Файл: Петровский. Автоматизация технологических процессов и производств.pdf
Добавлен: 15.11.2018
Просмотров: 7077
Скачиваний: 85
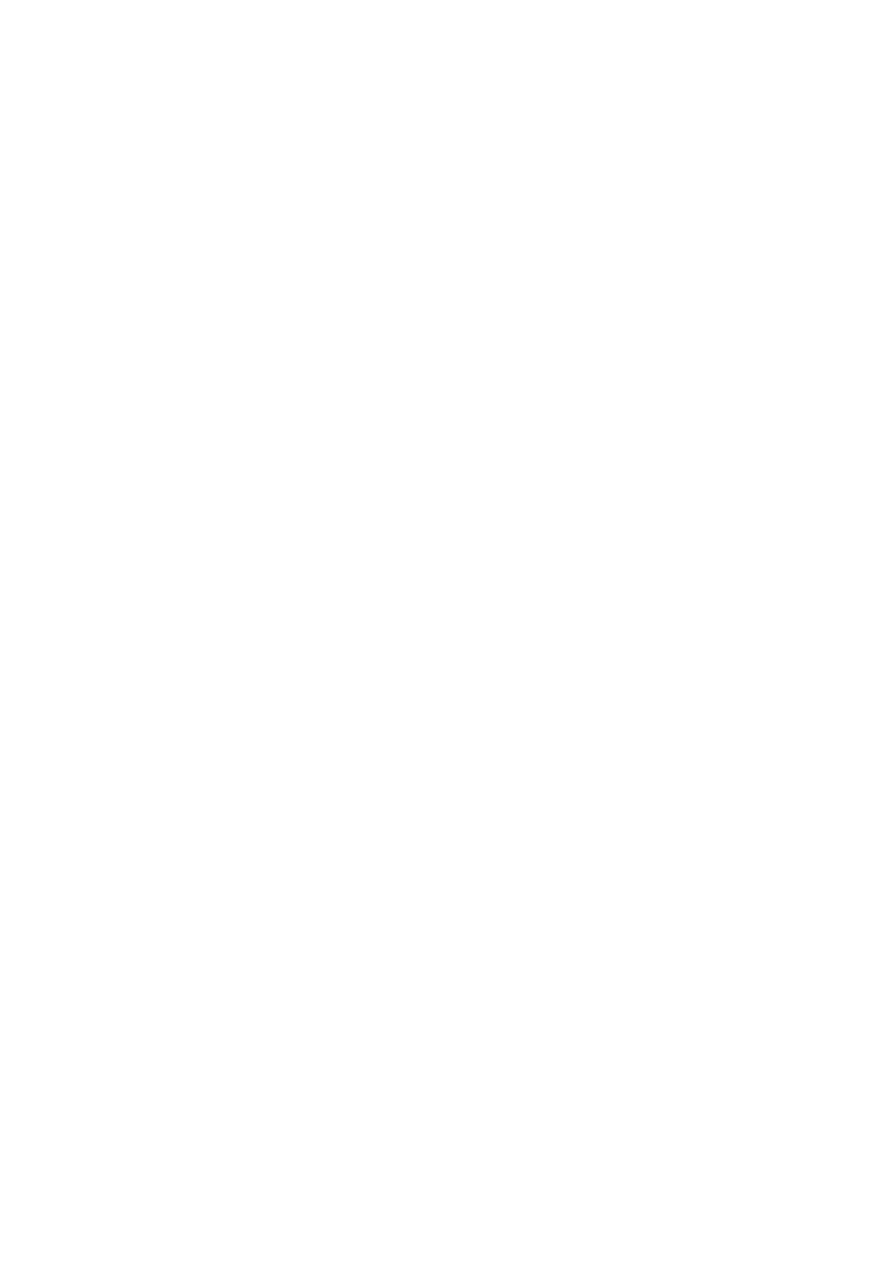
66
стема научных исследований (АСНИ); система автоматизированного проекти-
рования (САПР); автоматизированная система технологической подготовки
производства (АСТПП); автоматизированная система управления (АСУ).
