Добавлен: 22.11.2023
Просмотров: 140
Скачиваний: 2
ВНИМАНИЕ! Если данный файл нарушает Ваши авторские права, то обязательно сообщите нам.
, высота его торца или очертания верхнего и нижнего плеч не соответствуют шаблону 800р-1;
в) имеется трещина.
Наличие изгиба предохранителя определяют, пропуская его в вырезы а и б шаблона 800р-1 (рис. 16). Если предохранитель не проходит в вырезы, то его надо выправить. Пропуская предохранитель через вырез а, надевают его отверстием на шип 7, укрепленный в обойме 2, до упора в основание. Предохранитель годен, если он свободно проходит через вырез в листе шаблона и располагается заподлицо с верхней плоскостью листа или ниже ее.
Рис. 16
После ремонта предохранитель проверяют шаблоном 800р-1, как указано выше.
Подъемник замка
Подъемник замка признают неисправным и направляют в ремонт, если любой из его проверяемых размеров не соответствует требованиям проверки шаблоном 847р (рис. 17), и исправным, если:
а) подъемник, надетый на пробку 2, входит в обойму 5;
б) проходит в вырез 7;
в) буртиком входит в вырез б;
г) отверстием не надевается на пробку 7;
д) надетый на пробку 3, не подходит широким пальцем под шляпку стойки 4, а узким пальцем проходит мимо проходной части сухаря 8 и не проходит мимо непроходной. После ремонта подъемник замка проверяют шаблоном 847р, как указано выше.
Рис. 17
Валик подъемника
Валик подъемника признают неисправным и направляют в ремонт, если любой из его проверяемых размеров не соответствует требованиям проверки шаблоном 919р (рис. 18), и исправным, если:
Рис. 18
а) цилиндрические части стержня проходят в соосно расположенные большое 2 и малое 7 кольца шаблона и вращаются в них;
б) стержень валика не проходит цилиндрической частью большего диаметра в вырез 8, а меньшего диаметра - в вырез 7;
в) цилиндрическая часть большего диаметра не проходит по длине в вырез б и проходит в вырез 4;
г) паз для крепящего болта, установленный на контрольный буртик 3, полностью закрывает его;
д) квадратная часть стержня проходит в отверстие 5 и не проходит в вырез 7.
После ремонта валик подъемника проверяют шаблоном 919р, как указано выше.
Выявление изгибов
Погнутый хвостовик автосцепки должен быть выправлен в том случае, если его изгиб г (рис. 19), измеряемый от первоначальной продольной оси корпуса в средней части, превышает 3 мм.
Рис. 19
Разметка корпуса для определения изгиба в горизонтальной плоскости производится, как показано на рис. 13, а. Сначала находят и обозначают середину хвостовика на расстоянии 20 мм от упора головы, а также на торце и в средней части. После этого соединяют линией точки, обозначающие середину хвостовика в начале и в конце. Изгиб определяют как отклонение указанной линии от середины хвостовика в его средней части. Изгиб г в вертикальной плоскости отсчитывают в средней части хвостовика от первоначальной продольной оси корпуса, которая является продолжением литейного шва на большом зубе. Не разрешается выправлять хвостовик автосцепки с заваренными или незаваренными трещинами в зоне выправляемых мест.
Трещины в хвостовике корпуса автосцепки глубиной до 5 мм допускается вырубать с плавным переходом на литейную поверхность без последующей заварки. Мелкие трещины (сетчатые) глубиной не более 8 мм в перемычке хвостовика разрешается вырубать с последующей заваркой при условии, что после их вырубки толщина перемычки будет не менее 40 мм.
Сварочные работы. Корпус автосцепки
•Заварка вертикальных трещин 1 сверху и снизу в зеве со стороны большого зуба в углах, образованных ударной стенкой зева и боковой стенкой большого зуба. (Рис. 20).
