Файл: Физикотехнологические основы получения композиционных материалов.doc
ВУЗ: Не указан
Категория: Не указан
Дисциплина: Не указана
Добавлен: 07.11.2023
Просмотров: 282
Скачиваний: 4
СОДЕРЖАНИЕ
Физико-технологические основы получения композиционных материалов
1.1. Характеристика композиционных материалов
1.2. Классификация композиционных материалов
1.3. Требования, предъявляемые к армирующим и матричным материалам
Изготовление изделий из металлических композиционных материалов
2.3. Способы получения полуфабрикатов и готовых изделий
3.2. Краткая характеристика порошковых материалов
3.3. Приготовление смеси и формообразование заготовок
3.4. Спекание и окончательная обработка заготовок
4. Изготовление деталей из полимерных композиционных материалов
4.3. Способы формообразования деталей в высокоэластичном состоянии
5. Получение деталей из композиционных пластиков
7. Технологические особенности проектирования и изготовления деталей из композиционных материалов
7.1. Технологические требования к конструкциям изготовляемых деталей
7.2. Технологические особенности дополнительной механической обработки заготовок
Оглавление
Введение 3
1.Физико-технологические основы получения композиционных материалов 5
1.1. Характеристика композиционных материалов 5
1.2. Классификация композиционных материалов 6
1.3. Требования, предъявляемые к армирующим и матричным материалам 8
2.Изготовление изделий из металлических композиционных материалов 13
2.1. Волокна для армирования композиционных материалов 13
2.2. Материалы матриц 17
2.3. Способы получения полуфабрикатов и готовых изделий 18
3.Изготовление деталей из композиционных порошковых материалов 24
3.1. Способы получения и технологические свойства порошков 24
3.2. Краткая характеристика порошковых материалов 27
3.3. Приготовление смеси и формообразование заготовок 28
3.4. Спекание и окончательная обработка заготовок 32
4. Изготовление деталей из полимерных композиционных материалов 36
4.1. Классификация и технологические свойства пластмасс 36
4.2. Способы формообразования деталей в вязкотекучем состоянии 39
4.3. Способы формообразования деталей в высокоэластичном состоянии 43
5. Получение деталей из композиционных пластиков 46
6. Изготовление резиновых технических деталей 49
6.1. Состав и свойства резиновых технических материалов 49
6.2. Способы изготовления резиновых технических деталей 50
7. Технологические особенности проектирования и изготовления деталей из композиционных материалов 53
7.1. Технологические требования к конструкциям изготовляемых деталей 53
7.2. Технологические особенности дополнительной механической обработки заготовок 54
7.3. Техника безопасности и охрана окружающей среды при изготовлении деталей из композиционных материалов 57
Заключение 59
Список использованной литературы 60
Введение
Развитие всех отраслей промышленности, а также задача повышения качества выпускаемых изделий потребовали создания новых конструкционных материалов. Авиация, ракетно-космическая техника, ядерная энергетика и многие другие отрасли нуждаются в материалах, характеризующихся высокими прочностью, термостойкостью и жаропрочностью, малой плотностью, теплопроводностью и электропроводимостью, диэлектрическими, магнитными и другими специальными физическими свойствами. Объединение различных ценных свойств отдельных материалов позволило создать единое целое - композицию. Современное материаловедение уже добилось значительных успехов в исследовании и разработке композиционных материалов (КМ).
Композиционные материалы (композиты) (от лат. compositio – составление), многокомпонентные материалы, состоящие из полимерной, металлической, углеродной, керамической или др. основы (матрицы), армированной наполнителями из волокон, нитевидных кристаллов, тонкодиспeрсных частиц и др. Путем подбора состава и свойств наполнителя и матрицы (связующего), их соотношения, ориентации наполнителя можно получить материалы с требуемым сочетанием эксплуатационных и технологических свойств. Использование в одном материале нескольких матриц (полиматричные композиционные материалы) или наполнителей различной природы (гибридные композиционные материалы) значительно расширяет возможности регулирования свойств композиционных материалов.
Принципы армирования для упрочнения известны в технике с глубокой древности. Еще в Вавилоне использовали тростник для армирования глины при постройке жилищ, а в Древней Греции железными прутьями укрепляли мраморные колонны при постройке дворцов и храмов. В 1555-1560 гг. при постройке храма Василия Блаженного в Москве русские зодчие Барма и Постник использовали армированные железными полосами каменные плиты. Прообразом композиционные материалы являются широко известный железобетон, представляющий собой сочетание бетона, работающего на сжатие и стальной арматуры, работающей на растяжение, а также полученные в XIX веке прокаткой слоистые материалы.
Успешному развитию современным КМ содействовали: разработка и применение в конструкциях волокнистых стеклопластиков, обладающих высокой удельной прочностью (1940-1950 гг.). Открытие весьма высокой прочности, приближающейся к теоретической, нитевидных кристаллов и доказательства возможности использования их для упрочнения металлических и неметаллических материалов (1950-1960 гг.), разработка новых армирующих материалов – высокопрочных и высокомодульных непрерывных волокон бора, углерода, Al2O3, SiC и волокон других неорганических тугоплавких соединений, а также упрочнителей на основе металлов (1960-1970 гг.).
