Файл: Содержание Раздел Общие характеристики судна 3 Раздел Общее устройство судна 6 Раздел Судовые энергетические установки 11 Раздел Вспомогательная котельная установка .docx
ВУЗ: Не указан
Категория: Не указан
Дисциплина: Не указана
Добавлен: 10.01.2024
Просмотров: 127
Скачиваний: 1
ВНИМАНИЕ! Если данный файл нарушает Ваши авторские права, то обязательно сообщите нам.
Основными видами износа и повреждений цилиндров и их втулок являются: износ рабочей поверхности; наработки в верхнем поясе; раковины, задиры, царапины и коррозийные повреждения на рабочей поверхности; вмятины и забоины на опорной поверхности цилиндровой втулки; разрушение поверхности, омываемой водой; разрушение и поломка посадочных поясков втулки. По результатам дефектации определяют необходимость растачивания втулки. Растачивание цилиндров производят на судне специальным переносным приспособлением либо в цехе на расточном станке.
При ремонте трещин на рубашке цилиндров (блоке цилиндров) применяют электродуговую сварку. Иногда трещины заделывают путем постановки ввертышей, а затем часто применяют сварку. Последовательность установки ввертышей показана на рис. 106. По концам трещин засверливают отверстия диаметром d, чтобы предотвратить распространение трещины дальше. Для изготовления ввертышей на латунном или медном прутке диаметром d1 (обычно d—d 1) нарезают резьбу. По всей длине трещины накернивают центры отверстий под ввертыши на расстоянии, равном диаметру ввертыша, сверлят отверстия, нарезают и устанавливают ввертыши. Затем последовательно сверлят, нарезают и устанавливают ввертыши, центрами отверстий которых являются середины расстояний между кромками двух рядом расположенных отверстий. Ввертыши устанавливают по всей длине трещины с перекрытием половины диаметра каждого смежного ввертыша. Поставленные на место ввертыши расклепывают и запиливают или заваривают и зачищают.
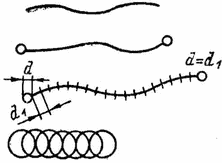
Рис. 1. Порядок заделки трещины ввертышами.
В настоящее время для заделки трещин и восстановления уплотнительных поясков в блоках цилиндров успешно применяют пластмассы на основе эпоксидных смол. На рис. показано восстановление уплотнительных поясков блока цилиндра с применением эпоксидных смол. Место, на которое будет наложена эпоксидная смола, тщательно очищают от ржавчины и отложений графита и обезжиривают. Затем в блоке цилиндра устанавливают распорное кольцо (желательно резиновое), между ним и поверхностью цилиндра прокладывают бумагу .
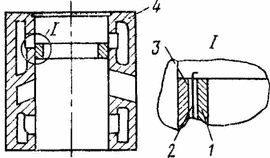
Рис. 2. Восстановление уплотнительных поясков блока цилиндров.
Эпоксидным составом заполняют восстанавливаемое место. По истечении 2 ч, когда начнется затвердевание состава, поверхность заглаживают стальной пластиной, смоченной водой. Через 6 ч кольцо и бумагу удаляют, восстановленный участок подчищают напильником и шабером. Через 12—20 ч состав затвердевает окончательно.
Ремонт пораженных коррозией нерабочих поверхностей втулок цилиндров состоит в их очистке и окраске суриком. Значительное разъедание втулок, раковины и свищи часто устраняют электрометаллизацией.
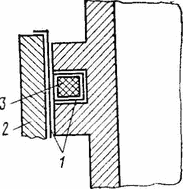
На рис. 2 показано восстановление посадочных поясков втулок цилиндров с помощью эпоксидных смол.
Выпрессованную из блока втулку тщательно очищают. В канавку укладывают с натягом специальное кольцо квадратного сечения, точно соответствующее размерам канавки; кольцо покрыто бумагой . Подготовленную для восстановления поверхность покрывают эпоксидным составом, в который добавлены соответствующие компоненты, и наносят состав на восстанавливаемый участок. Накладывают бумагу и надевают стяжной хомут из полосовой стали толщиной 0,5—1,0 мм с таким расчетом, чтобы он плотно обтянул втулку с резиновым кольцом. Установив хомут, уплотняют состав стальной пластиной.
