Файл: Физикотехнологические основы получения композиционных материалов.doc
ВУЗ: Не указан
Категория: Не указан
Дисциплина: Не указана
Добавлен: 07.11.2023
Просмотров: 277
Скачиваний: 4
СОДЕРЖАНИЕ
Физико-технологические основы получения композиционных материалов
1.1. Характеристика композиционных материалов
1.2. Классификация композиционных материалов
1.3. Требования, предъявляемые к армирующим и матричным материалам
Изготовление изделий из металлических композиционных материалов
2.3. Способы получения полуфабрикатов и готовых изделий
3.2. Краткая характеристика порошковых материалов
3.3. Приготовление смеси и формообразование заготовок
3.4. Спекание и окончательная обработка заготовок
4. Изготовление деталей из полимерных композиционных материалов
4.3. Способы формообразования деталей в высокоэластичном состоянии
5. Получение деталей из композиционных пластиков
7. Технологические особенности проектирования и изготовления деталей из композиционных материалов
7.1. Технологические требования к конструкциям изготовляемых деталей
7.2. Технологические особенности дополнительной механической обработки заготовок
2.2. Материалы матриц
В качестве материалов матриц при изготовлении МКМ применяют освоенные промышленностью металлы и сплавы, а также сплавы, создаваемые специально для получения МКМ. В зависимости от требуемых эксплуатационных свойств применяют следующие материалы: легкие металлы и сплавы на основе алюминия и магния; сплавы на основе титана, меди; жаропрочные и жаростойкие сплавы на основе железа, никеля и кобальта; тугоплавкие сплавы на основе вольфрама, молибдена и ниобия.
Алюминиевые сплавы обладают хорошей пластичностью, коррозионной стойкостью, но сравнительно невысокой прочностью. Для пропитки КМ применяют алюминиевые сплавы с хорошими литейными свойствами, например силумины, имеющие в своем составе повышенное содержание кремния. Перспективным для жаропрочных КМ является САП (спеченный алюминиевый порошок), который представляет собой алюминий, упрочненный дискретными частицами оксида алюминия. МКМ на основе САП имеют высокую жаропрочность (до 500°С), хорошо обрабатываются давлением, резанием и обладают высокой коррозионной стойкостью.
Магний и его сплавы характеризуются низкой плотностью, относительно высокими механическими свойствами, способностью сопротивляться ударным нагрузкам и вибрациям. Кроме того, они достаточно пластичны и хорошо обрабатываются давлением.
Титановые сплавы имеют малую плотность, а по прочностным характеристикам превосходят алюминиевые и магниевые сплавы. Они имеют достаточно хорошие литейные свойства и могут обрабатываться пластическим деформированием в широком интервале температур (600 - 1200 °С). Для армирования КМ промышленностью налажен выпуск фольги из титановых сплавов толщиной 3 - 200 мкм.
Медь и медные сплавы имеют высокую электропроводимость и теплопроводность. В технологическом отношении медь и ее сплавы характеризуются высокими пластическими свойствами. В большинстве случаев медные сплавы пластически деформируются в холодном состоянии.
Жаропрочные и жаростойкие сплавы получают на основе системы никель - хром с легирующими добавками вольфрама, молибдена, титана, алюминия. Они стойки к образованию окалины на поверхности в газовых средах при нагреве свыше 500°С. Повышенная длительная прочность, высокое сопротивление ползучести и усталости достигаются за счет введения в сплавы титана и алюминия. В настоящее время сплавы на никелевой и кобальтовой основе, легированные различными элементами, способны работать при температурах до 1100°С.
Пластические свойства таких сплавов низки, поэтому их подвергают обработке давлением. МКМ из жаропрочных сплавов изготовляют преимущественно жидкофазными методами (литье, пропитка), а также методами порошковой металлургии (прессование, спекание).
Порошковой металлургией стало возможно получать МКМ с матрицей из особотугоплавких сплавов - ниобия, вольфрама, молибдена и сплавов на их основе. Волокнистыми наполнителями (нитевидными кристаллами из тугоплавких соединений) эти матрицы армируют с целью придания им особых эксплуатационных свойств (ударопрочности, термостойкости и других специальных физических характеристик).
2.3. Способы получения полуфабрикатов и готовых изделий
При разработке технологического процесса получения изделий из КМ приходится в комплексе решать многие вопросы: выбор армирующих и матричных материалов, их химическое взаимодействие, смачивание, способы ориентации армирующих волокон, способы окончательного объединения волокон и матрицы в единое целое (изделие), выбор оптимальных технологических режимов и др. Не существует универсального технологического процесса, пригодного для получения любого изделия из КМ. Неудачно выбранные технологический метод и режимы изготовления КМ приводят к тому, что прогнозируемые физико-механические и эксплуатационные показатели на практике не реализуются.