Автоматизированная транспортно-складская система (АТСС) – сово-
купность взаимосвязанных автоматизированных складских и подъемно-
транспортных устройств для перемещения, ориентации и хранения предметов
труда и технологической оснастки в производственном процессе.
Автоматизированная система инструментального обеспечения (АСИО) –
совокупность взаимосвязанных автоматизированных средств, включающая
участки подготовки инструмента, устройства транспортирования, накопления,
смены и контроля качества, обеспечивающие подготовку, хранение, автомати-
ческую установку и замену инструмента. АСИО должна обеспечивать рацио-
нальное использование фонда машинного времени металлорежущих станков,
сокращение вспомогательного времени при их обслуживании, контроль и уход
за инструментом.
Автоматизированная система контроля (САК) – совокупность взаимо-
связанных автоматизированных средств активного и послеоперационного кон-
троля. Предпочтение должно отдаваться устройствам активного контроля,
обеспечивающим не только контроль состояния режущего инструмента, но и
контроль обрабатываемых заготовок.
Устройства автоматического поддержания точности должны обеспечивать
получение качественного изделия на данной стадии обработки, корректировать
положение режущего инструмента по мере его износа, контролировать измене-
ние размеров детали и выдавать необходимые сигналы в критических ситуаци-
ях. Устройства должны быть универсальными, т. е. обеспечивать контроль всех
операций, выполняемых на станке, иметь минимальные габаритные размеры,
размещаться в станке, а также иметь элементы настройки и регулирования.
Диагностический сигнал, формируемый устройством, должен быть про-
порциональным изменению контролируемого размера во всем диапазоне опе-
рационного допуска на обработку и пригодным для ввода в систему ЧПУ стан-
