8, 9, 10и 12замкодержателя выполняют вручную из-за сложной формы поверхностей. При этом применяют приспособления для расположения замкодержателей в удобном для сварочных работ положении. Механическую обработку осуществляют в приспособлениях, устанавливаемых на вертикально-фрезерном станке. Предохранители замка, имеющие деформации плеч, правят в нагретом состоянии под прессами с использованием специальных штампов. Поверхности 13 (рис.9.6, в) и под шип 2восстанавливают электронаплавкой после правки. При механической обработке особое внимание обращают на качество обработки торца верхнего плеча, так как от этого будет зависеть надежность действия предохранителя замка от саморасцепа.
Ремонт наплавкой изношенных поверхностей 14, 15, 16 подъемника (рис.9, г) и поверхности 17 валика подъемника (рис.9, д) производится в основном с помощью ручной сварки с использованием специальных приспособлений, а механическая обработка - на вертикально-фрезерных и других станках.
После ремонта детали механизма сцепления проверяют шаблонами и передают для сборки на сборочный стенд и установки в корпус автосцепки. На опору в нижней части кармана, расположенную на стенке со стороны большого зуба, укладывают подъемник большим пальцем кверху. В окно, предусмотренное для замкодержателя, вводят замкодержатель противовесом вперед и овальным отверстием навешивают на шип. В окно, предназначенное для замка, вкладывают замок с предварительно надетым на его шип предохранителем так, чтобы замок встал на свою опору, а верхнее плечо предохранителя легло на полочку на внутренней стенке со стороны малого зуба. В отверстие на этой стенке снаружи вставляют валик подъемника, который проходит через овальное отверстие в замке и входит в квадратное отверстие в подъемнике замка. В выемку валика подъемника вставляют запорный болт через отверстие в приливе на стенке корпуса и закрепляют гайкой. Предварительно под головку болта и под гайку устанавливают фасонные шайбы, которые загибают на грани головки болта и гайки.
Правильность сборки механизма проверяют вдавливанием замка рукой внутрь кармана заподлицо с ударной стенкой зева и при отпускании замок должен свободно возвращаться в исходное положение. Также проверяют подвижность замкодержателя. Отсутствие заедания в механизме при расцеплении проверяют поворотом валика подъемника.
2.1 Техническое состояние п ремонт автосцепного устройства..
Обслуживание автосцепного устройства происходит на основании Инструкции по ремонту и обслуживанию автосцепного устройства подвижного состава железных дорог ЦВ-ВНИИЖТ-494.
Проверка автосцепного устройства при техническом обслуживании вагонов и локомотивов.
Требования, изложенные в данной главе, относятся к проверке автосцепного устройства во время технического обслуживания вагонов при подготовке поездов на пунктах технического обслуживания, а также вагонов под погрузку, при техническом обслуживании (TO-2: TO-3) локомотивов и вагонов дизель- и электропоездов, техническом обслуживании специального подвижного состава и в других случаях, специально оговоренных ОАО «РЖД».
Запрещается постановка в поезда и следование в них вагонов и других единиц подвижного состава, у которых автосцепное устройство имеет хотя бы одну из следующих неисправностей (в том числе выявляемых в зоне, видимой при осмотре с пролазкой):
а) трещина корпуса автосцепки;
б) трещина тягового хомута, излом клина тягового хомута или валика, неисправное или нетиповое их крепление. Признаками излома клина являются изгиб болта, поддерживающего клин, блестящая намятина заплечиков клина, металлическая пыль на хомуте, увеличенный или уменьшенный выход автосцепки, а также двойной удар при ударе молотком по клину снизу;
в) излом или трещина центрирующей балочки, маятниковых подвесок (или направляющей рейки центрирующего прибора безмаятникового типа), неправильно поставленные маятниковые подвески грузовых вагонов (широкими головками вниз), излом пружин, отсутствие гаек или обрыв болтов пружин центрирующего прибора;
г) износ или другие повреждения корпуса и механизма сцепления, при которых возможен саморасцеп автосцепок.
