ВУЗ: Не указан
Категория: Не указан
Дисциплина: Не указана
Добавлен: 09.11.2023
Просмотров: 440
Скачиваний: 2
СОДЕРЖАНИЕ
2.2 Производственная программа выпуска деталей. Тип производства
2.3 Анализ технологичности конструкции детали
2.4 Выбор и обоснование метода получения заготовки
2.5 Определение конструкторского и технологического кода детали
2.6 Разработка технологического процесса изготовления детали
3.1 Исходные данные для расчета
3.2 Расчет капитальных вложений
3.3 Расчет производственной площадки
3.4 Расчёт потребности в основных материалах и затрат на них
3.5 Расчет кол-ва промышленно – производственного персонала
3.5 Расчёт плановых фондов заработной платы (ФЗП)
3.6 Расчёт плановых фондов оплаты труда основных рабочих
3.7 Расчет себестоимости по статьям калькуляции единицы продукции
3.9 Технико-экономические показатели деятельности предприятия
4.1 Цели и задачи охраны труда
4.2 Положение о проведении обучения, инструктажей и обучение безопасным приемам труда
– установку на станке тяжелых деталей и снятие их производить грузоподъемными механизмами (кран-блок и пр.) При переноске больших тяжестей пользоваться тележкой;
– при обработке изделий образующуюся мелкую стружку удалять со станка щеткой, а не рукой, сливную стружку в виде ленты отводить от резца специальным крепком;
– при обработке изделий из хрупких металлов (чугун, бронза т.п.) надевать предохранительные очки для защиты отлетающих частичек стружки;
– при обработке пруткового материала и валов, находящихся вне шпинделя, пруток, вал ограждать специальной трубкой, трубку укреплять неподвижно на станке;
– при зачистке вращающего изделия напильником, шабром и шкуркой быть особо осторожным во избежание захвата рукавов одежды кулачком патрона или хомутика;
– перед тем, как приступить к зачистке изделия или установке его в патроне, отвести суппорт, а также заднюю бабку вправо, как можно дальше, чтобы не повредить руки о резец;
– если в процессе работы станка под резец попал какой-либо посторонний предмет, то удаление его производить лишь после полной остановки станке и отвода суппорта от изделия;
– выверку изделия, укрепленного в планшайбе, производить мелком, закрепленным в державке, а не держать мелок в руке;
– охлаждение деталей и режущего инструмента производить при помощи специальных приспособлений;
– рабочее место должно быть хорошо освещено (45 люкс), содержаться в чистоте и не загромождаться изделиями и посторонними предметами;
– необходимый ручной инструмент всегда должен быть в исправности и храниться в надлежащем порядке на рабочем месте или тумбочке;
– пользоваться защитными средствами: от горячей стружки стружколомателями, стружкозабирателями и защитными экранами или пользоваться очками, если при работе возможно повреждение глаз отделяющейся стружкой;
– при подрезании торцов и уступов следует обращать внимание на прочность закрепления детали в патроне, недостаточное прочное закрепление детали может привести к вырву ее из патрона и причинить повреждение токарю. При поддержании торце или уступа близко расположенного к кулачкам патрона нужно быть особенно внимательным во избежание возможного захвата одежды и ранения токаря кулачками;
– при обработке цилиндрически поверхностей следует срочно закреплять детали в резец. нельзя работать с изношенными центрами во избежание, чтобы детали не могли вырваться из центров;
– следует быть особенно внимательными и осторожными при зачистке детали шкуркой или напильником. Следить, чтобы напильник не соскользнул с обрабатываемой детали;
– не следует пользоваться при установке резца по высоте центра к всякого рода не приспособленными для этого подкладками. Под действием давления стружек подкладки и резец могут выскочить и поранить токаря;
– при установке, снятии и изменении обрабатываемого изделия, при смене патрона и изделия, отодвигать дальше заднюю бабку станка;
– не брать и не подавать что-либо через станок во время его работы;
– обязательно останавливать станок:
а) при уходе от станка на короткое время;
б) при временном прекращении работы;
в) при уборке, смазке, чистке, наладке станка;
г) при ремонте станка, установки, регулировки и смени инструмента и обрабатываемых изделий;
д) для подтягивания болтов, гаек; клиньев и других соединений;
е) для регулировки зажимных приспособлений станка (крепежных болтов, кулаков и т.п.);
ж) для измерения обрабатываемых деталей;
з) для установки и снятия деталей и приспособлений; патронов;
и) для удаления стружки и инструмента, патрона, обрабатываемого изделия:
к) для проверки чистоты обработки детали.
– перед заточкой инструмента на наждаке проверить: испытан ли заточный круг на прочность, имеется ли об этом отметка на круге, нет, ли на ней выбоин и трещин.
– наждак должен закрываться предохранительным кожухом, иметь экран и подручник, расстояние между подручником и кругом не должно превышать 3-х мм. подручник не должен иметь выбоин.
– при заточке резца, подавай резец на круг без рывка резкого нажима, предохраняя круг от ударов и толчков.
– следить, чтобы освещение на рабочем месте было достаточно, а осветительная сеть у рабочего места исправная.
– немедленно сообщить начальнику РМЦ и дежурному электромонтеру о замеченной неисправности: искры, вспышки в электрических устройствах, о повреждении изоляции в электропроводах, об неизолированных открытых токоведущих частях.