ка. Конструкция контрольного устройства и вид диагностического сигнала
должны быть инвариантны к факторам, присущим процессу резания: действию
стружки, технологической среды (СОЖ, газовая среда и т. д.), изменению уров-
ня вибрации механизмов и узлов станка, переменному шуму в рабочей зоне
станка, а также изменению температуры заготовки, отклонению твердости ма-
териала и неоднородности физико-механического состава.
Система ЧПУ станка должна обеспечивать возможность задания эталон-
ных значений диагностических сигналов и отклонений от них, прием сигналов
с устройства контроля, их математическую обработку и сравнение с эталонным
значением, а также выполнение математических операций с необходимым
быстродействием и точностью для формирования команд.
На рис. 19 представлена ГПС механической обработки корпусных цилин-
дрических деталей МАК-2, разработанная НИТИ «Прогресс», г. Ижевск. ГПС
предназначена для автоматизированного изготовления сложных корпусных де-
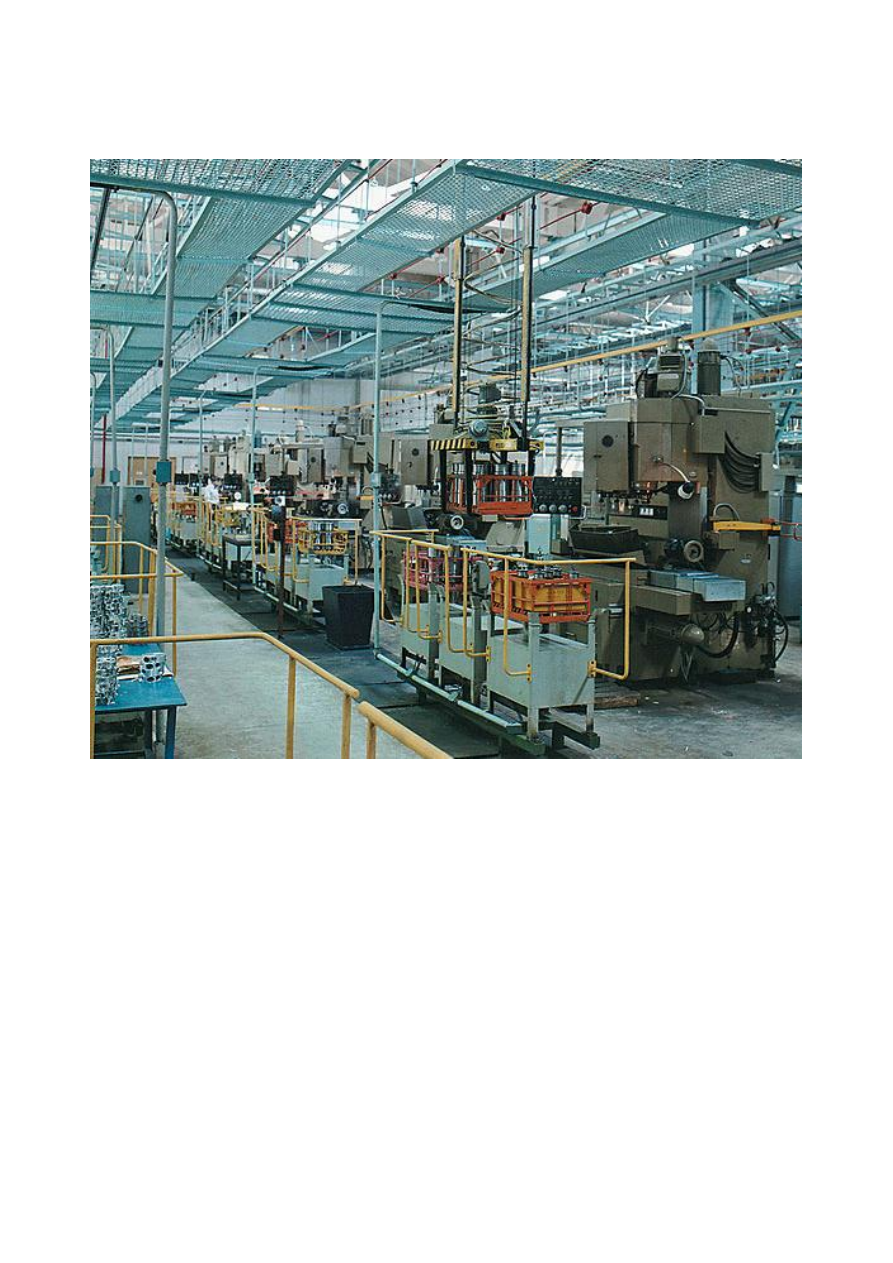
67
талей цилиндрической формы размерами 150
400 мм из высокопрочных ста-
лей, в том числе закаленных. Тип производства серийный.
Рис. 19. ГПС механической обработки корпусных цилиндрических деталей
ГПС состоит из четырех гибких автоматизированных участков, в состав
которых входят многоцелевые станки, подвесные транспортные роботы и мо-
ечно-сушильные агрегаты, а также гибкий автоматизированный участок уни-
версальных станков, транспортно-накопительная система, централизованная
система инструментального обеспечения и интегрированная автоматизирован-
ная система управления.
Основное металлорежущее оборудование ГПС – многоцелевые станки с
ЧПУ токарной группы – модели СТП0220Пр и 16К20ФЗС18; и фрезерно-
сверлильно-расточной группы модели ОЦ1И21, ОЦ1И22, ОЦ1И22Н. Техноло-
гические характеристики ГПС приведены в табл. 15.
