Файл: Курсовая работа (курсовой проект) по учебному курсу Технология машиностроения Вариант 1 (при наличии).docx
Добавлен: 24.10.2023
Просмотров: 241
Скачиваний: 6
ВНИМАНИЕ! Если данный файл нарушает Ваши авторские права, то обязательно сообщите нам.
4. Проектирование маршрута и плана обработки
4.1Выбор типового технологического процесса
При разработке технологического процесса изготовления любой детали в машиностроительном производстве возникает задача – выбрать из нескольких вариантов разработки один, обеспечивающий наиболее экономичное решение. Поэтому с целью экономии труда и времени технологической подготовки производства необходимо использовать типовые процессы обработки деталей и типовых поверхностей деталей. Типовой технологический процесс обработки червяков и колес червячных передач состоит из следующих основных этапов:
-
Обработка заготовки резанием для получения необходимых геометрических форм, а также основных базовых поверхностей. -
Повторная обработка резанием и дополнительное формообразование детали. -
Черновое зубонарезание для червяков и колес. -
Термическая обработка. -
Обработка монтажных и базовых поверхностей после термической обработки. -
Окончательная обработка и отделка зубьев червяков после термической обработки.
Кроме получения точных размеров и формы червяка и червячного колеса в делительной передаче необходимо, чтобы технологический процесс их изготовления обеспечивал длительное сохранение полученных размеров и формы. Эта задача решается в результате придания материалам червяка и колеса нужной структуры, твердости и равновесия внутренних напряжений, соответствующими способами получения заготовок, режимами термической обработки и распределением съема припусков между последовательными операциями механической обработки. Соответственно в технологический процесс необходимо включить металлографический контроль заготовок, определение твердости и проверка отсутствия трещин.
Таким образом, учитывая особенности изготовления, укрупненный технологический маршрут обработки делительного червяка из цементуемой стали выглядит следующим образом:
-
ковка заготовки; -
отжиг поковки; -
черновое обтачивание поковки; -
высокий отпуск; -
предварительная механическая обработка; -
высокий отпуск; -
цементация; -
нормализация и высокий отпуск; -
промежуточная механическая обработка для снятия цементационного слоя; -
закалка и низкий отпуск; -
первое получистовое шлифование; -
стабилизирующий отпуск; -
второе получистовое шлифование; -
стабилизирующее старение; -
окончательное шлифование.
Схема распределения припусков по различным операциям в процессе механической обработки витков делительного червяка показана на рис.1.
Предварительная механическая обработка заканчивается шлифованием витков (рис.1) для выравнивания припуска и толщины цементованного слоя. При предварительном точении снимается припуск 1,0–1,5 мм по толщине витка, а при предварительном шлифовании – 0,15- 0,20 мм. При первом получистовом шлифовании витков снимается наибольший припуск (55-60%) для устранения деформаций и черноты поверхности, полученных при термической обработке. Для обеспечения одинаковой толщины цементованного слоя необходимо уделять особое внимание равномерности съема припуска с обеих сторон витка. Уже на этом этапе осуществляется согласование толщины витка червяка с толщиной витка шевера.
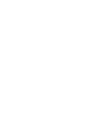
Рис.4.1 Распределение припусков при обработке однозаходного червяка по операциям:
1 – черновая прорезка; 2 – предварительная проточка; 3 – предварительное шлифование;
4 – 1-ое получистовое шлифование; 5 - 2-ое получистовое; 6 – чистовое шлифование
Достигаемая точность обработки червяка определяется в основном последними операциями шлифования профиля. Второе получистовое шлифование производится уже с высокой точностью на червячно- или резьбошлифовальных станках классов точности А и С, причем используется станок, на котором шлифовался шевер, предназначенный для нарезания колеса, сопрягаемого с данным червяком (соблюдаются условия идентичности их винтовых поверхностей). Наиболее подходят для этой цели станки мод. 5822 и МВ-107. При чистовом шлифовании витков обеспечивают требуемую чертежом шероховатость поверхности, толщину витка и идентичность винтовой поверхности с режущей поверхностью шевера. При этом снимается припуск по толщине, равный 0,10-0,15 мм, причем за номинал принимается фактическая толщина витка шевера, уменьшенная на величину бокового зазора в паре.
