Файл: Физикотехнологические основы получения композиционных материалов.doc
ВУЗ: Не указан
Категория: Не указан
Дисциплина: Не указана
Добавлен: 07.11.2023
Просмотров: 295
Скачиваний: 4
СОДЕРЖАНИЕ
Физико-технологические основы получения композиционных материалов
1.1. Характеристика композиционных материалов
1.2. Классификация композиционных материалов
1.3. Требования, предъявляемые к армирующим и матричным материалам
Изготовление изделий из металлических композиционных материалов
2.3. Способы получения полуфабрикатов и готовых изделий
3.2. Краткая характеристика порошковых материалов
3.3. Приготовление смеси и формообразование заготовок
3.4. Спекание и окончательная обработка заготовок
4. Изготовление деталей из полимерных композиционных материалов
4.3. Способы формообразования деталей в высокоэластичном состоянии
5. Получение деталей из композиционных пластиков
7. Технологические особенности проектирования и изготовления деталей из композиционных материалов
7.1. Технологические требования к конструкциям изготовляемых деталей
7.2. Технологические особенности дополнительной механической обработки заготовок
Рис. 15. Схема литья под давлением
Форма и размеры прессуемых деталей зависят от формообразующих элементов пресс-формы, к которым предъявляют высокие требования по точности и качеству поверхности. Формообразующие детали пресс-форм изготовляют из высоколегированных или инструментальных сталей с последующей закалкой до высокой твердости. Для повышения износостойкости и улучшения внешнего вида прессуемых деталей формообразующие элементы пресс-форм полируют и хромируют.
Листы и плиты из термореактивных композиционных материалов прессуют пакетами на прессах. Заготовки материала (из хлопчатобумажной ткани, стеклоткани и т.д.) пропитывают смолой и укладывают между горячими плитами пресса. Число уложенных слоев ткани определяет толщину листов и плит. Размеры прессуемых деталей ограничиваются мощностью гидравлического пресса. Трубы, прутки круглого и фасонного сечений получают прессованием реактопластов через калиброванное отверстие пресс-формы. Процесс прессования характеризуется низкой производительностью и сложностями технологического характера.
Литье под давлением - высокопроизводительный и эффективный способ массового производства деталей из термопластов. Перерабатываемый материал из загрузочного бункера 8(рис. 15) подается дозатором 9 в рабочий цилиндр 6 с электронагревателем 4. При движении поршня 7 определенная доза материала поступает в зону обогрева, а уже расплавленный материал через сопло 3 и литниковый канал - в полость пресс-формы 1, в которой формируется изготовляемая деталь 2. В рабочем (нагревательном) цилиндре на пути потока расплава установлен рассекатель 5, который заставляет расплав протекать тонким слоем у стенок цилиндра. Это ускоряет прогрев и обеспечивает более равномерную температуру расплава. При движении поршня в исходное положение с помощью дозатора 9 очередная порция материала подается в рабочий цилиндр. Для предотвращения перегрева выше 50 - 70°С в процессе литья пресс-форма охлаждается проточной водой. После охлаждения материала пресс-форма размыкается и готовая деталь с помощью выталкивателей извлекается из нее. Широко применяют также литьевые машины с червячной пластикацией материала, в которых вместо поршня используют вращающиеся червяки.
Литьем под давлением получают детали сложной конфигурации с различными толщинами стенок, ребрами жесткости, с резьбами и т.д. Применяют литейные машины, позволяющие механизировать и автоматизировать процесс получения деталей. Производительность процесса литья в 20 - 40 раз выше производительности прессования, поэтому литье под давлением является одним из основных способов переработки пластических масс в детали. Качество отливаемых деталей зависит от температур пресс-формы и расплава, давления прессования, продолжительности выдержки под давлением и т.д.
Центробежное литье применяют для получения крупногабаритных и толстостенных деталей из термопластов (кольца, шкивы, зубчатые колеса и т.п.). Центробежные силы плотно прижимают залитый материал к внутренней поверхности формы. После охлаждения готовую деталь извлекают из формы и заливают новую порцию расплавленного материала.
Выдавливание (или экструзия) отличается от других способов переработки термопластов непрерывностью, высокой производительностью процесса и возможностью получения на одном и том же оборудовании большого многообразия деталей. Выдавливание осуществляют на специальных червячных машинах - автоматах.Оправку применяют для получения отверстия при выдавливании труб.
Непрерывным выдавливанием можно изготовлять детали различного профиля При получении пленок из термопластов (полиэтилена, полипропилена и др.) используют метод раздува. Расплавленный материал продавливают через кольцевую щель насадной головки и получают заготовку в виде трубы, которую сжатым воздухом раздувают до требуемого диаметра. После охлаждения пленку подают на намоточное приспособление и сматывают в рулон. При производстве листового материала используют щелевые головки шириной до 1600 мм. Выходящее из щелевого отверстия полотно проходит через валки гладильного и тянущего устройств. Здесь же происходит предварительное охлаждение листа, а на роликовых конвейерах - окончательное охлаждение. Готовую продукцию сматывают в рулоны или разрезают на листы определенных размеров с помощью специальных ножниц.
