ВУЗ: Не указан
Категория: Не указан
Дисциплина: Не указана
Добавлен: 09.11.2023
Просмотров: 525
Скачиваний: 2
СОДЕРЖАНИЕ
1.1 Служебное назначение, техническая характеристика и описание изделия
2.1 Обоснование темы курсового проекта
2.3 Выбор детали для разработки технического процесса ее изготовления
3.1 Описание детали, материала и его свойства
3.2 Анализ технологического изготовления детали
3.3 Определение типа производства и его характеристика
3.4 Выбор и обоснование вида заготовки
3.5 Технико-экономическое обоснование методов получения изготовления
3.6 Определение конфигурации и допусков исходных материалов
3.7 Требования к графическому изображению исходной заготовки
3.9 Выбор методов и количества необходимых переходов обработки
4. Формирование маршрутного технологического процесса изготовления
5.Методы расчета припусков на механическую обработку
6.Нормирование ставочных работ
7.Обоснование выбора оборудования, приспособлений, режущего и измерительного инструмента
7.1 Обоснование выбора и описание основного технологического оборудования
7.2 Обоснование выбора и описание технологической оснастки
7.4 Обоснование выбора и описание измерительного инструмента
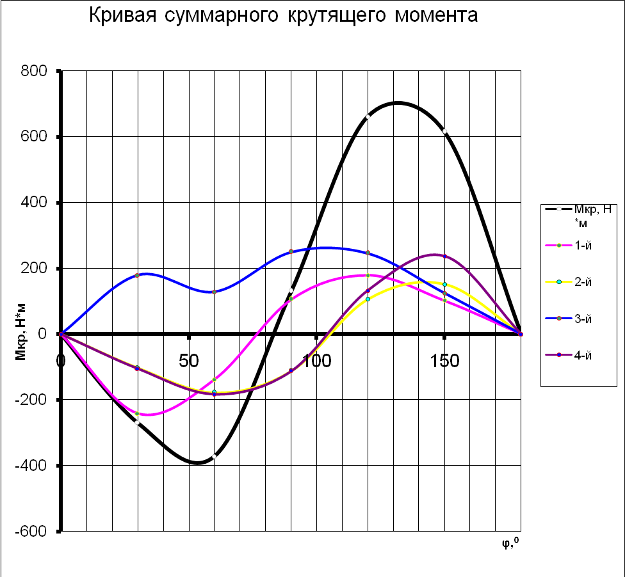
Рис. 46 – Кривая суммарного крутящего момента
7.1 Обоснование выбора и описание основного технологического оборудования
Задняя подвеска – зависимая с винтовыми цилиндрическими пружинами и гидравлическими амортизаторам.
Балка заднего моста закреплена на кузове четырьмя продольными (реактивными) и одной поперечной штангами на резинометаллических шарнирах одинаковой конструкции (сайлент-блоках).
Пружины упираются нижними концами через пластмассовые прокладки в чашки, приваренные к балке заднего моста, а верхними концами – через резиновые виброизолирующие прокладки, в кузов. Ход сжатия пружин ограничен цилиндрическими упорами, являющимися частью кузова автомобиля. На торцах упоров установлены резиновые буферы.
7.2 Обоснование выбора и описание технологической оснастки
Дополнительный буфер сжатия установлен на кронштейне над картером редуктора.
Амортизаторы крепятся на разборных резинометаллических шарнирах – верхними проушинами к шпилькам на кронштейнах кузова, а нижними – к кронштейнам на балке заднего моста.
7.3 Обоснование выбора и описание режущего инструмента
Для обработки наружных поверхностей и внутренних поверхностей при токарной обработке применяются резцы со сменными многогранными пластинами, это позволяет сократить время на наладку инструмента:
- черновая обработка материал режущей части ВК10;
- чистовая ВК6;
Для обработки наружных поверхностей применяется резец упорный с углом φ=95˚.
Фрезерная обработка: материал режущей части Р6М5.
Обработка отверстий: сверление отверстий производится сверлами с материалом режущей части ВК8. Зенкерование, развертывание производится зенкером и разверткой с материал режущей части Р6М5
Шлифование отверстия выполняется кругом ГОСТ 2424-83.