Центровые отверстия червяка являются постоянными технологическими и измерительными базами. Поэтому после каждой операции термической обработки производится их восстановление притиркой чугунными или твердосплавными притирами на токарных станках или шлифованием на специальных станках. Требования к шероховатости, прилеганию центровых отверстий и величины биения базовой поверхности после соответствующего этапа механической обработки приведены в таблице 1.7.
Таблица 1.7
Операция, для которой подготовляется центровое отверстие | Площадь пятна контакта в % | Ra, мкм | Биение базовой поверхности в мм |
Предварительное точение................ Предварительное шлифование........ Промежуточное точение.................. 1-ое получистовое шлифование....... 2-ое получистовое шлифование....... Чистовое шлифование...................... | 50-60 50-60 60 80 90 100 | 12,5 6,3 3,2 1,6 0,8 0,4 | 0,050-0,060 0,020-0,025 0,020-0,025 0,012-0,016 0,008-0,01 0,0025-0,006 |
Наша деталь отличается от детали, типовой маршрут изготовления которой рассмотрен выше. Рассмотрим отличия:
-
Операция 2-ого получистового шлифования поверхности червяка и стабилизирующее старение исключается из процесса обработки, поскольку данная операция производится для делительных червяков 3-4-ой степени точности. В данном случае для обеспечения выполнения требований к качеству поверхностного слоя червяка достаточно одной операции получистового шлифования. -
Для обеспечения требований к базовым поверхностям операцию получистового шлифования можно исключить, так как применяется средство активного контроля (двухконтактная скоба) при круглом врезном шлифовании. Данное следящее устройство обеспечит контроль шлифуемого размера непосредственно во время обработки и позволит сократить время обработки базовых поверхностей и количество операций шлифования. -
Операцию нарезания наружной резьбы (резьбонарезная операция) необходимо выполнить до закалки детали.
Технологический маршрут обработки делительного червяка полностью представлен в п.1.3.6 пояснительной записки.
4.2 Особенности обработки деталей на станках с ЧПУ
Так как деталь “Вал червячный” предназначена для передачи крутящего момента в делительной цепи коробки передач зубообрабатывающего станка, следовательно, к ней предъявляются высокие требования по точности и шероховатости поверхности (подробнее см. раздел 1.1.5). Кроме того, предполагается выпускать 1000 деталей в год (среднесерийное производство). В данном случае применение универсального оборудования нецелесообразно, так как при среднесерийном производстве обработку ведут на предварительно настроенных станках, количество обрабатываемых поверхностей на одной операции (токарный станок) ограничивается четырьмя (2 цилиндра и 2 торца). Ко всему прочему, универсальные станки могут не дать требуемой точности. В результате для обработки детали понадобится большое количество универсальных станков, следовательно, большое число рабочих, наладчиков и т. д. Все эти проблемы будут устранены путем применения оборудования с ЧПУ. Несмотря на более высокую стоимость, данные станки при применении соответствующего инструмента, режимов резания и правильной технологии обладают высокой производительностью и позволяют получить большую точность. Поэтому токарные операции будут выполняться на станках с ЧПУ. Приведем некоторые аспекты и особенности обработки на станках с ЧПУ [10].
Проектирование токарной операции является частью более общей задачи разработки технологического процесса изготовления детали. Необходимо знать не только, в каком виде заготовка поступает на токарную операцию, но и какова должна быть ее точность после обработки. Технологическую разработку токарной операции на станках с ЧПУ начинают с составления эскиза заготовки в том виде, который она принимает после предшествующей обработки с указанием всех размеров и технических требований. Рекомендуется на эскизе тонкими линиями показать контур детали, получаемый после обработки, с указанием допустимых отклонений и качества поверхности.