Рис. 20
Разрешается заварка, если после разделки трещины не выходят на горизонтальные плоскости наружных ребер большого зуба. Повторные трещины, образовавшиеся по ранее выполненному шву, можно разделывать длиной на 5—8 мм больше чем длина выполненной заварки. Ранее наплавленный металл должен быть удален. Перед заваркой подготовленных трещин производить предварительный местный подогрев до температуры 250—300° С. В случае длительного перерыва и остывания места сварки ниже температуры 250° С следует повторно подогреть. •Наплавка изношенных поверхностей 2 (Рис. 20) по контуру зацепления. Граница наплавленного металла должна быть на расстоянии 15 мм от закруглений в углах зева и иметь плавный переход к изнашиваемым поверхностям на длине 15 мм, а также твердость не менее НВ 250. Твердость металла для изотермических и пассажирских вагонов должна быть не менее НВ 450. Для получения металла такой твердости рекомендуется использовать электроды ОЗН – 400, порошковую проволоку. ППТН500, пластинчатые электроды с применением легирующих присадок по технологии ВНИИЖТа. Заварка трещин 3 (Рис. 20) в хвостовике корпуса.
Трещины глубиной более 5мм заваривают при условии, что после разделки поперечное сечение стенок хвостовика не уменьшается более чем на 25%. •Наплавка перемычек хвостовика со стороны прилегания клина 5 и с торца 6. Толщина перемычек перед наплавкой для автосцепки СА-3 не менее 40 мм. При наплавке должны использоваться электроды УОНИ-13/85. •Наплавка боковых стенок отверстия 4 (Рис. 20) для клина тягового хомута. Наплавляют при износе более 3 мм, но не более 8 мм с последующей механической обработкой заподлицо с основным металлом. •Заварка трещин в углах окон 7 (Рис. 20) для замка и замкодержателя.
Разделка трещин в верхних углах окна для замка не должна выходить на горизонтальную поверхность головы, в верхнем углу окна для замкодержателя — за положение верхнего ребра со стороны большого зуба, а длина разделанной трещины в нижних углах для замка и замкодержателя не должна превышать 20 мм. При заварке трещин требуется дополнительный местный подогрев головы автосцепки до температуры 250— 300° С. Если заваривают трещины непосредственно после разделки, дополнительно подогревать не нужно. Не допускается разделывать трещины воздушно-дуговым способом угольным электродом. •Наплавка полочки 9 (Рис. 20) поддерживающей верхнее плечо предохранителя, или приварка новой полочки. Перед приваркой полочку закрепляют в правильном положении при помощи специального кондуктора. Со стороны вершины угла разделки обязательно следует подваривать. •Наплавка поверхности хвостовика по месту 10 (Рис. 20) прилегания к центрирующей балочке.
Наплавляют при износе от 3 до 8 мм. •Заварка трещин 11 (Рис. 20) перемычки между отверстием для сигнального отростка замка и отверстием для направляющего зуба замка.
Разрешается заваривать, если трещина не выходит на вертикальную стенку кармана. •Наплавка шипа для навешивания замкодержателя. Перед наплавной требуется дополнительный местный подогрев. •Наплавка изношенных стенок 12 (Рис. 20) отверстия валика подъемника. Разрешается при всех ремонта.
Замок
•Наплавка изношенной замыкающей поверхности 1 (Рис. 21) замка. Твердость наплавленного металла должна быть не менее НВ 250. Изношенные поверхности замков автосцепок рефрижераторных и пассажирских вагонов должны после механической обработки закаливаться до твердости НВ 400—450.
•Приварка шипа 2 (Рис. 21) для навешивания предохранителя или наплавка изношенной его части. После наплавки производят механическую обработку до чертежных размеров. •Наплавка задней кромки 3 (Рис. 21) овального отверстия для валика. Износ не должен превышать более 8 мм. •Приварка отломавшегося сигнального отростка 4 (Рис. 21) замка. Применяют электроды типа Э42А или Э46.
Рис. 21
•Наплавка изношенной радиальной опоры и направляющего зуба 5 (Рис. 21). Применяют электроды марки УОНИ-13/85 или порошковую проволоку марки ПП-ТН250. •Наплавка изношенных мест 6 (Рис. 21) нижней части замка. Применяют электроды марки УОНИ-13/85 или порошковую проволоку марки ПП-ТН250.
Замкодержатель
•Заварка трещин 1 (Рис. 22) в замкодержателе. Допускается заваривать только одну трещину. •Наплавка изношенных частей 2 (Рис. 22) замкодержателя. Рекомендуется электроды марки УОНИ-13/85 или порошковая проволока марки ПП-ТН250.
