Файл: Пояснительная записка выпускной квалификационной работы содержит 55 страниц формата А4, 12 рисунков, 8 таблиц, 5 используемых источников информации.docx
ВУЗ: Не указан
Категория: Не указан
Дисциплина: Не указана
Добавлен: 26.10.2023
Просмотров: 64
Скачиваний: 2
ВНИМАНИЕ! Если данный файл нарушает Ваши авторские права, то обязательно сообщите нам.
СОДЕРЖАНИЕ
1.1 Назначение, состав и техническая характеристика механизма
1.3 Требования, предъявляемые к приводу
2 Расчёт мощности и выбор двигателя
2.1 Расчёт статических моментов
2.2 Предварительный выбор двигателя
2.3 Расчёт нагрузочной диаграммы
2.4 Проверки двигателя по нагреву и перегрузочной способности
3 выбор и характеристика основного электрооборудования
3.1 Выбор и характеристика преобразователя частоты
3.2 Выбор и характеристика силового трансформатора
4 Расчёт и построение статических характеристик
5.1 Защита от перегрузки и коротких замыканий
6 Разработка системы управления мехатронной системой
РЕФЕРАТ
Пояснительная записка выпускной квалификационной работы содержит 55 страниц формата А4, 12 рисунков, 8 таблиц, 5 используемых источников информации.
МОСТОВОЙ КРАН, ПЕРЕМЕЩЕНИЕ КРАНА, АСИНХРОННЫЙ ДВИГАТЕЛЬ, ТРЕВЕРС, ПЧ-АД, ТАХОГРАММА, НАГРУЗОЧНАЯ ДИАГРАММА, ПЕРЕДАТОЧНАЯ ФУНКЦИЯ, ОБЪЕКТ РЕГУЛИРОВАНИЯ, СТРУКТУРНАЯ СХЕМА, ПЕРЕХОДНЫЕ ПРОЦЕССЫ.
Объект исследования - мостовой кран №27 ЭСПЦ ПАО “ММК”», предназначенный для перемещения стальковша до электросталеплавильной печи.
Целью работы является проектирование электропривода переменного тока для подъема кроном груза.
В итоге были выбраны: двигатель переменного тока, преобразователь чатсоты и трансформатор. Была спроектирована схема объекта регулирования и построены переходные процессы.
сОДЕРЖАНИЕ
1 тЕХНОЛОГИЧЕСКАЯ ЧАСТЬ 4
1.1 Назначение, состав и техническая характеристика механизма 4
1.2 Технология 7
1.3 Требования, предъявляемые к приводу 13
2 Расчёт мощности и выбор двигателя 15
2.1 Расчёт статических моментов 15
2.2 Предварительный выбор двигателя 17
2.3 Расчёт нагрузочной диаграммы 20
2.4 Проверки двигателя по нагреву и перегрузочной способности 27
3 выбор и характеристика основного электрооборудования 30
3.1 Выбор и характеристика преобразователя частоты 30
3.2 Выбор и характеристика силового трансформатора 31
4 Расчёт и построение статических характеристик 34
5 Защита электропривода 37
5.1 Защита от перегрузки и коротких замыканий 37
5.2 Защита от перенапряжений 38
5.3 Контроль изоляции 39
6 Разработка системы управления мехатронной системой 40
7 Моделирование работы мехатронной системы 49
Заключение 52
Список использованных источников 53
1 тЕХНОЛОГИЧЕСКАЯ ЧАСТЬ
1.1 Назначение, состав и техническая характеристика механизма
Мостовые краны – это краны, которые обычно устанавливаются в производственных и сборочных цехах. Они состоят из одной или двух балочных балок, моста, который можно перемещать в боковом направлении и грузовой тележки.
В отличие от мобильных или строительных кранов, мостовые краны обычно используются в промышленном производстве или для технического обслуживания, где эффективность или время простоя являются критическими факторами.