Восстановление посадочных поясков втулок с помощью эпоксидных смол.
Ремонт втулок цилиндров при наличии задиров и царапин глубиной до 0,5 мм производят зачисткой их острых кромок шабером или шлифовальной машиной с наждачным кругом, а более глубокие дефекты устраняют расточкой; наработки устраняют этими же методами. После ремонта цилиндр и втулку испытывают гидравлическим давлением; величина давления принимается по таблице гидравлических испытаний.
Основными дефектами крышек цилиндров являются обгорание со стороны камеры сгорания при соприкосновении с горячими газами и разъедание со стороны полости охлаждения, а также появление трещин, обычно в перемычках между отверстиями для клапанов.
Обгоревшие места стальных крышек очищают до чистого металла, наплавляют электросваркой, отжигают и обрабатывают наплавленное место по шаблону, изготовленному из листовой стали. Этим же шаблоном пользуются для определения степени обгорания, прикладывая шаблон к дефектному месту и щупом замеряя зазор между ним и поверхностью обгоревшего места. Чугунные крышки с обгоревшими днищами заменяют новыми. Стальные крышки, имеющие трещины, ремонтируют электросваркой, чугунные — постановкой стяжек и ввертышей.
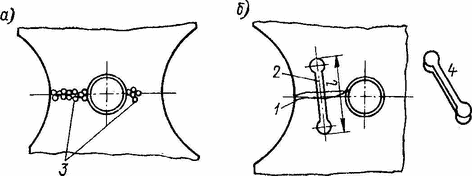
Рис. 3. Способы заделки трещин крышки цилиндра.
На рис.3, а показана постановка ввертышей по описанному выше способу; б — форма разделки паза для вкладыша . Паз разделывают перпендикулярно к трещине ; форма вкладыша соответствует форме паза, длина же вкладыша меньше длины паза на 1,0—1,5 мм. Перед постановкой вкладыш нагревают до 830—900° С, а трещину заполняют чугунной замазкой (25 частей мелких чугунных опилок, одна часть нашатыря и одна часть серного цвета). Нагретый вкладыш устанавливают в паз; остывая, вкладыш будет стягивать трещину. Нарушение форм гнезд для клапанов из-за нагара, обгорания или наклепа устраняют механической обработкой с последующей притиркой при сборке клапанов.
Центрирующий бурт крышки цилиндра может иметь забоины; их зачищают шабером, а при значительной глубине крышку заменяют новой. При прогорании бурта вследствие пропуска из-под него выпускных газов крышку бракуют. После устранения дефектов крышку цилиндра испытывают гидравлическим давлением на прочность.
Характерными дефектами вкладышей подшипников, залитых баббитом, являются: износ рабочих поверхностей, растрескивание, выкрашивание и отставание баббита, задиры, риски и выплавление баббита. Износ вкладышей подшипников выражается в увеличении масляного зазора, что приводит к ускорению износа трущихся пар при дальнейшей эксплуатации двигателя. Если величина зазора превышает допустимую, прибегают к уменьшению зазора, регулируя набор прокладок в разъемах вкладышей (подтяжка подшипников). В случае
невозможности регулировать зазоры прокладками, а также при появлении многочисленных трещин, отставания и выкрашивания баббита вкладыши перезаливают. Незначительные дефекты на рабочей поверхности устраняют подпайкой и зачисткой дефектных мест. Перезаливку вкладышей выполняет специалист-заливщик. После перезаливки вкладыша обрубают наплывы баббита, шабрят разъемы вкладыша, изготовляют временные прокладки в разъем, собирают обе половины вкладышей в хомут и передают на расточку. После расточки спинки вкладышей пригоняют по гнездам; при сборке двигателя рабочие поверхности вкладышей пришабривают по шейкам коленчатого вала. Вкладыши, залитые свинцовистой бронзой, не ремонтируют, а заменяют новыми. В случае необходимости замены хотя бы одного вкладыша заменяют весь комплект вкладышей на двигателе. Установка прокладок в разъеме вкладышей не допускается.
