Добавлен: 12.12.2023
Просмотров: 299
Скачиваний: 8
СОДЕРЖАНИЕ
1 Характеристика предприятия и объекта проектирования
1.2 Характеристика объекта проектирования
2 Расчетно-технологический раздел
2.3. Определение коэффициента технической готовности
2.4. Определение коэффициента использования автомобилей
2.5. Определение суммарного годового пробега автомобилей в АТП
2.6. Определение годовой программы по техническому обслуживанию и диагностике автомобилей
2.7. Расчет сменной программы по видам ТО и диагностики
2.8. Определение трудоемкости технических воздействий
2.9. Определение общей годовой трудоемкости технических воздействий
2.10. Определение количества ремонтных рабочих на объекте проектирования
3.1 Выбор метода организации производства ТО и ТР на АТП
3.2 Схема технологического процесса на объекте проектирования
3.2 Выбор режима работы производственных подразделений
3.4 Распределение исполнителей по специальностям и квалификации
3.5Подбор технологического оборудования
3.6 Планировка объекта проектирования
3 Организационный раздел
3.1 Выбор метода организации производства ТО и ТР на АТП
Среди прочих методов организации производства ТО и ремонта в настоящее время наиболее прогрессивным является метод, основанный на формировании ремонтных подразделений по технологическому принципу (метод технологических комплексов) с внедрением централизованного управления производством (ЦУП).
Основные организационные принципы этого метода заключаются в следующем:
-
Управление процессом ТО и ремонта подвижного состава в АТП осуществляются централизованно отделом (центром) управления производством. -
Организация ТО и ремонта в АТП основывается на технологическом принципе формирования производственных подразделений (комплексов), при котором каждый вид технического воздействия (ЕО, ТО-1, ТО-2, Д-1, Д-2, ТР автомобилей, ремонт агрегатов) выполняется специализированными подразделениями. -
Подразделения (бригады, участки и исполнители), выполняющие однородные виды технических воздействий, для удобства управления ими объединяются в производственные комплексы:
– комплекс технического обслуживания и диагностики (ТОД);
– комплекс текущего ремонта (ТР);
– комплекс ремонтных участков (РУ).
-
Подготовка производства (комплектование оборотного фонда, доставка агрегатов, узлов и деталей на рабочие места и с рабочих мест, мойка агрегатов, узлов и деталей перед отправкой в ремонт, обеспечение рабочим инструментом, перегон автомобилей в зонах ожидания ТО и ремонта) осуществляется, централизовано комплексом подготовки производства (ПП). -
Обмен информацией между отделом управления и всеми производственными подразделениями базируется на двусторонней диспетчерской связи, средствах автоматики и телемеханики.
Основной задачей ЦУП является сбор и обработка информации о состоянии производственных ресурсов и объемах работ, подлежащих выполнению, а также планирование и контроль за деятельностью производственных подразделений на основе анализа имеющейся информации. ЦУП состоит из двух подразделений: отдела оперативного управления и отдела обработки и анализа информации.
При централизованной системе управления производственные подразделения, организованные по бригадам для удобства управления должны объединяться в производственные комплексы.
Проектируемый сварочно-жестяницкий участок АТП относится к комплексу РУ, где между участком и ЦУП существует оперативное подчинение.
Управлениеучасткомпроисходитчерезначальникаремонтногоучастка,намастератекущегоремонта,инаотделениепоремонтутопливнойаппаратурыдизельногодвигателя.МастертекущегоремонтаимеетоперативноеподчинениечерезЦУП.
Схема управления объектом, представленная на рисунке 3.2, состоит из трех звеньев. Первое звено: старший мастер производства. Он подчиняется главному инженеру и осуществляет руководство всеми работами, выполняемыми в соответствующих производственных подразделениях. Мастер участка, который является вторым звеном схемы. В его подчинении находится сам сварочно-жестяницкий участок, который является третьим и заключительным звеном схемы. В нем осуществляются непосредственные работы по ремонту кузова и других металлических частей автомобиля.
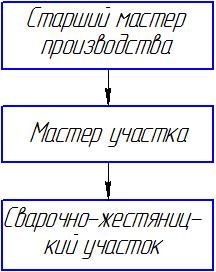
Рисунок 4.2 – Схема управления сварочно-жестяницким участком
3.2 Схема технологического процесса на объекте проектирования
На участок поступает заявка на ремонт автомобиля с указанием неисправностей целостности кузова (рамы) и других элементов. Заявка оформляется на специалиста. Автомобиль предварительно перед заездом в ремонтно-механические мастерские (РММ) моется. А затем устанавливается на специально отведенный участок в РММ.
Внешним осмотром специалист дает заключение о снятии дефектной детали либо ремонте ее на автомобиле. Затем дефектная деталь правится (рихтуется) подгоняется починочный материал. Далее починочный материал сваривается к детали и отремонтированная деталь устанавливается на автомобиль либо сдается на склад оборотных агрегатов.