Рис. 22
Предохранитель замка
•Наплавка изношенных поверхностей 1 (Рис. 23). Наплавляют при любом износе.
Предохранитель, отлитый из стали Г13ФЛ ремонту сваркой не подлежит.
Рис. 23
•Заварка изношенного отверстия 2 (Рис. 23) предохранителя. Величина разработки не ограничивается.
Подъемник замка.
•Наплавка изношенных поверхностей 1 (Рис. 24) подъемника. Износ не ограничивается.
Рис. 24
Валик подъемника
•Наплавка изношенных поверхностей 1 (Рис. 25).
Рекомендуется электроды марки УОНИ-13/85 или порошковая проволока марки ПП-ТН250.
Рис. 25
Механическая обработка
Обработка наплавленных поверхностей деталей автосцепки производится с применением фрезерных, строгальных станков, шлифовальных машинок и специализированной оснастки до альбомных размеров.
Клеймение и окраска
После ремонта и проверки шаблонами на замок, замкодержатель, предохранитель, подъемник, валик подъемника, собранную автосцепку, ставят клейма. Клейма на деталях ставят в определенных местах. Например, на собранной автосцепке клеймо должно быть расположено на расстоянии 180 мм от упора и на 80 мм от верха головы корпуса. Все старые клейма должны быть зачищены. Клеймо состоит из номера ремонтного пункта и даты ремонта цифрами высотой не менее 6 мм на глубину 0,25 мм (например, клейм не допускается. После приемки детали автосцепного устройства окрашивают черной краской, за исключением внутренних поверхностей зева корпуса и поглощающего аппарата, а также деталей механизма. Сигнальный отросток замка должен быть окрашен в красный цвет. Не допускается смазывать детали механизма автосцепки и поверхности трения поглощающих аппаратов.
Проверка.
Контур зацепления собранной автосцепки проверяют проходным шаблоном 828р, при этом лапу замкодержателя вжимают заподлицо с ударной поверхностью зева корпуса. Шаблон должен свободно проходить по всей высоте головы автосцепки. Проверку действия механизма автосцепки выполняют в следующем порядке: проверяют действие предохранителя замка от саморасцепа; убеждаются в отсутствии преждевременного включения предохранителя; контролируют обеспечение удержания механизма в расцепленном положении; выявляют возможность расцепления сжатых автосцепок (т. е. когда лапа замкодержателя прижата заподлицо с ударной стенкой зева); проверяют уход замка от вертикальной кромки малого зуба при включенном предохранителе; контролируют расстояние от вертикальной кромки малого зуба до кромки замка в его нижнем свободном положении и от кромки замка до кромки лапы замкодержателя по горизонтали; проверяют положение лапы замкодержателя относительно ударной стенки зева, когда замок находится в заднем крайнем положении.
Схема технологического процесса
2.4 Качество работы участка, показатели качества продукции вагонного депо. Организация технического контроля
Современная рыночная экономика предъявляет принципиально иные по сравнению с централизованной экономикой требования к качеству выпускаемой продукции. Выживаемость организации, ее устойчивое положение на рынке транспортных услуг определяется уровнем конкурентоспособности. В свою очередь конкурентоспособность связана с двумя показателями уровнем цены и уровнем качества продукции, причем второй фактор в связи с созданием конкурентной среды вагоноремонтных организаций постепенно выходит на первое место.
Качество — это авторитет организации, увеличение прибыли, рост процветания, и работа по управлению качеством — главная задача всего персонала — от руководителя до конкретного исполнителя.
Качество продукции важнейший показатель вагонного депо. Повышение качества ремонта вагонов в значительной мере определяется ростом эффективности производства, экономией всех видов ресурсов, используемых в депо.
Качество — это совокупность свойств продукции, обусловливающих ее пригодность удовлетворять определенные потребности в соответствии с ее назначением.
в) имеется трещина.
Наличие изгиба предохранителя определяют, пропуская его в вырезы а и б шаблона 800р-1 (рис. 16). Если предохранитель не проходит в вырезы, то его надо выправить. Пропуская предохранитель через вырез а, надевают его отверстием на шип 7, укрепленный в обойме 2, до упора в основание. Предохранитель годен, если он свободно проходит через вырез в листе шаблона и располагается заподлицо с верхней плоскостью листа или ниже ее.
