Файл: Пояснительная записка выпускной квалификационной работы содержит 55 страниц формата А4, 12 рисунков, 8 таблиц, 5 используемых источников информации.docx
ВУЗ: Не указан
Категория: Не указан
Дисциплина: Не указана
Добавлен: 26.10.2023
Просмотров: 66
Скачиваний: 2
ВНИМАНИЕ! Если данный файл нарушает Ваши авторские права, то обязательно сообщите нам.
СОДЕРЖАНИЕ
1.1 Назначение, состав и техническая характеристика механизма
1.3 Требования, предъявляемые к приводу
2 Расчёт мощности и выбор двигателя
2.1 Расчёт статических моментов
2.2 Предварительный выбор двигателя
2.3 Расчёт нагрузочной диаграммы
2.4 Проверки двигателя по нагреву и перегрузочной способности
3 выбор и характеристика основного электрооборудования
3.1 Выбор и характеристика преобразователя частоты
3.2 Выбор и характеристика силового трансформатора
4 Расчёт и построение статических характеристик
5.1 Защита от перегрузки и коротких замыканий
6 Разработка системы управления мехатронной системой

Коэффициент приведения С1:

Сравнив коэффициенты приведения, убеждаемся в том, что коэффицент приведения подобран правильно.
Векторное управление частотным управляемым асинхронным электроприводом связано как с изменением частоты и значений тока переменных асинхронного двигателя, так и с относительной ориентацией их векторов в полярной или декартовой системе координат. Регулируя значения амплитуды переменных и углов между их векторами, АД полностью контролируется как в статистике, так и в динамике, что заметно улучшает качество переходных процессов по сравнению со скалярным контролем. Этот факт имеет решающее значение для выбора систем с векторным управлением.
На рисунке 7 показана структурная схема системы ПЧ-АД с управлением по потокосцеплению ротора.
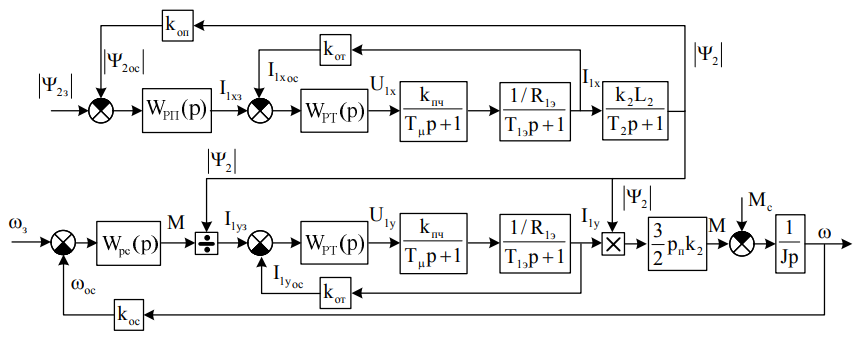
Рисунок 7 – Структурная схема системы ПЧ-АД при ориентации координат x,y по потокосцеплению ротора.
Эквивалентное сопротивление цепи статора рассчитывается следующим образом:

Электромагнитная постоянная времени этой цепи:

Коэффициент обратной связи по току равен:

Постоянная времени интегрирования:

где

Передаточная функция регуляторов тока выглядит следующим образом:
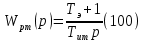
Передаточная функция потокосцепления представлена ниже:
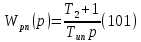
Электромагнитная постоянная времени цепи ротора рассчитывается:

Постоянная интегрирования ПИ-регулятора потокосцепления ротора:
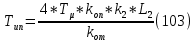

Коэффициент обратной связи по потокосцеплению:

Максимальное потокосцепление:

При определении передаточной функции регулятора скорости необходимо учитывать, что регулятор скорости должен компенсировать влияние рабочего блока на формирование электромагнитного момента асинхронного двигателя. Для этого на выходе РС должен быть включен делитель, аналогичный системам двухфазного регулирования скорости двигателей постоянного тока. В этом случае передаточная функция регулятора скорости выглядит следующим образом:

где J∑ - суммарный момент инерции электропривода, кг*м2;
kос - коэффициент обратной связи по скорости, В·с.