Обработка производится в универсальных переналаживаемых приспособ-
лениях с быстросменными наладками. Полнота обработки изделий достигается
применением в составе ГПС участков из многоцелевых станков с ЧПУ для ос-
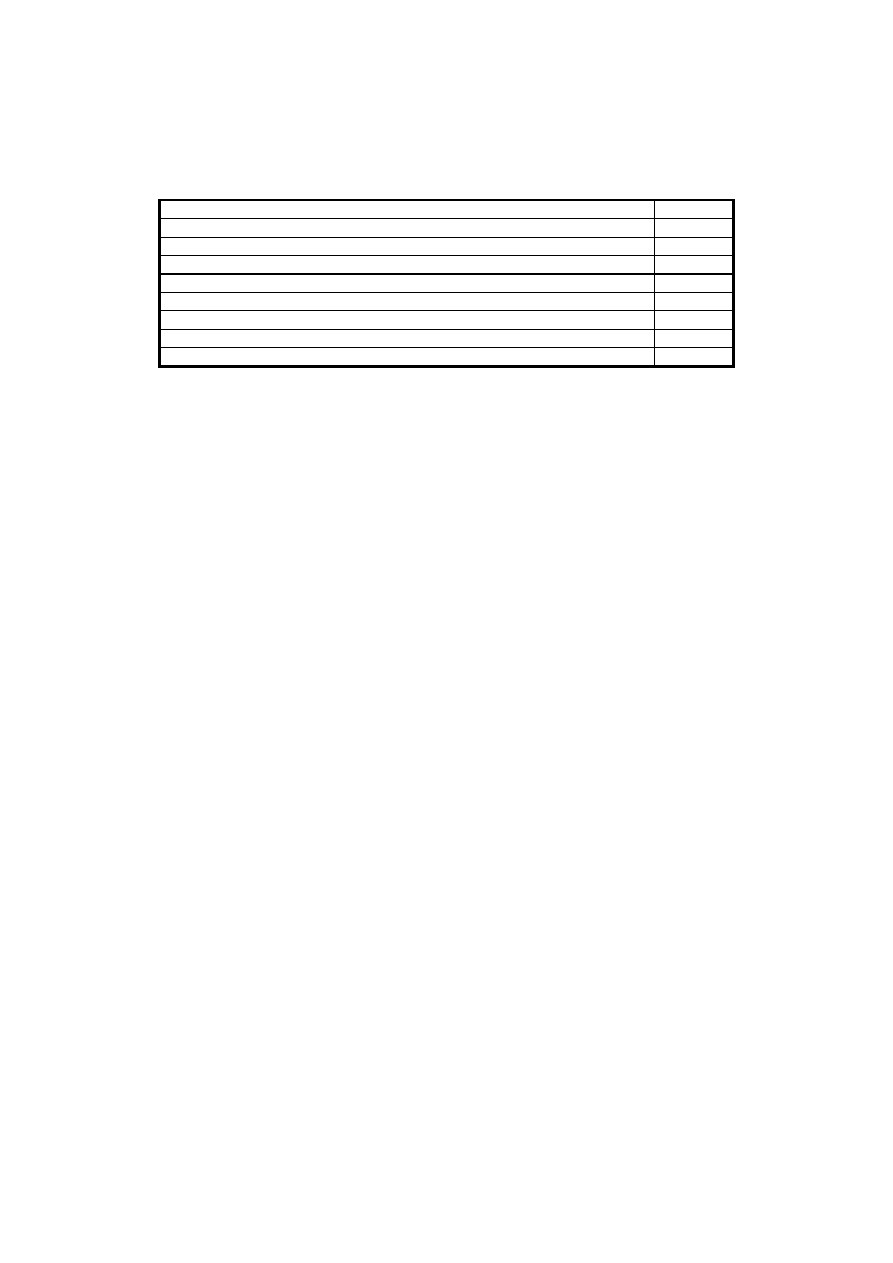
68
новных формообразующих операций, а также участков универсальных станков
и слесарных рабочих мест для финишных операций.
Таблица 15
Технологические характеристики ГПС МАК-2
Доля станков ЧПУ,% в общей станкоемкости
85
– 90
Наибольшие размеры обрабатываемых деталей, мм.
Диаметр
150
Длина
400
Количество станков в ГПС, шт.
76
В том числе:
многоцелевых с ЧПУ,
54
универсальных
22
Площадь, занимаемая ГПС, кв. м.
2630
Запуск деталей производится расчетными партиями, а межоперационное
перемещение грузов – транспортными партиями в единой унифицированной
таре подвесными транспортными роботами.