Схема технологического процесса обслуживания автомобилей на сварочно-жестяницком участке представлена на рисунке 3.3.
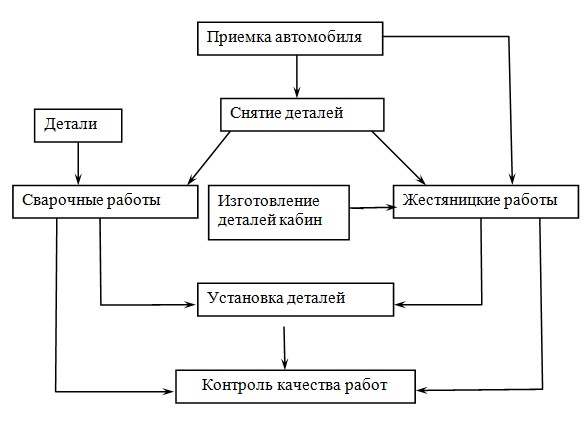
Рисунок 3.3 – Схема технологического процесса на сварочно-жестяницком участке
На участке выполняются работы по устранению дефектов в автомобильных деталях из стали, алюминиевых сплавов и чугуна с помощью ручной дуговой сварки, аргонно-дуговой сварки, газовой сварки и наплавки.
Детали, подлежащие ремонту после очистки и сушки поставляются в сварочное отделение, крупногабаритные или тяжёлые детали и части доставляются в помещение сварочного отделения с помощью перекатной тележки. Затем производится внешний осмотр и дефектовка детали. Подбирается необходимый вид ремонта и соответствующее оборудование.
Для соединения листов металла используется сварка сплошным или прерывистым швом. Сплошной шов используется, если элементы кузова располагаются встык, а прерывистый при наличий зазора между листами.
Перед началом сварки, свариваемое изделие зачищают место вокруг сварки от ржавчины, грязи, краски, нагара. После зачистки поверхности изделия обезжиривают бензином или ацетоном. После сборки отдельных частей изделия проверяют правильность сборки и производят наложение прихваток. После окончания сварки должен быть отбит шлак со шва изделия.
При газовой сварки применяют ацетиленовые генераторы или баллоны с ацетиленом; баллоны с кислородом, редукционные вентили для регулирования рабочего давления газа, набор горелок, резаков и наконечников к ним; стол для сварочных работ. Ацетилен получают в специальных аппаратах-генераторах в результате разложения карбида кальция при действии на него воды.
При газовой сварке используется газовая горелка, в которой смешиваются в определенных пропорциях кислород и ацетилен, давая при воспламенении пламя высокой температуры. Оба газа поступают по шлангам от газовых баллонов через редукторы, снижающие давление.
Для сварки постоянным током используют стационарные электрогенераторы СМГ-2а и СМГ2б или передвижные типа СУГ; переменным током-сварочные агрегаты типа СТЭ-22. При электросварке используют металлические столы с контактом для крепления одного из проводов. Также для ручной дуговой сварки применяют сварочные выпрямители ВД-306 для преобразования переменного тока в постоянный.
Сварку выполняют на постоянном токе. Источником постоянного тока является выпрямитель. Для возбуждения дуги необходимо коснуться свариваемого изделия торцом электрода и сейчас же отвести электрод от изделия на 3–4 мм. В зависимости от марки стали, выбираю тип (Э46А) и марку электрода (УОНИИ13/45). В зависимости от толщины металла (1 мм) выбираю диаметр электрода (1,6мм), и по диаметру электрода выбираю силу тока,(45-55А).
Жестяницкие работы предназначены для устранения вмятин, трещин, разрывов, а также в частичном изготовлении деталей кузовов. Помятые места обшивки и оперения кабины и кузова исправляют, как правило, вручную, специальным инструментом (металлическими и деревянными молотками, различными оправками) и приспособлениями. Сквозные пробоины, трещины и разрывы крыльев или облицовки кузова устраняют с помощью газовой сварки. При изготовлении материала для заделки сквозных пробоин применяют механические и ручные ножницы для резки листового металла. При ремонте
поврежденное место вырезают жестяницкими ножницами, острым зубилом, при разрушении значительной части оперения заменяют новой.
Правку осуществляют на правильных плитах. При правке листового материала толщиной менее 1 мм применяют деревянные или металлические молотки. Перед правкой листового материала вначале выявляют все выпуклости и отмечают их мелом, затем лист укладывают, на правильную плиту так чтобы выпуклости находились, сверху. После этого начинают наносить удары молотком с одного края в направлении выпуклости, а затем с другого края.
Вмятины на крыльях, капоте и кузове автомобиля выправляют сначала при помощи фигурных рычажков, затем под вмятину устанавливают болванку или оправку и ударами металлического или деревянного молотка выправляют вмятину.