Действие предохранителя от саморасцепа проверяют специальным ломиком (рис.8.26).
Для проверки ломик заостренным концом вводят сверху в пространство между ударной стенкой зева одной автосцепки и торцевой поверхностью замка другой (смежной) автосцепки (рис.8.27, о положение 1). Поворачивая выступающий конец ломика по направлению стрелки, нажимают заостренным конном на замок.
Если он не ухолит внутрь кармана и при этом слышен четкий металлический стук от удара предохранителя в противовес замкодержателя, значит предохранительное устройство от саморасцепа исправно. Также проверяют и смежную автосцепку.
При проверке автосцепок пассажирских вагонов между секциями локомотивов, а также грузовых вагонов, если находящийся в них груз препятствует введению ломика сверху, ломик вводят снизу через отверстие в нижней стенке кармана и, упираясь в кромку отверстия, нажимают на замок в нижней части (рис. 8.27, б положение 4).
Если при проверке действия предохранителя от саморасцепа обнаружено, что замок раскачивается более чем на 20 мм (определяют это при помощи заостренной части ломика, имеющей ширину 20 мм) или выходит за кромку ударной поверхности малого зуба, то необходимо проверить, лежит ли на полочке верхнее плечо предохранителя. Для этого изогнутый конец ломика заводят за выступ замка (рис.8.27, а положение
2) и нажимают на выступающую часть ломика по направлению стрелки, выталкивая замок из кармана корпуса до отказа. Если замок неподвижен или его свободное качание значительно уменьшилось, то это означает, что предохранитель соскочил с полочки.
Когда автосцепки натянуты и увести замки внутрь кармана корпуса ломиком невозможно, надежность работы механизма определяют по состоянию замкодержателя, предохранителя и полочки. Чтобы проверить замкодержатель, ломик вводят в пространство между ударными поверхностями автосцепок сверху или снизу через отверстие корпуса, предназначенное для восстановления сцепленного состояния у ошибочно расцепленных автосцепок (рис. 8.27, б положение 3), и нажимают на лапу замкодержателя. Если лапа после прекращения нажатия возвратится в первоначальное положение и будет прижиматься к ударной поверхности малого зуба смежной автосцепки, то замкодержатель исправен. В случае, когда противовес замкодержателя отломан, лапа свободно качается, и при нажатии на нее ломиком проверяющий не ощущает заметного сопротивления. Заедание замкодержателя внутри кармана корпуса, обнаруживаемое при нажатии на его лапу ломиком сверху, свидетельствует о возможном изгибе полочки для верхнего плеча предохранителя, препятствующем свободному повороту замкодержателя. Наличие верхнего плеча предохранителя проверяют ломиком, который вводят в карман корпуса через отверстие для сигнального отростка (рис. 8.27, а положение 5). Прижимая ломик к замкодержателю, упирают его изогнутый конец в предохранитель и перемещают по направлению к полочке. Металлический звук от удара предохранителя о полочку при отпускании ломика указывает на то, что верхнее плечо предохранителя не изломано. Если ломик при перемещении не упрется в полочку, значит, она отсутствует;
д) трещина или сквозная протертость корпуса поглощающего аппарата; повреждения, вызывающие потерю поглощающим аппаратом упругих свойств, о чем свидетельствует наличие зазора между упорными угольниками и упорной плитой или корпусом аппарата (при поглощающем аппарате 73 ZW указанный суммарный зазор допускается не более 5 мм);
е) зазор между потолком розетки и хвостовиком корпуса автосцепки менее 25 мм (для центрирующего прибора с жесткой опорой);
ж) выход вкладышей крепления крышки поглощающего аппарата Ш-6-ТО-4 за наружные плоскости боковых стенок корпуса;
з) ход более 70 мм поглощающего аппарата, установленного на вагоны с розеткой старой конструкции, имеющей длину выступающей части 185 мм;
Корпусы автосцепки необходимо нагревать в печах с восстановительной или нейтральной атмосферой для того, чтобы избежать выгорание углерода и легирующих присадок в процессе нагрева, а правку заканчивать при температуре выправляемой зоны не менее 650°С для предотвращения образования остаточных термических напряжений и трещин.
