Файл: Физикотехнологические основы получения композиционных материалов.doc
ВУЗ: Не указан
Категория: Не указан
Дисциплина: Не указана
Добавлен: 07.11.2023
Просмотров: 290
Скачиваний: 4
СОДЕРЖАНИЕ
Физико-технологические основы получения композиционных материалов
1.1. Характеристика композиционных материалов
1.2. Классификация композиционных материалов
1.3. Требования, предъявляемые к армирующим и матричным материалам
Изготовление изделий из металлических композиционных материалов
2.3. Способы получения полуфабрикатов и готовых изделий
3.2. Краткая характеристика порошковых материалов
3.3. Приготовление смеси и формообразование заготовок
3.4. Спекание и окончательная обработка заготовок
4. Изготовление деталей из полимерных композиционных материалов
4.3. Способы формообразования деталей в высокоэластичном состоянии
5. Получение деталей из композиционных пластиков
7. Технологические особенности проектирования и изготовления деталей из композиционных материалов
7.1. Технологические требования к конструкциям изготовляемых деталей
7.2. Технологические особенности дополнительной механической обработки заготовок
В последнее время находят широкое применение так называемые гибридные КМ.
Гибридными называют КМ, содержащие в своем составе три или более компонентов. В зависимости от распределения компонентов гибридные КМ обычно делят на следующие классы: однородные КМ (рис. 2, а), с равномерным распределением каждого армирующего компонента по всему объему композиции; линейно неоднородные КМ с объединением отдельных волокон в жгуты (рис. 2, б);
КМ с плоскостной неоднородностью (рис. 2, в), в которых волокна каждого типа образуют чередующиеся слои, и макронеоднородные КМ, когда разнородные волокна образуют зоны, соизмеримые с характерным размером изделия из КМ (рис. 2, г). При этом возможно использовать структуру типа "оболочка - сердцевина". Такое сочетание компонентов рассматривается как наиболее перспективное. Конструктор, проектируя изделие из КМ, армирующие волокна (например, из углерода, бора и др.) помещает в оболочку из металлической проволоки, сетки, фольги и т.п. Такие "полуфабрикаты" характеризуются высокой технологичностью при изготовлении изделий из волокнистых КМ. Помимо рассмотренных возможны и другие сочетания компонентов в композиции.
По способу получения полимерные и резиновые КМ разделяют на литейные и прессованные. Металлические КМ аналогично делят на литейные и деформируемые. Литейные получают путем пропитки арматуры расплавленным матричным материалом (сплавом). Для получения деформируемых МКМ применяют спекание, прессование, штамповку, ковку на молотах и др.
1.3. Требования, предъявляемые к армирующим и матричным материалам
Армирующие материалы подразделяют на порошкообразные и волокнистые. Порошковые материалы должны удовлетворять требованиям по химическому составу, размерам и форме отдельных фракций, по технологическим свойствам (насыпная масса, текучесть, прессуемость, спекаемость) при изготовлении изделий порошковой металлургией. Они не должны содержать загрязнений, влаги, масел и других примесей, должны храниться в условиях, исключающих окислительные процессы на поверхности порошковых зерен.
Армирующие волокна, используемые для получения КМ, должны иметь следующие свойства: малую плотность, высокую температуру плавления, минимальную растворимость в материале матрицы, высокую прочность во всем интервале рабочих температур, высокую химическую стойкость, технологичность, отсутствие фазовых превращений в зоне рабочих температур, отсутствие токсичности при изготовлении и эксплуатации. Применяют в основном три вида волокон: нитевидные кристаллы, металлическую проволоку, неорганические и поликристаллические волокна.
Нитевидные кристаллы ("усы") рассматривают как наиболее перспективный материал для армирования металлов, полимеров, керамики. Сверхвысокая прочность в широком диапазоне рабочих температур, малая плотность, химическая инертность ко многим материалам матрицы и ряд других свойств делают их незаменимыми в качестве армирующих материалов. Однако широкое их внедрение сдерживается пока несовершенством технологии их получения в промышленных масштабах, сложностью ориентации их в материале матрицы, сложностью технологии деформирования изделий из композиций с нитевидными кристаллами и др.
Металлическая проволока из высокопрочной стали, вольфрама, молибдена и других металлов имеет меньшую прочность, чем нитевидные кристаллы. Однако ее выпускают промышленно в больших количествах и в связи с более низкой стоимостью широко применяют в качестве арматуры, особенно для КМ на металлической основе.
Неорганические и поликристаллические волокна имеют малую плотность, высокую прочность и химическую стойкость. Широко применяют углеродные, борные, стеклянные и другие волокна для армирования пластмасс и металлов.