Запрещается:
– работать на станке с неправильно выполненными или изношенными центровыми отверстиями и центрами. При неустойчивом креплении
изделия и отсутствии оградительных приспособлений;
– производить во время работы станка наладку, установку, снимать, измерять или проверять обрабатываемое изделие и режущий инструмент, передавать или принимать через станок какие-либо предметы;
– крепить изделия неисправными зажимными приспособлениям, а также пользоваться поврежденным и не имеющим рукояток инструментом (напильники, шабер и др.);
– курить и зажигать огонь при обработке сплавов, содержащих магнит, а также при применении горючих жидкостей;
– производить какой-либо ремонт электроборудования;
– останавливать станок прижатием руки на патроне, обрабатываемую деталь или шкив;
– работать на станке в расстегнутой одежде с не заправленным галстуком и распущенными волосами;
– оставлять рабочий станок без присмотра, а также поручить работу на нем другим лицам.
После работы:
– очистить станок и рабочее место;
– положить инструмент на постоянное место хранения;
– заявить мастеру или начальнику цеха о замеченных неполадках в работе станка;
– сдать станок сменщику и предупредить его о всех «даже малейших неисправностях станка».
4.4 Защита от вибрации
Вибрация – упругие механические колебания малой амплитуды.
Амплитуда – максимальное значение смещения или изменения переменной величины от среднего значения при колебательном или волновом движении.
Амплитуда скорости вибрации (виброскорости) Vm может быть определена по формуле:
Vm =
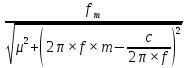
где fm — амплитуда возмущающей вибросилы, Н;
μ — коэффициент сопротивления, Н∙с/м;
f — частота вибрации, Гц;
m — масса системы, кг;
с — коэффициент жесткости системы, Н/м
На основе анализа формулы можно сделать следующие выводы: для уменьшения виброскорости Vm необходимо снижать силу Fm (снижать виброактивность машины) и увеличивать знаменатель, а именно — повышать сопротивление системы μ и не допускать, чтобы 2πfm = c/2πf. При равенстве этих членов наступает явление резонанса, и уровень вибрации резко возрастает.
Таким образом, для защиты от вибрации необходимо применять следующие методы:
а) снижение виброактивности машин (уменьшение силы Fm);
б) отстройка от резонансных частот (2πfm ≠ с/2πf);
в) вибродемпфирование (увеличение μ);
г) виброгашение (увеличение m) — для высоких и средних частот;
д) повышение жесткости системы (увеличение с) — для низких и средних частот;
е) виброизоляция;
ж) применение индивидуальных средств защиты.
Снижение виброактивности машин (уменьшение силы Fm) достигается изменением технологического процесса, применением машин с такими кинематическими схемами, при которых динамические процессы, вызываемые ударами, резкими ускорениями и т. п. были бы исключены или предельно снижены (например, замена клепки сваркой); хорошей динамической и статической балансировкой механизмов, смазкой и чистотой обработки взаимодействующих поверхностей; применением кинематических зацеплений пониженной виброативности (например, использование шевронных и косозубых зубчатых колес вместо прямозубых); заменой подшипников качения на подшипники скольжения; применением конструкционных материалов с повышенным внутренним трением.
Отстройка от резонансных частот (2πfm ≠ с/2πf) заключается в изменении режимов работы машины и соответственно частоты возмущающей вибросилы; собственной частоты колебаний машины путем изменения жесткости системы с (например, установка ребер жесткости) или изменения массы m системы (например, закрепление на машине дополнительных масс).
Виброгашение (увеличение m) осуществляют путем установки агрегатов на массивный фундамент (рисунок 6)
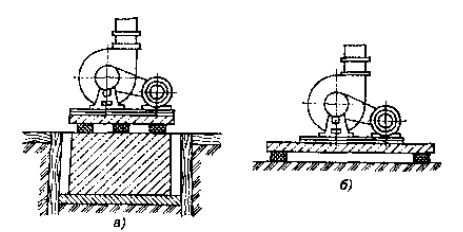
Виброгашение наиболее эффективно при средних и высоких частотах вибрации. Этот способ нашел широкое применение при установке тяжелого оборудования (молотов, прессов, вентиляторов, насосов и т. п.).
Одним из способов подавления вибраций является установка динамических виброгасителей.
Схема динамического виброгасителя показана на рисунке 7.
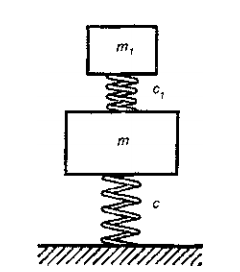
Рисунок 7 – Схема динамического виброгасителя
Динамический виброгаситель крепится на вибрирующем агрегате, поэтому в нем в каждый момент времени возбуждаются колебания, находящиеся в противофазе с колебаниями агрегата. Недостатком динамического виброгасителя является то, что он подавляет колебания только определенной частоты, соответствующей его собственной. Такие виброгасители применяют в агрегатах, например, турбогенераторах, имеющих характерный, постоянный во времени дискретный спектр вибрации. На рисунке 8 изображен динамический виброгаситель с двумя степенями свободы, и схема установки виброгасителя на турбогенераторе. Грузики перемещаются по резьбе и фиксируются гайками. Это позволяет менять жесткость виброгасителя, а, следовательно, его собственную частоту и частоту подавляемых вибраций. Такие виброгасители удобно настраивать на заданную частоту.
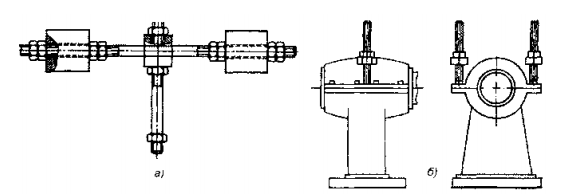
Рисунок 8 — динамический гаситель с двумя степенями свободы для дизель-генератора; б — схема турбоагрегата с динамическим виброгасителем
Повышение жесткости системы (увеличение с), например, путем установки ребер жесткости. Как видно из формулы этот способ эффективен только при низких частотах и в ряде случаев средних.