Файл: 1Технологический анализ чертежа 4 1Общая информация о детали 4.docx
Добавлен: 25.10.2023
Просмотров: 361
Скачиваний: 3
ВНИМАНИЕ! Если данный файл нарушает Ваши авторские права, то обязательно сообщите нам.
СОДЕРЖАНИЕ
Анализ поверхностей детали и технических требований, способ их достижения
Определение типа производства и организационной формы производства
Определение коэффициента закрепления операции
Выбор организационной формы производства
Экономическое обоснование целесообразности выбранного метода
Разработка операционного технологического процесса
Расчет диаметральных операционных размеров назначение припусков на обработку
Расчет режимов резания и основного технологического времени
Нормирование технологического процесса
Определение количества необходимого оборудования и его загрузки
– число оборотов шпинделя в минуту, об/мин;
– подача инструмента, мм/об;
– число проходов.
Суммарное основное (технологическое) время на операцию определяется по формуле:
где
– основное (технологическое) время на i – ый переход;
– количество проходов;
Время выполнения ручной вспомогательной работы
где
– вспомогательное время на установку и снятие детали,
=0,1 мин;
– вспомогательное время, мин;
Вспомогательное время, связанное с операцией, не вошедшее во время цикла автоматической работы станка по программе, предусматривает выполнение следующей работы:
– вспомогательное время на измерение, мин.
Необходимые размеры деталей, обрабатываемых на станках с ЧПУ, обеспечиваются в автоматическом цикле обработки.
В связи с этим время на контрольные измерения (после окончания работы по программе)
должно включаться в норму штучного времени только в том случае
, если это предусмотрено технологическим процессом и с учётом необходимой периодичности таких измерений в процессе работы, и только в тех случаях, если оно не может быть перекрыто временем цикла автоматической работы станка по программе.
Так как время на контрольные измерения перекрывается временем цикла автоматической работы станка по программе, то
.
Машинно-вспомогательное время, связанное с переходом, определяется по паспортным данным станков и входит в качестве составляющих элементов во время автоматической работы станка.
Ввести коррекцию, 0,1 мин;
Смена инструмента, 0,05 мин;
Подвод инструмента от исходных точек зоны обработки и отвод, 0,04 мин.
Результаты нормирования операций сводим в таблицу 11.1.
Таблица 5.20 – Результаты нормирования операций
Для каждого станка в технологическом процессе должны быть подсчитаны коэффициент загрузки и коэффициент использования станка по основному времени.
1.Коэффециент загрузки станка
где
- расчетное количество станков (данные берем из пункта 2.2)
– принятое количество станков (данные берем из пункта 2.2)
Для Фрезерно-центровальной
Для Токарной черновой операции
Для Токарной чистовой операции
Для Фрезерной операции
Для Сверлильной операции
Для Круглошлифовальной
Коэффициент использования оборудования по основному времени свидетельствует о доле машинного времени работы станка. И он определяется как отношение основного времени к штучно-калькуляционному.
Для Фрезерно-центровальной
Для Токарной черновой операции
Для Токарной чистовой операции
Для Фрезерной операции
Для Сверлильной операции
Для Круглошлифовальной
Использование станков по мощности привода этот фактор характеризуется коэффициентом использования оборудования, который представляет собой отношение необходимой мощности на приводе станка к мощности установленного электродвигателя.
Для Фрезерно-центровальной
Для Токарной черновой операции
Для Токарной чистовой операции
Для Фрезерной операции
Для Сверлильной операции
Для Круглошлифовальной
Рисунок 6 – График эффективности загрузки оборудования
По графику можно судить о средней эффективности загрузки оборудования.
Пути повышения коэффициента загрузки оборудования заключаются в сокращении количества используемого оборудования на участке, что вполне обосновано среднесерийным типом производства. Для этого необходимо применять универсальные, многоцелевые станки с ЧПУ, а также производить их загрузку обработкой других деталей одного типоразмера.
По коэффициенту основного времени
Рисунок 7 – График использования оборудования по основному времени
Коэффициент использования оборудования по основному времени можно повысить, уменьшив простои станков (вспомогательное время) за счет применения механизированных приспособлений, повышающих уровень автоматизации. Для данного технологического процесса коэффициент использования оборудования по основному времени вполне приемлем.
По мощности привода станка
Рисунок 8 – График использования оборудования по мощности
Повышение коэффициента использования оборудования по мощности заключается в правильности выбора оборудования (его типоразмера) и режимов обработки, для того чтобы значительная часть мощности расходовалась на резание, а не на холостые ходы станка. Для данного технологического процесса коэффициент использования оборудования по мощности достаточно рационален, так как деталь крупногабаритная, и использовать другие станки не рационально.
Таблица 5.21 – Определение средних коэффициентов загрузки оборудования
3.1 Разработка станочного приспособления
3.1.1 Определение конструкции и расчет специальных средств технологического оснащения
При разработке конструкции приспособления необходимо стремиться к уменьшению времени на установку и съем обрабатываемой детали, необходимо соблюдать правила выбора баз, стабильного взаимного положения заготовки и режущего инструмента при обработке, удобную установку, контроль и снятие детали, свободное удаление стружки, удобство управления станком и приспособлением