Обслуживание рабочих мест плановое, по сменно-суточному заданию. По-
следовательность подачи грузов на рабочие места: приспособление, комплект
инструментальных наладок, заготовки. Подача грузов производится автомати-
чески, а разгрузка в целях безопасности – по запросам с рабочих мест.
Межоперационное хранение грузов производится на приемных столах и в
таре транспортно-накопительной системы. Загрузку заготовок на станки, снятие
со станка и укладку в тару производят операторы станков.
Удаление стружки централизованное, механизированное, специальными
конвейерами скребкового типа. Обеспечение СОЖ централизованное, через
раздаточные колонки.
5.2. Автоматизированная транспортно-складская система
В состав АТСС включают автоматизированные склады, краны, конвейеры,
тележки, промышленные роботы, передающие, тактовые и ориентирующие
устройства.
Структурные единицы АТСС – дорогостоящие громоздкие агрегаты – их
применение должно удовлетворять критериям целесообразности. Они приме-
няются там, где суточные комплекты занимают большие объемы и площади.
Автоматизированные склады предназначены для хранения, приемки и вы-
дачи материальных объектов производственного процесса с максимальным ис-
пользованием объемов складских помещений, высоким уровнем автоматизации
транспортно-погрузочных операций и максимальным быстродействием.
Пример типовой конструкции автоматизированного склада показан на рис.
20.
Склад состоит из модулей. Каждый модуль представляет собой два ряда
многоярусных стеллажей 1, в проходе которых по верхнему и нижнему рельсо-
вым путям перемещается подъемно-транспортный механизм - штабелер 2.