Мостовые краны обычно используются в производствах, связанных с обработкой стали и других металлов, таких как медь и алюминий. На каждом этапе производственного процесса, пока он не покинет завод в качестве готового продукта, металл обслуживается мостовым краном. Сырье погружают в печь с помощью крана, затем горячий металл прокатывают до определенной толщины и закаливают или отжигают, а затем хранят с помощью мостового крана для охлаждения, готовые рулоны поднимают и загружают на грузовые автомобили и поезда с помощью мостового крана, и изготовитель или штамповщик использует мостовой кран для обработки стали на своем заводе. В автомобильной промышленности используются мостовые краны для обработки сырья. Почти все бумажные фабрики используют мостовые краны для регулярного технического обслуживания, требующего удаления тяжелых прижимных валков и другого оборудования. Мостовые краны используются при первоначальном строительстве бумагоделательных машин, поскольку они облегчают установку тяжелых чугунных сушильных барабанов для бумаги и другого массивного оборудования, некоторые весом до 70 тонн.
Во многих случаях стоимость мостового крана может быть в значительной степени компенсирована экономией за счет отказа от аренды мобильных кранов при строительстве объекта, который использует большое количество тяжелого технологического оборудования. На рисунке 1 представлен пример промышленного мостового крана.
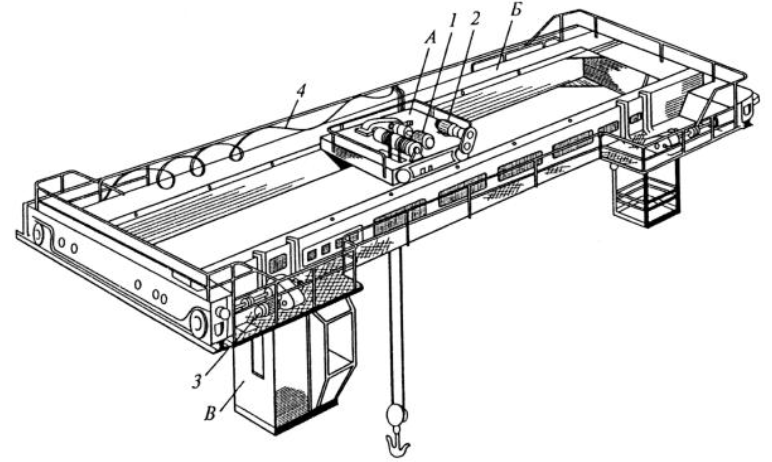
Рисунок 1 – Мостовой кран:
1 – Электропривод подъема лебедки; 2 – Электропривод передвижения тележки; 3 – Электроривод передвижения моста; 4 – Кабель питания электроприводов.
Рассматриваемый в выпускной квалификационной работе мостовой кран содержит следующий перечень механизмов-
-
механизм главного подъема. -
механизм вспомогательного подъема 1. -
механизм вспомогательного подъема 2. -
механизм передвижения главной тележки. -
механизм передвижение вспомогательной тележки. -
механизм передвижения крана.
Основные технические характеристики крана приведены в таблице 1.
Таблица 1 - Техническая характеристика крана
Грузоподъемность: | |
Главного подъема | 225 т. |
Вспомогательного подъема 1 | 63 т. |
Вспомогательного подъема 2 | 20 т. |
Скорости: | |
Главного подъема | 10 м\мин. |
Вспомогательного подъема 1 | 10 м\мин. |
Вспомогательного подъема 2 | 14 м\мин. |
Передвижения главной тележки | 35 м\мин. |
Передвижение вспомогательной тележки | 40 м\мин |
Передвижения крана | 63 м\мин |
Высота: | |
Главного подъема | 32 м. |
Вспомогательного подъема 1 | 34 м. |
Вспомогательного подъема 2 | 32 м. |
Пролёт | 25,5 м. |
Напряжение питания | 380 В. |
Токосъем крана | троллеи |
Кинематическая схема механизма главного подъема мостового крана показана на рисунке 2.