Суммарное основное (технологическое) время на операцию определяется по формуле:
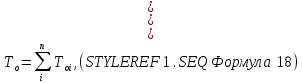
где


Время выполнения ручной вспомогательной работы

где



Вспомогательное время, связанное с операцией, не вошедшее во время цикла автоматической работы станка по программе, предусматривает выполнение следующей работы:
-
установить заданное взаимное положение детали и инструмента по координатам, и в случае необходимости произвести повторную настройку, 0,05 мин; -
включить и выключить программу ЧПУ, 0,1 мин; -
проверить приход детали или инструмента в заданную точку после обработки, 0,05 мин; -
установить защитный щиток от брызг эмульсии и снять, 0,1 мин.


Необходимые размеры деталей, обрабатываемых на станках с ЧПУ, обеспечиваются в автоматическом цикле обработки.
В связи с этим время на контрольные измерения (после окончания работы по программе)

, если это предусмотрено технологическим процессом и с учётом необходимой периодичности таких измерений в процессе работы, и только в тех случаях, если оно не может быть перекрыто временем цикла автоматической работы станка по программе.
Так как время на контрольные измерения перекрывается временем цикла автоматической работы станка по программе, то


Машинно-вспомогательное время, связанное с переходом, определяется по паспортным данным станков и входит в качестве составляющих элементов во время автоматической работы станка.
Ввести коррекцию, 0,1 мин;
Смена инструмента, 0,05 мин;
Подвод инструмента от исходных точек зоны обработки и отвод, 0,04 мин.
Результаты нормирования операций сводим в таблицу 11.1.
Таблица 5.20 – Результаты нормирования операций
№ и наименование операции | ![]() | ![]() | ![]() | ![]() | ![]() | ![]() |
015 Фрезерно-центровальная | 1,2 | 0,64 | 2,2 | 15,0 | 60 | 2,9 |
020 Токарная с ЧПУ | 3,8 | 2,0 | 8,8 | 12,5 | 10,3 | |
025 Токарная с ЧПУ | 1,2 | 0,64 | 2,2 | 12,5 | 2,9 | |
030 Токарная с ЧПУ | 1,53 | 0,6 | 2,05 | 12,5 | 2,4 | |
035 Круглошлифовальная | 4,06 | 2,39 | 10,3 | 15,0 | 11,6 |
- 1 ... 5 6 7 8 9 10 11 12 13
Определение количества необходимого оборудования и его загрузки
Для каждого станка в технологическом процессе должны быть подсчитаны коэффициент загрузки и коэффициент использования станка по основному времени.
1.Коэффециент загрузки станка
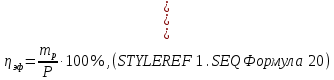
где


Для Фрезерно-центровальной
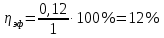
Для Токарной черновой операции
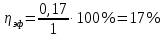
Для Токарной чистовой операции
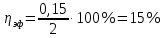
Для Фрезерной операции