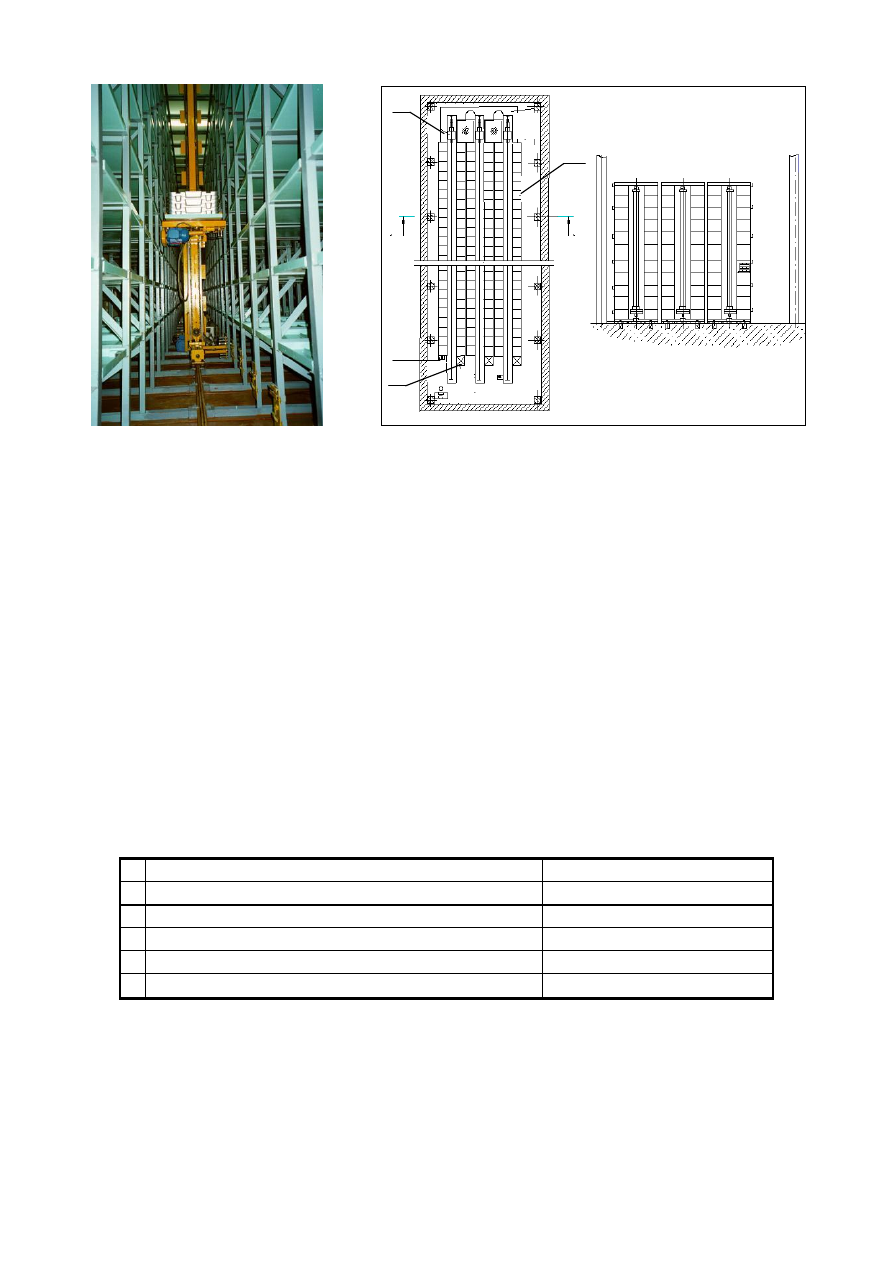
69
Рис. 20. Автоматизированный склад
В ячейках стеллажей размещаются тара или поддоны с грузом. В переднем
торце стеллажа каждого модуля монтируются столы 3 приема и выдачи груза. В
непосредственной близости от стола устанавливается шкаф 4 управления шта-
белером, содержащий средства автоматики исполнительных механизмов.
Штабелер – подъемно-транспортное устройство, состоящее из колонны с
грузоподъемной платформой, на которой смонтирован выдвижной телескопи-
ческий грузозахват. По команде ЦПУ на загрузку склада штабелер подает на
приемное устройство пустую тару или приспособления-спутники, которые за-
гружаются заготовками, затем транспортируются в заданные ячейки стеллажа.
При поступлении команды на разгрузку склада штабелер забирает тару или
приспособления-спутники из ячеек стеллажа, транспортирует и устанавливает
их на стол загрузки-разгрузки.
Таблица 16
Технические характеристики автоматизированных складов
1 Высота склада, м
4 - 8
2 Длина склада, м
10 - 60
3 Число модулей в складе
1…6
4 Грузоподъемность штабалера, кг
100…1000
5 Грузозахват
телескопический
6 Габаритные размеры тары (поддона) в плане, мм
от 300
400 до 800
1200
Управление складом ведется оператором с клавиатуры ПЭВМ. Система
управления складом связана с ЦПУ производственного комплекса, откуда зада-
ется автоматический режим работы. Система управления позволяет произво-
дить учет, обработку, систематизацию и вывод данных по хранимым объектам.
Краткие технические характеристики автоматизированных складов приве-
дены в табл. 16.