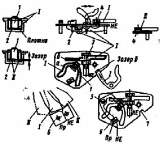
Рис. 16
После ремонта предохранитель проверяют шаблоном 800р-1, как указано выше.
Подъемник замка
Подъемник замка признают неисправным и направляют в ремонт, если любой из его проверяемых размеров не соответствует требованиям проверки шаблоном 847р (рис. 17), и исправным, если:
а) подъемник, надетый на пробку 2, входит в обойму 5;
б) проходит в вырез 7;
в) буртиком входит в вырез б;
г) отверстием не надевается на пробку 7;
д) надетый на пробку 3, не подходит широким пальцем под шляпку стойки 4, а узким пальцем проходит мимо проходной части сухаря 8 и не проходит мимо непроходной. После ремонта подъемник замка проверяют шаблоном 847р, как указано выше.
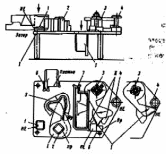
Рис. 17
Валик подъемника
Валик подъемника признают неисправным и направляют в ремонт, если любой из его проверяемых размеров не соответствует требованиям проверки шаблоном 919р (рис. 18), и исправным, если:
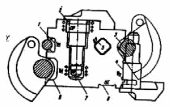
Рис. 18
а) цилиндрические части стержня проходят в соосно расположенные большое 2 и малое 7 кольца шаблона и вращаются в них;
б) стержень валика не проходит цилиндрической частью большего диаметра в вырез 8, а меньшего диаметра - в вырез 7;
в) цилиндрическая часть большего диаметра не проходит по длине в вырез б и проходит в вырез 4;
г) паз для крепящего болта, установленный на контрольный буртик 3, полностью закрывает его;
д) квадратная часть стержня проходит в отверстие 5 и не проходит в вырез 7.
После ремонта валик подъемника проверяют шаблоном 919р, как указано выше.
Выявление изгибов
Погнутый хвостовик автосцепки должен быть выправлен в том случае, если его изгиб г (рис. 19), измеряемый от первоначальной продольной оси корпуса в средней части, превышает 3 мм.
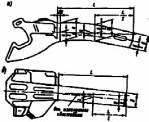
Рис. 19
Разметка корпуса для определения изгиба в горизонтальной плоскости производится, как показано на рис. 13, а. Сначала находят и обозначают середину хвостовика на расстоянии 20 мм от упора головы, а также на торце и в средней части. После этого соединяют линией точки, обозначающие середину хвостовика в начале и в конце. Изгиб определяют как отклонение указанной линии от середины хвостовика в его средней части. Изгиб г в вертикальной плоскости отсчитывают в средней части хвостовика от первоначальной продольной оси корпуса, которая является продолжением литейного шва на большом зубе. Не разрешается выправлять хвостовик автосцепки с заваренными или незаваренными трещинами в зоне выправляемых мест.
Трещины в хвостовике корпуса автосцепки глубиной до 5 мм допускается вырубать с плавным переходом на литейную поверхность без последующей заварки. Мелкие трещины (сетчатые) глубиной не более 8 мм в перемычке хвостовика разрешается вырубать с последующей заваркой при условии, что после их вырубки толщина перемычки будет не менее 40 мм.
Сварочные работы. Корпус автосцепки
•Заварка вертикальных трещин 1 сверху и снизу в зеве со стороны большого зуба в углах, образованных ударной стенкой зева и боковой стенкой большого зуба. (Рис. 20).
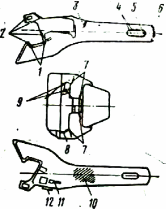
Рис. 20
Разрешается заварка, если после разделки трещины не выходят на горизонтальные плоскости наружных ребер большого зуба. Повторные трещины, образовавшиеся по ранее выполненному шву, можно разделывать длиной на 5—8 мм больше чем длина выполненной заварки. Ранее наплавленный металл должен быть удален. Перед заваркой подготовленных трещин производить предварительный местный подогрев до температуры 250—300° С. В случае длительного перерыва и остывания места сварки ниже температуры 250° С следует повторно подогреть. •Наплавка изношенных поверхностей 2 (Рис. 20) по контуру зацепления. Граница наплавленного металла должна быть на расстоянии 15 мм от закруглений в углах зева и иметь плавный переход к изнашиваемым поверхностям на длине 15 мм, а также твердость не менее НВ 250. Твердость металла для изотермических и пассажирских вагонов должна быть не менее НВ 450. Для получения металла такой твердости рекомендуется использовать электроды ОЗН – 400, порошковую проволоку. ППТН500, пластинчатые электроды с применением легирующих присадок по технологии ВНИИЖТа. Заварка трещин 3 (Рис. 20) в хвостовике корпуса.