4.3. Способы формообразования деталей в высокоэластичном состоянии
Для получения многих круногабарит-ных деталей наиболее целесообразной является переработка листовых термопластичных материалов. Технологический процесс получения деталей основан на использовании свойств термопластов, нагретых до высокоэластичного состояния. Основными технологическими способами являются пневматическая формовка, вакуумная формовка и штамповка.
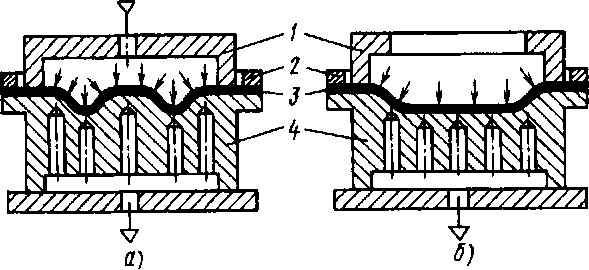
Рис. 16. Схемы пневматической (а) и вакуумной (б) формовок
При пневматической и вакуумной формовке (рис. 16) предварительно разогретую и зажатую в рамку 2 заготовку 3 плотно прижимают к матрице 4 верхней камерой 1 и формуют с помощью сжатого воздуха (при пневмоформовке) или под давлением атмосферного воздуха (при вакуум-формовке). После охлаждения готовую деталь сжатым воздухом удаляют с матрицы. При пневмо- и вакуумной формовке матрицу предварительно подогревают до 40 - 60°С.
Листовые материалы нагревают главным образом в электрических нагревательных шкафах, оснащенных контролирующими и автоматически регулирующими приборами. Необходимым условием является равномерный нагрев листовых заготовок. В противном случае на различных участках материала будет неодинаковая пластичность, что вызовет брак при формовке из-за разрывов, трещин, коробления и т.д. Для равномерного нагрева шкафы оснащают вентилятором для перемешивания воздуха. Температура нагрева зависит от вида перерабатываемого материала.
Особенностью вакуумной формовки является простота установки и обслуживания. Однако небольшой перепад давления препятствует применению этого способа для получения толстостенных (более 2,5 мм) и сложных конфигураций деталей, а также деталей из жестких термопластов.
Пневматическая формовка позволяет получать детали сложных пространственных конфигураций и различных толщин в зависимости от давления подаваемого воздуха. Для предотвращения быстрого и неравномерного охлаждения, возможного возникновения внутренних напряжений формуют подогретым до 50 - 70°С сжатым воздухом.
Разновидностью пневматической формовки является изготовление деталей без применения матрицы или пуансона. Разогретый лист зажимают в кольцо и с помощью сжатого воздуха или под действием атмосферного давления получают сферическое изделие. Поскольку формуют без соприкосновения с формообразующими деталями, получаемые детали имеют высокую прозрачность (колпаки кабин самолетов, детали для оптики и светотехники). В производственных условиях часто применяют комбинированное формообразование, при котором совмещают операции выдувания и пневматического обжима, а также, если необходимо, штамповки, опрессовки и т.д.
Штамповкой получают главным образом детали незамкнутой пространственной формы (козырьки, обтекатели, стекла кабин и т.д.). Термопластичный листовой материал, разогретый до определенной температуры, формуют с помощью пуансона и матрицы. При штамповке изменяются форма и размеры листовых заготовок за счет перемещения и перераспределения объема материала.
Штампуют на обычных гидравлических или механических прессах. Пуансоны и матрицы изготовляют из дерева и других неметаллических материалов при производстве небольшого числа деталей и из металлов - при массовом производстве.
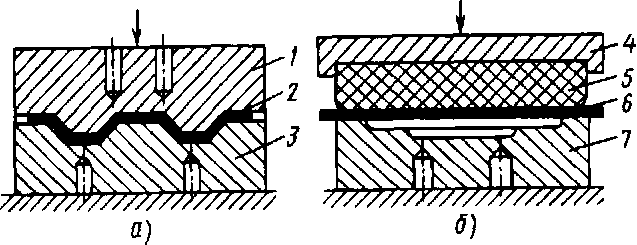
Рис. 17. Схемы штамповки жестким (а) и эластичным (б) пуансонами
В зависимости от материала, из которого изготовляют пуансоны, различают два основных вида штамповки: жестким и эластичным пуансонами.
Схема штамповки жестким пуансоном показана на рис. 17 а. Зазор между пуансоном 1 и матрицей 3 равен толщине штампуемого материала 2 с допуском ± 10%; необходимое взаимное расположение пуансона и матрицы обеспечивается направляющими. В пуансоне и матрице делают отверстия для выхода воздуха.
Штамповкой эластичным пуансоном получают детали из листовых термопластов, имеющих небольшие углубления и четкий рисунок. Предварительно разогретую заготовку 6 помещают на форму 7 (рис. 17 б). Плоский резиновый пуансон 5, вмонтированный в обойму
4, опускают на заготовку и к нему прилагают давление. Штампуют на гидравлических или винтовых прессах.
При штамповке, как и при других видах формообразования материалов в высокоэластичном состоянии, качество получаемых деталей зависит от точного соблюдения технологического процесса.