А-А
А
А
1
2
4
3
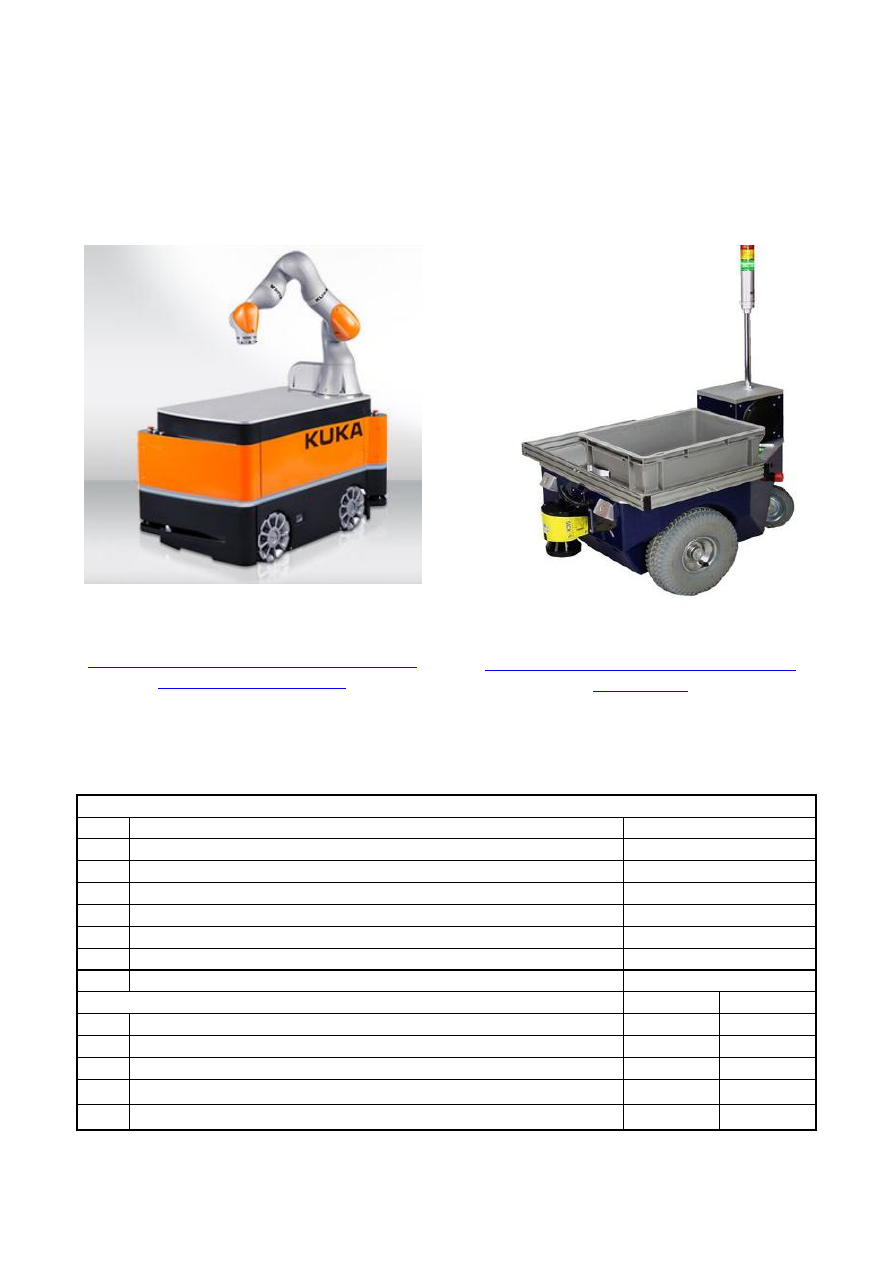
70
Универсальными транспортными средствами являются напольные автома-
тизированные платформы. Для выполнения погрузочно-разгрузочных операций
их оснащают различными подъемными, поворотными и выдвижными столами
или промышленными роботами. Платформы, оснащенные программируемыми
системами управления, называют транспортными роботами (ТР). Пример кон-
структивного исполнения ТР представлен на рис.21.
Рис. 21. Транспортный робот KMR iiwa
компании KUKA Roboter GmbH
https://www.youtube.com/watch?v=ymAgKy
Рис. 22. Транспортный робот ММТ-400
компании
Neobotix GmbH
http://www.neobotix-robots.com/transport-
Таблица 17
Технические характеристики транспортного робота KMR iiwa
Платформа
1
Высота платформы, мм
700
2
Длина со сканерами зон безопасности, мм
1190
3
Ширина со сканерами и зон безопасности, мм
720
4
Вес, кг
400
5
Максимум. полезная нагрузка, кг
400
6
Макс. скорость прямо вперед и в стороны, км / ч
4
7
Максимум. скорость по диагонали, км / ч
2
8
Диаметр колеса, мм
250
Робот LBR iiwa
7 R800
14 R800
1
Полезная нагрузка, кг
7
14
2
Количество осей
7
7
3
Точность позиционирования (ISO 9283), мм
± 0,1
± 0,1
4
Точность скоростей
± 2%
± 2%
5
Вес
22,3
22,3