Технологическому процессу получения КМ предшествуют вспомогательные операции: очистка, мойка и сушка волокон, объединение их в жгуты или каркасы, получение элементарных соединений матрица - волокно, сборка чередующихся слоев элементов и др.
Короткие армирующие элементы вводят в матричные материалы в разориентированном состоянии или предварительно ориентируя их в определенном направлении.
В производственных условиях из разориентированных кристаллов, коротких волокон и проволок изготовляют полуфабрикаты: войлок, маты и т.д. Используют различные способы войлокования: жидкостные, воздушные, вакуумные и гравитационные. В качестве примера на рис. 4 показана схема жидкостного войлокования коротких волокон. Суспензия из питающего бака 1 поступает на сетку 2, покрытую фильтровальной бумагой. С помощью роликов 3 она проходит над камерами 4 для отсоса жидкости. Прижимными валками 5 войлок уплотняется и поступает в печь
6,где он просушивается или, при необходимости, спекается.
Д
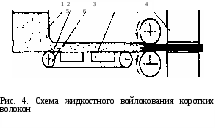
ля получения армирующих элементов с требуемой ориентацией применяют технологию текстильной переработки. Короткие волокна перерабатывают в пряжу. Пряжей называют нить из коротких волокон, соединенных путем кручения. Пряжа может быть однородная (из одного вида волокна) или смешанная (из смеси различных волокон). Пряжу можно использовать для непосредственного армирования КМ или сшивать нитями в ткань или ленты. Сетки и ткани получают в результате ткацкой переработки непрерывных волокон и металлических проволок. Направление и порядок взаимного расположения армирующих элементов определяют их структуру и свойства. Возможны и другие варианты соединения отдельных волокон из пластичных материалов в единый армирующий элемент.
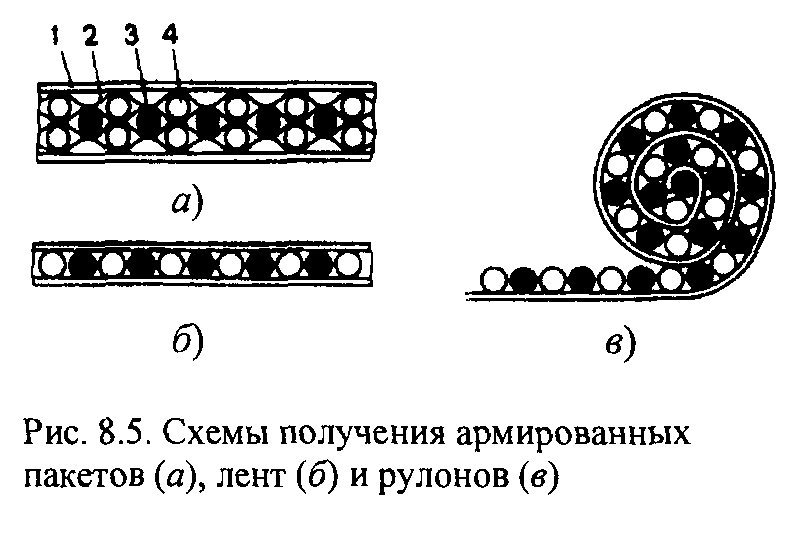

Жесткие волокна, например из вольфрама, молибдена, ниобия и их сплавов, ориентируют в материале матрицы в виде пакетов, листов, рулонов и т.п. Пакеты (рис. 5, а) получают путем послойной укладки рифленой фольги 2из материала матрицы, армирующих волокон 3и волокон 4из материала матрицы или любого другого материала. Набранные таким образом пакеты определенной высоты соединяют полосами материала матрицы 1. Ленты (рис. 5, 6)получают путем поочередной укладки армирующих и матричных волокон между полосами. В отдельных случаях ленты сматывают в рулоны (рис. 5, в). Чтобы закрепить волокна на матричной полосе, на них плазменным напылением наносят тонкий слой материала матрицы.
На предприятиях обычно организуют выпуск полуфабрикатов в виде листов, труб, профилей и т.д. Основой производства полуфабрикатов и изделий из КМ служат так называемые препреги, представляющие собой однослойные ленты с одним рядом армирующих волокон или тканей, пропитанных или покрытых материалом матрицы с одной или с обеих сторон. Используют также пропитанные металлом жгуты волокон или индивидуальные волокна с покрытиями материалом матрицы.
Все технологические способы получения препрегов, полуфабрикатов и изделий из МКМ условно можно разделить на четыре основные группы: парогазофазные, жидкофазные, твердожидкофазные и твердофазные.