Дефектами коленчатых валов являются: износ шеек, задиры, риски, трещины на шейках и щеках, скручивание и изгиб вала, нарушение формы и увеличение диаметра отверстий для соединительных болтов фланцев, ослабление. посадки шеек в щеках у составных валов, поломки валов.
Если эллиптичность и конусность шеек вала превышают допустимые значения, а также при наличии глубоких задиров и царапин шейки обрабатывают на токарных станках проточкой и шлифованием.
При значительном износе шеек для восстановления их номинального размера иногда применяют электронаплавку и электрометаллизацию напылением. Последняя операция состоит в том, что металл, расплавленный электрической дугой и распыленный струей сжатого воздуха давлением 500—700 кН/м2 (0,5—0,7 кгс/см2), наносится в виде мельчайших частиц на поверхность детали. Движущиеся с большой скоростью частицы расплавленного металла, ударяясь о поверхность детали, расплющиваются и заполняют шероховатость, образуя наплавленный металлизацией слой. Металлизацию напыливанием производят с помощью специальных аппаратов — металлизаторов. После металлизации поверхность подлежит механической обработке. Иногда мотылевые шейки коленчатого вала обрабатывают опиливанием для придания им правильной цилиндрической формы. Опиливание осуществляют личными и бархатными напильниками с применением калибра.
Исправление деформированных отверстий для болтов во фланцах коленчатого вала
, состоящего из отдельных секций, производят одновременным развертыванием отверстий в сопрягаемых фланцах. При значительной деформации отверстия наплавляют, рассверливают, а затем совместно развертывают отверстия в сопрягаемых фланцах.
При нарушении плотности посадки шеек в щеках составных валов шейки выпрессовывают из посадочных мест, наплавляют ослабленные поверхности и обрабатывают до нужных размеров с последующей запрессовкой на места.
Дефектами распределительных валов и их кулачковых шайб являются: износ рабочих шеек валов, риски и задиры на шейках, прогиб вала, износ профильной части шайб и трещины на их поверхности.
При наличии эллиптичности и конусности шеек распределительных валов, рисок и задиров на них шейки протачивают и шлифуют до получения правильной цилиндрической формы; уменьшение диаметра шеек при этом допускается не более 3% номинального. Применяется хромирование шеек с последующей обработкой механическим способом.
Прогибы распределительных валов целесообразно устранять правкой в тех случаях, когда валы изготовлены за одно целое с кулачковыми шайбами. Валы со съемными шайбами при наличии этого дефекта заменяют новыми, так как изготовление новых валов в ряде случаев обходится дешевле, чем разборка и правка.
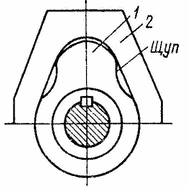
Рис. 4. Проверка износа кулачковых шайб.
Износ кулачковых шайб проверяют специальными шаблонами, изготовленными из листовой стали. Щупом (рис. 4) замеряют зазор между кулачковой шайбой и шаблоном ; допускаемый износ составляет 1—3 мм, при большем износе кулачковые шайбы наплавляют твердым сплавом с последующей механической обработкой по шаблону. При выкрашивании кромок или наличии трещин съемную кулачковую шайбу заменяют новой.
У тихоходных двигателей большой и средней мощности распределительные валы могут состоять из двух-трех частей, соединяемых на фланцах. Отверстия во фланцах могут быть деформированы; этот дефект устраняют совместным развертыванием отверстий сопрягаемых фланцев.
У шестерен распределительных валов часто встречаются такие дефекты, как ослабление посадки шестерен на валу, износ и поломка зубьев. Величину износа зубьев проверяют шаблоном и щупом: зазор между зубьями не должен превышать 0,10 мм, зазор между вершиной зуба одной шестерни и впадиной другой должен быть не менее 0,25 и не более 0,5 мм. Допускается увеличение зазора на 75—100%, при большем зазоре шестерни заменяют новыми.