Основное назначение наполнителей -придание КМ специальных свойств. Например, волокнистые наполнители вводят с целью получения максимальных прочностных характеристик.
Матрица в армированных композициях является основой, придает изделию форму и делает материал монолитным. Материал матрицы должен позволять композиции воспринимать внешние нагрузки. Матрица принимает участие в создании несущей способности композиции, обеспечивая передачу силы на волокна. При нагружении за счет пластичности матрицы силы от разрушенных или дискретных (коротких) волокон передаются соседним волокнам. Передача нагрузки зависит прежде всего от качества соединений, т.е. от хорошей адгезии между компонентами КМ. Без этого невозможны передача нагрузки волокон и, следовательно, армирование.
Получению качественного соединения способствуют взаимная диффузия с образованием твердого раствора; поверхностное химическое взаимодействие между компонентами композиции; отсутствие на поверхности раздела каких-либо загрязняющих слоев.
При изготовлении композиции в жидкой фазе материал матрицы должен смачивать армирующий материал (волокно). Качество соединения зависит от смачиваемости волокон материалом матрицы, что обусловливается определенной степенью физического и химического сродства компонентов. Процесс смачивания сопровождается чаще всего частичным растворением волокон в материале матрицы или их химическим взаимодействием. Следовательно, смачивание почти всегда приводит к поверхностному разрушению волокна. Но без химического взаимодействия невозможно смачивание.
Смачивание зависит также от взаимного физического сродства компонентов, т.е. от соотношения их поверхностных энергий (рис. 3).
а) 6)
С
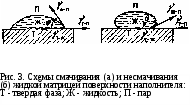
пособность жидкой матрицы смачивать или не смачивать наполнитель зависит от соотношения сил поверхностного натяжения на границах твердая фаза - жидкость (γт - ж), жидкость - пар (γ
ж - п) и твердая фаза - пар (γт - п).
Если γт - п > γт - ж + γж - п cos θ, смачивание удовлетворительное, и наоборот, если γт - ж > γт - п + γж - п cos θ, смачивание неудовлетворительное. Исследование смачивания обычно проводят путем нанесения капли жидкого материала матрицы на подложку из материала наполнителя. О смачиваемости судят по величине краевого угла θ (рис. 3, а, б).
Смачивание может быть улучшено средствами, влияющими на первоначальное равновесие между силами поверхностного натяжения. Наиболее эффективные способы улучшения смачиваемости - нанесение на армирующие волокна специальных покрытий и введение в материал матрицы специальных легирующих добавок. Улучшить смачивание при пропитке волокон металлическими расплавами можно, применив ультразвуковую обработку жидкой фазы. В отдельных случаях положительный эффект может быть достигнут за счет повышения температуры расплава и увеличения времени нахождения композиции в жидком состоянии.
Таким образом, создавая новые КМ жидкофазными способами, следует принимать во внимание, что материал матрицы должен полностью смачивать армирующие волокна, не должен разъедать или иным способом разрушать волокна. Кроме того, матрице отводится роль защитного покрытия, предохраняющего волокна от механических повреждений и окисления.
Изготовление изделий из металлических композиционных материалов
2.1. Волокна для армирования композиционных материалов
Для армирования КМ с металлической матрицей используют освоенные промышленностью высокопрочные волокна углерода, бора, карбида кремния и вольфрама, оксидов алюминия и циркония, проволоку из стальных, вольфрамовых и молибденовых сплавов, а также нитевидные кристаллы ("усы").
Волокна углерода и бора используют обычно для армирования легких сплавов на основе алюминия и магния. Изделия из этих КМ характеризуются высокими прочностью и жесткостью и могут длительно эксплуатироваться при температурах 300 - 450 °С. Волокна бора с барьерным покрытием из карбида кремния могут успешно эксплуатироваться при температурах 600 °С и даже до 800 °С при соответствующем материале матрицы.
Волокна карбида кремния и вольфрама предназначены для армирования жаропрочных КМ на основе никелево-хромистых сплавов с рабочими температурами 1100 - 1300 °С.
Термостойкие и жаропрочные волокна из оксидов алюминия и циркония могут быть эффективными при армировании КМ, длительно работающих при температурах 1400 - 1600 °С.
Проволоку из стальных, вольфрамовых и молибденовых сплавов широко используют для армирования высокопрочных КМ.
Нитевидные кристаллы весьма перспективны в качестве армирующего материала для получения высокопрочных и жаропрочных КМ.