Трещины глубиной более 5мм заваривают при условии, что после разделки поперечное сечение стенок хвостовика не уменьшается более чем на 25%. •Наплавка перемычек хвостовика со стороны прилегания клина 5 и с торца 6. Толщина перемычек перед наплавкой для автосцепки СА-3 не менее 40 мм. При наплавке должны использоваться электроды УОНИ-13/85. •Наплавка боковых стенок отверстия 4 (Рис. 20) для клина тягового хомута. Наплавляют при износе более 3 мм, но не более 8 мм с последующей механической обработкой заподлицо с основным металлом. •Заварка трещин в углах окон 7 (Рис. 20) для замка и замкодержателя.
Разделка трещин в верхних углах окна для замка не должна выходить на горизонтальную поверхность головы, в верхнем углу окна для замкодержателя — за положение верхнего ребра со стороны большого зуба, а длина разделанной трещины в нижних углах для замка и замкодержателя не должна превышать 20 мм. При заварке трещин требуется дополнительный местный подогрев головы автосцепки до температуры 250— 300° С. Если заваривают трещины непосредственно после разделки, дополнительно подогревать не нужно. Не допускается разделывать трещины воздушно-дуговым способом угольным электродом. •Наплавка полочки 9 (Рис. 20) поддерживающей верхнее плечо предохранителя, или приварка новой полочки. Перед приваркой полочку закрепляют в правильном положении при помощи специального кондуктора. Со стороны вершины угла разделки обязательно следует подваривать. •Наплавка поверхности хвостовика по месту 10 (Рис. 20) прилегания к центрирующей балочке.
Наплавляют при износе от 3 до 8 мм. •Заварка трещин 11 (Рис. 20) перемычки между отверстием для сигнального отростка замка и отверстием для направляющего зуба замка.
Разрешается заваривать, если трещина не выходит на вертикальную стенку кармана. •Наплавка шипа для навешивания замкодержателя. Перед наплавной требуется дополнительный местный подогрев. •Наплавка изношенных стенок 12 (Рис. 20) отверстия валика подъемника. Разрешается при всех ремонта.
Замок
•Наплавка изношенной замыкающей поверхности 1 (Рис. 21) замка. Твердость наплавленного металла должна быть не менее НВ 250. Изношенные поверхности замков автосцепок рефрижераторных и пассажирских вагонов должны после механической обработки закаливаться до твердости НВ 400—450.
•Приварка шипа 2 (Рис. 21) для навешивания предохранителя или наплавка изношенной его части. После наплавки производят механическую обработку до чертежных размеров. •Наплавка задней кромки 3 (Рис. 21) овального отверстия для валика. Износ не должен превышать более 8 мм. •Приварка отломавшегося сигнального отростка 4 (Рис. 21) замка. Применяют электроды типа Э42А или Э46.
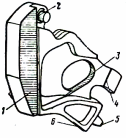
Рис. 21
•Наплавка изношенной радиальной опоры и направляющего зуба 5 (Рис. 21). Применяют электроды марки УОНИ-13/85 или порошковую проволоку марки ПП-ТН250. •Наплавка изношенных мест 6 (Рис. 21) нижней части замка. Применяют электроды марки УОНИ-13/85 или порошковую проволоку марки ПП-ТН250.
Замкодержатель
•Заварка трещин 1 (Рис. 22) в замкодержателе. Допускается заваривать только одну трещину. •Наплавка изношенных частей 2 (Рис. 22) замкодержателя. Рекомендуется электроды марки УОНИ-13/85 или порошковая проволока марки ПП-ТН250.