Парогазофазные способы применяют для нанесения на волокна жгута, ленты и ткани барьерных или технологических покрытий. Применять эти способы для полного компактирования КМ нецелесообразно, так как они характеризуются низкой производительностью процесса.
Жидкофазные способы используют на всех стадиях производства КМ - от полуфабрикатов до изделий. К ним относятся протяжка волокон, жгутов и тканей через расплав материала матрицы для пластифицирования волокна и получения соответствующих препрегов; пропитка пакетов препрегов материалом матрицы на стадии получения полуфабрикатов или готовых изделий из КМ; плазменные и некоторые другие виды газотермического распыления металлов для получения ленточных препрегов и "корковых" полуфабрикатов, подвергаемых последующему компактировапию методами обработки давлением.
Универсальным и наиболее освоенным промышленностью способом изготовления КМ является пропитка. Этот способ имеет ряд преимуществ перед твердофазными способами изготовления МКМ: более высокую производительность процесса; практическое отсутствие силового воздействия на компоненты, что обеспечивает возможность получать крупногабаритные изделия, в том числе сложного фасонного профиля; возможность создания непрерывности процесса пропитки, механизации и автоматизации технологического процесса.
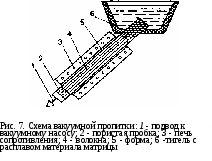
В зависимости от условий обеспечения смачиваемости системы армирующий каркас - расплав материала матрицы применяют две схемы пропитки: самопроизвольную пропитку и пропитку под давлением.
Самопроизвольную пропитку осуществляют путем заливки расплавленного материала в форму с уложенным в ней каркасом из армирующих волокон.
Наиболее перспективным и производительным является способ непрерывной протяжки армирующих каркасов через расплав материала матрицы. По этой схеме разрабатываются технологические процессы непрерывного литья полуфабрикатов из КМ. Принципиальные преимущества этого способа производства КМ - в его непрерывности, малом времени контактирования волокон с расплавом, малых трудозатратах и капиталовложениях. Перспективной считается вертикальная схема пропитки, при которой волокна, ленты, препреги проходят через ванну с расплавом и на выходе через фильеру получают форму сечения полуфабриката (рис. 6). Поэтапное сужение сечения фильеры на выходе позволяет получать полуфабрикаты с высоким объемным содержанием армирующих волокон.
Принудительную пропитку обычно используют при недостаточной смачиваемости в системе матрица - волокно или для ускорения процесса пропитки для компонентов с удовлетворительной и хорошей смачиваемостью.
В
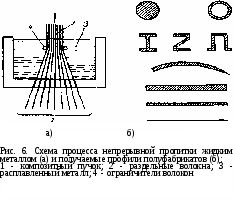
качестве примера на рис. 7 показана схема вакуумной пропитки КМ. Заполнение пор расплавленным металлом осуществляется за счет разности между атмосферным давлением и давлением, созданным в порах при вакуумировании. Вертикальное расположение тигля обеспечивает ускорение процесса протекания за счет дополнительного давления массы расплава.
Разновидностью пропитки под давлением является создание избыточного давления сжатым газом на зеркало расплавленного металла. Эффективность процесса пропитки значительно повышается при наложении ультразвуковых колебаний.
Твердожидкофазные способы используют для получения полуфабрикатов и изделий из КМ методами горячего прессования, волочения и прокатки пакетов, препрегов. Необходимым условием является нанесение матричного материала на ленты, препреги и ткани в таком количестве, чтобы его оказалось достаточно в жидкой фазе для равномерной пропитки волоконного каркаса расплавом. Прессование осуществляется в интервале кристаллизации сплава материала матрицы. Прессование КМ в условиях твердожидко-го состояния матричных сплавов способствует снижению давления и уменьшает вероятность разрушения волокон.
Твердофазные способы используют для компактирования изделий из полуфабрикатов. Основным критерием применимости твердофазных способов является возможность деформирования компонентов КМ. Но при этом совместное пластическое деформирование матрицы и волокон не должно приводить к разрушению арматуры. Это обстоятельство является основным препятствием для более широкого использования способов соединения арматуры и матрицы пластическим деформированием. Если в качестве арматуры выбраны волокна или проволоки со значительным запасом пластичности, то уплотнять МКМ можно ковкой, прокаткой, импульсным прессованием и др. Возможны также различные способы диффузионной сварки.
К процессам соединения в твердофазном состоянии предъявляют высокие требования по подготовке компонентов: высокая чистота поверхностей контактирования, отсутствие оксидных пленок и т.д. Это является дополнительным препятствием для более широкого применения твердофазных способов при изготовлении изделий из КМ.