Волокна углерода относятся к числу перспективных армирующих элементов в связи с низкой плотностью (1400 - 2000 кг/м3), высокими пределом прочности при растяжении (до 3500 МПа), модулем упругости (до 700000 МПа) и малым диаметром волокон (5 - 12 мкм).
Для получения волокон углерода в качестве сырья используют органические волокна из вискозы (целлюлозные искусственные волокна) и полиакрилнитрила (поливиниловое синтетическое волокно), которые получают выдавливанием полимера в вязкотекучем состоянии через фильеры определенного размера. В качестве сырья используют также пеки из каменноугольной смолы или нефти.
Волокна углерода получают путем последовательного нагрева исходного полимерного волокна до температур, превышающих температуру деструкции полимера. На первом этапе исходное сырье нагревают до температуры 200 - 300°С. При этом волокна окисляются и возникают поперечные связи между макромолекулами. На втором этапе волокна нагревают до температуры 1000 - 1500°С, при этом волокно уже на 80 - 95% состоит из элементарного углерода. После термообработки (при 1500 - 3000°С) получают волокна, содержащие 98 - 99% углерода, закристаллизовавшегося в систему, близкую к графиту.
Например, процесс получения волокон углерода из полиакрилнитрильного сырья проводят по следующей схеме: нагрев исходного волокна до температуры 220°С и выдержка в течение 20 ч, затем температуру повышают до 980°С и выдерживают в атмосфере водорода 24 ч; на следующем этапе волокно выдерживают в течение 2 ч при температуре 2480 - 2500 °С и создают принудительную вытяжку волокна в течение 15 - 20 мин. Заключительную операцию термообработки проводят при температуре 2700°С в течение 15 мин. Вытягивание волокон углерода в процессе их производства улучшает ориентацию структуры и значительно повышает прочность и модуль упругости.
Волокна углерода имеют относительно высокую химическую стойкость к атмосферным условиям и некоторым кислотам (серной, азотной, соляной), что определяет их долговечность при хранении, а также долговечность КМ на их основе. Термостойкость при длительной эксплуатации не превышает 400°С. К недостаткам углеродных волокон следует отнести низкую прочность на сжатие, химическую активность при взаимодействии с расплавленными металлическими матрицами и малую смачиваемость, особенно с полимерными матрицами.
Волокна бора характеризуются низкой плотностью (2400 - 3000 кг/см3); прочностью при растяжении (до 3800 МПа) и модулем упругости (до 400000 МПа). Их получают осаждением бора из газовой смеси водорода и треххлористого бора на нагреваемую вольфрамовую проволоку (диаметром 10 - 12 мкм). В результате осаждения образуется сердечник из боридов вольфрама (диаметром 15 - 17 мкм), вокруг которого располагается слой поликристаллического бора. Сердечник образуется вследствие диффузии и взаимодействия бора с вольфрамовой проволокой. Поэтому в волокнах бора существует явно выраженная поверхность раздела между оболочкой и сердцевиной. Прочность волокон во многом зависит от появляющихся дефектов в процессе их получения. Снижение прочности в основном связано с появлением локальных дефектов структуры борного слоя в виде крупных кристаллов, инородных включений, трещин, пустот и др. Эти дефекты, имеющие технологическое происхождение, могут располагаться на поверхности волокон, в борном слое, в сердцевине и на границе раздела между ними.
В промышленных условиях возможно изготовление волокон диаметром 75 - 200 мкм. Производительность процесса во многом зависит от температуры осаждения. При пониженных температурах (980°С) скорость осаждения невелика. Однако повышение температуры (до 1200 - 1315 °С) одновременно приводит к росту крупных кристаллов, что заметно снижает прочность волокон. Для повышения термостойкости волокон на бор тем же способом наносят тонкий слой (2 - 6 мкм) карбидов кремния или бора.
В процессе получения волокон бора в качестве подложки могут быть использованы также углеродные нити.
Высокая температура плавления бора (2050°С) определяет как термостойкость волокон бора, так и высокую поверхностную энергию, необходимую для обеспечения хорошей смачиваемости. Это оказывает положительное влияние на технологические свойства волокон бора.
Волокна карбида кремния определяются следующими физико-механическими характеристиками: плотностью 3200 - 3500 кг/м3, прочностью при растяжении 1700 - 2500 МПа, модулем упругости 450000 - 480000 МПа. Они жаростойки и жаропрочны и поэтому весьма перспективны для создания КМ на металлической основе с высокотемпературными характеристиками.