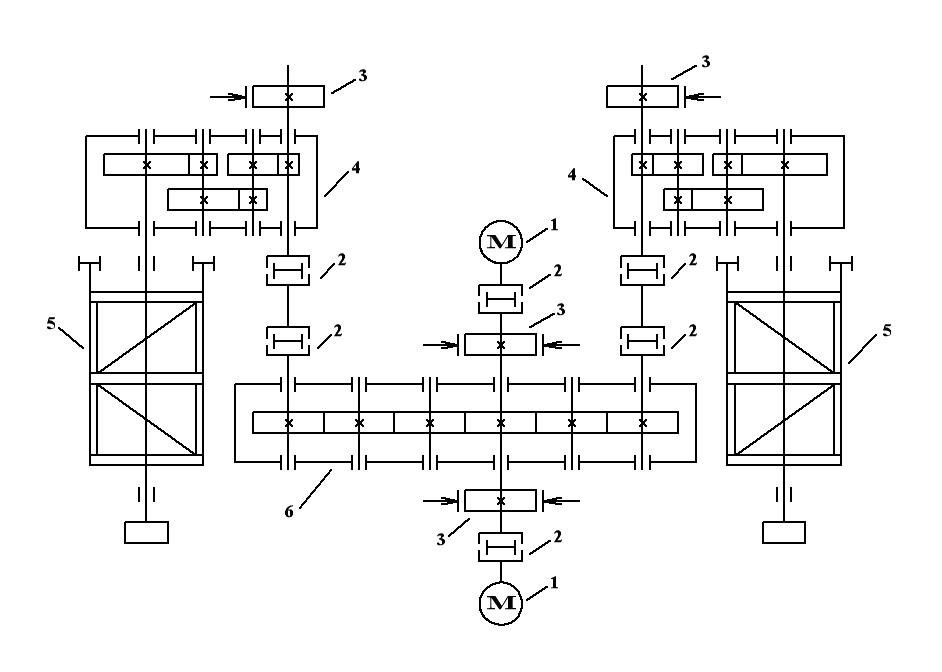
Рисунок 2 – Кинематическая схема механизма главного подъема мостового крана:
1- электродвигатели; 2- муфты; 3- тормозное устройство; 4- редукторы; 5- барабаны; 6- дифференциальное устройство
1.2 Технология
Процесс начинается с выплавки стали в электросталеплавильный печах или в дуговых плавильных печах.
После плавки сталь сливают в сталеразливочный ковш, оборудованный двумя продувочными блоками. Металл продувают с интенсивностью 200-1000 л/мин (на каждую пробку) аргоном. При наполнении ковша на 1/5—1/4 высоты в металл отдается шлаковая смесь в количестве 1,5-2,0 т (соотношение известь/шпат
4:1) и алюминий в количестве до 500 кг.
По окончании выпуска от ковша отсоединяются аргонные шланги. Ковш с металлом передается сталевозом на внепечную обработку (на УПК или на АДС).
Уровень налива металла в ковше должен быть не более 400мм от верхней кромки ковша.
На установке «печь - ковш» производится подготовка жидкой стали в сталеразливочном ковше.
На данном агрегате проходят следующие операции:
продувка металла аргоном;
корректировка химического состава металла;
нагрев металла электродугой;
десульфурация металла белым основным шлаком;
измерение температуры, окисленности;
отбор проб металла и шлака и отправка их на экспресс-анализ;
микролегирование или получение металла с узкими пределами содержания элементов путем ввода порошковой проволоки с различными видами наполнителей;
добавление углерода в металл доливкой жидкого чугуна.
Плавки, предназначенные для обработки на установке печь-ковш, сливаются в сталеразливочный ковш, специально оборудованный для донной продувки.
Сталеразливочный ковш устанавливается на сталевоз. Сталевоз передвигается под крышку установки, после чего крышку опускают.
Включается подача аргона. Электроды опускаются в рабочую позицию, производится нагрев металла. Через 3-4 мин. продувки и нагрева производится измерение температуры. При необходимости производится измерение окисленности.
