Файл: 1Технологический анализ чертежа 4 1Общая информация о детали 4.docx
Добавлен: 25.10.2023
Просмотров: 367
Скачиваний: 3
ВНИМАНИЕ! Если данный файл нарушает Ваши авторские права, то обязательно сообщите нам.
СОДЕРЖАНИЕ
Анализ поверхностей детали и технических требований, способ их достижения
Определение типа производства и организационной формы производства
Определение коэффициента закрепления операции
Выбор организационной формы производства
Экономическое обоснование целесообразности выбранного метода
Разработка операционного технологического процесса
Расчет диаметральных операционных размеров назначение припусков на обработку
Расчет режимов резания и основного технологического времени
Нормирование технологического процесса
Определение количества необходимого оборудования и его загрузки
Произведем проверку правильности выполненных расчетов:



Условие выполняется.
- 1 ... 5 6 7 8 9 10 11 12 13
Расчет режимов резания и основного технологического времени
Расчет режимов резания для одного технологического перехода и назначение режимов резания по нормативам для остальных переходов
Операция 020 Токарная с ЧПУ. Подрезать торец 1
-
Материал режущей части – Т15К6 (ГОСТ 3882-74). Выбираем четырехгранную пластину по ГОСТ 19049-80 [3, табл. 4.13, с. 128]. Основные размеры: l = 9,525 мм; d = 9,525 мм; S= 3,18 мм; r = 0,8 мм [3, табл. 4.15, с. 138]. -
Геометрические параметры резца:
главный передний угол γ = 10°;
главный задний угол α = 10°;
главный угол в плане φ = 45°;
вспомогательный угол в плане φ1 = 45°;
радиус вершины лезвия r = 0,5 мм.
-
Глубина резания
t = 2,8 мм (черновое точение).
-
Подача
S = 1,3 мм/об [1, табл. 13, с. 366].
-
Скорость резания
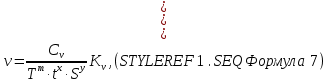
где T= 60 мин;


где
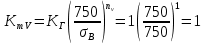




-
Частота вращения заготовки

-
Определение действительной частоты вращения
nд = 1000 об/мин (приложение Б).
-
Фактическая скорость резания

-
Сила резания

где


где


= 1;





-
Мощность резания


где



Эффективная мощность резания не превышает мощность станка, следовательно, принятые режимы резания являются допустимыми.
Режимы резания для других операций и переходов рассчитываются аналогично и сведены в таблицу 5.3.
Таблица 5.19 – Результаты расчета режимов резания
Номер и наименование операции | t, мм | D, мм | S, мм/об | V, м/мин | n, об/мин |
015 Фрезерно-центровальная | 2 | 19,4 | 0,6 | 169,5 | 900 |
2,5 | 5 | 0,3 | 14,3 | 900 | |
020 Токарная с ЧПУ | 2,8 | 16 | 1,3 | 94,2 | 1000 |
2 | 4 | 0,6 | 169,5 | 900 | |
1,8 | 72 | 0,3 | 14,3 | 900 | |
1,6 | 27 | 0,5 | 300 | 2100 | |
0,6 | 0,6 | 0,1 | 250 | 2100 | |
1,6 | 16 | 0,5 | 200 | 1500 | |
3,0 | 65 | 0,5 | 200 | 1500 | |
025 Токарная с ЧПУ | 2,8 | 16 | 1,3 | 94,2 | 1000 |
2 | 4 | 0,6 | 169,5 | 900 | |
1,8 | 72 | 1,0 | 400 | 2200 | |
1,6 | 14 | 0,5 | 350 | 2200 | |
2,0 | 2 | 0,5 | 200 | 1800 | |
1,5 | 16 | 0,5 | 200 | 1500 | |
030 Токарная с ЧПУ | 5,0 | 5 | 0,27 | 300 | 1200 |
4,0 | 4 | 0,27 | 300 | 1200 | |
5,25 | 10,5 | 0,6 | 45 | 900 | |
1,5 | 12 | 0,5 | 35 | 700 | |
035 Круглошлифовальная | 0,16 | 16 | 0,5 | кр=30м/с д=50м/мин | кр=3820 д=245 |
0,16 | 21 | 0,5 | кр=30м/с д=50м/мин | кр=3820 д=265 | |
0,16 | 22 | 0,5 | кр=30м/с д=50м/мин | кр=3820 д=289 | |
0,16 | 26 | 0,5 | кр=30м/с д=50м/мин | кр=3820 д=289 | |
0,16 | 22 | 0,5 | кр=30м/с д=50м/мин | кр=3820 д=289 |
- 1 ... 5 6 7 8 9 10 11 12 13
Нормирование технологического процесса
Норма штучного времени на операцию на станках с ЧПУ определяется по следующей формуле:

где








Время цикла автоматической работы по программе определяется по формуле:

где


Основное машинное время на операцию обработки определяется по формуле:
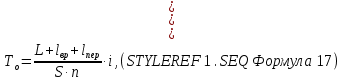
где