Волокна карбида кремния получают в вертикальных реакторах по аналогичной схеме, как и при получении волокон бора. Сердечником при этом служат вольфрамовая проволока или пековые моноволокна углерода. В последнем случае прочность и термостойкость волокон карбида кремния существенно повышаются из-за более низкого уровня напряжений между оболочкой и сердечником. Температура подложки при осаждении карбида кремния составляет 1100 - 1200 °С. Соотношение компонентов парогазовой фазы подбирают в зависимости от требуемого диаметра волокна, диаметра нити подложки и размеров реактора. Промышленностью освоен выпуск непрерывных волокон карбида кремния диаметром 80 - 120 мкм.
Высокая химическая стойкость к атмосферным воздействиям, практическое отсутствие реакции между материалами матрицы и волокнами и хорошая смачиваемость позволяют использовать эти волокна без нанесения барьерных покрытий при изготовлении КМ с металлической матрицей.
Волокна из оксидов алюминия, циркония характеризуются высокими прочностью и теплостойкостью. В настоящее время осваивается промышленный выпуск волокон из этих материалов.
Металлическая проволока - наиболее доступный и дешевый вид волокон, используемых для армирования КМ. Промышленностью уже давно освоено производство проволоки из различных металлов и сплавов. Для армирования КМ используют проволоки из высокоуглеродистых и высоколегированных сталей, характеризующихся высокими физико-механическими свойствами. В последнее время широко используют проволоки из вольфрамовых и молибденовых сплавов, специально выпускаемые для армирования КМ.
Нитевидные кристаллы ("усы") - тонкие короткие волокна с монокристаллической структурой. Технологически возможно получение кристаллов диаметром до 10 мкм и длиной до 10 мм. Характерно, что прочность "усов" резко возрастает с уменьшением диаметра. Например, нитевидный кристалл железа диаметром 3 мкм имеет прочность при растяжении более 12000 МПа, а при диаметре 10 мкм - менее 3000 МПа.
Наиболее распространенными способами получения нитевидных кристаллов являются выращивание из покрытий, выращивание в электрическом поле, осаждение из газовой фазы, химические способы.
Выращивание нитевидных кристаллов из покрытий может происходить самопроизвольно при нормальной температуре из легкоплавких металлов (цинка, олова и др.). Покрытия наносят электролитически, путем парового осаждения или погружения подложки в расплавленный металл.
В электрическом полевыращивают кристаллы из железа, меди, серебра и др. Процесс осаждения ведут при больших плотностях тока в присутствии органических примесей (глюкозы, олеиновой кислоты и др.), применяя катоды с малой рабочей поверхностью.
Процесс осаждениякристаллов из газовой фазы основан на испарении исходного вещества с последующим массопереносом его через газовую фазу и конденсации в зоне осаждения. На рост усов оказывают влияние градиент температуры в камере, давление пара и чистота исходного вещества.
Наиболее распространены химическиеспособы получения нитевидных кристаллов, которые нашли применение не только в лабораторной практике, но и в промышленности. Восстановление различных соединений металлов является основным химическим способом получения нитевидных кристаллов. В качестве исходных соединений используют сульфиды, оксиды и галогениды.
Для создания КМ на металлической основе в качестве армирующих элементов применяют нитевидные кристаллы таких тугоплавких соединений, как карбиды кремния, бора, оксида алюминия и др.
Благодаря совершенству структуры нитевидные кристаллы имеют высокие, близкие к теоретическим прочностные характеристики. Например, нитевидные кристаллы из карбида кремния имеют плотность 3320 кг/м3, прочность при растяжении 21000 МПа и модуль упругости 490000 МПа. Это свидетельствует о большой перспективности нитевидных кристаллов для армирования КМ с металлическими матрицами. Уже сейчас можно говорить о промышленных масштабах выпуска нитевидных кристаллов из карбида кремния и оксида алюминия.
Волокна в чистом виде редко применяют для армирования КМ. На волокна, жгуты, ленты тонким слоем наносят барьерные и технологические покрытия. Барьерные покрытия предназначены для защиты волокна от разрушения (деградации) в результате физико-химического взаимодействия его с матричными сплавами. Они представляют собой термодинамические стойкие химические соединения. Их фазовый состав (бориды, нитриды, карбиды, оксиды и т.д.) выбирают в зависимости от характера физико-химической и термомеханической совместимости армирующих материалов и матричных сплавов. С этой целью используют различные паро-газофазные способы осаждения химических соединений на поверхность непрерывно движущихся волокон. Толщина покрытий составляет несколько микрометров.
Технологические покрытия предназначены для улучшения смачивания волокна матричным металлическим расплавом и повышения сил адгезии. В большинстве случаев технологические покрытия получают теми же способами, что и барьерные покрытия.
Барьерные и технологические покрытия обычно совмещают в едином цикле предварительной подготовки волокон при производстве КМ.