Правка деформированного зева и хвостовиков на многих предприятиях производится под обычными прессами. Эта правка малоэффективна и недостаточна. Разработана и внедрена более совершенная конструкция пресса, который состоит из станины, установочных кондукторов и нажимных копиров, имеющих конфигурацию корпуса автосцепки, гидронасосной станции с приводом и приборами управления.
После закрепления нагретого корпуса включают гидравлическую систему и штоки цилиндров с закрепленными на них нажимными копирами одновременно перемещаются по направлению к установочным кондукторам. При движении копиры встречаются с поверхностями корпуса, самоустанавливаются соответственно их поверхностям и производят правку. Предварительно в зев корпуса автосцепки вставляют планку-ограничитель, исключающую сужение зева больше нормы.
После разборки механизма сцепления автосцепки все его детали измеряют проходными и непроходными шаблонами. По результатам измерений устанавливают объем ремонта. Повреждения деталей механизма сцепления и износы поверхностей устраняют сваркой и наплавкой. Для повышения износостойкости и твердости наплавляемого слоя рекомендуется использовать полуавтоматическую наплавку порошковой проволокой ПП-ТН350 и ПП-ТН500, а также наплавку лежачим пластинчатым электродом.
Этот метод целесообразно использовать при восстановлении замыкающей поверхности 1 замка (рис.9, а). Остальные изношенные поверхности 3, 5, 6 замка, имеющие небольшие площади и достаточно сложную форму, наплавляют обычно вручную. При изломе сигнального отростка 4 приваривают встык новый, заранее отштампованный, а при изломе шипа 2 для предохранителя рассверливают отверстие в замке и в него вставляют новый шип. По скошенным кромкам отверстия с обеих сторон замка обваривают новый шип.
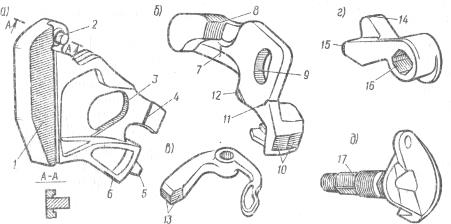
Рис.9 Зоны износов и повреждений на деталях механизма сцепления
Наплавленную поверхность замыкающей части замка обрабатывают в основном на вертикально-фрезерных станках, так как они наиболее производительны, или с помощью шлифовально-пневматической машинки. Обработка поверхности замыкающей части замка представляет определенную сложность, так как эта поверхность имеет уклон 5° (от кромки к середине замка). Поэтому для обработки таких поверхностей разработано специальное приспособление, устанавливаемое на столе фрезерного станка.
Погнутые замкодержатели выправляют нагретыми до температуры 820-900°С в специальном штампе, позволяющем значительно снизить трудоемкость правки при высоком качестве выполнения операции.
Заварку трещин 7, 11 (рис.9, б) и наплавку изношенных поверхностей 8, 9, 10и 12замкодержателя выполняют вручную из-за сложной формы поверхностей. При этом применяют приспособления для расположения замкодержателей в удобном для сварочных работ положении. Механическую обработку осуществляют в приспособлениях, устанавливаемых на вертикально-фрезерном станке. Предохранители замка, имеющие деформации плеч, правят в нагретом состоянии под прессами с использованием специальных штампов. Поверхности 13 (рис.9.6, в) и под шип 2восстанавливают электронаплавкой после правки. При механической обработке особое внимание обращают на качество обработки торца верхнего плеча, так как от этого будет зависеть надежность действия предохранителя замка от саморасцепа.