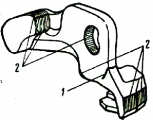
Рис. 22
Предохранитель замка
•Наплавка изношенных поверхностей 1 (Рис. 23). Наплавляют при любом износе.
Предохранитель, отлитый из стали Г13ФЛ ремонту сваркой не подлежит.
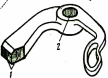
Рис. 23
•Заварка изношенного отверстия 2 (Рис. 23) предохранителя. Величина разработки не ограничивается.
Подъемник замка.
•Наплавка изношенных поверхностей 1 (Рис. 24) подъемника. Износ не ограничивается.
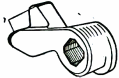
Рис. 24
Валик подъемника
•Наплавка изношенных поверхностей 1 (Рис. 25).
Рекомендуется электроды марки УОНИ-13/85 или порошковая проволока марки ПП-ТН250.
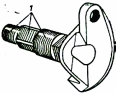
Рис. 25
Механическая обработка
Обработка наплавленных поверхностей деталей автосцепки производится с применением фрезерных, строгальных станков, шлифовальных машинок и специализированной оснастки до альбомных размеров.
Клеймение и окраска
После ремонта и проверки шаблонами на замок, замкодержатель, предохранитель, подъемник, валик подъемника, собранную автосцепку, ставят клейма. Клейма на деталях ставят в определенных местах. Например, на собранной автосцепке клеймо должно быть расположено на расстоянии 180 мм от упора и на 80 мм от верха головы корпуса. Все старые клейма должны быть зачищены. Клеймо состоит из номера ремонтного пункта и даты ремонта цифрами высотой не менее 6 мм на глубину 0,25 мм (например, клейм не допускается. После приемки детали автосцепного устройства окрашивают черной краской, за исключением внутренних поверхностей зева корпуса и поглощающего аппарата, а также деталей механизма. Сигнальный отросток замка должен быть окрашен в красный цвет. Не допускается смазывать детали механизма автосцепки и поверхности трения поглощающих аппаратов.
Проверка.
Контур зацепления собранной автосцепки проверяют проходным шаблоном 828р, при этом лапу замкодержателя вжимают заподлицо с ударной поверхностью зева корпуса. Шаблон должен свободно проходить по всей высоте головы автосцепки. Проверку действия механизма автосцепки выполняют в следующем порядке: проверяют действие предохранителя замка от саморасцепа; убеждаются в отсутствии преждевременного включения предохранителя; контролируют обеспечение удержания механизма в расцепленном положении; выявляют возможность расцепления сжатых автосцепок (т. е. когда лапа замкодержателя прижата заподлицо с ударной стенкой зева); проверяют уход замка от вертикальной кромки малого зуба при включенном предохранителе; контролируют расстояние от вертикальной кромки малого зуба до кромки замка в его нижнем свободном положении и от кромки замка до кромки лапы замкодержателя по горизонтали; проверяют положение лапы замкодержателя относительно ударной стенки зева, когда замок находится в заднем крайнем положении.
Схема технологического процесса
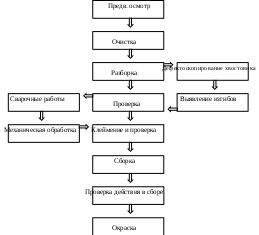
2.4 Качество работы участка, показатели качества продукции вагонного депо. Организация технического контроля
Современная рыночная экономика предъявляет принципиально иные по сравнению с централизованной экономикой требования к качеству выпускаемой продукции. Выживаемость организации, ее устойчивое положение на рынке транспортных услуг определяется уровнем конкурентоспособности. В свою очередь конкурентоспособность связана с двумя показателями уровнем цены и уровнем качества продукции, причем второй фактор в связи с созданием конкурентной среды вагоноремонтных организаций постепенно выходит на первое место.
Качество — это авторитет организации, увеличение прибыли, рост процветания, и работа по управлению качеством — главная задача всего персонала — от руководителя до конкретного исполнителя.
Качество продукции важнейший показатель вагонного депо. Повышение качества ремонта вагонов в значительной мере определяется ростом эффективности производства, экономией всех видов ресурсов, используемых в депо.
Качество — это совокупность свойств продукции, обусловливающих ее пригодность удовлетворять определенные потребности в соответствии с ее назначением.