При получении результатов химического анализа металла производится корректировка его химического состава добавлением необходимого количества раскислителей и легирующих материалов, из расчета получения массовой доли вводимых элементов па 0,05 % выше нижнего предела в готовой стали с учётом их усвоения.
После ввода последней части ферросплавов металл смешивается с аргоном в течение не менее 5 минут. Не раньше, чем через 5 минут продувки после легирования, делают температурный и структурный анализ.
Перед получением результатов экспресс-анализа металл смешивают с расходом от 200 до 500 л/мин .
После получения результатов химического анализа, если требуется, проводится дальнейшая корректировка химического состава.
Достигнув необходимого химического состава и определив температуру, установка поднимается для отсоединения шлангов подведения аргона и заземления, сталевоз выдвигается под сталевоз, установленный с ковшом, и ковш смещаются на МНЛЗ.
В агрегате доводки стали жидкая сталь подготавливается в стальном лотке для литья при непрерывной разливке.
В агрегате доводки стали выполняются следующие технические функции:
а) очистка металла с помощью аргона, подаваемого в верхнюю фурму для усреднения химического состава металла и его температуры в сталеразливочном ковше;
б) измерение температуры и отбор проб металла и, при необходимости, проб шлака;
в) отправка образцов металла и шлака для экспресс-анализа;
г) Коррекция химического состава стали и ее микролегирование с помощью фиксированной добавки к материалу;
д) улучшение химического состава металла по алюминию введением алюминиевой катанки или чушкового алюминия;
е) микролегирование или получение металла с узкими пределами содержания присадок путем введения порошковой проволоки с различными типами наполнителей;
ж) химический прогрев металла;
и) охлаждение металла;
к) Заполнение поверхности жидкого металла гранулированным шлаком.
Контроль в процессе ковшевой обработки осуществляется путем измерения температуры и окисления металла, анализом проб металла и шлака, измерения скорости потока и давления аргона для продувки, измерения массы легирующих присадок.
Описание технологии обработки металла на агрегате доводки стали.
После электропечей и ДСА сталеразливочный ковш помещается на сталевоз АДС. Аргоновые шланги подключаются к продувочной системе ковша.
По объёму расплава, для усреднения состава металла и усреднения температуры, используется продувка с помощью аргона в течение 3 минут. После продувки измеряют температуру и отбирают пробу металла. Пробы отправляются пневмопочтой на экспресс-анализ.
По прибытии на АДС температура металла может варьироваться от 1600 до 1650 (в зависимости от марки стали).
По результатам экспресс-анализа определяется требование улучшения химической структуры металла. Корректирующие присадки добавляют частями массой не более 500 кг с диапазоном 0,5-2,0 минуты.
После добавления присадок с марганцем или кремниевых ферросплавов металл обдувают аргоном в течение не менее 5 минут, а при добавлении хромсодержащих ферросплавов - не менее 6 минут.
В медно- и никелесодержащих материалах химическая структура металла улучшается путем добавления никелевого, никельсодержащего и/или медьсодержащего материала.
При необходимости металл охлаждают с помощью сляба, который подвешивают с помощью цепей. После снятия сляба металл продувают не менее 2 минут.
Период продувки аргоном должен быть не менее:
а) для хромированной стали - 15 минут;
б) Для остальных легированных сплавов - 13 минут;
в) для углеродистых сталей - 12 минут.
На плавках, в которых температура металла ниже, чем требуется для нормальной продувки, после усредняющей продувки, металл химически нагревается. После доводки поверхность металла покрывается теплоизоляционной смесью. Расход смеси может варьироваться до 2,5 тонн.
После достижения необходимого химического состава и определенной температуры ковш перемещается на МНЛЗ.
Непрерывную разливку стали в заготовки сечением 100x100, 124x124, 120x150 и 152x170 мм производят на радиальных сортовых МНЛЗ.
Основные технологические параметры разливки стали на машине непрерывного литья заготовок представлены в таблице 2 и таблице 3.