Ремонт наплавкой изношенных поверхностей 14, 15, 16 подъемника (рис.9, г) и поверхности 17 валика подъемника (рис.9, д) производится в основном с помощью ручной сварки с использованием специальных приспособлений, а механическая обработка - на вертикально-фрезерных и других станках.
После ремонта детали механизма сцепления проверяют шаблонами и передают для сборки на сборочный стенд и установки в корпус автосцепки. На опору в нижней части кармана, расположенную на стенке со стороны большого зуба, укладывают подъемник большим пальцем кверху. В окно, предусмотренное для замкодержателя, вводят замкодержатель противовесом вперед и овальным отверстием навешивают на шип. В окно, предназначенное для замка, вкладывают замок с предварительно надетым на его шип предохранителем так, чтобы замок встал на свою опору, а верхнее плечо предохранителя легло на полочку на внутренней стенке со стороны малого зуба. В отверстие на этой стенке снаружи вставляют валик подъемника, который проходит через овальное отверстие в замке и входит в квадратное отверстие в подъемнике замка. В выемку валика подъемника вставляют запорный болт через отверстие в приливе на стенке корпуса и закрепляют гайкой. Предварительно под головку болта и под гайку устанавливают фасонные шайбы, которые загибают на грани головки болта и гайки.
Правильность сборки механизма проверяют вдавливанием замка рукой внутрь кармана заподлицо с ударной стенкой зева и при отпускании замок должен свободно возвращаться в исходное положение. Также проверяют подвижность замкодержателя. Отсутствие заедания в механизме при расцеплении проверяют поворотом валика подъемника.
2.1 Техническое состояние п ремонт автосцепного устройства..
Обслуживание автосцепного устройства происходит на основании Инструкции по ремонту и обслуживанию автосцепного устройства подвижного состава железных дорог ЦВ-ВНИИЖТ-494.
Проверка автосцепного устройства при техническом обслуживании вагонов и локомотивов.
Требования, изложенные в данной главе, относятся к проверке автосцепного устройства во время технического обслуживания вагонов при подготовке поездов на пунктах технического обслуживания, а также вагонов под погрузку, при техническом обслуживании (TO-2: TO-3) локомотивов и вагонов дизель- и электропоездов, техническом обслуживании специального подвижного состава и в других случаях, специально оговоренных ОАО «РЖД».
Запрещается постановка в поезда и следование в них вагонов и других единиц подвижного состава, у которых автосцепное устройство имеет хотя бы одну из следующих неисправностей (в том числе выявляемых в зоне, видимой при осмотре с пролазкой):
а) трещина корпуса автосцепки;
б) трещина тягового хомута, излом клина тягового хомута или валика, неисправное или нетиповое их крепление. Признаками излома клина являются изгиб болта, поддерживающего клин, блестящая намятина заплечиков клина, металлическая пыль на хомуте, увеличенный или уменьшенный выход автосцепки, а также двойной удар при ударе молотком по клину снизу;
в) излом или трещина центрирующей балочки, маятниковых подвесок (или направляющей рейки центрирующего прибора безмаятникового типа), неправильно поставленные маятниковые подвески грузовых вагонов (широкими головками вниз), излом пружин, отсутствие гаек или обрыв болтов пружин центрирующего прибора;
г) износ или другие повреждения корпуса и механизма сцепления, при которых возможен саморасцеп автосцепок.
Действие предохранителя от саморасцепа проверяют специальным ломиком (рис.8.26).
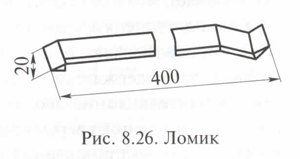
Для проверки ломик заостренным концом вводят сверху в пространство между ударной стенкой зева одной автосцепки и торцевой поверхностью замка другой (смежной) автосцепки (рис.8.27, о положение 1). Поворачивая выступающий конец ломика по направлению стрелки, нажимают заостренным конном на замок.
Если он не ухолит внутрь кармана и при этом слышен четкий металлический стук от удара предохранителя в противовес замкодержателя, значит предохранительное устройство от саморасцепа исправно. Также проверяют и смежную автосцепку.