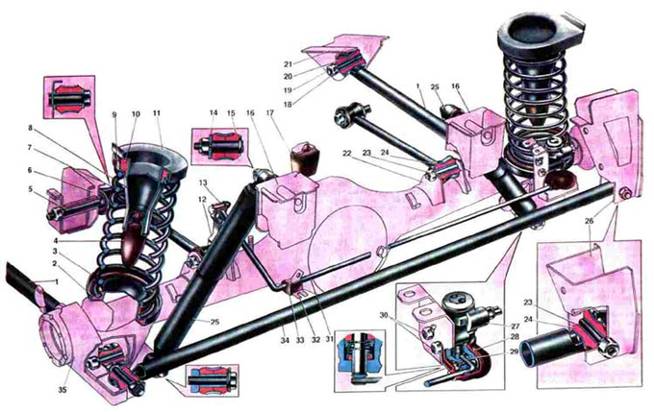
Рис. 47 – Задняя подвеска
Задняя подвеска: 1. Нижняя продольная штанга; 2. Нижняя изолирующая прокладка пружины подвески
; 3. Нижняя опорная чашка пружины подвески; 4. Буфер хода сжатия; 5. Болт крепления верхней продольной штанги; 6. Кронштейн крепления верхней продольной штанги; 7. Пружина подвески; 8. Опора буфера хода сжатия; 9. Верхняя обойма прокладки пружины; 10. Верхняя изолирующая прокладка пружины; 11. Верхняя опорная чашка пружины подвески; 12. Стойка рычага привода регулятора давления; 13. Резиновая втулка рычага привода регулятора давления; 14. Шайба шпильки крепления амортизатора; 15. Резиновые втулки проушины амортизатора; 16. Кронштейн крепления заднего амортизатора; 17. Дополнительный буфер хода сжатия; 18. Шайба распорной втулки; 19. Распорная втулка нижней продольной штанги; 20. Резиновая втулка нижней продольной штанги; 21. Кронштейн крепления нижней продольной штанги; 22. Кронштейн крепления верхней продольной штанги к балке моста; 23. Распорная втулка поперечной и продольной штанг; 24. Резиновая втулка верхней продольной и поперечной штанг; 25. Задний амортизатор; 26. Кронштейн крепления поперечной штанги к кузову; 27. Регулятор давления тормозов; 28. Защитный чехол регулятора давления; 29. Ось рычага привода регулятора давления; 30. Болты крепления регулятора давления; 31. Рычаг привода регулятора давления; 32. Обойма опорной втулки рычага; 33. Опорная втулка; 34. Поперечная штанга; 35. Опорная пластина кронштейна крепления поперечной штанги.
7.4 Обоснование выбора и описание измерительного инструмента
Для контроля размеров детали применяется как стандартизированный инструмент, так и нестандартный. Для контроля отверстий применяются предельные калибры - пробки, для наружных цилиндрических поверхностей п калибр-скобы.
Средства контроля:
-
Штангенциркуль ШЦ-I-125-0.05 ГОСТ 166-89 -
Штангенциркуль ШЦ-II-400-0.1 ГОСТ 166-89 -
Калибр пробка 8133-0926 H7 ГОСТ 14810-69 ø12 -
Пробка 8221-3036 ГОСТ 17758-72 -
Штангензубомер ШЗН-18 ГОСТ 1643-81 -
Профилометр Surftest SJ-410 Mitutoyo
Заключение
Замена рулевых наконечников это трудоемкий процесс, которое отнимает время. Но можно и самому поменять наконечники, но после замены обязательно нужно в авосервисе провести диагностику сход – развала. Конечно, в целях экономии средств можно менять только один наконечник, а второй «еще походит». С другой стороны, в целях экономии времени и сил гораздо выгоднее поменять сразу оба.
После окончания ремонта не забудьте протянуть колесные болты на земле, а не в подвешенном расстоянии. Следите за состоянием своего автомобиля на должном уровне.
Список литературы
-
ГОСТ 24932-81. Калибры для конических соединений. Допуски. -
ГОСТ 12.0.003-2015 - Система стандартов безопасности труда (ССБТ). Опасные и вредные производственные факторы. Классификация -
Аверченков В.И. Технология машиностроения. Сборник задач и упражнений. Издательство: ИНФРА-М Год: 2016. – 334 с. -
Аверьянов И.Н. Проектирование и расчет станочных и контрольно-измерительных приспособлений в курсовых и дипломных проектах. Рыбинск. 2017. – 218 с. -
Косилова А.Г., Мещеряков Р.К. Справочник технолога-машиностроителя. Т2. М.: Машиностроение, 2017. – 345 с. -
Кувалдин Ю.И. Расчет припусков и промежуточных размеров при обработке резанием: учебное пособие для практических занятий, курсового и дипломного проектирования / Ю.И. Кувалдин, В.Д. Перевощиков. Киров: Изд-во ВятГУ, 2015. - 163 с. -
Мамаев В.С., Осипов Е.Г. Основы проектирования машиностроительных заводов. М., «Машиностроение» 2015. - 290 с. -
Мельников Г.Н., Вороненко В.П. (1990) Проектирование механосборочных цехов. М., «Машиностроение» 2014. - 352 с. -
Методические указания по организации и выполнению выпускной квалификационной работы. Санкт-Петербург. Академия машиностроения имени Ж.Я. Котина. 2019. – 218 с. -
Наерман. М. Справочник молодого шлифовщика. М.: Высш. шк. 2016. - 207 с. -
Общемашиностроительные нормативы времени вспомогательного, на обслуживание рабочего места и подготовительно заключительного для технического нормирования станочных работ. Серийное производство. М.: Высш. шк. – 2017. – 440 с. -
Охрана труда и окружающей среды. Методические указания к выполнению выпускной квалификационной работы для обучающихся всех специальностей. Санкт-Петербург. Академия машиностроения имени Ж.Я. Котина. 2019. -
Стружестрах Е.И. Справочник нормировщика-машиностроителя. Том 2. Техническое нормирование станочных работ. Москва 1961. 863 с.
Приложение

Задняя подвеска