С развитием теории и технологии КМ стало возможным создавать изделия, работающие в экстремальных условиях. Так, при разработке космического корабля многоразового использования "Буран" требовалось создать легкую конструкцию, способную длительно работать в исключительно тяжелых условиях: при сверхвысоких динамических и акустических нагрузках от мощных ракетных двигателей и сверхзвукового потока воздуха при подъеме; охлаждении в открытом космосе и нагреве облицовки корабля до температуры свыше тысячи градусов при входе в плотные слои атмосферы при посадке. Решения этих задач удалось достичь благодаря использованию конструкторами нетрадиционных новых, в том числе и композиционных, материалов со специальными свойствами.
Практически всякий современный материал представляет собой композицию, поскольку материалы редко используются в чистом виде. Действительно, почти все металлические сплавы содержат несколько фаз, которые либо создаются специально (для придания материалу заданных эксплуатационных и технологических свойств), либо образуются в результате наличия в металле вредных примесей. Вышеперечисленное объясняет актуальность рассматриваемой проблемы.
Целью данной работы является рассмотрение технологических особенностей изготовления различных деталей из широкого спектра композиционных материалов. Задачи, поставленные для достижения цели:
-
Дать определение, рассмотреть характеристики и основы получения композиционных материалов; -
Изучить классификацию современных композиционных материалов. -
Рассмотреть технологии изготовления деталей из различных видов композиционных материалов, изучить особенности работы с ними.
- 1 2 3 4 5 6 7 8 9 ... 14
Физико-технологические основы получения композиционных материалов
1.1. Характеристика композиционных материалов
На современном этапе понятие композиционного материала должно удовлетворять следующим критериям: композиция должна представлять собой объемное сочетание хотя бы двух химически разнородных материалов с четкой границей раздела между этими компонентами (фазами) и характеризоваться свойствами, которых не имеет никакой из ее компонентов в отдельности. Композицию получают путем введения в основной материал (матрицу) определенного количества другого материала, который добавляется в целях получения специальных свойств. КМ может состоять из двух, трех и более компонентов. Размеры частиц входящих компонентов могут колебаться в широких пределах - от сотых долей микрометра (для порошковых наполнителей) до нескольких миллиметров (при использовании волокнистых наполнителей).
Отличие большинства КМ от традиционных материалов в том, что процесс получения КМ технологически совмещается с процессом изготовления изделия.
Проектирование изделия из КМ начинается с конструирования самого материала - выбора его компонентов и назначения оптимальных технологических процессов производства. Особенность создания конструкций из КМ в отличие от конструкций из традиционных материалов заключается в том, что конструирование материала, разработка технологического процесса изготовления и проектирование самой конструкции - это единый взаимосвязанный процесс.
Физико-механические свойства КМ в зависимости от концентрации компонентов, их геометрических параметров и ориентации, а также технологии изготовления могут меняться в очень широких пределах. Тем самым открывается возможность специального создания (конструирования) материала с заданными свойствами для определенного изделия.
Наглядным подтверждением широкого применения КМ является использование углепластиков в авиации (рис. 1).
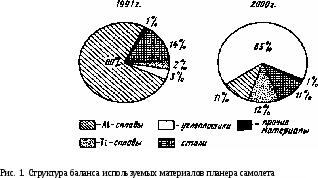
Аналогичная тенденция применения КМ характерна и для других отраслей промышленности, так как это неразрывно связано с повышением технико-экономических показателей выпускаемых изделий.
1.2. Классификация композиционных материалов
Все КМ условно можно классифицировать по следующим признакам: материалу композиции, типу арматуры и ее ориентации, способу получения композиции и изделий из них, по назначению.
В зависимости от материала матрицы КМ можно разделить на следующие основные группы: композиции с металлической матрицей - металлические композиционные материалы (МКМ), с полимерной - полимерные композиционные материалы (ПКМ), с резиновой - резиновые композиционные материалы (РКМ) и с керамической - керамические композиционные материалы (ККМ).
Название ПКМ обычно присваивают в зависимости от армирующего материала. Например, ПКМ, армированные стеклянными волокнами, называют стеклопластиками. Аналогично получили свои названия металлопластики, асбестопластики, углепластики, боропластики и т.д.
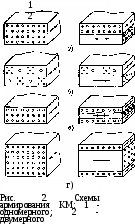
У металлических и керамических КМ пока еще нет четких правил присвоения названий. Обычно вначале указывают материал матрицы, а затем армирующий материал, например медно-вольфрамовые, алюминиево-стальные КМ и т.п.
По типу арматуры и ее ориентации КМ подразделяют на две основные группы: изотропные и анизотропные.
Изотропные КМ имеют одинаковые свойства во всех направлениях. К этой группе относят КМ с порошкообразными наполнителями. К числу изотропных условно относят и КМ, армированные короткими (дискретными) частицами. КМ при этом получаются квазиизотропными, т.е. изотропными в объеме всего изделия, но анизотропными в микрообъемах.
У анизотропных материалов свойства зависят от направления армирующего материала. Их подразделяют на однонаправленные, слоистые и трехмерно-направленные. Анизотропия материала закладывается конструктором для получения КМ с заданными свойствами. Однонаправленные КМ чаще всего проектируют для изготовления изделий, работающих на растяжение. Слоистые КМ получают путем продольно-поперечной укладки с правильным чередованием слоев. Трехмерно-направленное армирование обычно достигается за счет использования "сшитых" в поперечном направлении армирующих тканей, сеток и т.п. Кроме такой анизотропии образуется еще технологическая анизотропия, возникающая при пластическом деформировании изотропных материалов (металлов).