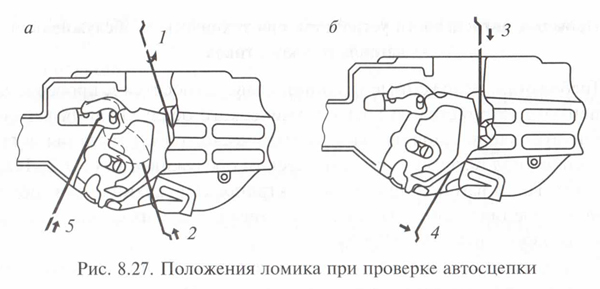
При проверке автосцепок пассажирских вагонов между секциями локомотивов, а также грузовых вагонов, если находящийся в них груз препятствует введению ломика сверху, ломик вводят снизу через отверстие в нижней стенке кармана и, упираясь в кромку отверстия, нажимают на замок в нижней части (рис. 8.27, б положение 4).
Если при проверке действия предохранителя от саморасцепа обнаружено, что замок раскачивается более чем на 20 мм (определяют это при помощи заостренной части ломика, имеющей ширину 20 мм) или выходит за кромку ударной поверхности малого зуба, то необходимо проверить, лежит ли на полочке верхнее плечо предохранителя. Для этого изогнутый конец ломика заводят за выступ замка (рис.8.27, а положение
2) и нажимают на выступающую часть ломика по направлению стрелки, выталкивая замок из кармана корпуса до отказа. Если замок неподвижен или его свободное качание значительно уменьшилось, то это означает, что предохранитель соскочил с полочки.
Когда автосцепки натянуты и увести замки внутрь кармана корпуса ломиком невозможно, надежность работы механизма определяют по состоянию замкодержателя, предохранителя и полочки. Чтобы проверить замкодержатель, ломик вводят в пространство между ударными поверхностями автосцепок сверху или снизу через отверстие корпуса, предназначенное для восстановления сцепленного состояния у ошибочно расцепленных автосцепок (рис. 8.27, б положение 3), и нажимают на лапу замкодержателя. Если лапа после прекращения нажатия возвратится в первоначальное положение и будет прижиматься к ударной поверхности малого зуба смежной автосцепки, то замкодержатель исправен. В случае, когда противовес замкодержателя отломан, лапа свободно качается, и при нажатии на нее ломиком проверяющий не ощущает заметного сопротивления. Заедание замкодержателя внутри кармана корпуса, обнаруживаемое при нажатии на его лапу ломиком сверху, свидетельствует о возможном изгибе полочки для верхнего плеча предохранителя, препятствующем свободному повороту замкодержателя. Наличие верхнего плеча предохранителя проверяют ломиком, который вводят в карман корпуса через отверстие для сигнального отростка (рис. 8.27, а положение 5). Прижимая ломик к замкодержателю, упирают его изогнутый конец в предохранитель и перемещают по направлению к полочке. Металлический звук от удара предохранителя о полочку при отпускании ломика указывает на то, что верхнее плечо предохранителя не изломано. Если ломик при перемещении не упрется в полочку, значит, она отсутствует;
д) трещина или сквозная протертость корпуса поглощающего аппарата; повреждения, вызывающие потерю поглощающим аппаратом упругих свойств, о чем свидетельствует наличие зазора между упорными угольниками и упорной плитой или корпусом аппарата (при поглощающем аппарате 73 ZW указанный суммарный зазор допускается не более 5 мм);
е) зазор между потолком розетки и хвостовиком корпуса автосцепки менее 25 мм (для центрирующего прибора с жесткой опорой);
ж) выход вкладышей крепления крышки поглощающего аппарата Ш-6-ТО-4 за наружные плоскости боковых стенок корпуса;
з) ход более 70 мм поглощающего аппарата, установленного на вагоны с розеткой старой конструкции, имеющей длину выступающей части 185 мм;