Настройку контура регулирования скорости на симметричный оптимум осуществляется при помощи ПИ-регулятора скорости со следующей передаточной функцией:

Для придания сигналу задания по скорости вида S-образной характеристики, а также для уменьшения перерегулирования по моменту, после блока задания скорости установлен фильтр.
Структурная схема, реализованная в программе MatLab Simulink, представлена на рисунке 8.
7 Моделирование работы мехатронной системы
Чтобы упростить моделирование, обработку и анализ переходных процессов, операция работы мостового крана разделена на четыре характерных области:
- опускание траверсы до точки “закрепления” ковша;
- подъём ковша с металлом для дальнейшего перемещения;
- опускание пустого ковша;
- подъём траверсы до верхней точки мостового крана.
Также для достижения большей наглядности время статических режимов работы электропривода было умышлено уменьшено. Переходные процессы, смоделированные в MatLab, по схеме, представленной на рисунке 8, представлены на рисунках 9, 10, 11 и 12 .
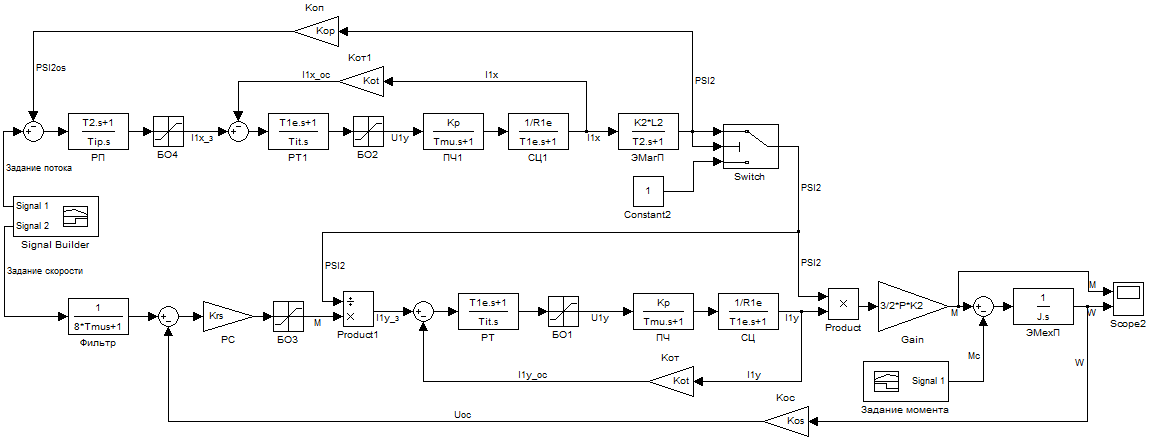
Рисунок 8 – Структурная схема системы ПЧ-АД при ориентации координат x,y по потокосцеплению ротора, реализованная в программе MatLab
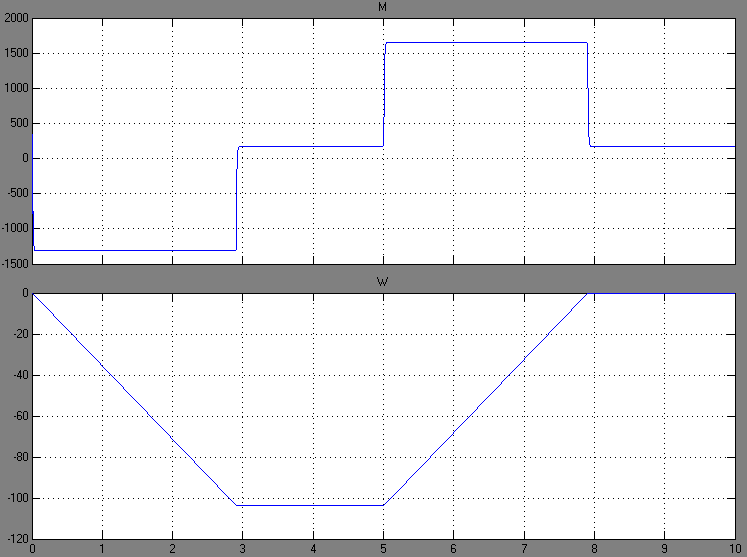
Рисунок 9 – Переходные процессы момента и скорости двигателя при опускании траверсы
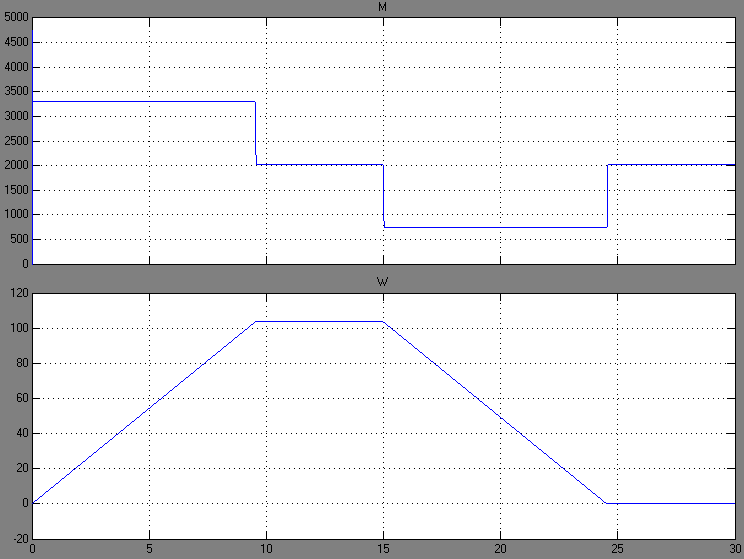
Рисунок 10 – Переходные процессы момента и скорости двигателя при подъёме ковша с металлом
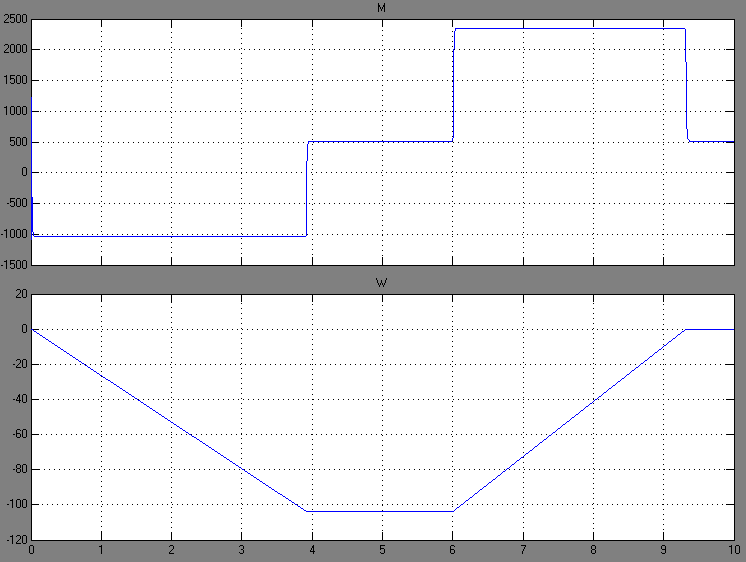
