Файл: Пояснительная записка выпускной квалификационной работы содержит 55 страниц формата А4, 12 рисунков, 8 таблиц, 5 используемых источников информации.docx
ВУЗ: Не указан
Категория: Не указан
Дисциплина: Не указана
Добавлен: 26.10.2023
Просмотров: 51
Скачиваний: 2
ВНИМАНИЕ! Если данный файл нарушает Ваши авторские права, то обязательно сообщите нам.
СОДЕРЖАНИЕ
1.1 Назначение, состав и техническая характеристика механизма
1.3 Требования, предъявляемые к приводу
2 Расчёт мощности и выбор двигателя
2.1 Расчёт статических моментов
2.2 Предварительный выбор двигателя
2.3 Расчёт нагрузочной диаграммы
2.4 Проверки двигателя по нагреву и перегрузочной способности
3 выбор и характеристика основного электрооборудования
3.1 Выбор и характеристика преобразователя частоты
3.2 Выбор и характеристика силового трансформатора
4 Расчёт и построение статических характеристик
5.1 Защита от перегрузки и коротких замыканий
6 Разработка системы управления мехатронной системой
1.3 Требования, предъявляемые к приводу
Для качественного выполнения подъема, спуска и перемещения грузов электропривод крановых механизмов должен удовлетворять следующим основным требованиям:
-
Высокая плавность регулирования скорости; -
Диапазон регулирования скорости должен составлять не менее 30:1; -
Ошибка регулирования скорости не должна превышать 5%; -
Обеспечение заданного ускорения и замедления с жидким металлом не более 0,1..0,2 м/с2, ускорение механизма подъёма не более 0,5 м/с2; -
Реверсирование электропривода и обеспечение его работы, как в двигательном режиме, так и в тормозном режиме, с обеспечением рекуперации энергии в сеть; -
Повышенная надёжность электрооборудования.
2 Расчёт мощности и выбор двигателя
2.1 Расчёт статических моментов
Статический момент в двигательном режиме при подъеме груза на валу двигателя определяется по формуле:
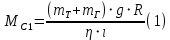
где


g – ускорение свободного падения, м/с2;
R – радиус канатного барабана, м;



Статический момент в генераторном режиме при опускании груза определяется по формуле [1]:

где


g – ускорение свободного падения, м/с2;
R – радиус канатного барабана, м;



Статический момент в двигательном режиме при подъёме траверсы на валу двигателя определяется по формуле [1]:
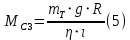
где

g – ускорение свободного падения, м/с2;
R – радиус канатного барабана, м;



Статический момент в генераторном режиме при опускании траверсы на валу двигателя определяется по формуле [1]:
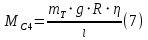
где

g – ускорение свободного падения, м/с2;
R – радиус канатного барабана, м;



2.2 Предварительный выбор двигателя
Для начала рассчитаем момент инерции привода, приведенный к валу двигателя при подъеме груза [2]:

где


, кг∙м2;
mт и mг – масса траверсы и груза, кг;
R - радиус канатного барабана, м;


Далее переходим к расчету момента инерции привода, приведённый к валу двигателя при опускании груза [2]:

где


mти mк – масса траверсы и ковша, кг;
R - радиус канатного барабана, м;


После переходим к моменту инерции привода, приведённого к валу двигателя при подъёме/опускании траверсы [2]:

где


mт– масса траверсы, кг;
R - радиус канатного барабана, м;


Определим мощность двигателя следующим выражением [2]:

где



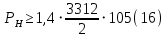

Выбираем двигатель фирмы SIEMENS модель 1MA8-317–6BD с номинальными параметрами, приведёнными в таблице 5.
Таблица 5–Номинальные параметры предварительно выбранного двигателя
Название | SIEMENS 1MA8-317–6BD |
Мощность, кВт | 215 |
Скорость, об/мин | 990 |
КПД, % | 96 |
Ток, А | 380 |
Момент, Н∙м | 2070 |
Напряжение, В | 380 |
cosφ | 0.88 |
Момент инерции, кг∙м2 | 7.3 |