Для Сверлильной операции
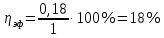
Для Круглошлифовальной
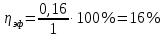
Коэффициент использования оборудования по основному времени свидетельствует о доле машинного времени работы станка. И он определяется как отношение основного времени к штучно-калькуляционному.
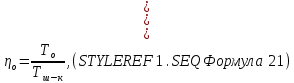
Для Фрезерно-центровальной
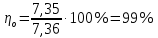
Для Токарной черновой операции
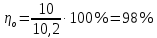
Для Токарной чистовой операции
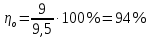
Для Фрезерной операции
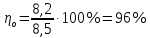
Для Сверлильной операции
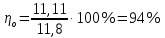
Для Круглошлифовальной
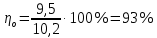
Использование станков по мощности привода этот фактор характеризуется коэффициентом использования оборудования, который представляет собой отношение необходимой мощности на приводе станка к мощности установленного электродвигателя.
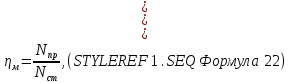
Для Фрезерно-центровальной
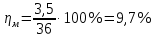
Для Токарной черновой операции
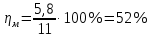
Для Токарной чистовой операции
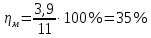
Для Фрезерной операции
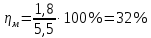
Для Сверлильной операции
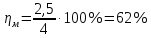
Для Круглошлифовальной
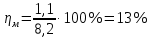
Построение диаграмм загрузки
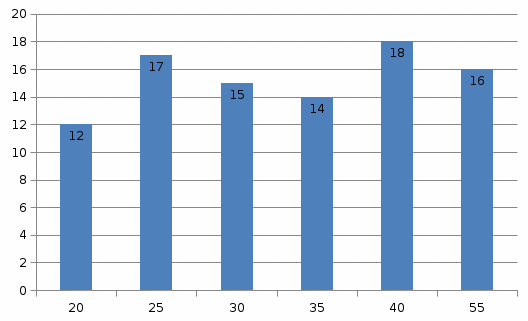
Рисунок 6 – График эффективности загрузки оборудования
По графику можно судить о средней эффективности загрузки оборудования.
Пути повышения коэффициента загрузки оборудования заключаются в сокращении количества используемого оборудования на участке, что вполне обосновано среднесерийным типом производства. Для этого необходимо применять универсальные, многоцелевые станки с ЧПУ, а также производить их загрузку обработкой других деталей одного типоразмера.
По коэффициенту основного времени
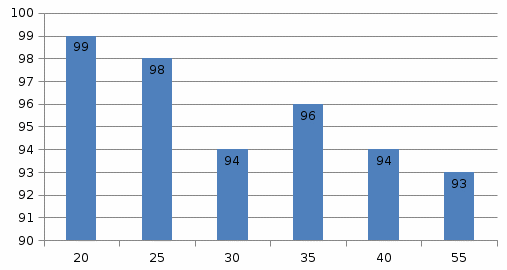
Рисунок 7 – График использования оборудования по основному времени
Коэффициент использования оборудования по основному времени можно повысить, уменьшив простои станков (вспомогательное время) за счет применения механизированных приспособлений, повышающих уровень автоматизации. Для данного технологического процесса коэффициент использования оборудования по основному времени вполне приемлем.
По мощности привода станка
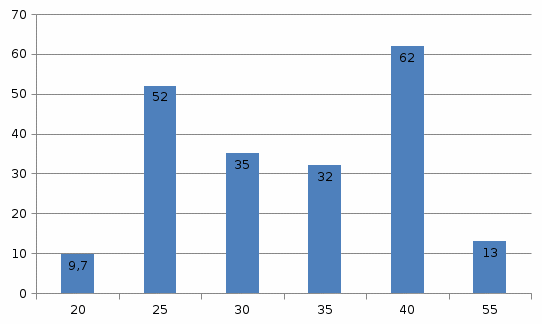
Рисунок 8 – График использования оборудования по мощности
Повышение коэффициента использования оборудования по мощности заключается в правильности выбора оборудования (его типоразмера) и режимов обработки, для того чтобы значительная часть мощности расходовалась на резание, а не на холостые ходы станка. Для данного технологического процесса коэффициент использования оборудования по мощности достаточно рационален, так как деталь крупногабаритная, и использовать другие станки не рационально.
Таблица 5.21 – Определение средних коэффициентов загрузки оборудования
Операция | Модель станка | ηэф, % | ηо, % | ηм, % | |||
Фрезерно-центровальная | Фрезерно-центровальный полуавтомат МР-71М | 12 | 99 | 9,7 | |||
Токарная черновая | Токарный станок 16К20 | 17 | 98 | 52 | |||
Токарная чистовая | Токарный станок 16К20 | 15 | 94 | 35 | |||
Фрезерная | Вертикально-фрезерный 6Р11 | 14 | 96 | 32 | |||
Сверлильная | Вертикально-сверлильный 2Н132 | 18 | 94 | 62 | |||
Шлифовальная | Круглошлифовальный станок 3М151 | 16 | 93 | 13 | |||
Среднее значение | 15,3 | 95,6 | 33,9 |
-
Конструкторский раздел
3.1 Разработка станочного приспособления
3.1.1 Определение конструкции и расчет специальных средств технологического оснащения
При разработке конструкции приспособления необходимо стремиться к уменьшению времени на установку и съем обрабатываемой детали, необходимо соблюдать правила выбора баз, стабильного взаимного положения заготовки и режущего инструмента при обработке, удобную установку, контроль и снятие детали, свободное удаление стружки, удобство управления станком и приспособлением