Рисунок 11 – Переходные процессы момента и скорости двигателя при опускании ковша
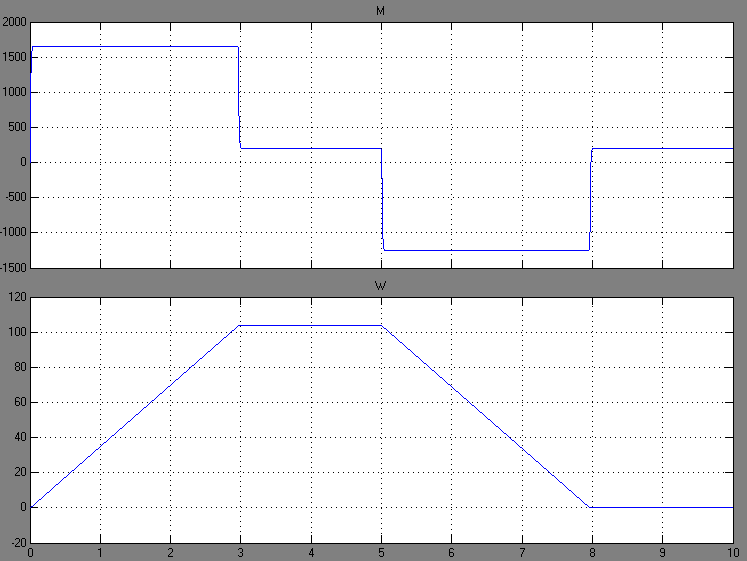
Рисунок 12 – Переходные процессы момента и скорости двигателя при подъеме траверсы
Заключение
В данной выпускной квалификационной работе описана технология работы главного подъема мостового крана №27 ЭСПЦ ПАО «ММК».
Рассчитаны и построены тахограмма и нагрузочная диаграмма. Выбран двигатель и проверил его по нагреву и перегрузочной способности. Рассчитанный привод отвечает всем технологическим требованиям.
Рассчитаны и выбраны преобразователь частоты и трансформатор.
Построены механические характеристики электропривода.
Выбрана необходимая защита силовой схемы.
Получены переходные процессы работы двигателя, по которым можно судить о состоятельности построенной системы для использования ее в механизме главного подъема мостового крана №27 ЭСПЦ ПАО «ММК».
.
Список использованных источников
-
Косматов В.И. Проектирование электроприводов металлургического производства: Учебное пособие. 3-е изд. перераб.-Магнитогорск: МГТУ, 2002.-224 с. -
Электрооборудование металлургических кранов [Текст]/ Б. М. Рапутов - М.: Металлургия, 1977 - 248 c -
Косматов В.И. Электрический привод: Учебное пособие. – Магнитогорск: ГОУ ВПО «МГТУ», 2012. -
Чунихин А.А. Электрические аппараты: Учебник для вузов. — 3-е изд., перераб. и доп. — М.: Энергоатомиздат, 1988. — 720 с. -
СМК-О-СМГТУ-36-16: Стандарт организации. Курсовая работа: структура, содержание, общие правила выполнения и оформления. Магнитогорск, 2016