Таблица 2 – Фонд времени работы машины
1.2 Технология
Процесс начинается с выплавки стали в электросталеплавильный печах или в дуговых плавильных печах.
После плавки сталь сливают в сталеразливочный ковш, оборудованный двумя продувочными блоками. Металл продувают с интенсивностью 200-1000 л/мин (на каждую пробку) аргоном. При наполнении ковша на 1/5—1/4 высоты в металл отдается шлаковая смесь в количестве 1,5-2,0 т (соотношение известь/шпат
Параметры работы МНЛЗ | Величина |
Календарное время, ч Плановые ремонтные дни- а) периодический ремонт ( 8 ч/неделя), ч б) капитальный ремонт, ч | 8760 408 72 |
Теоретическое рабочее время, ч | 8280 |
Время простоев (внеплановые простои, неисправности и аварии), ч | 360 |
Фактическое рабочее время, ч | 7920 |
Таблица 3 - Показатели работы МНЛЗ
Сечение заготовки, мм | Вес погонного метра, т | Скорость разливки, м/мин | Производительность, т/ч | Время разливки, мин | Длина, м |
100x100 | 0,0784 | 5,00-5,60 | 114,0-127,7 | 92-82 | 16,6-18,6 |
124x124 | 0,1206 | 3,00-4,40 | 105,2-154,3 | 100-68 | 15,2-22,3 |
120x150 | 0,1411 | 2,80-3,60 | 114,9-147,7 | 91-71 | 13,3-17,1 |
152x170 | 0,2026 | 2,00-2,70 | 117,8-159,1 | 89-66 | 15,1-20,4 |
Разливку стали производят сериями методом «плавка на плавку». Количество плавок, разливаемых непрерывно в серии, определяется производственными условиями и лимитируется -
а) стойкостью промежуточного ковша при разливке открытой струей с масляной смазкой;
б) стойкостью кристаллизаторов при разливке со стопорным управлением, заменой погружных стаканов и промежуточных ковшей по ходу серии.
При разливке методом «плавка на плавку» непрерывно в серии разливаются плавки одной или сходных по химическому составу марок стали. Для сокращения «переходной» зоны допускается снижение уровня металла в промежуточном ковше при переходе на разливку смежной плавки или замена промежуточного ковша.
Оборудование должно обеспечивать установку сталеразливочного ковша со следующей плавкой в положение разливки после окончания разливки из предыдущего ковша за время не более 2 мин. Стальковш во время разливки должен быть накрыт футерованной крышкой.
Емкость промежуточного ковша дельтаобразной формы в пределах 26-28 т. должна обеспечивать смену ковшей (для сечения 120 x 150 и 152 x 170 мм) при работе методом «плавка на плавку» практически без снижения скорости разливки. Длительность смены ковшей должна быть не более 6,0 мин. Стойкость промковша - не менее 5 плавок.
В таблице 4 представлены основные параметры быстродействия и производительности машины.
Таблица 4 - Скорость, производительность и время разливки
Сечение разливки, мм | Скорость разливки, м/мин | Производительность, т/ч | Время разливки, мин | Длина, м |
100 х 100 | 5,60 | 127,7 | 82 | 18,6 |
100 х 100 | 5,00 | 114,0 | 92 | 16,6 |
124 х 124 | 4,40 | 154,3 | 68 | 22,3 |
124 х 124 | 4,00 | 140,2 | 75 | 20,3 |
124 х 124 | 3,00 | 105,2 | 100 | 15,2 |
120 х 150 | 3,60 | 147,7 | 71 | 17,1 |
120 х 150 | 3,20 | 131,3 | 80 | 15,2 |
120 х 150 | 2,80 | 114,9 | 91 | 13,3 |
152 х 170 | 2,70 | 159,1 | 66 | 20,4 |
152 х 170 | 2,40 | 141,4 | 74 | 18,2 |
152 х 170 | 2,00 | 117,8 | 89 | 15,1 |