Несмотря на то, что перед разработкой технологических процессов проводится анализ технологичности детали, при проектировании токарной операции на станках с ЧПУ рекомендуется дополнительно проанализировать ее технологичность. При этом обращается внимание на унификацию элементов детали, упрощение геометрической формы, обеспечение жесткости при обработке.
При применении станков с ЧПУ необходимо наиболее полно использовать технологические возможности этого оборудования. Для каждого станка имеется определенный комплект инструмента. Следует проверить возможность обработки детали с его применением. В случае необходимости разрабатывают предложения по изменению конструкции детали.
Наибольший эффект достигается при использовании станков с ЧПУ для решения наиболее сложных технологических задач, например для обработки деталей сложного профиля, в случае высокой концентрации переходов обработки, исключения слесарных работ и сложных приспособлений. На станках с ЧПУ нецелесообразно обрабатывать детали с числом ступеней меньше трех и детали, время установки и выверки которых велико. Станок с ЧПУ должен быть занят обработкой деталей одного наименования в год в течение 10 - 25 ч. На токарных станках с ЧПУ последовательность переходов обработки следующая:
а) предварительная (черновая) обработка основных участков поверхностей детали: подрезка торцов, центрирование перед сверлением отверстий диаметром до 20 мм, сверление (если используются два сверла, то вначале сверлом большего диаметра), рассверливание отверстий, точение (получистовая обработка) наружных поверхностей, а затем растачивание внутренних поверхностей;
б) обработка дополнительных участков поверхностей детали (кроме канавок для выхода шлифовального круга, резьбы и т.п.); в тех случаях, когда черновая и чистовая обработки внутренних поверхностей проводятся одним резцом, все дополнительные участки обрабатывают после чистовой обработки;
в) окончательная (чистовая) обработка основных участков поверхности детали, сначала внутренних, потом наружных;
г) обработка дополнительных участков поверхностей детали, не требующих черновой обработки: сначала в отверстиях или на торцах, затем на наружной поверхности.
Обработка на токарных станках с ЧПУ характеризуется следующей точностью. Однократная обработка поверхности обеспечивает точность 12-13-го квалитета и параметр шероховатости поверхности Rа 3,2 мкм. Радиус при вершине резца при этом назначают по наименьшему радиусу галтели на детали; в других случаях галтель выполняют по программе. При более высоких требованиях к качеству поверхности (Rа менее 1,6 мкм) на последнем чистовом переходе уменьшают подачу и увеличивают частоту вращения. При более высоких требованиях к точности (7- 9-го квалитета) окончательную обработку осуществляют чистовым резцом с коррекцией на размер. Для обеспечения высокой точности размеров при чистовой обработке резец устанавливают в такой плоскости, чтобы погрешность позиционирования револьверной головки не влияла на точность размера обрабатываемой поверхности.
Черновую обработку со снятием напуска проводят по-разному: если перепад диаметров ступеней больше длины ступени, то обработку ведут с поперечной подачей (в противном случае - с продольной подачей). Современные системы ЧПУ позволяют вести эту обработку по постоянному циклу. При составлении программы задают исходный и требуемый контур. Система ЧПУ автоматически формирует управляющие команды для выполнения обработки. Схемы перемещения инструментов при обработке основных участков поверхности приведены на рис. 18 – 20 [10]. Обычно эти участки обрабатывают черновыми, а затем чистовыми резцами.
На станках с ЧПУ фаски, канавки для выхода инструмента обрабатывают, как указано выше, или тогда, когда это наиболее целесообразно применительно к стойкости инструмента и производительности обработки. При этом учитывают, что работа вершины резца при врезании улучшается, если снята фаска. Если обработка начинается со снятия фасок, то детали будут без заусенцев (по этой же причине канавки выполняют нередко после чистового перехода). Фаски целесообразно снимать серединой режущего лезвия инструмента.
Для уменьшения трудоемкости программирования канавки сложной формы обрабатывают по типовой программе резцами за несколько переходов.